Ski-Dooin' it
Expert
SO... i had issues earlier in the season with my header/motor flange warping, had it machined smooth and WOW, the same boost levels were a LOT more powerful then with it leaking. ran good for a while, i noticed some cracking in my header, so i took it off and did some major welding on the collector part of it.. NOW i noticed that the flange on the motor side is warped(presumably from the intense welding) I dont want to get it machined again as I feel like im just going backwards then making it so much thinner..
My thought was to cut the flange between each cylinder so that it can mate properly.. there is a genlte warp across the whole thing and there is no way the tiny little bolts are going to suck it back in as a whole, but as peices it might come together nice?? Hate to destroy a $60 flange, but man, my boost is so freakin inconsistant and weak right now. I have to run like 20+ psi in the flats to get it to hold 13/14 in deep mushy spring snow..this isnt helping me nail down my clutching at all!
My thought was to cut the flange between each cylinder so that it can mate properly.. there is a genlte warp across the whole thing and there is no way the tiny little bolts are going to suck it back in as a whole, but as peices it might come together nice?? Hate to destroy a $60 flange, but man, my boost is so freakin inconsistant and weak right now. I have to run like 20+ psi in the flats to get it to hold 13/14 in deep mushy spring snow..this isnt helping me nail down my clutching at all!

kinger
VIP Member
I think I asked this once and msot agreed it would be fine to cut them, but hopefully a header builder will chime in.
Factory does it and on rear mount turbos they hold up just fine. Not sure if the front mounts need the combined strength of the flange for support of the turbo or not.
Factory does it and on rear mount turbos they hold up just fine. Not sure if the front mounts need the combined strength of the flange for support of the turbo or not.
Ski-Dooin' it
Expert
Good thinking, i kinda got inspired from looking at a rear mount and seeing those seperate. My turbo is hung all on its own with 2 stroke exhaust springs providing more then enough up force. even if it causes a little bit of issues, im building a new header in about a month, just trying to figure this out as no matter how good my header's are, they keep freakin leakin!!

kinger
VIP Member
Hence why I would never touch a front mount. Way too many header/heat problems.
You might get it trailable going down a trail at 50mph at light loads but in the mountains under full load most of the time I cant imagine the heat they see.
I thought I read somewhere there was a better gasket being used now that would allow th header to be warped a bit and still seal.
Sorry I'm not much help I dont pay a lot of attention to turbo stuff. Good luck!
You might get it trailable going down a trail at 50mph at light loads but in the mountains under full load most of the time I cant imagine the heat they see.
I thought I read somewhere there was a better gasket being used now that would allow th header to be warped a bit and still seal.
Sorry I'm not much help I dont pay a lot of attention to turbo stuff. Good luck!
Ski-Dooin' it
Expert
i did find a better gasket, I totally forgot about it, i bet if i order one up i can have it soon enough to get out and play with for the weekend. its a thick graphite one that will crush down better allowing the mild warpage mine has...
and yeah, the heat is somewhat insane.. 1 minute WOT barely moving will blow your mind. the whole header and turbine side of the exhaust get NICE and red, im moving my exhaust for next year as my tunnel dump is behind the drivers and the one is wearing out way faster... its hot down there!!
and yeah, the heat is somewhat insane.. 1 minute WOT barely moving will blow your mind. the whole header and turbine side of the exhaust get NICE and red, im moving my exhaust for next year as my tunnel dump is behind the drivers and the one is wearing out way faster... its hot down there!!
thamax
Pro
u must be thinking of remflex gaskets and they make one just for that motor and work really well and have life time warranty and can be crushed up to a 1/4 of and will not breakdown, leak or stick either surface and have a temp rating of 2500 degrees. they have a website check them out. i would go that route and stage 8 hardware
MRFUSION
Pro
- Joined
- May 19, 2008
- Messages
- 162
- Location
- Peace River Alberta
- Country
- Canada
- Snowmobile
- 2011 Custom Built Nypex
2008 Custom Union Bay 980 MM Chassis
Anyone using those Remflex gaskets in their front mount header application? I like the flexible gasket idea but with the header supporting the turbo will there be movement at all even when crushed? I may try some of these gaskets. Shad
thamax
Pro
yeah they worked really well for me i used them on several front mounts until i switched to the mid mount impulse setup never had one fail yet.
Ski-Dooin' it
Expert
thanks for the info, and yeah, those are the ones I was lookin at!
MRFUSION
Pro
- Joined
- May 19, 2008
- Messages
- 162
- Location
- Peace River Alberta
- Country
- Canada
- Snowmobile
- 2011 Custom Built Nypex
2008 Custom Union Bay 980 MM Chassis
Yeah sorry I meant mid mount header system, I have a Nypex I built with the mid mount header. Just thought these gaskets might be a good idea, dont need heat loss or leaks melting stuff. Thanx for the info guys. Shad
JIM
Extreme
I had remflex make me up 28 of them and they are almost gone. Of the 24 out there I havent had a pm back saying anyone had problems. You have to folllow the directions to a T on the package and you should never have to replace it again. I doesnt come off easy, they are sticky suckers and you will end up scraping your old one off if you have to pull the header. Sold most of them to boondocker apex guys.. Just a few left..
Thanks Jim
Thanks Jim
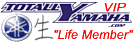

