Stigapex
Suspended
I assume I can just replace my oem map sensor
with a 3 bar sensor if I adjust the fuel-table.
What sensor should I buy ?
with a 3 bar sensor if I adjust the fuel-table.
What sensor should I buy ?
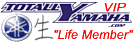

nate007
Lifetime Member
- Joined
- Dec 25, 2006
- Messages
- 2,770
- Reaction score
- 60
- Points
- 1,333
- Location
- Iowa City, Iowa
- Country
- USA
- Snowmobile
- 1. '06 Apex -twin screw
2. '04 Redline Revolt 800
3. '09 Nytro XTX - twin screw
It totally depends on the rest of your system? What means are you using to re-scale the OEM sensor?
All map sensors are a 0-5v sensor, and the oem sensor is only designed to tell the computer what to do over the vaccuum (load) side of the scale, with no boost.
Not saying that you are, but lets say if you just change to a 3bar sensor, it's going to be giving the computer a signal that is way out of scale for what the engine needs.
If you've got a piggyback system that will allow for an additional map sensor, you'll need to leave the oem sensor alone so the ecu doesn't know whats going on, and connect the 3bar to the piggy back for fuel control. Unless you are able to re-scale/recalibrate the factory ecu, don't change any of the oem sensors! A piggy back system effectively runs the fuel(and ignition if capable) in the background and makes it so teh factory ecu doesn't think anything is different.
Post what other components you have and how much boost you're running and I'll try to help.
FYI (just for info's sake) 1bar=14.7psi of boost, so 2 bar= 29psi, etc, etc.. For instance, if you put a 3 bar sensor on a system only running 12psi, you're never going to use the majority of the scale of the sensor, and you will lose "resolution", and only be using the bottom 1/3 of the scale. (0-1.25v +/- instead of 0-5v) If you're at 12psi, I would stick with a 1.5bar (20-21psi) sensor so you can use more points along the scale fo the sensor for more precise fuel contol. This is only general info, as every system is different, and it depends on the number of "points" along that 0-5v scale that it reads. For instance, I run a 2.5 bar sensor, and my piggy back has 18 points along the scale to use, so all of my fuel/spark adjustability is only using the lower 8 points of the scale since I'm running 12psi. (not exact info, but hope this helps)
All map sensors are a 0-5v sensor, and the oem sensor is only designed to tell the computer what to do over the vaccuum (load) side of the scale, with no boost.
Not saying that you are, but lets say if you just change to a 3bar sensor, it's going to be giving the computer a signal that is way out of scale for what the engine needs.
If you've got a piggyback system that will allow for an additional map sensor, you'll need to leave the oem sensor alone so the ecu doesn't know whats going on, and connect the 3bar to the piggy back for fuel control. Unless you are able to re-scale/recalibrate the factory ecu, don't change any of the oem sensors! A piggy back system effectively runs the fuel(and ignition if capable) in the background and makes it so teh factory ecu doesn't think anything is different.
Post what other components you have and how much boost you're running and I'll try to help.
FYI (just for info's sake) 1bar=14.7psi of boost, so 2 bar= 29psi, etc, etc.. For instance, if you put a 3 bar sensor on a system only running 12psi, you're never going to use the majority of the scale of the sensor, and you will lose "resolution", and only be using the bottom 1/3 of the scale. (0-1.25v +/- instead of 0-5v) If you're at 12psi, I would stick with a 1.5bar (20-21psi) sensor so you can use more points along the scale fo the sensor for more precise fuel contol. This is only general info, as every system is different, and it depends on the number of "points" along that 0-5v scale that it reads. For instance, I run a 2.5 bar sensor, and my piggy back has 18 points along the scale to use, so all of my fuel/spark adjustability is only using the lower 8 points of the scale since I'm running 12psi. (not exact info, but hope this helps)
Stigapex
Suspended
Mcxpress use megatune to adjust fuel. It is no problem what I see to adjust the fuel table to fit with the signal from a 3 bar sensor. The oem map sensor reads some boost if I pass 17 Psi. Mcx delivered a bypass system to bypass boost before the map sensor. Over 17 psi I get a code 13. I need to have the possibility to run 20-22 psi. If I put in a 3 bar map sensor instead of the oem sensor, and then adjust the fuel table. Wouldnt that work ?
