Turbo article by Erik Marklund , MC Xpress AB
4-stroke snowmobile engine – perfect for turbo?
Snowmobiles are mainly a recreational vehicle and are fun to ride.
You can find endless aftermarket parts for the most popular models to make them even more fun for the owner.
For many people the engine performance is the most interesting part.
And that’s what we think too.
Power increase methods
When the intake valves open in a naturally aspirated engine, it’s only the atmospheric pressure that fills up the cylinder with an air and fuel mixture. Due to flow losses and the short amount of time, the volumetric efficiency is often below 90%.
On a well-tuned racing engine, you can come up to just over 110 % in short rpm-ranges.
But with a compressor, the volumetric efficiency can be 200% or almost whatever you like.
You can of course enlarge the cylinder volume and rpm to achieve more flow through a naturally aspirated engine, but this can also be done with a boosted engine.
Different types of compressors
Two main types of compressors are available.
Supercharger -driven by a belt from the crankshaft of the engine
Turbocharger -driven by the exhaust outlet from the engine.
Why do all the car and truck manufacturers almost exclusively use turbochargers instead of superchargers?
*A turbocharged engine produces more power and torque at a certain boost.
You can expect that at least 30% of the power increase that the supercharger makes, needs to drive, for example, a roots compressor. For instance:
If you have an RX1 with stock 140 hp, you install a turbo and get 260 hp (=120 hp power increase) you could expect about 80 hp increase if it had been a supercharger because it takes 40 hp to drive it.
If you design a turbo system in a proper way, the energy that drives the turbine wheel is free. About 45 % of the energy from the fuel is getting lost through the exhaust system on a naturally aspirated engine.
On a turbo engine some of the energy from the exhaust pulses and some of the heat drives the turbine wheel of the turbo.
*A modern turbocharger is very reliable and normally lasts longer than the engine itself.
*A turbo reduces noise on both intake and exhaust side.
*At high altitude, the turbocharger compensates (if it’s designed big enough) the lower density of the air and the engine doesn’t loose much performance.
* Turbochargers are made in large quantities and this makes them less expensive.
*A turbocharger has normally higher adiabatic efficiency than a supercharger.
It means that it’s creating less heat to the pressurized intake air =better reliability and power.
A turbocharged engine is smaller, lighter and consumes less fuel than a naturally aspirated engine with the same power.
The benefits with a supercharged engine compared to a turbocharged are that the stock exhaust system can be used, but this also makes the system heavier. Some super chargers make boost from low rpm with very quick response from the start.
But the low rpm-boost can also be a problem when you are boon docking in the trees.
Car manufacturers tend to make systems that turn off the compressor at slow speed to get less fuel consumption, preventing the engine from building up heat and making the riding more enjoyable.
Turbo chargers.
You can find a lot of different turbo chargers on the market.
What’s common is that they all have an exhaust turbine, bearing section and compressor.
The choice of the turbo is very important. The compressor must be able to pump the air you require even at high altitude. The adiabatic efficiency must be high.
The turbine housing and wheel would give as low backpressure in the exhaust manifold as possible (=bigger is better) but still start to boost early (=smaller is better).
Sometimes twin flow entry turbine housing is the best choice. It starts to boost earlier but creates more backpressure at high rpm. If you then choose a bigger twin flow entry turbine housing, it can sometimes both start to boost earlier and also give less backpressure.
Ball bearing turbos have less friction at low speed and start to boost earlier but have more friction at high speed. Sleeve bearing turbos have the reputation to be more reliable.
The turbine wheel and shaft needs to be light to get quicker response.
Boost control systems.
Two different systems are used today to control the turbo pressure on gasoline engines.
Waste gate controlled is the most common. When a certain pressure has been reached, a valve opens and lets some exhaust gases pass right out to the exhaust system without passing through the turbine wheel. The turbo pressure can easily be adjusted by just changing the preload of a spring.
The other system has a turbine housing with small guide vanes inside (variable turbine geometry VTG). The flow area in the turbine is changed to obtain required pressure.
The VTG system can build up boost earlier and still give the same top end power.
Reliability problems due to high heat have made them more popular on diesel engines.
Two stroke and turbo
