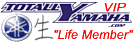

Looks to be the same as the one in lower right. Fan relay. Swapping them is also a option. What is the significance of the c1219 vs c1314 ?Pic of fusebox and relays. ISC relay (Idle Speed Control) blue. Maybe guys with poor idling will test and change the relay?
View attachment 124553
Janne339
TY 4 Stroke Junkie
- Joined
- Oct 31, 2015
- Messages
- 559
- Reaction score
- 395
- Points
- 738
- Location
- Sweden
- Country
- Sweden
- Snowmobile
- 2021 Sidewinder LTX GT
I wonder as well? Maybe Grizztracks know C1219 vs C1314?

grizztracks
Tech Advisor
- Joined
- Feb 24, 2005
- Messages
- 3,116
- Reaction score
- 970
- Points
- 1,753
- Location
- Scio, NY
- Country
- USA
- Snowmobile
- FX Nytro RTX, RS Vector, SR Viper RTX SE
According to the parts diagram all five of the 4 pin relays are the same so they all should be interchangeable. I don't see any reference to those extra numbers so I believe it's irrelevant.
Relay, 4-pin (20 amp)
Part# 8JP-H2189-00-00
The two shift relays are 5-pin (30 amp)
Part# 8JP-H2185-00-00
Relay, 4-pin (20 amp)
Part# 8JP-H2189-00-00
The two shift relays are 5-pin (30 amp)
Part# 8JP-H2185-00-00
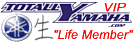

Get this. Here is mine. All the same number. Is that a Chinese Relay?
Janne339
TY 4 Stroke Junkie
- Joined
- Oct 31, 2015
- Messages
- 559
- Reaction score
- 395
- Points
- 738
- Location
- Sweden
- Country
- Sweden
- Snowmobile
- 2021 Sidewinder LTX GT
I guess it Chinese. I have been looking on Bosch relay but not found any replacement yet.
Janne339
TY 4 Stroke Junkie
- Joined
- Oct 31, 2015
- Messages
- 559
- Reaction score
- 395
- Points
- 738
- Location
- Sweden
- Country
- Sweden
- Snowmobile
- 2021 Sidewinder LTX GT
Found this when reading on Omron relays website.
Janne339
TY 4 Stroke Junkie
- Joined
- Oct 31, 2015
- Messages
- 559
- Reaction score
- 395
- Points
- 738
- Location
- Sweden
- Country
- Sweden
- Snowmobile
- 2021 Sidewinder LTX GT
The ISC relay powers all these systems through it's contacts from the same power feed that powers it's own control coil
I'm not have the knowledge so I don't understand that? Why use a relay when the control coil and contacts using the same power feed? What is the advantage?
What happens if you "strap" the ISC relay?
Last edited:
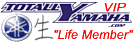

Mike P
Lifetime Member
- Joined
- Nov 18, 2015
- Messages
- 564
- Reaction score
- 276
- Points
- 808
- Location
- Berlin CT
- Country
- USA
- Snowmobile
- Sr Viper R-TX SE
- LOCATION
- Berlin CT
If the source voltage, the battery can not be maintained at any point in a circuit then from that point forward all voltage to ground will suffer. If a connection is made before the primary load in this case the starter the voltage will be less susceptible to the affects of load induced voltage drop.The control voltage is sourced at the line-side of the starter solenoid. The voltage will drop while cranking and I believe the engineers have not missed this when they designed the system.Mike you do understand that what we are thinking is the issue is voltage drop to ECU. Not the starter but it also is highly important due to the voltage drop at ECU to have a real good battery and all connections. Critical.
However in our circuit we are limited by the components in the circuit installed by the manufacturer. The battery, wire size, length of wire, connection type(solder or press fit), circuit configuration(key to relay...) and the quality of these components will all contribute to the efficiency of an electrical circuit. Every component needs to be at its functional best or the others will suffer in some way. I do not have any of the problems or issues suggested in this thread and others. My battery was a little weak back in November and I did notice some unusual issues while cranking. I put a jump start on and fired right up in the shop at 55 degrees. A simple;
NOCO Genius Boost Plus GB40 1000 Amp 12V UltraSafe Lithium Jump Starter
I did connect a second 12v anti-gravity (lipo-4) battery to the feed for the fuse block, with a Shockley diode to prevent the two batteries from seeing each other. This fixed the issue with the voltage drop. I located the battery right next to the fuse block unfortunately the manufacturer of the Lipo-4 recommended removing it from the circuit. They did not want the two different types of battery installed for fear of any type of reaction.
My friend with his LTX-LE turbo has hot start issues but he noticed it only happens when his oil light comes on. After turning the key on and off until the light goes out he is then able to fire it up. This is an issue that he has had from day one pre turbo. That shouldn't be hard for find.
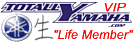

