
- Joined
- Apr 14, 2003
- Messages
- 6,539
- Reaction score
- 3,171
- Points
- 1,983
- Location
- Hessel, Michigan
- Country
- USA
- Snowmobile
- Sidewinder, SR Viper XTX, SR Viper XTX, 2016 Apex XTX and Pro-Line Pro Stock 1000
Apexallday - Yes, huge defect in the die. I believe this is why the casting mold was changed a few years ago (the clutch I just worked on was from a 2008 Nytro)
I am removing all flash inside the secondary and inspecting every clutch I work on.
What bothers me is that when I went to balance this clutch, I couldn't believe how this clutch could have even been balanced. On the pic after blasting with the 8BV01, where I show the moveable sheave (sheave without the steel shaft) from the backside, the mold was broken out by the date code pillar. Do you see it? Right on the web....about 1 o'clock when looking at the picture. Talk about having die issues.
I am removing all flash inside the secondary and inspecting every clutch I work on.
What bothers me is that when I went to balance this clutch, I couldn't believe how this clutch could have even been balanced. On the pic after blasting with the 8BV01, where I show the moveable sheave (sheave without the steel shaft) from the backside, the mold was broken out by the date code pillar. Do you see it? Right on the web....about 1 o'clock when looking at the picture. Talk about having die issues.

Winderallday!
VIP Member
- Joined
- Dec 4, 2007
- Messages
- 588
- Reaction score
- 167
- Points
- 1,058
- Location
- SW, Ontario
- Country
- Canada
- Snowmobile
- 2018 Sidewinder DX
Apexallday - Yes, huge defect in the die. I believe this is why the casting mold was changed a few years ago (the clutch I just worked on was from a 2008 Nytro)
I am removing all flash inside the secondary and inspecting every clutch I work on.
What bothers me is that when I went to balance this clutch, I couldn't believe how this clutch could have even been balanced. On the pic after blasting with the 8BV01, where I show the moveable sheave (sheave without the steel shaft) from the backside, the mold was broken out by the date code pillar. Do you see it? Right on the web....about 1 o'clock when looking at the picture. Talk about having die issues.[/QUOTE
Yeah, definitely see that, looks like it was welded up and feathered out. Would think this amount of extra aluminum would cause a significant balance issue unless it was done for a balancing issue in the first place due to another mold defect or error when cutting the die in the first place. Usually you see partially drilled holes to balance not wads of aluminum added.

- Joined
- Apr 14, 2003
- Messages
- 6,539
- Reaction score
- 3,171
- Points
- 1,983
- Location
- Hessel, Michigan
- Country
- USA
- Snowmobile
- Sidewinder, SR Viper XTX, SR Viper XTX, 2016 Apex XTX and Pro-Line Pro Stock 1000
it did make a huge difference in balancing....that is how I noticed it. Should see the drill point marks in the clutch now to balance it correctly. How this ever got balanced and passed is beyond me.
steveg_nh
TY 4 Stroke Junkie
- Joined
- Jul 23, 2017
- Messages
- 560
- Reaction score
- 82
- Points
- 238
- Location
- Southern NH
- Country
- USA
- Snowmobile
- 2007 Attak
So before I dig in here I just want to confirm the new secondary spring I got. I was under the impression it was going to be white. Given the part number and everybody saying I want the white spring. It has no white markings on it at all so how do I confirm this is not the wrong spring in the right bag?
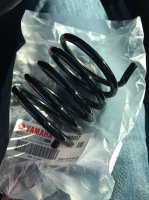
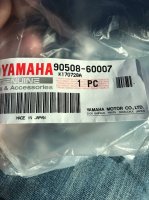
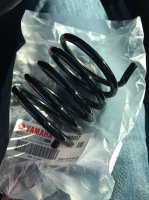
Last edited:

Winderallday!
VIP Member
- Joined
- Dec 4, 2007
- Messages
- 588
- Reaction score
- 167
- Points
- 1,058
- Location
- SW, Ontario
- Country
- Canada
- Snowmobile
- 2018 Sidewinder DX
So before I dig in here I just want to confirm the new secondary spring I got. I was under the impression it was going to be white. Given the part number and everybody saying I want the white spring. It has no white markings on it at all so how do I confirm this is not the wtong spring not just in the wrong bag?
View attachment 131067 View attachment 131068
Should be good to go Steve.
steveg_nh
TY 4 Stroke Junkie
- Joined
- Jul 23, 2017
- Messages
- 560
- Reaction score
- 82
- Points
- 238
- Location
- Southern NH
- Country
- USA
- Snowmobile
- 2007 Attak
Based in part number on bag yes but how can I confirm the spring? Number of turns? Thickness of coils?