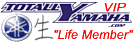

nate007
Lifetime Member
- Joined
- Dec 25, 2006
- Messages
- 2,770
- Reaction score
- 60
- Points
- 1,333
- Location
- Iowa City, Iowa
- Country
- USA
- Snowmobile
- 1. '06 Apex -twin screw
2. '04 Redline Revolt 800
3. '09 Nytro XTX - twin screw
I had to look up the Mega tune, as I'm not familiar with it, but regardless of what it is, as long as it is not a replacement for the entire factory ecu, do not replace the factory sensor!!
All Piggy back systems are simply "fooler" systems, that adjust the fuel by either modifying a signal from a factory sensor on the "IN" side of the factory ECU, or using additional sensors to modify fuel on the "OUT" side of the ecu.
If you have the factory ecu, don't change any factory sensors for ones that aren't exact replacements.
I would recommend calling MCXPress to see if that system will accept additional inputs from outside sources. I do see it has a wideband capability, but see if it has other "analog inputs", you can add a sensor into your intercooler(or equivalent) to read boost pressure and adjust accordingly.
All Piggy back systems are simply "fooler" systems, that adjust the fuel by either modifying a signal from a factory sensor on the "IN" side of the factory ECU, or using additional sensors to modify fuel on the "OUT" side of the ecu.
If you have the factory ecu, don't change any factory sensors for ones that aren't exact replacements.
I would recommend calling MCXPress to see if that system will accept additional inputs from outside sources. I do see it has a wideband capability, but see if it has other "analog inputs", you can add a sensor into your intercooler(or equivalent) to read boost pressure and adjust accordingly.
Stigapex
Suspended
If the map sensor input to the ecu is only for adjusting fuel I cant se a problem using another sensor. If the map sensor is used to adjust other things, I can see a problem. But nomather what mapsensor is used it still give signal 0-5 v. Mcxpress system bypass the oem mapsensor by not let it read boost. That mean , I think , from 0 psi and up the map sensor give a signal just under 5 v. What I see , the signal is the same from 0 psi and up.
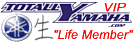

nate007
Lifetime Member
- Joined
- Dec 25, 2006
- Messages
- 2,770
- Reaction score
- 60
- Points
- 1,333
- Location
- Iowa City, Iowa
- Country
- USA
- Snowmobile
- 1. '06 Apex -twin screw
2. '04 Redline Revolt 800
3. '09 Nytro XTX - twin screw
Not necessarilly, What you will end up with is engine codes for MAP sensor voltage, because as the ecu proceses the signal it's also making sure it's within range given the rpm and throttle position.
For instance, (and I'm throwing ranges out there that aren't researched, but it'll give you the idea) a stock MAP sensor is calibrated to run on the vaccuum side only , which is what a stock machine sees, and is in essence, a "load" meter for the engine.
At idle, lets say the engine pulls 14"hg, and the map sensor is calibrated to tell the computer to inject fuel at a rate to run at idle, sending a signal of .75 volts. That same engine at higher rpm at WOT will be recieving a signal of 4.75v and telling the ecu to inject the correct ammount of fuel for a WOT run on a STOCK engine.
Now lets say you swap to a 3 bar sensor. It may read close to 3bar at idle with a .50-.65 volt range, but then when you run the engine up to highr rpm and boost, you may only be sending a signal to the ecu of 3.25v at 17psi of boost (4.75+ would be max at nearly 42psi), wich makes the ecu think you're a lower rpm and lighter throttle on a STOCK machine, which will make your engine go BOOM right away.
The signal is not the same from 0psi and up. The stock sensor is 0-5v on a NEGATIVE psi (vaccuum), and a 3 bar sensor has a small ammount of negative and mainly positive psi signal range. The factory sensor doesn't know what to do with pressure readings, as it puts it 'out of range'
Now I also know you say you are going to re-tune yout fuel maps, but with any aftermarket system that does not replace the factory ecu, it is either bypassing the ecu for certain things, or modifying the signal to the injectors FROM the ecu.