Mike P
Lifetime Member
- Joined
- Nov 18, 2015
- Messages
- 564
- Reaction score
- 276
- Points
- 808
- Location
- Berlin CT
- Country
- USA
- Snowmobile
- Sr Viper R-TX SE
- LOCATION
- Berlin CT
Omron has put in one paragraph exactly what a low-voltage or under-voltage condition in a control circuit will do to the stability of an energized circuit. If a gasoline fired motor requires a fuel to be at a certain octane and the same motor is then used with a different type of fuel the results will be different than the design spec. The same would apply to electrical circuits, voltage representing the fuel and octane would be the 9.5, 11, 12-volts . Motor or circuit design, both depend on all of the components working together, but if the octane or the voltage is wrong....
It was just an analogy that came to mine while reading that paragraph.
Last edited:
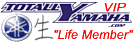

If replacing these relays here is best source I found. I have not bought yet so please confirm its the correct relay. I am attempting to find a Solid State replacement. Not focusing too much on the relay though since it is not the main issue but could definitely contribute.
http://www.mouser.com/ProductDetail...=sGAEpiMZZMt98bArVJter/6pJWs6UE7HFCuJUoV5z3k=
http://www.mouser.com/ProductDetail...=sGAEpiMZZMt98bArVJter/6pJWs6UE7HFCuJUoV5z3k=
Janne339
TY 4 Stroke Junkie
- Joined
- Oct 31, 2015
- Messages
- 559
- Reaction score
- 395
- Points
- 738
- Location
- Sweden
- Country
- Sweden
- Snowmobile
- 2021 Sidewinder LTX GT
If replacing these relays here is best source I found. I have not bought yet so please confirm its the correct relay. I am attempting to find a Solid State replacement. Not focusing too much on the relay though since it is not the main issue but could definitely contribute.
http://www.mouser.com/ProductDetail/Song-Chuan/303-1AH-C-R1-U01-12VDC/?qs=sGAEpiMZZMt98bArVJter/6pJWs6UE7HFCuJUoV5z3k=
Yes, this seems to be the stock relays.
I will said it's a big issue if they not works properly during cranking.
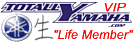

Right. Maybe rotation with miles might be a good idea? Being mechanical they have to wear and become weaker over time. I wonder when they wear if they would tend to wear to the closed or open position? I would think to the closed but the contacts to the open. Which wears first? Grizz would know. I am thinking corrosion and pitting of contacts would be first.
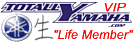