Winderallday!
VIP Member
- Joined
- Dec 4, 2007
- Messages
- 588
- Reaction score
- 167
- Points
- 1,058
- Location
- SW, Ontario
- Country
- Canada
- Snowmobile
- 2018 Sidewinder DX
Based in part number on bag yes but how can I confirm the spring? Number of turns? Thickness of coils?
Lots of specs below the part number in the chart to verify the right spring.
steveg_nh
TY 4 Stroke Junkie
- Joined
- Jul 23, 2017
- Messages
- 560
- Reaction score
- 82
- Points
- 238
- Location
- Southern NH
- Country
- USA
- Snowmobile
- 2007 Attak
Thanks! I didn't look closely at the whole chart on my phone, so didn't see the other values. I'm sure it's right, but expected it to be white! Even the chart says white.
So when you mount the helix, and set the spring at 3-3, I know you have to forcibly turn the helix clockwise to get the bolt holes to line up. Just to confirm, you are just turning until the bolt hole aligns with the very next sheave hole, you aren't trying to wind it any more than that. Not that I think you could even do that extra turn by hand...

So when you mount the helix, and set the spring at 3-3, I know you have to forcibly turn the helix clockwise to get the bolt holes to line up. Just to confirm, you are just turning until the bolt hole aligns with the very next sheave hole, you aren't trying to wind it any more than that. Not that I think you could even do that extra turn by hand...
steveg_nh
TY 4 Stroke Junkie
- Joined
- Jul 23, 2017
- Messages
- 560
- Reaction score
- 82
- Points
- 238
- Location
- Southern NH
- Country
- USA
- Snowmobile
- 2007 Attak

RobX-1
VIP Member
- Joined
- Apr 13, 2003
- Messages
- 2,299
- Reaction score
- 1,482
- Points
- 1,583
- Location
- Coldwater, OH
- Country
- USA
- Snowmobile
- 18 50th Apex XT-X, 08 40th Apex LTX GT, 08 40th Nytro RTX, & 03 RX-1
Yep and if it was multi colored, you would have a line of that color to the left or right of the white line (eg. orange-pink-orange). Other than that one coil having the single dash or series of dashes is all there is.
steveg_nh
TY 4 Stroke Junkie
- Joined
- Jul 23, 2017
- Messages
- 560
- Reaction score
- 82
- Points
- 238
- Location
- Southern NH
- Country
- USA
- Snowmobile
- 2007 Attak
Ha ha. I expected it all to be white. Easily missed that.
Is my assumption correct about installing the spring, and how much you turn it clockwise before you put the bolts in? Just a third of a turn or whatever to get the holes the helix to line up with the first set of sheave holes it encounters?
Is my assumption correct about installing the spring, and how much you turn it clockwise before you put the bolts in? Just a third of a turn or whatever to get the holes the helix to line up with the first set of sheave holes it encounters?

- Joined
- Apr 14, 2003
- Messages
- 6,539
- Reaction score
- 3,171
- Points
- 1,983
- Location
- Hessel, Michigan
- Country
- USA
- Snowmobile
- Sidewinder, SR Viper XTX, SR Viper XTX, 2016 Apex XTX and Pro-Line Pro Stock 1000
Yamaha secondary springs will be all black with the color of the spring as a single dot. Primary Yamaha springs will have 3 colored dots to represent which spring it is.