Almost any engine can be turbocharged. The two-stroke engine can also be turbocharged but is more sensitive to backpressure in the exhaust system and due to reliability problems and rather cold exhaust gases not as suitable to turbo charge as a four-stroke engine.
Power increase with turbo
At 14 Psi turbo pressure you can expect twice as much power than stock.
MC Xpress RX1 normal turbo kit creates 240 hp DIN at 10 PSi of boost.
We have dyno tested the RX1 engine up to 404 hp DIN at 26 PSi with a bigger turbo.
Detonation.
The most common reason for failure on a turbo engine is heating problems due to detonation.
Temperature, pressure, timing and fuel quality are the four parameters that are important to control, to avoid detonation.
*The temperature in the combustion chamber should be as cool as possible before the spark.
Rich air fuel mixture (Lambda 0,8 to 0,85), cool intake air and low backpressure in the exhaust system are important.
*The pressure in the combustion chamber should not be too high. The turbo pressure and the compression ratio determine the pressure. If you lower the compression ratio, the more turbo pressure you can set before detonation. You can run about 6 PSi of boost with stock compression ratio on the Yamaha RS/RX1 and Apex engines with high octane pump gas.
*A high rpm engine can use higher turbo pressure. This makes the modern 4 stroke snowmobile and motorcycle engines very suitable for turbo charging.
* Higher octane allows higher turbo pressure.
The shape inside the combustion chamber is also important. On a four-stroke turbo engine –especially when high turbo pressure is used- the squish area is not important.
It is better to use rather flat pistons and remove the squish area.
A thick head gasket works great together with stock pistons.
Old formula one-turbo engines had no squish area.
We removed the squish area on the Suzuki GSXR 1300 turbo that won the famous dyno shootout competition in Florida this year.
The power was measured to 701 hp on the rear wheel.
We tested this engine a lot with our dyno before it was sent to the USA.
Intercooler.
The idea with turbo charging is to get as high density as possible on the intake air.
When air is compressed, the temperature rises. (Law of Physics). When it’s compressed through a turbo or supercharger, it gets even hotter because the adiabatic efficiency is not
100 %. It is 75 % if it’s a modern turbo and normally not higher than 50-60 % with a super-charger.
Air that’s getting hot is expanding (lower density) and this is the opposite of what we want.
At 14 Psi turbo pressure you can expect the intake air temperature is about 120 deg C. The hot compressed air can be cooled down through an intercooler placed between the turbo and the intake plenum. The air will get a higher density (= more oxygen in each cylinder) but also allow you to use higher turbo pressure.
Air/fuel ratio
On a gasoline engine, the air fuel ratio is very important.
A too rich mixture will cause less performance and sometimes the engine can misfire.
If the mixture is too lean, it will cause an engine failure.
High revving engines with 4 or 5 valves per cylinder like the new Yamaha RS, RX1 and Apex engines demands a rather rich mixture. At full throttle and turbo pressure the A/F ratio should be between 11.5 to 12.5:1. The exhaust temperature will then be about 850° C.
It is possible to blow pressurized air through the carburettors on the Yamaha snowmobiles.
The air/fuel mixture can be adjusted by adjusting the jets and pressures inside the carbs.
The fuel pressure to the carbs should be slightly higher (about 3 PSi) than the turbo pressure.
This can be made by installing a special kind of fuel pressure regulator and a fuel pump that’s big enough, considering, flow and pressure.
Fuel injection is used on the new Apex. When installing a turbo, much more fuel is needed.
The stock injectors can’t deliver much more fuel than they already do at full throttle and rpm.
We think that the best way to solve the fuel demand is to install extra injectors in the plenum controlled by an external control box. The stock EFI-box, with the entire mapping that Yamaha has developed, is left un-touched. When turbo pressure arrives, fuel will start to come through the external injectors. The injector’s location close to the velocity stacks inside the plenum and far away from the intake valves are superior. The vaporising of the fuel is much better with higher performance as a result.
Snowmobiles are probably the most suitable vehicles for turbo charging. You want them to be powerful even at high altitude. You want them to be light and reliable.
And finally, one of the most important things: The clutch on a snowmobile makes the turbo lag disappear.
We can expect to see more 4 stroke turbo sleds from the manufacturers, just wait and see.
I think the future is already here!
HAVE FUN AND RIDE SAFE.
Erik Marklund, MC Xpress AB
4-stroke snowmobile engine – perfect for turbo?
Snowmobiles are mainly a recreational vehicle and are fun to ride.