nate007
Lifetime Member
- Joined
- Dec 25, 2006
- Messages
- 2,770
- Location
- Iowa City, Iowa
- Country
- USA
- Snowmobile
- 1. '06 Apex -twin screw
2. '04 Redline Revolt 800
3. '09 Nytro XTX - twin screw
I do build alot of custom header packages, and for thos who have seen the Nytro system our shop has designed, we do use a one-piece flange. There are benifits to this, as well as draw backs.
Assuming the head is flat from one port to the next, a one piece flange can help add a small measure of strength in some situations, and also allow one port to help another port stay sealed in most situations.
Now the drawbacks are there as well, including installation headaches, warping due to inadequate flange thickness or improper welding techniques.
There isn't a header design out there that itself is a poor design if it does it's job. The problems almost always stem from incorrect material choice for the particular application (which is usually a cost issue) or improper welding for the application. A one piece flange for a front mount sled header should be welded a small amount at a time to prevent warping, and/or use various products to control excess heat from dispersing over the rest of the flange. Another method for controlling warping would be in the finishing/machining after the welding.
On a side note, I would welcome anyone who has a spare turbo header to send me one and I'll build one for them to test. I don't want to get into a "who's-who" about what header it is, as long as it's a good fitting header, and someone would be willing to test mine for durability against their current header..
pm me for details.
Assuming the head is flat from one port to the next, a one piece flange can help add a small measure of strength in some situations, and also allow one port to help another port stay sealed in most situations.
Now the drawbacks are there as well, including installation headaches, warping due to inadequate flange thickness or improper welding techniques.
There isn't a header design out there that itself is a poor design if it does it's job. The problems almost always stem from incorrect material choice for the particular application (which is usually a cost issue) or improper welding for the application. A one piece flange for a front mount sled header should be welded a small amount at a time to prevent warping, and/or use various products to control excess heat from dispersing over the rest of the flange. Another method for controlling warping would be in the finishing/machining after the welding.
On a side note, I would welcome anyone who has a spare turbo header to send me one and I'll build one for them to test. I don't want to get into a "who's-who" about what header it is, as long as it's a good fitting header, and someone would be willing to test mine for durability against their current header..
pm me for details.
TWIN TURBO
Expert
I agree with Nate.
I have built a number of HIGH PERF headers without a issue but I use 321 stainless and EVERY header gets surfaced after it's welded. When you weld anything esp a header it will pull. The header flange is the last part that gets welded when building a header because of that very reason. If you weld it first it will bend when you weld up the rest of it. Keep in mind that the flange is bolted to the head. It doen't get near as hot as the rest of the header so expansion is minimal there, besides aluminum and stainless have a closer expansion rate than steel and aluminum.
That said, you could cut the flange between cylinders if you have a problem. You don't have to cut all the way through. You can just cut it about 3/4 of the way. I've seen a number of guys do this but if you follow proper procedures you should not have to.
I have built a number of HIGH PERF headers without a issue but I use 321 stainless and EVERY header gets surfaced after it's welded. When you weld anything esp a header it will pull. The header flange is the last part that gets welded when building a header because of that very reason. If you weld it first it will bend when you weld up the rest of it. Keep in mind that the flange is bolted to the head. It doen't get near as hot as the rest of the header so expansion is minimal there, besides aluminum and stainless have a closer expansion rate than steel and aluminum.
That said, you could cut the flange between cylinders if you have a problem. You don't have to cut all the way through. You can just cut it about 3/4 of the way. I've seen a number of guys do this but if you follow proper procedures you should not have to.

Similar threads
- Replies
- 24
- Views
- 2K
- Replies
- 17
- Views
- 4K
-
This site uses cookies to help personalise content, tailor your experience and to keep you logged in if you register.
By continuing to use this site, you are consenting to our use of cookies.