Svartstreck
Extreme
while you're at it, check if there are bolts that are longer than they need to be, i bet there are dozens of them.
Nikolai
TY 4 Stroke God
Good idea. I probably have a 1/3 less bolts than a factory sled. My sled is already pretty gutted so I won't have as many places I can replace the oem steel bolts.
Rick texted me and mentioned maybe doing the oil pan, stator cover, and water pump cover bolts. Anyone have thoughts on these? They're all in visible areas so it'd be easy to keep an eye on them.
Rick texted me and mentioned maybe doing the oil pan, stator cover, and water pump cover bolts. Anyone have thoughts on these? They're all in visible areas so it'd be easy to keep an eye on them.
Svartstreck
Extreme
Ski loops, brake lever, exhaust brackets?
Shouldn't be too much load there
Shouldn't be too much load there

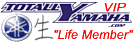

birkebeiner
Lifetime Member
- Joined
- Jul 27, 2009
- Messages
- 895
- Reaction score
- 102
- Points
- 718
- Location
- Norway
- Country
- Norway
- Snowmobile
- 2015 Yamaha SR Viper X-TX
Why not titanium bolts??
yamaha1973
TY 4 Stroke Master
- Joined
- Nov 27, 2011
- Messages
- 1,288
- Reaction score
- 14
- Points
- 743
- Location
- St. Peter Minnesota
- Country
- USA
- Snowmobile
- 2014 Viper XTX SE
Nikolai
TY 4 Stroke God
Ti is too much money for me. 7075 is 60% lighter than steel, 20% lighter than Ti, and about 1/2 the price of Ti. I can justify Alu bolts, but I have a hard time spending the coin for Ti bolts.
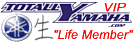

birkebeiner
Lifetime Member
- Joined
- Jul 27, 2009
- Messages
- 895
- Reaction score
- 102
- Points
- 718
- Location
- Norway
- Country
- Norway
- Snowmobile
- 2015 Yamaha SR Viper X-TX
Can see the cost issue, but you wouldn't need to worry about breaking them. Ti is what, twice the strength of Al?
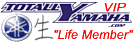

birkebeiner
Lifetime Member
- Joined
- Jul 27, 2009
- Messages
- 895
- Reaction score
- 102
- Points
- 718
- Location
- Norway
- Country
- Norway
- Snowmobile
- 2015 Yamaha SR Viper X-TX
Then again, how much more would it be for Ti over Al for a few bolts?
Nikolai
TY 4 Stroke God
It is stronger, but why use Ti if Aluminum will do the job? Ti would a couple hundred dollars more and be heavier as well.
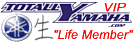