You can find endless aftermarket parts for the most popular models to make them even more fun for the owner.
For many people the engine performance is the most interesting part.
And that’s what we think too.
Power increase methods
When the intake valves open in a naturally aspirated engine, it’s only the atmospheric pressure that fills up the cylinder with an air and fuel mixture. Due to flow losses and the short amount of time, the volumetric efficiency is often below 90%.
On a well-tuned racing engine, you can come up to just over 110 % in short rpm-ranges.
But with a compressor, the volumetric efficiency can be 200% or almost whatever you like.
You can of course enlarge the cylinder volume and rpm to achieve more flow through a naturally aspirated engine, but this can also be done with a boosted engine.
Different types of compressors
Two main types of compressors are available.
Supercharger -driven by a belt from the crankshaft of the engine
Turbocharger -driven by the exhaust outlet from the engine.
Why do all the car and truck manufacturers almost exclusively use turbochargers instead of superchargers?
*A turbocharged engine produces more power and torque at a certain boost.
You can expect that at least 30% of the power increase that the supercharger makes, needs to drive, for example, a roots compressor. For instance:
If you have an RX1 with stock 140 hp, you install a turbo and get 260 hp (=120 hp power increase) you could expect about 80 hp increase if it had been a supercharger because it takes 40 hp to drive it.
If you design a turbo system in a proper way, the energy that drives the turbine wheel is free. About 45 % of the energy from the fuel is getting lost through the exhaust system on a naturally aspirated engine.
On a turbo engine some of the energy from the exhaust pulses and some of the heat drives the turbine wheel of the turbo.
*A modern turbocharger is very reliable and normally lasts longer than the engine itself.
*A turbo reduces noise on both intake and exhaust side.
*At high altitude, the turbocharger compensates (if it’s designed big enough) the lower density of the air and the engine doesn’t loose much performance.
* Turbochargers are made in large quantities and this makes them less expensive.
*A turbocharger has normally higher adiabatic efficiency than a supercharger.
It means that it’s creating less heat to the pressurized intake air =better reliability and power.
A turbocharged engine is smaller, lighter and consumes less fuel than a naturally aspirated engine with the same power.
The benefits with a supercharged engine compared to a turbocharged are that the stock exhaust system can be used, but this also makes the system heavier. Some super chargers make boost from low rpm with very quick response from the start.
But the low rpm-boost can also be a problem when you are boon docking in the trees.
Car manufacturers tend to make systems that turn off the compressor at slow speed to get less fuel consumption, preventing the engine from building up heat and making the riding more enjoyable.
Turbo chargers.
You can find a lot of different turbo chargers on the market.
What’s common is that they all have an exhaust turbine, bearing section and compressor.
The choice of the turbo is very important. The compressor must be able to pump the air you require even at high altitude. The adiabatic efficiency must be high.
The turbine housing and wheel would give as low backpressure in the exhaust manifold as possible (=bigger is better) but still start to boost early (=smaller is better).
Sometimes twin flow entry turbine housing is the best choice. It starts to boost earlier but creates more backpressure at high rpm. If you then choose a bigger twin flow entry turbine housing, it can sometimes both start to boost earlier and also give less backpressure.
Ball bearing turbos have less friction at low speed and start to boost earlier but have more friction at high speed. Sleeve bearing turbos have the reputation to be more reliable.
The turbine wheel and shaft needs to be light to get quicker response.
Boost control systems.
Two different systems are used today to control the turbo pressure on gasoline engines.
Waste gate controlled is the most common. When a certain pressure has been reached, a valve opens and lets some exhaust gases pass right out to the exhaust system without passing through the turbine wheel. The turbo pressure can easily be adjusted by just changing the preload of a spring.
The other system has a turbine housing with small guide vanes inside (variable turbine geometry VTG). The flow area in the turbine is changed to obtain required pressure.
The VTG system can build up boost earlier and still give the same top end power.
Reliability problems due to high heat have made them more popular on diesel engines.
Two stroke and turbo
Almost any engine can be turbocharged. The two-stroke engine can also be turbocharged but is more sensitive to backpressure in the exhaust system and due to reliability problems and rather cold exhaust gases not as suitable to turbo charge as a four-stroke engine.
