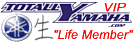

1nc 2000
Lifetime Member Tim
- Joined
- Feb 26, 2010
- Messages
- 3,050
- Location
- Marquette, MI
- Country
- USA
- Snowmobile
- Yamaha FX Nytro RTX SE
Stm 60y weights set up for 270.
Dalton black blue spring. 14.8 mm rollers.
This is what's in it right now, but still testing.
Dalton black blue spring. 14.8 mm rollers.
This is what's in it right now, but still testing.
Well as long as you have the driven bolted solid to the bearing I don't see an issue. Here is the problem. Many are going to think that using the stock washer or the adjustment plug they have it bolted down solid just because it doesn't move.
Some people are not smart when it come to this stuff and they will have issues, because the driven can still float if not done properly. They can't figure it out that bolted solid means machining the alum plug or spacing it solid means the bolt has to hold only on the driven shaft and not the helix like it does from the factory. You can show them and they still don't understand how this works. So many, I'd even say the majority that need pictures and instructions still won't get it done properly. So not done properly and there will be many issues.
There is a shoulder behind the bearing, if the driven is indeed bolted down solid to it, it remains the same as the circlip holding the bearing on, but you must be certain to use a washer the size of the shaft of the driven outside and not the size of the helix, also the proper shimming for the outside of this assembly so it "DOES NOT FLOAT" OR "APPLY TOO MUCH PRESSURE TO THE JACKSHAFT" pushing against the bearing or trying to bend the washer. It takes so time and the proper shims to get this part spot on. If you make the effort to get this done properly it will be fine. It will also require shimming for deflection inside the driven sheave halves which most will not understand as well. If you have the know how to do it, great, but for most they will need pictures and need to explaining than people have time for.
If one does not understand the principle, or you feel the need to ask questions, they probably should not be doing it, even though its quite simple.
Washer size needs to be as below with proper Apex style shim washer below it, and belt deflection needs to be set inside the Driven like the old Cat reverse cam drivens. Or, you need to shim tight against the driven shaft and use your outside adjuster accordingly. Its simple if you understand the reasoning behind all of it. Machining the driven becomes easier for those that don't understand at that point.
View attachment 144269
Skillfully done...nice...awaiting reports on the team
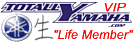

- Joined
- Nov 29, 2009
- Messages
- 1,230
- Age
- 49
- Location
- sabattus, maine
- Country
- USA
- Snowmobile
- 76 exciter, 87 phazer, 89 bravo, 00 srx x3, 01 srx, 02/04 viper, 06 ape
Thanks, I was just curious about the weight profile. I've been running ulmers combo and I haven't had the belt issues many have had here. His setup has some similarities to yours. 60ys though, I was thinking about trying the 60y or Dalton profile.Stm 60y weights set up for 270.
Dalton black blue spring. 14.8 mm rollers.
This is what's in it right now, but still testing.

ROCKERDAN
OCD Sledhead
- Joined
- Oct 8, 2005
- Messages
- 7,503
- Location
- Huntsville Ontario & Niagara NY
- Country
- Other
- Snowmobile
- '18 RTX 50th "Winder"
Got like new 60ys for sale below...if anyone wants.Thanks, I was just curious about the weight profile. I've been running ulmers combo and I haven't had the belt issues many have had here. His setup has some similarities to yours. 60ys though, I was thinking about trying the 60y or Dalton profile.
YS is flatter, Y more curvature.