birkebeiner
Lifetime Member
- Joined
- Jul 27, 2009
- Messages
- 895
- Reaction score
- 102
- Points
- 718
- Location
- Norway
- Country
- Norway
- Snowmobile
- 2015 Yamaha SR Viper X-TX
True.
arteeex
TY 4 Stroke Master
I think a version of the 80/20 rule is going to apply here. Look for the heaviest parts and figure out how make them 5% lighter. It's going to add up to more weight than saving 35% on a handful of small parts.
Be aware that aluminum bolts under repetitive load will weaken with time and stretch under load more so than steel. I suspect anyone using aluminum bolts in performance applications is replacing them on a regular schedule. And, the first time you snap a head off an aluminum bolt you'll discover weight savings wasn't worth the dime.
FYI - for calculations shear strength is usually considered to be about 50 - 60% of the tensile strength. The best aluminum bolts are weaker than mild steel.
Be aware that aluminum bolts under repetitive load will weaken with time and stretch under load more so than steel. I suspect anyone using aluminum bolts in performance applications is replacing them on a regular schedule. And, the first time you snap a head off an aluminum bolt you'll discover weight savings wasn't worth the dime.
FYI - for calculations shear strength is usually considered to be about 50 - 60% of the tensile strength. The best aluminum bolts are weaker than mild steel.
Nikolai
TY 4 Stroke God
You bring up a good point. I think if we use aluminum bolts with the idea that they are a "torque once" bolt, then applications on the engine are good because you're the putting the bolt in one time and never touching it again. I've been looking at the microfiche and there 37 easy to replace (and visible) bolts on the Nytro motor.
11 - crankcase cover bolt, part# 90109-06015-00
4 - oil cooler bolt, part# 90110-06163-00
15 - oil pan bolt, part# 90109-06015-00
4 - water pump cover bolt, part# 91312-06040-00
3 - water pump cover bolt part# 98580-06016-00
The crankcase cover and oil pan bolts are the same part number, so there's 26 of the same bolt. I think I'm going to order a couple of their equivalent in 7075 and do some at home testing to see at what torque they fail. If they pass the home torque test I'll replace them on the motor. I'll order enough so I can test at different torque settings and see how much they stretch (or snap) if re-used.
Some of the test I'm thinking of are
- number of times torqued to factory spec, then removed, and torqued to factory spec again before snapping the bolt head
- continue to raise the torque setting (on a new bolt each time) to see at what torque the head will snap off
Any other ideas or tests you guys would like to see?
11 - crankcase cover bolt, part# 90109-06015-00
4 - oil cooler bolt, part# 90110-06163-00
15 - oil pan bolt, part# 90109-06015-00
4 - water pump cover bolt, part# 91312-06040-00
3 - water pump cover bolt part# 98580-06016-00
The crankcase cover and oil pan bolts are the same part number, so there's 26 of the same bolt. I think I'm going to order a couple of their equivalent in 7075 and do some at home testing to see at what torque they fail. If they pass the home torque test I'll replace them on the motor. I'll order enough so I can test at different torque settings and see how much they stretch (or snap) if re-used.
Some of the test I'm thinking of are
- number of times torqued to factory spec, then removed, and torqued to factory spec again before snapping the bolt head
- continue to raise the torque setting (on a new bolt each time) to see at what torque the head will snap off
Any other ideas or tests you guys would like to see?
Nikolai
TY 4 Stroke God
Andrew was kind enough to weigh a 90109-06015-00 bolt he had at work and it was 7.5 grams. Even 37 of them would only weigh 278 grams which is .69 lbs, putting the weight loss with aluminum bolts right at .4 lbs. Not worth the money unless my sled comes in 450.4 lbs haha. The only weigh (no pun) it's going to be cost effective is to replace 8 mm or larger bolts.
6mm x 25 mm 7075 Allen head bolts from Pro-Bolt are $11.14 per 10. So about $45 to replace all 37 bolts and lose not quite half a pound, plus the cost of gasket material from breaking all the seals.
6mm x 25 mm 7075 Allen head bolts from Pro-Bolt are $11.14 per 10. So about $45 to replace all 37 bolts and lose not quite half a pound, plus the cost of gasket material from breaking all the seals.
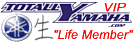

Super Sled
Lifetime Member
- Joined
- Feb 25, 2009
- Messages
- 3,631
- Reaction score
- 5
- Points
- 1,218
- Location
- Riding on the North Shore, MN
- Country
- USA
- Snowmobile
- Summit X
If you want to make the Nytro MTX weigh too much less your going to have to start removing major components and/ or mass from the sled -- like replacing the entire bulk head with a lighter weight version. The big issue here is Yamaha designed a lot of durability into the sled, which translated into bulk and weight. The same things that make the sled such high quality make it heavy.
Nikolai
TY 4 Stroke God
Again, this discussion is about aluminum bolts.
Similar threads
- Replies
- 5
- Views
- 6K
- Replies
- 16
- Views
- 13K
- Replies
- 1
- Views
- 584
- Replies
- 0
- Views
- 611
-
This site uses cookies to help personalise content, tailor your experience and to keep you logged in if you register.
By continuing to use this site, you are consenting to our use of cookies.