melmaq
Extreme
- Joined
- Jun 16, 2011
- Messages
- 65
- Location
- Umeå, Sweden
- Website
- www.youtube.com
- Country
- Sweden
- Snowmobile
- TNytro MCX 240
Awesome to see you back Nikolai!
now, get back to work!
now, get back to work!
Nikolai
TY 4 Stroke God
Worked on it all weekend, hours of additional bondo and sanding. Started getting pretty close yesterday and finally got to the point where I only had to fill in what seemed like 100 low spots.


After a final sanding the imperfections were small enough that it was hard to see them, so I masked off the sled and painted it with gray primer. Overall it's close, I'll have a day or two of touch up before it's done but my goal is to make body panels this weekend.






More to come...


After a final sanding the imperfections were small enough that it was hard to see them, so I masked off the sled and painted it with gray primer. Overall it's close, I'll have a day or two of touch up before it's done but my goal is to make body panels this weekend.






More to come...
Last edited:
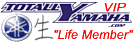

moab11
Lifetime Member
- Joined
- Feb 4, 2010
- Messages
- 424
- Location
- Thunder Bay, Ontario
- Country
- Canada
- Snowmobile
- 2016 SKS 155
Looking Good!
Nikolai
TY 4 Stroke God
Well, I didn't have to do too much additional filling. After I sand this tomorrow I'll paint it again and double check it.
Filled in around the brake caliper (shape wasn't quite right) and filled the inner corners to get rid of the sharp bends.

Mostly small fillers on the side to get rid of a few holes and ripples.

Same thing on the other side. Just a few small ripples and low spots to fill in.

Had a flat spot on the back of the secondary to fill in and I filled the entire lower edge to reduce the bend.


Filled in around the brake caliper (shape wasn't quite right) and filled the inner corners to get rid of the sharp bends.

Mostly small fillers on the side to get rid of a few holes and ripples.

Same thing on the other side. Just a few small ripples and low spots to fill in.

Had a flat spot on the back of the secondary to fill in and I filled the entire lower edge to reduce the bend.


Wow awesome work
edge_232
Expert
- Joined
- Jan 15, 2014
- Messages
- 254
- Age
- 50
- Location
- Madison WI
- Country
- USA
- Snowmobile
- 2011 Nytro MTX slowly being modded
2005 IQR Trail Converted
A ton of time consuming work but it's looking good!
Nikolai
TY 4 Stroke God
Nikolai
TY 4 Stroke God
Sportsterdanne
TY 4 Stroke Guru
I used both wax and PVA when i made hoods back in the Days.
Nikolai
TY 4 Stroke God
I spent all day Sunday cutting up fabric (there's a lot more pieces than it looks like). The carbon fiber cut good but the carbon/kevlar was a pain. The Titanium Fiscars are the way to go, regular scissors wouldn't even begin to cut it. http://www2.fiskars.com/Crafting/Pr...r-9-Titanium-Nitride-Shop-Shears#.VL3osyx7SAk

Monday was a paid day off so I started on the chaincase side and managed to finish it. The carbon/kevlar is pretty flexible so I used it for the first layer. For the second layer I used carbon fiber, and for the third and final layer I used carbon/kevlar again so the blue would be visible. The entire panel is a minimum of 3 layers, and with multiple overlapping, the stressed areas such as around the brake caliper and especially in front of the oil tank are 4-5 layers. Pretty time consuming but I got it to follow all the indents in the subframe and the shape of the chaincase, ect. With the fit being so tight I'm anticipating only needing a few fasteners to hold it together. Tomorrow after work I'll pop this side off and lay up the clutch side. It looks better in person and once I eventually get around to sanding the seams and applying another coat of resin the seams should be less noticeable.


It's hard to tell in the pics because of the poor lighting, but the blue really stands out as soon as it's in natural light outside.

Monday was a paid day off so I started on the chaincase side and managed to finish it. The carbon/kevlar is pretty flexible so I used it for the first layer. For the second layer I used carbon fiber, and for the third and final layer I used carbon/kevlar again so the blue would be visible. The entire panel is a minimum of 3 layers, and with multiple overlapping, the stressed areas such as around the brake caliper and especially in front of the oil tank are 4-5 layers. Pretty time consuming but I got it to follow all the indents in the subframe and the shape of the chaincase, ect. With the fit being so tight I'm anticipating only needing a few fasteners to hold it together. Tomorrow after work I'll pop this side off and lay up the clutch side. It looks better in person and once I eventually get around to sanding the seams and applying another coat of resin the seams should be less noticeable.