ROCKERDAN
OCD Sledhead
- Joined
- Oct 8, 2005
- Messages
- 7,503
- Location
- Huntsville Ontario & Niagara NY
- Country
- Other
- Snowmobile
- '18 RTX 50th "Winder"
How much backpressure are you running?I got some trail time in yesterday with my secondary locked down solid. Running EPI purple spring and 41-37 helix. Pulls super hard and clutches were not super hot. Could put my hand on clutch sheaves anywhere. Both clutches felt the same. Wish I had a temp gun. Did not get any top end runs over 110 mph due to no room for long pulls. Time to start playing with the amount of wrap on secondary spring to see what I like the best for the trails I ride.
Also, where does the EPI Purple fall, is it stiffer then B/o?
thanks
Dan
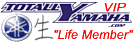

- Joined
- Nov 29, 2009
- Messages
- 1,230
- Age
- 49
- Location
- sabattus, maine
- Country
- USA
- Snowmobile
- 76 exciter, 87 phazer, 89 bravo, 00 srx x3, 01 srx, 02/04 viper, 06 ape
Yes, that's why I might try the Y, hard to take a chance on my perfect belt life though, and I don't have the time for testing and tuning that I used to.Got like new 60ys for sale below...if anyone wants.
YS is flatter, Y more curvature.
![]()

ROCKERDAN
OCD Sledhead
- Joined
- Oct 8, 2005
- Messages
- 7,503
- Location
- Huntsville Ontario & Niagara NY
- Country
- Other
- Snowmobile
- '18 RTX 50th "Winder"
Which tune you running? Man if I had good belt life I would not touch it..lolYes, that's why I might try the Y, hard to take a chance on my perfect belt life though, and I don't have the time for testing and tuning that I used to.
Dan
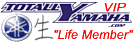

- Joined
- Nov 29, 2009
- Messages
- 1,230
- Age
- 49
- Location
- sabattus, maine
- Country
- USA
- Snowmobile
- 76 exciter, 87 phazer, 89 bravo, 00 srx x3, 01 srx, 02/04 viper, 06 ape
Ran Hurricane 270/290 last year, running the header jukebox this year with Sandale Hyperflow. Talking to Sandale they made significantly more than 270 with the hyperflow on the regular jukebox. Hurricane hasn't tested the header tunes with the Sandale yet so I'll be a Guinea pig if we ever get snow. I'll be sending Hurricane my logs.
But I'll be running the 300 tune where 93 is available and 270 where not.
Kept my Hurricane trail muffler just in case I run lean with the Sandale.
But I'll be running the 300 tune where 93 is available and 270 where not.
Kept my Hurricane trail muffler just in case I run lean with the Sandale.
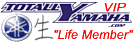