Mike P
Lifetime Member
- Joined
- Nov 18, 2015
- Messages
- 564
- Reaction score
- 276
- Points
- 808
- Location
- Berlin CT
- Country
- USA
- Snowmobile
- Sr Viper R-TX SE
- LOCATION
- Berlin CT
The pick-up and drop-out voltage would seem to be pretty darn good, probably more important than most might think in this situation. Looking at the data sheet for the relay in your link it looks very good. An interesting read from Panasonic;If replacing these relays here is best source I found. I have not bought yet so please confirm its the correct relay. I am attempting to find a Solid State replacement. Not focusing too much on the relay though since it is not the main issue but could definitely contribute.
http://www.mouser.com/ProductDetail/Song-Chuan/303-1AH-C-R1-U01-12VDC/?qs=sGAEpiMZZMt98bArVJter/6pJWs6UE7HFCuJUoV5z3k=
One common electrical characteristic that is specified of relays is the pick up and drop out voltage. These values are defined as follows: Pick up voltage (also defined as pull in voltage, or must operate voltage): As the voltage of a de-energized relay is increased, the value at or below which all contacts must function. Drop out voltage (also defined as release, or must release voltage): As the voltage on an energized relay is decreased, the value at or above which all contacts must return to their de-energized position. These values are important to engineers when certain designs are required to function within a certain voltage range. For example, let's say a 12V relay is being used to turn on a motor. The motor will function as long as the contacts are closed. However, if for some reason the voltage input to the relay is decreased to a certain level, the contacts will open and the motor will turn off. Therefore, it is important that pick and and drop out voltage values are considered when designing any type of project that may cause the input voltage of the relay to fluctuate (i.e. battery input). Pick up voltage and drop out voltage values are simple to measure. A power supply and a digital multi-meter are the only two components needed. The following schematic can be used for measurement:

- Set the DMM (Digital Multimeter) in Continuity mode
- Connect t he leads to the common and the normally open terminal pins.
- Slowly begin to increase the "coil power supply."
- When the DMM beeps, it means the contacts have engaged and current is detected.
- The voltage reading on the "coil power supply" is called the Pick Up Voltage.
- Continue to increase the "coil power supply" to the nomical coil voltage of the relay.
- Now slowly decrease the "coil power supply" output.
- When the DMM turns off (or stops beeping), it means the contacts have disengaged.
- The reading on the "coil power supply" is the Drop Out Voltage.
Janne339
TY 4 Stroke Junkie
- Joined
- Oct 31, 2015
- Messages
- 559
- Reaction score
- 395
- Points
- 738
- Location
- Sweden
- Country
- Sweden
- Snowmobile
- 2021 Sidewinder LTX GT
Not sure I understand everything, but the coils in the Viper relays gets the power when turning the start key on? After that the contacts in the relays close and feed their components?

grizztracks
Tech Advisor
- Joined
- Feb 24, 2005
- Messages
- 3,116
- Reaction score
- 970
- Points
- 1,753
- Location
- Scio, NY
- Country
- USA
- Snowmobile
- FX Nytro RTX, RS Vector, SR Viper RTX SE
Moisture and cold weather will eventually cause corrosion and freeze up of these relays like we see in all snowmobiles that run mechanical contact relays. I'm not sure of the quality of the relays being used but their specs are acceptable for most automotive applications. A pickup voltage of 7.2 volts should be sufficient however that spec is under ideal conditions, What happens when the temperature drops well below freezing and over time corrosion creates connection issues. The drop out voltage also could be much higher than the 1 volt so in reality it could be as high as the pickup voltage spec. The big problem I see here is that there are 3 relays that have to be powered for the engine to run so if any one of them fails it could leave you stranded. If the ECU is experiencing a low voltage situation then one way to correct the issue is to conserve power during the start cycle. Using solid state relays would be more reliable and also lower power consumption because they require very little voltage to activate them. I've also read that the O2 sensor is no longer needed with the new flash. If this is true was it removed to eliminate the O2 sensor's heater circuit load on the ECU?
I'd really like to know the logic behind the "engine kickback feature"................. Is it simply disabling the ignition outputs if a low voltage to the ECU is detected? I'm thinking so!
I'd really like to know the logic behind the "engine kickback feature"................. Is it simply disabling the ignition outputs if a low voltage to the ECU is detected? I'm thinking so!
Similar threads
-
This site uses cookies to help personalise content, tailor your experience and to keep you logged in if you register.
By continuing to use this site, you are consenting to our use of cookies.