The most important thing, and I should've explained this earlier, is that the "language that nearly ever powersport engine runs on is referred to as Alpha N. It is a pre-programmed map for both fuel and spark. Every machine is loaded with the same map from the factory based on a broad testing range. This is why some sleds seem to run harder than others. Some engines need more fuel than others, but the way manufacturing works in smaller segments such as powersports and motorcycles, etc. they don't have the capability to tune each individual machine.
That being said, the maps are based on rpm and throttle position as the two primary resources. The other offsets like MAP, EGT, MPH are secondary, and have little to no effect on ecu functions beyond approx 4500-5000 rpm. (mph is very slight)
Basically, your MAP sensor helps with low engine speeds and idle, and when you're on boost and at higher rpm's, the ecu isn't even looking at it.
This is why control boxes like the ones MPI uses, etc, has a separate boost reference input by way of a small capilary tube directly to the piggy back. This is the "post ecu" MAP sensor. Does your system have a boost reference input for a small hose to attach??
From that sensor, it senses boost and directly modifies injection signal to richen the mixtures after the ecu has done it's job, and since the injectors don't send a signal back, the ecu thinks it's running normally. Nearly every ecu using high impedance injectors uses a negative trigger system, which means there is constant 12v to the injectors, and the ecu simply switches the ground on and off to activate the injector(s). This makes it so the ecu doesn't have to draw as much current.
What happens then is that the piggy back system sees that negative injector signal and knows how long the factory ecu is holding the ground (trigger) for, and using it's internal sensor calibrated for boost, (capillary tube) modifies the trigger signal to hold it open longer for a longer injector pulse.
Hope this doesn't confuse the heck out of you, but basically your MCX system is designed to run the boost functions and "fool" the oem ecu into thinknig that its running as a stock motor. There should be a boost reference input. I'd bet it's a hose, but if not, there should be a wired input which would be used to connect an auxillary sensor such as the 3bar you're talking about. That should go to the piggy back, and not to the factory ecu!
Now your earlier post mentioned that you're getting a code "13"? I don't have an '11 Apex service manual in front of me, but I do for the older Apex and Nytro. I'll go on the assumption that the '11 also has the Engine braking reduction system, which is the electric solenoid on the throttle bodies that opens them slightly upon deceleration?
The code 13 is for a map sensor, but I'm really thinking that when you reach that level of boost, you're getting some boost pressure back through the EBRS system, and when it basically pushes that solenoid open, it knows where that solenoid should be based on the factory MAP sensor, and since the factory MAP sensor is at its max range during boost, the movement of that triggers that code 13...
I'm going to go out on a limb here, but after thinking about this some more, I might suggest some one-way valves on the idle tubes on your TB's so the boost doesn't blow back through, and I'm betting that would fix it.
Either way DONT change your MAP sensor...
For instance, (and I'm throwing ranges out there that aren't researched, but it'll give you the idea) a stock MAP sensor is calibrated to run on the vaccuum side only , which is what a stock machine sees, and is in essence, a "load" meter for the engine.
At idle, lets say the engine pulls 14"hg, and the map sensor is calibrated to tell the computer to inject fuel at a rate to run at idle, sending a signal of .75 volts. That same engine at higher rpm at WOT will be recieving a signal of 4.75v and telling the ecu to inject the correct ammount of fuel for a WOT run on a STOCK engine.
Now lets say you swap to a 3 bar sensor. It may read close to 3bar at idle with a .50-.65 volt range, but then when you run the engine up to highr rpm and boost, you may only be sending a signal to the ecu of 3.25v at 17psi of boost (4.75+ would be max at nearly 42psi), wich makes the ecu think you're a lower rpm and lighter throttle on a STOCK machine, which will make your engine go BOOM right away.
The signal is not the same from 0psi and up. The stock sensor is 0-5v on a NEGATIVE psi (vaccuum), and a 3 bar sensor has a small ammount of negative and mainly positive psi signal range. The factory sensor doesn't know what to do with pressure readings, as it puts it 'out of range'
Now I also know you say you are going to re-tune yout fuel maps, but with any aftermarket system that does not replace the factory ecu, it is either bypassing the ecu for certain things, or modifying the signal to the injectors FROM the ecu.
The most important thing, and I should've explained this earlier, is that the "language that nearly ever powersport engine runs on is referred to as Alpha N. It is a pre-programmed map for both fuel and spark. Every machine is loaded with the same map from the factory based on a broad testing range. This is why some sleds seem to run harder than others. Some engines need more fuel than others, but the way manufacturing works in smaller segments such as powersports and motorcycles, etc. they don't have the capability to tune each individual machine.