1nc 2000
Lifetime Member Tim
- Joined
- Feb 26, 2010
- Messages
- 3,050
- Location
- Marquette, MI
- Country
- USA
- Snowmobile
- Yamaha FX Nytro RTX SE
How much backpressure are you running?
Also, where does the EPI Purple fall, is it stiffer then B/o?
thanks
Dan
Wrapped 3-1 right now. It's the epi purple apex spring. Its stiffer than the b/o.
I have the new b/o. I have yet to try it though.
I'm running the 8jp belt.
WVTurboLTX
TY 4 Stroke Guru
- Joined
- Nov 9, 2014
- Messages
- 878
- Age
- 42
- Country
- USA
- Snowmobile
- 2009 Nytro XTX
2017 Sidewinder LTX LE
I made a shorter plug that gets a washer stacked on it to lock the shaft in. Well, close to locked in, there is .19mm float now. I then still use the thin washers on top of that to adjust deflection. I don't have the adjustment range I used to but it seems to be enough for now.Well as long as you have the driven bolted solid to the bearing I don't see an issue. Here is the problem. Many are going to think that using the stock washer or the adjustment plug they have it bolted down solid just because it doesn't move.
Some people are not smart when it come to this stuff and they will have issues, because the driven can still float if not done properly. They can't figure it out that bolted solid means machining the alum plug or spacing it solid means the bolt has to hold only on the driven shaft and not the helix like it does from the factory. You can show them and they still don't understand how this works. So many, I'd even say the majority that need pictures and instructions still won't get it done properly. So not done properly and there will be many issues.
There is a shoulder behind the bearing, if the driven is indeed bolted down solid to it, it remains the same as the circlip holding the bearing on, but you must be certain to use a washer the size of the shaft of the driven outside and not the size of the helix, also the proper shimming for the outside of this assembly so it "DOES NOT FLOAT" OR "APPLY TOO MUCH PRESSURE TO THE JACKSHAFT" pushing against the bearing or trying to bend the washer. It takes so time and the proper shims to get this part spot on. If you make the effort to get this done properly it will be fine. It will also require shimming for deflection inside the driven sheave halves which most will not understand as well. If you have the know how to do it, great, but for most they will need pictures and need to explaining than people have time for.
If one does not understand the principle, or you feel the need to ask questions, they probably should not be doing it, even though its quite simple.
Washer size needs to be as below with proper Apex style shim washer below it, and belt deflection needs to be set inside the Driven like the old Cat reverse cam drivens. Or, you need to shim tight against the driven shaft and use your outside adjuster accordingly. Its simple if you understand the reasoning behind all of it. Machining the driven becomes easier for those that don't understand at that point.
View attachment 144269
Hammer70
GRIPNRIP
- Joined
- Sep 6, 2015
- Messages
- 824
- Location
- Niagara, Ontario.
- Country
- Canada
- Snowmobile
- 82SS440/96VMAX/02SRX/08APE/15SRVIPER/17SIDEWINDER
I did mine 0 float with clip and BOP adjuster installed . Machined my own plug,shims and secondary shaft. Did 3 winders as per Dave at Hurricane. 200k yesterday no issues but only time will tell.
ronzx9
Pro
- Joined
- Jan 11, 2017
- Messages
- 139
- Age
- 61
- Location
- Ohio
- Country
- USA
- Snowmobile
- 2017 Sidewinder L-TX-LE, 2016 Grand Touring SE 1200
Hammer70, Where did you get that bellypan protector?
Hammer70
GRIPNRIP
- Joined
- Sep 6, 2015
- Messages
- 824
- Location
- Niagara, Ontario.
- Country
- Canada
- Snowmobile
- 82SS440/96VMAX/02SRX/08APE/15SRVIPER/17SIDEWINDER
snotek performance here in Ontario I’m sure you can get it at ulmer if he’s dealing with Precission now. Not 100% sureHammer70, Where did you get that bellypan protector?
Last edited:

ROCKERDAN
OCD Sledhead
- Joined
- Oct 8, 2005
- Messages
- 7,503
- Location
- Huntsville Ontario & Niagara NY
- Country
- Other
- Snowmobile
- '18 RTX 50th "Winder"
But with diff springs, tangs dont coincide so degrees typically dont match other springs. I was looking for a lbs tension moreso.Wrapped 3-1 right now. It's the epi purple apex spring. Its stiffer than the b/o.
I have the new b/o. I have yet to try it though.
I'm running the 8jp belt.
Dan

ROCKERDAN
OCD Sledhead
- Joined
- Oct 8, 2005
- Messages
- 7,503
- Location
- Huntsville Ontario & Niagara NY
- Country
- Other
- Snowmobile
- '18 RTX 50th "Winder"
Sounds near same as I did....I cut my float plug down and left it approx 1.5mm long. I then used two thin shims that fit overtop of my float plug, then my large 36mm washer on END of float plug, then 4 washers and then BOP adjuster. So I have removed the float altogether with just a touch of play if any at all.I made a shorter plug that gets a washer stacked on it to lock the shaft in. Well, close to locked in, there is .19mm float now. I then still use the thin washers on top of that to adjust deflection. I don't have the adjustment range I used to but it seems to be enough for now.
Still not sure confident any of this will make huge diff in belt life, but its my last gasp before going to TEAM.
Dan
Similar threads
- Replies
- 0
- Views
- 2K
- Replies
- 1
- Views
- 252
- Replies
- 21
- Views
- 2K
-
This site uses cookies to help personalise content, tailor your experience and to keep you logged in if you register.
By continuing to use this site, you are consenting to our use of cookies.