It's hard to tell in the pics because of the poor lighting, but the blue really stands out as soon as it's in natural light outside.
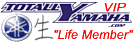

moab11
Lifetime Member
- Joined
- Feb 4, 2010
- Messages
- 424
- Location
- Thunder Bay, Ontario
- Country
- Canada
- Snowmobile
- 2016 SKS 155
That looks Awesome!
Caleb:
Given that losing weight is a priority, I can think of 2 reasons why it might be more beneficial to make the CF pieces more like the original design of the plastics rather than shaping them to fit tightly along the lines of the clutches, oil tank, chassis spars, etc. 1: All of the in-and-out bends you need to make in order follow the shape of the objects being covered will actually require using more CF material than they would if the pieces simply spanned the gaps. Less surface area to cover, less weight. 2: Provided the form of your CF pieces was more aerodynamic (for lack of a more accurately descriptive word) it would likely hold less snow. Less snow, less weight. The second point may not be much of a factor for you ... I doubt whether your design will hold much snow, but just something to consider (if ever you decide to make a second generation hood).
If I were to attempt to create a form for what you are doing now, I might try playing around with shrink wrap (the kind they use to cover boats for storage). You would need to make some small ribs or bows to support or "tent" the shrinkwrap (similar to a fabric-covered airplane wing) in order to create a form, but in this way you would be able to quickly change the shape of your form until you had something you liked. Beats filling your subframe/delta box full of expandable foam.
I dunno how you could take the form to next step of laying CF to make the pieces you need, but just thought I throw out some ideas I had when looking at what you're doing now, which is amazing BTW. Don't take my comments as criticism ... I think you have really good ideas and I watch this thread more so just to see what you'll come up with next.
Given that losing weight is a priority, I can think of 2 reasons why it might be more beneficial to make the CF pieces more like the original design of the plastics rather than shaping them to fit tightly along the lines of the clutches, oil tank, chassis spars, etc. 1: All of the in-and-out bends you need to make in order follow the shape of the objects being covered will actually require using more CF material than they would if the pieces simply spanned the gaps. Less surface area to cover, less weight. 2: Provided the form of your CF pieces was more aerodynamic (for lack of a more accurately descriptive word) it would likely hold less snow. Less snow, less weight. The second point may not be much of a factor for you ... I doubt whether your design will hold much snow, but just something to consider (if ever you decide to make a second generation hood).
If I were to attempt to create a form for what you are doing now, I might try playing around with shrink wrap (the kind they use to cover boats for storage). You would need to make some small ribs or bows to support or "tent" the shrinkwrap (similar to a fabric-covered airplane wing) in order to create a form, but in this way you would be able to quickly change the shape of your form until you had something you liked. Beats filling your subframe/delta box full of expandable foam.
I dunno how you could take the form to next step of laying CF to make the pieces you need, but just thought I throw out some ideas I had when looking at what you're doing now, which is amazing BTW. Don't take my comments as criticism ... I think you have really good ideas and I watch this thread more so just to see what you'll come up with next.
mike g
Extreme
Caleb:
If I were to attempt to create a form for what you are doing now, I might try playing around with shrink wrap (the kind they use to cover boats for storage). You would need to make some small ribs or bows to support or "tent" the shrinkwrap (similar to a fabric-covered airplane wing) in order to create a form, but in this way you would be able to quickly change the shape of your form until you had something you liked.
I dunno how you could take the form to next step of laying CF to make the pieces you need, but just thought I throw out some ideas I had when looking at what you're doing now, which is amazing BTW. Don't take my comments as criticism ... I think you have really good ideas and I watch this thread more so just to see what you'll come up with next.
Foil tape works well for this. Apply release agent to it then lay down fiberglass, pop the fiberglass and that's your female mold for the carbon fiber.
Nikolai
TY 4 Stroke God
OVR4D, I appreciate all comments/advice/critisism. It's how we learn and better ourselves. I strive to do the best work I can, and sometimes people have much better techniques/approaches than my own. This has been incredibly time consuming. I'm sure from the start of cutting off the old body work there's a couple hundred hours to get where I am now.
Sportsterdanne
TY 4 Stroke Guru
Updates ?
-
This site uses cookies to help personalise content, tailor your experience and to keep you logged in if you register.
By continuing to use this site, you are consenting to our use of cookies.