That being said, the maps are based on rpm and throttle position as the two primary resources. The other offsets like MAP, EGT, MPH are secondary, and have little to no effect on ecu functions beyond approx 4500-5000 rpm. (mph is very slight)
Basically, your MAP sensor helps with low engine speeds and idle, and when you're on boost and at higher rpm's, the ecu isn't even looking at it.
This is why control boxes like the ones MPI uses, etc, has a separate boost reference input by way of a small capilary tube directly to the piggy back. This is the "post ecu" MAP sensor. Does your system have a boost reference input for a small hose to attach??
From that sensor, it senses boost and directly modifies injection signal to richen the mixtures after the ecu has done it's job, and since the injectors don't send a signal back, the ecu thinks it's running normally. Nearly every ecu using high impedance injectors uses a negative trigger system, which means there is constant 12v to the injectors, and the ecu simply switches the ground on and off to activate the injector(s). This makes it so the ecu doesn't have to draw as much current.
What happens then is that the piggy back system sees that negative injector signal and knows how long the factory ecu is holding the ground (trigger) for, and using it's internal sensor calibrated for boost, (capillary tube) modifies the trigger signal to hold it open longer for a longer injector pulse.
Hope this doesn't confuse the heck out of you, but basically your MCX system is designed to run the boost functions and "fool" the oem ecu into thinknig that its running as a stock motor. There should be a boost reference input. I'd bet it's a hose, but if not, there should be a wired input which would be used to connect an auxillary sensor such as the 3bar you're talking about. That should go to the piggy back, and not to the factory ecu!
Now your earlier post mentioned that you're getting a code "13"? I don't have an '11 Apex service manual in front of me, but I do for the older Apex and Nytro. I'll go on the assumption that the '11 also has the Engine braking reduction system, which is the electric solenoid on the throttle bodies that opens them slightly upon deceleration?
The code 13 is for a map sensor, but I'm really thinking that when you reach that level of boost, you're getting some boost pressure back through the EBRS system, and when it basically pushes that solenoid open, it knows where that solenoid should be based on the factory MAP sensor, and since the factory MAP sensor is at its max range during boost, the movement of that triggers that code 13...
I'm going to go out on a limb here, but after thinking about this some more, I might suggest some one-way valves on the idle tubes on your TB's so the boost doesn't blow back through, and I'm betting that would fix it.
Either way DONT change your MAP sensor...
Stigapex
Suspended
nate007 said:Not necessarilly, What you will end up with is engine codes for MAP sensor voltage, because as the ecu proceses the signal it's also making sure it's within range given the rpm and throttle position.
If its like that, I'll agree with you, then I can't use another mapsensor.
For instance, (and I'm throwing ranges out there that aren't researched, but it'll give you the idea) a stock MAP sensor is calibrated to run on the vaccuum side only , which is what a stock machine sees, and is in essence, a "load" meter for the engine.
At idle, lets say the engine pulls 14"hg, and the map sensor is calibrated to tell the computer to inject fuel at a rate to run at idle, sending a signal of .75 volts. That same engine at higher rpm at WOT will be recieving a signal of 4.75v and telling the ecu to inject the correct ammount of fuel for a WOT run on a STOCK engine.
Now lets say you swap to a 3 bar sensor. It may read close to 3bar at idle with a .50-.65 volt range, but then when you run the engine up to highr rpm and boost, you may only be sending a signal to the ecu of 3.25v at 17psi of boost (4.75+ would be max at nearly 42psi), wich makes the ecu think you're a lower rpm and lighter throttle on a STOCK machine, which will make your engine go BOOM right away.
The signal is not the same from 0psi and up. The stock sensor is 0-5v on a NEGATIVE psi (vaccuum), and a 3 bar sensor has a small ammount of negative and mainly positive psi signal range. The factory sensor doesn't know what to do with pressure readings, as it puts it 'out of range'
Now I also know you say you are going to re-tune yout fuel maps, but with any aftermarket system that does not replace the factory ecu, it is either bypassing the ecu for certain things, or modifying the signal to the injectors FROM the ecu.