Power increase with turbo
At 14 Psi turbo pressure you can expect twice as much power than stock.
MC Xpress RX1 normal turbo kit creates 240 hp DIN at 10 PSi of boost.
We have dyno tested the RX1 engine up to 404 hp DIN at 26 PSi with a bigger turbo.
Detonation.
The most common reason for failure on a turbo engine is heating problems due to detonation.
Temperature, pressure, timing and fuel quality are the four parameters that are important to control, to avoid detonation.
*The temperature in the combustion chamber should be as cool as possible before the spark.
Rich air fuel mixture (Lambda 0,8 to 0,85), cool intake air and low backpressure in the exhaust system are important.
*The pressure in the combustion chamber should not be too high. The turbo pressure and the compression ratio determine the pressure. If you lower the compression ratio, the more turbo pressure you can set before detonation. You can run about 6 PSi of boost with stock compression ratio on the Yamaha RS/RX1 and Apex engines with high octane pump gas.
*A high rpm engine can use higher turbo pressure. This makes the modern 4 stroke snowmobile and motorcycle engines very suitable for turbo charging.
* Higher octane allows higher turbo pressure.
The shape inside the combustion chamber is also important. On a four-stroke turbo engine –especially when high turbo pressure is used- the squish area is not important.
It is better to use rather flat pistons and remove the squish area.
A thick head gasket works great together with stock pistons.
Old formula one-turbo engines had no squish area.
We removed the squish area on the Suzuki GSXR 1300 turbo that won the famous dyno shootout competition in Florida this year.
The power was measured to 701 hp on the rear wheel.
We tested this engine a lot with our dyno before it was sent to the USA.
Intercooler.
The idea with turbo charging is to get as high density as possible on the intake air.
When air is compressed, the temperature rises. (Law of Physics). When it’s compressed through a turbo or supercharger, it gets even hotter because the adiabatic efficiency is not
100 %. It is 75 % if it’s a modern turbo and normally not higher than 50-60 % with a super-charger.
Air that’s getting hot is expanding (lower density) and this is the opposite of what we want.
At 14 Psi turbo pressure you can expect the intake air temperature is about 120 deg C. The hot compressed air can be cooled down through an intercooler placed between the turbo and the intake plenum. The air will get a higher density (= more oxygen in each cylinder) but also allow you to use higher turbo pressure.
Air/fuel ratio
On a gasoline engine, the air fuel ratio is very important.
A too rich mixture will cause less performance and sometimes the engine can misfire.
If the mixture is too lean, it will cause an engine failure.
High revving engines with 4 or 5 valves per cylinder like the new Yamaha RS, RX1 and Apex engines demands a rather rich mixture. At full throttle and turbo pressure the A/F ratio should be between 11.5 to 12.5:1. The exhaust temperature will then be about 850° C.
It is possible to blow pressurized air through the carburettors on the Yamaha snowmobiles.
The air/fuel mixture can be adjusted by adjusting the jets and pressures inside the carbs.
The fuel pressure to the carbs should be slightly higher (about 3 PSi) than the turbo pressure.
This can be made by installing a special kind of fuel pressure regulator and a fuel pump that’s big enough, considering, flow and pressure.
Fuel injection is used on the new Apex. When installing a turbo, much more fuel is needed.
The stock injectors can’t deliver much more fuel than they already do at full throttle and rpm.
We think that the best way to solve the fuel demand is to install extra injectors in the plenum controlled by an external control box. The stock EFI-box, with the entire mapping that Yamaha has developed, is left un-touched. When turbo pressure arrives, fuel will start to come through the external injectors. The injector’s location close to the velocity stacks inside the plenum and far away from the intake valves are superior. The vaporising of the fuel is much better with higher performance as a result.
Snowmobiles are probably the most suitable vehicles for turbo charging. You want them to be powerful even at high altitude. You want them to be light and reliable.
And finally, one of the most important things: The clutch on a snowmobile makes the turbo lag disappear.
We can expect to see more 4 stroke turbo sleds from the manufacturers, just wait and see.
I think the future is already here!
HAVE FUN AND RIDE SAFE.
Erik Marklund, MC Xpress AB
Mountaintech
TY 4 Stroke God
Awesome post, right from the mouth of the master!!
peteracing
Expert
What more do you want to hear blower fans!
Nice, comphrehensive text
Actually, i am very surprized that the manufacturers dont jump in
turbocharging. Could it be because big 4 used to have turbobikes and
they didn't sell much?...

