Dan_16
Newbie
- Joined
- Feb 8, 2013
- Messages
- 2
- Reaction score
- 0
- Points
- 171
- Location
- Originaly NB'r in newfoundland
- Country
- Canada
- Snowmobile
- 08 nytro mtx 153
03 rev800
I got a few questions so here it is,
Sled is a 08 nytro mtx . custom rear mount turbo , front mount intercooler setup.
Just trying to figure out what is the best way to have the air intake temp sensor and the idle air control (located on the mag side of throttle bodies) hooked up either in the intercooler plenum or not. First, I've heard that some people run the AIT out in the atmosphere ? is there a reason for this or they don't have a location to have it in ? If it is made possible to have it in the intercooler would it be better? For the IAC i cant really find anything on were it is hooked up for boosted setup so if anyone has input on this let me know ! both are originally hooked up in the air box on a n/a setup .
hoping to get feedback . cheers !
Sled is a 08 nytro mtx . custom rear mount turbo , front mount intercooler setup.
Just trying to figure out what is the best way to have the air intake temp sensor and the idle air control (located on the mag side of throttle bodies) hooked up either in the intercooler plenum or not. First, I've heard that some people run the AIT out in the atmosphere ? is there a reason for this or they don't have a location to have it in ? If it is made possible to have it in the intercooler would it be better? For the IAC i cant really find anything on were it is hooked up for boosted setup so if anyone has input on this let me know ! both are originally hooked up in the air box on a n/a setup .
hoping to get feedback . cheers !
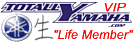

nate007
Lifetime Member
- Joined
- Dec 25, 2006
- Messages
- 2,770
- Reaction score
- 60
- Points
- 1,333
- Location
- Iowa City, Iowa
- Country
- USA
- Snowmobile
- 1. '06 Apex -twin screw
2. '04 Redline Revolt 800
3. '09 Nytro XTX - twin screw
I know the IAC discussion has been had before in regards to the blower setups, but I don't know of anyone who has actually tested to see if boost pressure being put to the idle circuit has any adverse effects or not. On my blower sleds, I simply added a hose to the IAC intake port and put a small breather filter on it and am drawing incoming air through that. I also have yet to test to see if any boosted air gets forced back through the iac system though, and lost that way. As a precautionaly measure to prevent this, I'm adding a check valve to the IAC intake line that will allow it to draw air in but not let boost presure escape. On the earlier Apex's with a coolant temp valve I don't see it causing much of an issue, but the Nytro's and other sleds with an iac motor (which makes the little noise you hear when you turn the key on) I'm concerned that higher boost levels could damage the stepper motor/valve by trying to force it open if it's trying to stay closed. A check valve on it would protect it from being forced open.
As far as the IAT is concerned, I've researched this at great lengths as well, but have been unable to find a conclusive answer. I have looked for someone that has knowledge of the temperature range in which the sensor is calibrated to operate within the ecu's tune. On a n/a sled, the IAT is not likely to see much of a wide range of temps, meaning the weather that sleds are generally ridden in is usually 0*f to around 50*f (on those late season days). Even though the actual temp and voltage specs of the sensor can be found, I have been unable to find out what the ecu does with that information. The two main things would be:
(1.) What range does the ECU actually recognise from the sensor - which is that even though the sensor may have the capability to read a wide range, Yamaha may have only programmed the temp range for riding on snow, and it might not read temps outside that? Most automotive tunes either calibrate the normal operating range and leave the extremes blank, or they match the "out of normal range" cells in the ecu to the upper and lower cells that have been calibrated.
(2.) How much of an actual afr calibration does it make? Basically, lets just say that the actual sensor can read temps of -40*f - 250*f. The computer may have only been tuned from Yamaha to actually use the temp range I mentioned ealier (0*-50*), and any temps beyone that range may cause the ecu to default to 'no calibration change" or "full rich. However, being that it's a powersport application and not an automotive application, the R&D isn't as broad, and the IAT may in the end only make a few percentage points change at most anyways. There may simply be little significance in the overall engine tuning/calibration coming from the IAT anyways.
Hopefully I haven't confused the heck out of you, but the reason I explained that is this:
When you introduce boost, you also introduce heat. Depending on your boost level, compressor type, intercooler efficiency and actual outside temps when riding, some boost systems could see air temps entering the engine as high as 180*+. If you simply put the IAT in the intercooler, you may be wasting your time if the computer doesn't know what temp its seeing, and/or what to do with it. On the flip side of that, if you do install it in the intercooler or other area that sees boost, and the ecu does actually know what temp it is and what to do with it, you may be able to use the added fuel from the elevated temps and not have to add as much with your tuning module.
I would like to find someone who has access to the ecu's tuning files to be able to find out what importance the IAT actually has on the entire system.
Long story short, it might not be worth putting it in if the computer can't use it. An aftermarket fuel controller that can read boost temps and calibrate for it would make a big difference though!
As far as the IAT is concerned, I've researched this at great lengths as well, but have been unable to find a conclusive answer. I have looked for someone that has knowledge of the temperature range in which the sensor is calibrated to operate within the ecu's tune. On a n/a sled, the IAT is not likely to see much of a wide range of temps, meaning the weather that sleds are generally ridden in is usually 0*f to around 50*f (on those late season days). Even though the actual temp and voltage specs of the sensor can be found, I have been unable to find out what the ecu does with that information. The two main things would be:
(1.) What range does the ECU actually recognise from the sensor - which is that even though the sensor may have the capability to read a wide range, Yamaha may have only programmed the temp range for riding on snow, and it might not read temps outside that? Most automotive tunes either calibrate the normal operating range and leave the extremes blank, or they match the "out of normal range" cells in the ecu to the upper and lower cells that have been calibrated.
