jesperholmstedt
Newbie
- Joined
- Jan 31, 2022
- Messages
- 10
- Age
- 35
- Location
- Jakobstad
- Country
- Other
- Snowmobile
- RS Venture TF -06
I am in the middle of some service before the season starts and I noticed on the driven axle that one nut was completely loose and just spinning on the axle. Attached an image plus I marked the nut on the exploded view image.
The problem here is I can't find a way to tighten this nut since the threads it's supposed to (I guess?) thread on to spins along when I try to tighten it. Am I missing something here?
I have no idea for how long this thing's been loose, what could be the consequences of driving with the nut not tightened properly?
The problem here is I can't find a way to tighten this nut since the threads it's supposed to (I guess?) thread on to spins along when I try to tighten it. Am I missing something here?
I have no idea for how long this thing's been loose, what could be the consequences of driving with the nut not tightened properly?
Attachments
fastdave
Extreme
- Joined
- Oct 20, 2011
- Messages
- 55
- Age
- 68
- Location
- Chippewa Falls, WI
- Country
- USA
- Snowmobile
- 2007 Yamaha RS Vector GT
The first season (2010) I got my 2007 RS Vector GT that same nut came loose. We were riding along and I heard strange noise. It took my buddy and me about a half hour on the trail side to get it threaded back on. We used a channel locks I think and a screwdriver to apply pressure. It was so long ago that all I remember for sure was that it was really hard to get it started and it took 2 guys to get it done. I cranked it down really good and it's never come loose again.I am in the middle of some service before the season starts and I noticed on the driven axle that one nut was completely loose and just spinning on the axle. Attached an image plus I marked the nut on the exploded view image.
The problem here is I can't find a way to tighten this nut since the threads it's supposed to (I guess?) thread on to spins along when I try to tighten it. Am I missing something here?
I have no idea for how long this thing's been loose, what could be the consequences of driving with the nut not tightened properly?
Last edited:
jesperholmstedt
Newbie
- Joined
- Jan 31, 2022
- Messages
- 10
- Age
- 35
- Location
- Jakobstad
- Country
- Other
- Snowmobile
- RS Venture TF -06
The first season (2010) I got my 2007 RS Vector GT that same nut came loose. We were riding along and I heard strange noise. It took my buddy and me about a half hour on the trail side to get it threaded back on. We used a channel locks I think and a screwdriver to apply pressure. It was so long ago that all I remember for sure was that it was really hard to get it started and it took 2 guys to get it done. I cranked it down really good and it's never come loose again.
The thing is I can't seem to figure out how to grab the threaded piece with a polygrip, from what I remember (not having the sled at home and being able to check right now) the threaded thing does not go through the metal plate?
So if I grab it, that has to be on the threads itself, which does not feel good at all.
But are the threaded piece supposed to spin on the axle in the first place?