Nice, comphrehensive text

Actually, i am very surprized that the manufacturers dont jump in
turbocharging. Could it be because big 4 used to have turbobikes and
they didn't sell much?...
slymax
TY 4 Stroke Junkie
I know who's kit I'm running
:ORC



sledheadgeorge
TY 4 Stroke God
- Joined
- Apr 28, 2003
- Messages
- 1,619
- Reaction score
- 54
- Points
- 1,008
- Location
- Ontario
- Country
- Canada
- Snowmobile
- Which one? I have 6
Excellent post.
I think all the non turbo sledheads here now have a comprehensive understanding of the technical end of " BOOST".
I wounder if we could fit one of those 701hp GSXR 1300cc engine in my sled.
But the two most important statements I agree with are...
#1 "4-stroke snowmobile engine - perfect for turbo"
#2 "Snowmobiles are .....the most suitable vehicles for turbo charging." :ORC

I think all the non turbo sledheads here now have a comprehensive understanding of the technical end of " BOOST".
I wounder if we could fit one of those 701hp GSXR 1300cc engine in my sled.

But the two most important statements I agree with are...
#1 "4-stroke snowmobile engine - perfect for turbo"

#2 "Snowmobiles are .....the most suitable vehicles for turbo charging." :ORC

Buster696
VIP Member
Great post Erik...
--Buster696--



--Buster696--

RTX
TY 4 Stroke God
- Joined
- Mar 31, 2005
- Messages
- 1,796
- Reaction score
- 482
- Points
- 1,338
- Location
- massachusetts / maine
- Country
- USA
- Snowmobile
- 2014 viper rtx
2006 apex rtx
this is a question not a slam at turbos so please dont attack me.
If turbos are as good / efficient as was stated.
why do most dragracing vehicles use superchargers.
If turbos are as good / efficient as was stated.
why do most dragracing vehicles use superchargers.
peteracing
Expert
Quick response and also sound! the sound of blown (roots) engines
attracs lots of people at races!. Turbos are banned everywhere ( f-1,
indy, because of TOO MUCH power!
attracs lots of people at races!. Turbos are banned everywhere ( f-1,
indy, because of TOO MUCH power!

woodsrider
TY 4 Stroke Junkie
- Joined
- Feb 17, 2005
- Messages
- 669
- Reaction score
- 11
- Points
- 893
- Location
- Lewiston, ID
- Country
- USA
- Snowmobile
- 2017 YZ450FX1 Moto-Trax 137 Mountain Kit
My theory as to why the manufacturers do not build high hp turbo sleds is they are afraid of product liability issues if someone were to get killed on a 200+hp machine. John Q Public probably has no business owning one of these sleds. :ORC
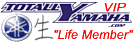

1CrazySledder
Lifetime Member
- Joined
- Aug 11, 2005
- Messages
- 2,006
- Reaction score
- 4
- Points
- 1,068
- Location
- Cartersville, GA.
- Country
- USA
- Snowmobile
- None, looking now!
woodsrider said:My theory as to why the manufacturers do not build high hp turbo sleds is they are afraid of product liability issues if someone were to get killed on a 200+hp machine. John Q Public probably has no business owning one of these sleds. :ORC
I agree. Plus the public that don't like sleds and just want something to complain about ( enviromentalists )would attack the big 4 simply for building these type of sleds. Plus the manf. want to keep the consumer price down. Personally, I would buy a stock turbo powered sled from Yamaha. We all know it would be the best, period.
1cs
Similar threads
- Replies
- 0
- Views
- 916
- Replies
- 1
- Views
- 408
-
This site uses cookies to help personalise content, tailor your experience and to keep you logged in if you register.
By continuing to use this site, you are consenting to our use of cookies.