(2.) How much of an actual afr calibration does it make? Basically, lets just say that the actual sensor can read temps of -40*f - 250*f. The computer may have only been tuned from Yamaha to actually use the temp range I mentioned ealier (0*-50*), and any temps beyone that range may cause the ecu to default to 'no calibration change" or "full rich. However, being that it's a powersport application and not an automotive application, the R&D isn't as broad, and the IAT may in the end only make a few percentage points change at most anyways. There may simply be little significance in the overall engine tuning/calibration coming from the IAT anyways.
Hopefully I haven't confused the heck out of you, but the reason I explained that is this:
When you introduce boost, you also introduce heat. Depending on your boost level, compressor type, intercooler efficiency and actual outside temps when riding, some boost systems could see air temps entering the engine as high as 180*+. If you simply put the IAT in the intercooler, you may be wasting your time if the computer doesn't know what temp its seeing, and/or what to do with it. On the flip side of that, if you do install it in the intercooler or other area that sees boost, and the ecu does actually know what temp it is and what to do with it, you may be able to use the added fuel from the elevated temps and not have to add as much with your tuning module.
I would like to find someone who has access to the ecu's tuning files to be able to find out what importance the IAT actually has on the entire system.
Long story short, it might not be worth putting it in if the computer can't use it. An aftermarket fuel controller that can read boost temps and calibrate for it would make a big difference though!
Dan_16
Newbie
- Joined
- Feb 8, 2013
- Messages
- 2
- Reaction score
- 0
- Points
- 171
- Location
- Originaly NB'r in newfoundland
- Country
- Canada
- Snowmobile
- 08 nytro mtx 153
03 rev800
alright thanks for the input ! Ill be running the IAT in the cooler for now, if it seams to affect the fuel calibration when running it will have to be moved . I wont be using a full standalone so there fore i wont be able to see what the IAT is reading and affecting fuel cells so there for it will be mostly assuming if it is doing something to the cells like you said from the hot'er air . Ridding temps go from -40C TO 0C and approx 800 - 1000 m above sea level.
FOr the IAC , mostly from what you said will be doing the same and for the check valve also , never though of it to cause a boost leak!
Thanks alot!
FOr the IAC , mostly from what you said will be doing the same and for the check valve also , never though of it to cause a boost leak!
Thanks alot!
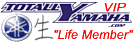

nate007
Lifetime Member
- Joined
- Dec 25, 2006
- Messages
- 2,770
- Reaction score
- 60
- Points
- 1,333
- Location
- Iowa City, Iowa
- Country
- USA
- Snowmobile
- 1. '06 Apex -twin screw
2. '04 Redline Revolt 800
3. '09 Nytro XTX - twin screw
You said you're not using a fuel stand alone? I should clarify that I was referring to a fuel "controller" when I explained that. most of the current products on the market for powersports aren't sophosticated enough to add additional sensors to them, which is what I was taking about.
I would assume that your turbo kit has some sort of tuner with it?
Also, the only reason I'd say to leave the IAT alone is that NOT knowing what the factory ecu does with the information makes me hesitant to experiment with it. Both for the risk of incorrect fueling, as well as the effort of welding in a fitting/etc to attach it to.
The way all "piggy back" controllers work is to interrupt signals FROM the sentors to the ecu, and the only real input it has within itself is for boost pressure. It then calculates the additional fuel needed for the added boost and then interrupts the signal FROM the ecu to the injectors to make them ad more fuel. It 'fools' the ecu into operating normally, so the ecu doesn't have a clue that boost has been added. That being said, simply putting the IAT into the intercooler will make the sled think it's operating in the Sahara desert, with all other inputs to the factory computer being recieved as normal. Having that IAT signal be the only input to the factory computer that will be way outside of it's normal operating range is why I'm hesitant to do it that way. It could be a non-issue, or it could make tuning a real PIA, it could cause a SES light/trouble code, or it could work beautifuly that way. I just haven't been able to figure out a definitive answer to that yet.
After I posted before, I did think of one person I know that might have the access to the information to solve this whole IAT issue. They're at Haydays right now, so hopefully I'll hear back beginning of the week. I'll post what I found out when I talk to them.
I would assume that your turbo kit has some sort of tuner with it?
Also, the only reason I'd say to leave the IAT alone is that NOT knowing what the factory ecu does with the information makes me hesitant to experiment with it. Both for the risk of incorrect fueling, as well as the effort of welding in a fitting/etc to attach it to.
The way all "piggy back" controllers work is to interrupt signals FROM the sentors to the ecu, and the only real input it has within itself is for boost pressure. It then calculates the additional fuel needed for the added boost and then interrupts the signal FROM the ecu to the injectors to make them ad more fuel. It 'fools' the ecu into operating normally, so the ecu doesn't have a clue that boost has been added. That being said, simply putting the IAT into the intercooler will make the sled think it's operating in the Sahara desert, with all other inputs to the factory computer being recieved as normal. Having that IAT signal be the only input to the factory computer that will be way outside of it's normal operating range is why I'm hesitant to do it that way. It could be a non-issue, or it could make tuning a real PIA, it could cause a SES light/trouble code, or it could work beautifuly that way. I just haven't been able to figure out a definitive answer to that yet.
After I posted before, I did think of one person I know that might have the access to the information to solve this whole IAT issue. They're at Haydays right now, so hopefully I'll hear back beginning of the week. I'll post what I found out when I talk to them.