Tayz588
Extreme
Hey im going to school for welding and one day a week we have a metal fab class. So instead of making the 5th skidloader bucket for some random person I was thinking of making my own skidplate. What are your guys thoughts on using the drilled out holes underneath for mounting. Thinking of using like 11 guage or maybe like 1/8th?? Just wondering how a metal one would work out. Anyone done it?
zackn291
Expert
I wouldn't do it. Too much un-needed weight to the front end. If you want one that bad just save for a floatation plate.
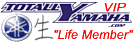

- Joined
- Nov 1, 2009
- Messages
- 3,564
- Location
- Winnipeg, Manitoba
- Country
- Canada
- Snowmobile
- 2009 Phazer RTX
zackn291 said:I wouldn't do it. Too much un-needed weight to the front end. If you want one that bad just save for a floatation plate.
agreed
Jeremy
Expert
Or even try some of that aluminum diamond plate (spelled wrong I think). That would shave some weight !!!
copo427ss
TY 4 Stroke Junkie
aluminum would be the only way to go
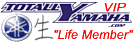

- Joined
- Nov 1, 2009
- Messages
- 3,564
- Location
- Winnipeg, Manitoba
- Country
- Canada
- Snowmobile
- 2009 Phazer RTX
You need a different welder for aluminum
marpolsdofer
TY 4 Stroke Guru
or you could do what I did for the tunnel cover 28ga weldable galvanised sheet metal. It is less then a pound on the tunnel cover but it is benndable and would be no need to weld.
Shoprat
Extreme
I teach metal shop, Depending on what alloy of aluminum you choose, there is no reason you can't make one. I love it when students want to attempt to do something like this. Over the years I have made many aluminum skid plates for peoples sleds. Contrary to what Zack says, aluminum usually weighs less than thick plastic and is very durable. Yeah it is easy to spend daddys money to buy a factory part, but there is no pride in it. I say go for it, build one, see how it works. If nothing else you will learn some new stuff.
phaze5
TY 4 Stroke Guru
i would do it, it cost me 4800 last year when i dinged my case, yes i said ding because thats the only mark there was, can you say tottalled?
yea its worth a couple pounds to save it
yea its worth a couple pounds to save it
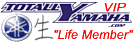

I agree.I have a plastic one but would really like some extra protection underneath it.Take a look at some of the pics of what all gets broke when hit and make those areas out of thicker aluminum like 1/4in rest could be very thin.Maybe you could make some $ on these.If done right I would get one.
Tayz588
Extreme
Posted: Wed Nov 11, 2009 8:41 am Post subject:
You need a different welder for aluminum
You can weld aluminum on a TIG, MIG, and also a stick welder if you have the new aluminum rods(that i think would suck). you dont need a "different" welder
Yeah I will have to to wait a month or so till we work with aluminum..just steel so far. If I made one I would make it out of aluminum like you guys said, and if i needed to weld on brackets to mount I would TIG them. Also I may make a front grab handle similar to what cannondale has. Wouldn't be hard at all.
You need a different welder for aluminum
You can weld aluminum on a TIG, MIG, and also a stick welder if you have the new aluminum rods(that i think would suck). you dont need a "different" welder
Yeah I will have to to wait a month or so till we work with aluminum..just steel so far. If I made one I would make it out of aluminum like you guys said, and if i needed to weld on brackets to mount I would TIG them. Also I may make a front grab handle similar to what cannondale has. Wouldn't be hard at all.
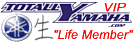

That grabbar/bumper saved alot of damage from a deer hit.Nice to that you can fit two hands on it.I need to get it straightened out after hitting that deer though.
Boo Rad
Veteran
Hit a deer on a sled. Wow. Did you have an extra pair of britches?
zackn291
Expert
would britches be another name for underwear?
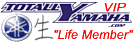

- Joined
- Nov 1, 2009
- Messages
- 3,564
- Location
- Winnipeg, Manitoba
- Country
- Canada
- Snowmobile
- 2009 Phazer RTX
well when i was in school welding with aluminum it had a cork type thing on the end so i assumed it was different... my bad
-
This site uses cookies to help personalise content, tailor your experience and to keep you logged in if you register.
By continuing to use this site, you are consenting to our use of cookies.