RobX-1
VIP Member
- Joined
- Apr 13, 2003
- Messages
- 2,188
- Location
- Coldwater, OH
- Country
- USA
- Snowmobile
- 18 50th Apex XT-X, 08 40th Apex LTX GT, 08 40th Nytro RTX, & 03 RX-1
The threaded sleeve that slides onto the jack shaft and into the bearing's inner diamter that the nut goes on to is meant to prevent the jack shaft bearing from coming loose/unseated. At least with the Apex, they later on switched to a housing for the jack shaft bearing that bolted onto the bulkhead.
Tpypically, the sleeve while on the jack shaft does not want to pass thru the bearing's inner diameter and hence why you use the nut on the backside to tigthen the sleeve (ie. drive it deep into the bearing's inner diameter. This is what is suppose to keep the sleeve from spinning. I wonder with it being loose and having spun on the jack shaft, that either the sleeve and/or jack shaft have worn some and tolerances are not what they should be. I would try pushing the threaded sleeve from the front side deeper into the bearing's inner diameter to see if that causes it to tighten and not spin as you tighten; unless its so worn you can pushe the threaded sleeve all the way thru the jack shaft bearing.
Tpypically, the sleeve while on the jack shaft does not want to pass thru the bearing's inner diameter and hence why you use the nut on the backside to tigthen the sleeve (ie. drive it deep into the bearing's inner diameter. This is what is suppose to keep the sleeve from spinning. I wonder with it being loose and having spun on the jack shaft, that either the sleeve and/or jack shaft have worn some and tolerances are not what they should be. I would try pushing the threaded sleeve from the front side deeper into the bearing's inner diameter to see if that causes it to tighten and not spin as you tighten; unless its so worn you can pushe the threaded sleeve all the way thru the jack shaft bearing.
jesperholmstedt
Newbie
- Joined
- Jan 31, 2022
- Messages
- 10
- Age
- 35
- Location
- Jakobstad
- Country
- Other
- Snowmobile
- RS Venture TF -06
Ash, so the threaded sleeve is put in from the clutch side so to speak, for some reason I always thought it was the other way around and that is why it did not make any sense.The threaded sleeve that slides onto the jack shaft and into the bearing's inner diamter that the nut goes on to is meant to prevent the jack shaft bearing from coming loose/unseated. At least with the Apex, they later on switched to a housing for the jack shaft bearing that bolted onto the bulkhead.
Tpypically, the sleeve while on the jack shaft does not want to pass thru the bearing's inner diameter and hence why you use the nut on the backside to tigthen the sleeve (ie. drive it deep into the bearing's inner diameter. This is what is suppose to keep the sleeve from spinning. I wonder with it being loose and having spun on the jack shaft, that either the sleeve and/or jack shaft have worn some and tolerances are not what they should be. I would try pushing the threaded sleeve from the front side deeper into the bearing's inner diameter to see if that causes it to tighten and not spin as you tighten; unless its so worn you can pushe the threaded sleeve all the way thru the jack shaft bearing.
So if I remove the secondary clutch I might be able to push the threaded sleeve further in and by that lock it in place. IF not too worn.
I will look into it as soon as possible. Thank you!

RobX-1
VIP Member
- Joined
- Apr 13, 2003
- Messages
- 2,188
- Location
- Coldwater, OH
- Country
- USA
- Snowmobile
- 18 50th Apex XT-X, 08 40th Apex LTX GT, 08 40th Nytro RTX, & 03 RX-1
Yes, sleeve is installed from the clutch side. Also, what makes the jack shaft bearing unique is the fact that it has a tapered inner race so when that sleeve is inserted/slid into into the inner race of the bearing from the front side, it is not suppose to pass thru the inner race of the jack shaft bearing; will get close to being flush with the inner race though. If there's still a considerable amount of the sleeve exposed from the clutch side, I would think tapping the sleeve in should snug it up enough for it not to spin to then allow you to tighten the nut.
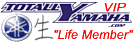

- Joined
- Jun 1, 2004
- Messages
- 7,740
- Location
- sudbury on
- Country
- Canada
- Snowmobile
- 2016 apex xtx
2011 apex xtx
2009 phaser rtx/x
1997 et410t/r
1988 vk 540
also if it has been running on the shaft long enough, you might have to take it apart to replace it as there might be no threads left in the nut if it doesn't thread on.
jesperholmstedt
Newbie
- Joined
- Jan 31, 2022
- Messages
- 10
- Age
- 35
- Location
- Jakobstad
- Country
- Other
- Snowmobile
- RS Venture TF -06
Thanks for the input I never thought about that either.also if it has been running on the shaft long enough, you might have to take it apart to replace it as there might be no threads left in the nut if it doesn't thread on.
It was really hard to the get the first couple of threads on but after a while I managed to get it on. But after just a couple of "turns" (by that I mean: knocks with a screwdriver to turn it) I noticed that the whole threaded thing spins along with it.
I guess the nut is supposed to screw on quite easy because I cannot see any locking mechanism on it - so I guess that means it has been spinning for a while...
Well, next time Im heading to the garage I will try with the polygrip and see if I manage to hold it still. Otherwise I guess I have to open it..
I guess that means removing the bearing also?
Similar threads
- Replies
- 21
- Views
- 4K
- Replies
- 0
- Views
- 817
- Replies
- 21
- Views
- 5K
- Replies
- 6
- Views
- 2K