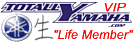

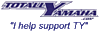
TC Rides
Lifetime Member
- Joined
- Feb 1, 2019
- Messages
- 25
- Age
- 59
- Location
- Wilmette, IL
- Country
- USA
- Snowmobile
- 2007 Yamaha Apex GT
All-
Any ideas welcome. I am installing new A Arm bushings on my 07 Apex and cannot get the outside, right side bolts out of the A Arms, both upper and lower bolts refuse to come out. The left side outer came apart (and went back together) easily. I have not done the left inner ones yet.
Obviously, the two A Arms are disconnected from the bulkhead, rotated 90 degrees forward and sitting on work bench. From this orientation, I used a hammer on threaded end of bolt to drive them downward (while supporting below). It almost seems like there is a c clip somewhere preventing these from being removed.
Lastly, anyone ever see a bushing break like below? Was not installed, but found in my hand when I poured out the bag.
Mods, please move this post if there is a better sub-forum for subject.
Thank you
Any ideas welcome. I am installing new A Arm bushings on my 07 Apex and cannot get the outside, right side bolts out of the A Arms, both upper and lower bolts refuse to come out. The left side outer came apart (and went back together) easily. I have not done the left inner ones yet.
Obviously, the two A Arms are disconnected from the bulkhead, rotated 90 degrees forward and sitting on work bench. From this orientation, I used a hammer on threaded end of bolt to drive them downward (while supporting below). It almost seems like there is a c clip somewhere preventing these from being removed.
Lastly, anyone ever see a bushing break like below? Was not installed, but found in my hand when I poured out the bag.
Mods, please move this post if there is a better sub-forum for subject.
Thank you
Attachments

RobX-1
VIP Member
- Joined
- Apr 13, 2003
- Messages
- 2,142
- Location
- Coldwater, OH
- Country
- USA
- Snowmobile
- 18 50th Apex XT-X, 08 40th Apex LTX GT, 08 40th Nytro RTX, & 03 RX-1
I suspect your a-arm bolts are tweaked and preventing them from sliding out. I had one that was kinked and was a burger to get out; at least the a-arm itself was still good and straight.

twyztid
VIP Member
- Joined
- Feb 14, 2011
- Messages
- 859
- Location
- Middleville, MI
- Country
- USA
- Snowmobile
- 2017 Sidewinder LTX SE - TD Power Trail, CAI, 3" Super Quiet
2012 RS Vector
2006 Apex GT
- LOCATION
- Middleville, MI
Your bolts are likely bent. I have run into that before. I had to use a sawzall with a metal blade to cut the bolt between where the spindle & a-arm meet (down through lip of the bushing) to get the bolt out.
RAMSOMAIR
TY 4 Stroke God
Yep, one on my brothers Apex was shaped like a Z almost.
Brotherdan
Expert
- Joined
- Sep 8, 2017
- Messages
- 361
- Age
- 52
- Location
- Belmont,maine
- Country
- USA
- Snowmobile
- 2011 apex xtx blue, starr suspension,gytr front shocks,camso 1.5 track cut down, snowtrackers work in process,2003 rx1er originally 121 converted to 136"monoshock 2 ck136 rear suspension with clicker vector ltx shock,muffin works tunnel extension, seat concepts(wrp) seat,apex hooked handlebars converted to all underhood wiring,8"lake effect billet aluminum riser,gytr frontshocks,yamaheater hand warmer kit,rocks ridelite,rocks power supply, rocks heated bag,, tunnel braces,blue skid plate,garmin gps, aggressive snowtrackers on apex single keel skis,rollerski ski wheel kit,108 warthog studs&blue studboy backers,pioneer wheel lowering kit, dupont slides, 4th wheel kit,yamaha saddle, tank& windshield bags, powermadd led handguards, bar mount mirror kit, apex radiator& electric fan added, apex rear cooler,autometer temp guage, apex new style large diameter drive shaft with extroverts machined for chaincase,thunder products clutching,1987 enticer 340ltr 2100miles,1984 enticer 340,1996 wolverine 350,big wheel kit,winch,racks,k&n,full skidplates
The bolts should easily slide right out I would also suspect they are bent & will require careful cutting of the bolts, or stuck in the spindle sleeves, make sure to use a nut on the bolt threads to prevent mushrooming,try some heat with mapp gas just don’t go crazy& lots of penetrating fluid if they are just stuck & you can free them up would be a much better problem than them being bent ,as far as the bushings it could be a quality/ brand issue I’ve only ever used the mpi/yamaha brand & never had any quality issuesAll-
Any ideas welcome. I am installing new A Arm bushings on my 07 Apex and cannot get the outside, right side bolts out of the A Arms, both upper and lower bolts refuse to come out. The left side outer came apart (and went back together) easily. I have not done the left inner ones yet.
Obviously, the two A Arms are disconnected from the bulkhead, rotated 90 degrees forward and sitting on work bench. From this orientation, I used a hammer on threaded end of bolt to drive them downward (while supporting below). It almost seems like there is a c clip somewhere preventing these from being removed.
Lastly, anyone ever see a bushing break like below? Was not installed, but found in my hand when I poured out the bag.
Mods, please move this post if there is a better sub-forum for subject.
Thank you
Last edited:
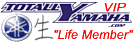

- Joined
- Jun 1, 2004
- Messages
- 7,730
- Location
- sudbury on
- Country
- Canada
- Snowmobile
- 2016 apex xtx
2011 apex xtx
2009 phaser rtx/x
1997 et410t/r
1988 vk 540
i have cracked some putting them in before i started using a threaded rod to do it with big washers. i have only ever used yamaha/ulmers kit when doing it.
i helped a guy do a vector last season and it was lucky i had all the bolts in a spare set of a arms as i needed them. i ended up using a chunk of wood to spread the arms while i used a death wheel to cut the bolts. the fun part was getting the bolts out of the sleeves as both of the ones that stuck split the sleeve at the end that the bolts go through that is in the spindle.
i helped a guy do a vector last season and it was lucky i had all the bolts in a spare set of a arms as i needed them. i ended up using a chunk of wood to spread the arms while i used a death wheel to cut the bolts. the fun part was getting the bolts out of the sleeves as both of the ones that stuck split the sleeve at the end that the bolts go through that is in the spindle.
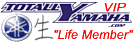

Teamblue4
Lifetime Member
- Joined
- Feb 20, 2008
- Messages
- 1,284
- Location
- Il.
- Country
- USA
- Snowmobile
- 2012 Apex XTX
2013 Apex SE
2014 Apex SE
2014 Apex XTX
2018 Apex XTX 50TH Anniversary
Bolts are rusted to the spindle sleeves, due to lack of maintenance, air hammer them loose.
Last edited:
yamahinn03
TY 4 Stroke Guru
- Joined
- Dec 28, 2004
- Messages
- 757
- Age
- 58
- Location
- oshkosh, wi
- Country
- USA
- Snowmobile
- 12 Nytro XTX (mine)
06 Apex GT (wifes)
07 Phazer (#2 sons)
02 Viper (#1 Sons)
Mine where not bent but seized in the collars/sleeves had to sawzall them out
Similar threads
- Replies
- 3
- Views
- 1K
- Replies
- 6
- Views
- 2K
-
This site uses cookies to help personalise content, tailor your experience and to keep you logged in if you register.
By continuing to use this site, you are consenting to our use of cookies.