Winderallday!
VIP Member
- Joined
- Dec 4, 2007
- Messages
- 588
- Reaction score
- 167
- Points
- 1,058
- Location
- SW, Ontario
- Country
- Canada
- Snowmobile
- 2018 Sidewinder DX
Thanks! I didn't look closely at the whole chart on my phone, so didn't see the other values. I'm sure it's right, but expected it to be white! Even the chart says white.
So when you mount the helix, and set the spring at 3-3, I know you have to forcibly turn the helix clockwise to get the bolt holes to line up. Just to confirm, you are just turning until the bolt hole aligns with the very next sheave hole, you aren't trying to wind it any more than that. Not that I think you could even do that extra turn by hand...
You are correct, the rotational force required to install the helix increases with the amount of twist angle spec (3+3=60 degrees, 6+1=70 degrees of twist etc), but generally 3+3 twist is fairly easy to attain by hand. I use an adjustable pin wrench in the available helix spring holes to rotate the helix ramps past the buttons then push helix into position over the three studs, then spin on the nuts to keep it from backing out.
As mentioned before, this is easier to do this with the clutch mounted on the secondary shaft/splines with the e-brake on. Need to keep inward force on the helix while doing this until you get at least one nut spun on a stud, as the spring tries to push the helix off the journal. An extra hand to hold and line up the back sheave with the studs into the helix is helpful but if you can do it solo, it saves on beers for your helper buddy

steveg_nh
TY 4 Stroke Junkie
- Joined
- Jul 23, 2017
- Messages
- 560
- Reaction score
- 82
- Points
- 238
- Location
- Southern NH
- Country
- USA
- Snowmobile
- 2007 Attak
Thanks. I just wanted to make sure I didn't have to spin the helix, say to the second hole or something, when putting it on. Just put it on, and spin clockwise until you get the holes to line up, no more needed.
steveg_nh
TY 4 Stroke Junkie
- Joined
- Jul 23, 2017
- Messages
- 560
- Reaction score
- 82
- Points
- 238
- Location
- Southern NH
- Country
- USA
- Snowmobile
- 2007 Attak
Really good progress this morning. Got the clutch pulled apart and cleaned. It was nasty and definitely sticky. Put the new buttons in (tapped them in with a small rubber mallet), shined everything up, and installed the new spring and put the helix back on. I was alone, of course, so I used spring clamps to hold the moveable sheave close to the fixed sheave so I could get the helix turned and set in place, and the nuts on. Set spring to 60 degrees (3-3).
I also added some shims, as the belt was sitting about 2mm below the top. Now it's about 1mm below. I have 1.5mm in shims on each screw now, so I need to swap out the 0.5mm shims for 1mm shims. Possibly should just leave the 1.5 and add 1 more for a total of 2.5mm. Seems a bit odd to need that much, but not going to overthink it. I guess the plates just need to pretty much touch with little standoff from the bolts at all. I did notice that when the plates were apart, that the 3 screws didn't seem to all be even though, as the moveable sheave rocked a bit, but looking at the design, precision isn't there.
Again, figure this isn't uncommon, as once together the belt was sitting the same all around. I haven't run it yet though, with the adjustments, so I will do that before I add another shim.

I also checked clutch alignment offset, and it was perfect at 15.5mm, and checked free play of the secondary, which was 1.2mm. All within spec.
I also added some shims, as the belt was sitting about 2mm below the top. Now it's about 1mm below. I have 1.5mm in shims on each screw now, so I need to swap out the 0.5mm shims for 1mm shims. Possibly should just leave the 1.5 and add 1 more for a total of 2.5mm. Seems a bit odd to need that much, but not going to overthink it. I guess the plates just need to pretty much touch with little standoff from the bolts at all. I did notice that when the plates were apart, that the 3 screws didn't seem to all be even though, as the moveable sheave rocked a bit, but looking at the design, precision isn't there.


I also checked clutch alignment offset, and it was perfect at 15.5mm, and checked free play of the secondary, which was 1.2mm. All within spec.
Similar threads
- Replies
- 4
- Views
- 1K
-
This site uses cookies to help personalise content, tailor your experience and to keep you logged in if you register.
By continuing to use this site, you are consenting to our use of cookies.