Hi. Has anyone experienced any problems with their steel sleeved block? Last season i broke a piston when running out of meth and sent the engine block for repair ( steel sleeves ) due to a damage in the cylinder bore. When i got the parts back a while age the block is so twisted that the crank would´nt even fit in the main bearings. I not lying when i say that i have apprx, 1mm left until the crank reaches the radius on the bottom of the bearing. When placing the crank in the bottom half of the engine block there´s no problem, and the crank rotates nice and easy! So the issue is in the upper half of the block. And the problem has clearly appeared when steel sleeving, because during deassembly we rotated the crank several turns in the block without issues. All bearings are fine ( not a scratch ).
Just like to know how i should move on with this project. In my eyes the block is destroyed.
Thanks.
/Svante.
Just like to know how i should move on with this project. In my eyes the block is destroyed.
Thanks.
/Svante.
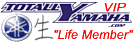

I wonder if the head would be enough to straighten it? If it does it must mean all strength is gone from block when they cut it for the sleeves. Its obviously not a good thing to deal with.
I believe its too much material between the head and mains to make a difference. I spoke to the company and they want me to send the block back for repair.
/Svante
/Svante
givemeaboost
TY 4 Stroke Junkie
- Joined
- Dec 5, 2003
- Messages
- 689
- Reaction score
- 24
- Points
- 1,028
- Location
- Great Falls, MT.
- Country
- USA
- Snowmobile
- 03 Rx1 Turbo
- LOCATION
- Great Falls,MT
Did you send both halves of the block assembly when they bored it ? It would have to be all bolted together to do any machining on it.
Ken........
Ken........
Yes i did. But clearly they did'nt have the block assembled when working on it. I noticed some minor marks on the surface on the upper half, but the marks wasnt on the bottom half. If something has been squeezed in between the marks should been on both planes. Im pretty sure that the upper half have been placed alone in the hydraulic press when installing the sleeves, causing the block half to bend. I have measured all 3 planes in a calibrated Carl Zeiss measure machine at work. The upper plane ( cylinder head plane on block ) has a total max/min difference of 0.068mm. The lower half plane on block ( Yamaha original ) total diff 0.017mm and the lower plane on upper half of block ( after the sleeves was installed ) total diff of 0.226mm. No wonder the crank would'nt spin, or even fit.. I have sent the block to the company again and they say they will fix the problem. Im curious how!
Thanks for the replies.
/Svante
Thanks for the replies.
/Svante
Who's block was it? I have had similar issues in the past very discouraging!
Its my engine block!
The only one i have
/Svante
The only one i have

/Svante
I meant who sleeved it and did the machine work!
TWIN TURBO
Expert
- Joined
- Aug 30, 2005
- Messages
- 317
- Reaction score
- 2
- Points
- 721
- Location
- Chicago IL.
- Website
- www.powerbygns.com
Sleeving Apex Blocks is for sure something that requires proper machine techniques. You can't install sleeves with the bottom half of the case installed, but I don't believe that was your problem. The block and lower case half do go in a oven with a torque plate installed imediately after sleeves are installed and then allowed to cool very slowly with everything torqued in place. One thing I know for sure is finish honing must be done with torque plate installed. It's all a long process that must be followed very closely if you want to keep all the stresses kept to a minimum, and don't get the block too hot as that will also add to the problem. The alinement of the main bores and the roundness of the cylinder bores are the most common source of issues.
The block main bores can be alined honed if it's not too far out of alinement.
The block main bores can be alined honed if it's not too far out of alinement.

How far out of alignment? 
I got the block back with the crank installed, i suppose they wanted to show me that they got it spinning.
I began measure the main bores and found that i have a ovality of the diameter from +0.02 to +0.25mm. When i stated that the block is junk i got the responce that the engine would probably work fine with the increased bearing clearance LOL, and that they know the block doesn't add up to Yamahas specification on bearing clearance. But still they say it will work?
I dont even want to touch it, its a waste to spend new gaskets/bearings on something that out of spec. Or what do you think?
/Svante