The most important thing, and I should've explained this earlier, is that the "language that nearly ever powersport engine runs on is referred to as Alpha N. It is a pre-programmed map for both fuel and spark. Every machine is loaded with the same map from the factory based on a broad testing range. This is why some sleds seem to run harder than others. Some engines need more fuel than others, but the way manufacturing works in smaller segments such as powersports and motorcycles, etc. they don't have the capability to tune each individual machine.
That being said, the maps are based on rpm and throttle position as the two primary resources. The other offsets like MAP, EGT, MPH are secondary, and have little to no effect on ecu functions beyond approx 4500-5000 rpm. (mph is very slight)
Basically, your MAP sensor helps with low engine speeds and idle, and when you're on boost and at higher rpm's, the ecu isn't even looking at it.
This is why control boxes like the ones MPI uses, etc, has a separate boost reference input by way of a small capilary tube directly to the piggy back. This is the "post ecu" MAP sensor. Does your system have a boost reference input for a small hose to attach??
From that sensor, it senses boost and directly modifies injection signal to richen the mixtures after the ecu has done it's job, and since the injectors don't send a signal back, the ecu thinks it's running normally. Nearly every ecu using high impedance injectors uses a negative trigger system, which means there is constant 12v to the injectors, and the ecu simply switches the ground on and off to activate the injector(s). This makes it so the ecu doesn't have to draw as much current.
What happens then is that the piggy back system sees that negative injector signal and knows how long the factory ecu is holding the ground (trigger) for, and using it's internal sensor calibrated for boost, (capillary tube) modifies the trigger signal to hold it open longer for a longer injector pulse.
Hope this doesn't confuse the heck out of you, but basically your MCX system is designed to run the boost functions and "fool" the oem ecu into thinknig that its running as a stock motor. There should be a boost reference input. I'd bet it's a hose, but if not, there should be a wired input which would be used to connect an auxillary sensor such as the 3bar you're talking about. That should go to the piggy back, and not to the factory ecu!
Now your earlier post mentioned that you're getting a code "13"? I don't have an '11 Apex service manual in front of me, but I do for the older Apex and Nytro. I'll go on the assumption that the '11 also has the Engine braking reduction system, which is the electric solenoid on the throttle bodies that opens them slightly upon deceleration?
The code 13 is for a map sensor, but I'm really thinking that when you reach that level of boost, you're getting some boost pressure back through the EBRS system, and when it basically pushes that solenoid open, it knows where that solenoid should be based on the factory MAP sensor, and since the factory MAP sensor is at its max range during boost, the movement of that triggers that code 13...
I'm going to go out on a limb here, but after thinking about this some more, I might suggest some one-way valves on the idle tubes on your TB's so the boost doesn't blow back through, and I'm betting that would fix it.
Either way DONT change your MAP sensor...
I'm not sure if there is a EBRS system, but I'll assume that.
I'm not exactly sure where you mean I should put the one way valves.
Anyway
Thanks very much for a very good and long explanation
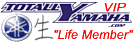

nate007
Lifetime Member
- Joined
- Dec 25, 2006
- Messages
- 2,770
- Reaction score
- 60
- Points
- 1,333
- Location
- Iowa City, Iowa
- Country
- USA
- Snowmobile
- 1. '06 Apex -twin screw
2. '04 Redline Revolt 800
3. '09 Nytro XTX - twin screw
The engine braking reduction system is part of the idle system, and it also opens the idle system slightly upon deceleration to reduce the engine braking. Its an electric valve on the throttle bodies instead of the older style thermostat valve that uses coolant to raise and lower idle speed during cold starts.
The larger vaccuum hoses that connect each individual throttle barrel to the central valve is what I'm talking about, and on the electric versions can be pushed open under higher boost situations. installing one way pcv style valves in those lines will help from having the boost pressure force that valve open, and should help keep that code from coming on.
I'm researching this a little further, I'll post back when I can.
The larger vaccuum hoses that connect each individual throttle barrel to the central valve is what I'm talking about, and on the electric versions can be pushed open under higher boost situations. installing one way pcv style valves in those lines will help from having the boost pressure force that valve open, and should help keep that code from coming on.
I'm researching this a little further, I'll post back when I can.