I got the block back with the crank installed, i suppose they wanted to show me that they got it spinning.
I began measure the main bores and found that i have a ovality of the diameter from +0.02 to +0.25mm. When i stated that the block is junk i got the responce that the engine would probably work fine with the increased bearing clearance LOL, and that they know the block doesn't add up to Yamahas specification on bearing clearance. But still they say it will work?
I dont even want to touch it, its a waste to spend new gaskets/bearings on something that out of spec. Or what do you think?
/Svante
TWIN TURBO
Expert
- Joined
- Aug 30, 2005
- Messages
- 317
- Reaction score
- 2
- Points
- 721
- Location
- Chicago IL.
- Website
- www.powerbygns.com
Svante said:How far out of alignment?
I got the block back with the crank installed, i suppose they wanted to show me that they got it spinning.
I began measure the main bores and found that i have a ovality of the diameter from +0.02 to +0.25mm. When i stated that the block is junk i got the responce that the engine would probably work fine with the increased bearing clearance LOL, and that they know the block doesn't add up to Yamahas specification on bearing clearance. But still they say it will work?
I dont even want to touch it, its a waste to spend new gaskets/bearings on something that out of spec. Or what do you think?
/Svante
Without getting to technical here my first question is ? Ovality or misalinement?
The standard main diameter is 1.4572" or 37.00 mm.
If the cases are not alined properly that has to be because the dowels are holding the cases incorectly. You can try moving the dowels to the other holes, there are 2 sets of dowel holes in all Apex or RX1 blocks. I have seen them from factory in different locations. The standard location is under the corners where the case bolts are. You may try moving them to where the main bearings are, sometimes you will see a improvement in the alinment by changing dowel locations.
I made a ground and polished heat treated bar that when first assembling cases, I install the bar and torque the main bolts. then I can slide the bar in and out to check for binding and main misalinement. Then I slide bar out and with a precision dial bore gauge I can measure the REAL diameter of the main bearings. With that the difference between those numbers and the diameter of the crank is the ACTUAL bearing clearence.
If the housing bore Vertical diameter is correct and you are able to turn the crank BY HAND with the main bolts torqued to spec. then it should be OK. You can increase the clearence a little but I would keep it at no more than .0025" or .06mm.
If you wnat me to look at it for you you can send it to me and I can determine if it is useable as is or if aline boring is required. $150.00USD for aline boring plus checking time.
Hope this helps
No the main bores has an ovality of,, im not lying 0.23mm. I calibrated and zeroed the gauge at 37mm. You will se by the pictures that the mains is way off. This is after i got the block back the second time ( after they align honed it ). Measured in 45deg intervals around through the whole block, they where all about the same.
Still they say it will run. I say it will probably run for seconds or maybe minutes before it breaks down. Funny thing is the responce i get after sending them the reports from our Carl Zeiss measure machine, all my other measures, and pictures of how bad it is they seem to not care at all. Looks like they want me to buy another engine and throw this pile of junk i just wasted $2300 on in the garbage.
The Carls zeiss reported theese numbers
Flatness top half of block ( cylinder head side ) 0.066mm
Flatness bottom half of block ( main bearing side ) 0.017mm
Flatness top half of block ( main bearing side, after steel sleeve install ) 0.226mm.
If i did´nt live on the other side of planet earth i would send you the block
but right now the shipment is more expensive than the whole block itself LOL.
/Svante.
Still they say it will run. I say it will probably run for seconds or maybe minutes before it breaks down. Funny thing is the responce i get after sending them the reports from our Carl Zeiss measure machine, all my other measures, and pictures of how bad it is they seem to not care at all. Looks like they want me to buy another engine and throw this pile of junk i just wasted $2300 on in the garbage.
The Carls zeiss reported theese numbers
Flatness top half of block ( cylinder head side ) 0.066mm
Flatness bottom half of block ( main bearing side ) 0.017mm
Flatness top half of block ( main bearing side, after steel sleeve install ) 0.226mm.
If i did´nt live on the other side of planet earth i would send you the block

/Svante.
Attachments
svante send the block to
http://www.vsmotor.no/
http://www.vsmotor.no/
TWIN TURBO
Expert
- Joined
- Aug 30, 2005
- Messages
- 317
- Reaction score
- 2
- Points
- 721
- Location
- Chicago IL.
- Website
- www.powerbygns.com
I understand about the shipping of the block and I agree that's pretty bad. You may be right the block may be too far gone at this point, you can't keep honing and honing because you will be increasing the free play in the oil pump and water pump drive chain.
I understand your concern!!!!!!!
Sorry
I understand your concern!!!!!!!
Sorry
Similar threads
- Replies
- 5
- Views
- 932
- Replies
- 0
- Views
- 537
-
This site uses cookies to help personalise content, tailor your experience and to keep you logged in if you register.
By continuing to use this site, you are consenting to our use of cookies.