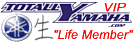

- Joined
- Nov 1, 2009
- Messages
- 3,564
- Location
- Winnipeg, Manitoba
- Country
- Canada
- Snowmobile
- 2009 Phazer RTX
MrSled said:PAvector said:09-12 Venture Gt stud protectors are only availible in Canada. With cost, shipping fees and many taxes your close to $300 to the US. Bought mine from a dealer right above Monteal.
Can you post the part number?
SMA-8ET21-50-10
http://www.yamaha-motor.ca/accessories/ ... model=3780
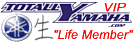

darv
Lifetime Member
- Joined
- Aug 9, 2005
- Messages
- 1,443
- Age
- 63
- Location
- International Falls,minnesota
- Country
- USA
- Snowmobile
- 08 Apex 40th LTX
i have a set / kit i do not need if some one wants them let me know
Be sure not to drill thru the gas tank when installing the front rivets. I skipped two of them because they would have been rubbing the tank. The skid, all the seats, seat supports and rear exhaust have to be removed. Strip it down to the tunnel top and bottom to install them. Gas tank can stay. It takes a few hours. When reinstalling the rear seat support, be carefull not to scratch the tunnel.
RSVentureCDN
Newbie
I can verify that SMA-8ET21-50-01 does fit the 2009 RS Venture. It took me about 8 hrs, not a small task. The second time might go a little easier.
gcr3903
Pro
- Joined
- Jan 31, 2007
- Messages
- 188
- Age
- 63
- Location
- Phillips, WI. - U.S.A. -
- Country
- USA
- Snowmobile
- 2004 RX-1
SAB1 said:Jst double checking, for the RS Venture your saying 108 picks? What picks do you recommend? Size?
108 makes no sense, seeing as the tracks a 144. Or am I wrong? My 05 RS Venture pushes so hard in the corners, I can't imagine it with studs.

gcr3903
Pro
- Joined
- Jan 31, 2007
- Messages
- 188
- Age
- 63
- Location
- Phillips, WI. - U.S.A. -
- Country
- USA
- Snowmobile
- 2004 RX-1
It's long but, here goes! Found online.
Here is what you need to consider when picking out your traction products and installing them:
What is your riding style and where are you riding?
The same snowmobile lightly ridden by a lightweight rider will normally require up to half as many studs as one ridden all-out by a heavier rider. Only you can determine exactly the type and quantity of studs you will need for your exact application. Manufacturers guides are a great place to get a ballpark figure of what you will need to get started. The goal is to have just enough studs to keep the track from spinning uncontrollably under normal maximum acceleration in your normal areas conditions. Any more and you risk chattering from lack of penetration, any less you risk damage to the studs and track from over stressing the studs and track holes.
Myth: "Running a larger number of studs weakens the track, so running less is better"
Fact: Absolutely wrong. If it takes you 192 studs to keep you from spinning uncontrollably in normal conditions, it is far better than over stressing 144 studs and destroying them by accidentally doing a burnout over a gravel bed. The extra weight is a small price you will have to pay for your aggressive riding. Yes, it will cut your top end speed down, but if you are going 105, wouldn't you rather have 192 studs stopping you when the deer jumps out into the trail, or your friend stops in front of you suddenly. I know I do. When you under stud you are over stressing the rubber in the track around the studs. This causes bent backers, cord damage and tear outs. Also, stud head size has a lot less to do with tear-outs than properly tightened nuts and correct length studs do.
With that being said, you have a snowmobile with the stock track in good or new condition and you want to select the proper type, size, length, and pattern to install. This is easier than you think.
This guide is geared toward trail riding with possibly a little fun lake racing against friends occasionally. If you are setting up for racing you probably know what you need anyway so we will concentrate only with carbide studs. Carbide tipped studs have shafts of super-hard Tungsten Carbide brazed into the alloy steel body of the stud. If the entire stud were made from carbide, it would fracture immediately because it offers very little fracture resistance as a whole. It does offer excellent abrasion resistance when you need to cross a road or travel through gravel. If you are trail riding you want carbide tipped studs. A solid steel, aluminum, or titanium stud will be worthlessly dull after the first ride on anything but ice.
The next thing you will want to consider is type. Conventional studs are generally two-piece or push thru. On lower horsepower sleds, you can get away with the older design of the two-piece, stud and t-nut. These are less reliable than the one-piece push through design that has come about and taken over the market of studs. Since push through studs are the most popular, I will concentrate on those primarily. You will typically find two sizes of push through studs, 7mm thread and 5/16" thread (about 8mm). 7mm, the smaller of the two, are used again, on the smaller or lower horsepower sleds. They are lighter but more fragile than the 5/16" thread studs and can't take near the amount of punishment. Normally just the thing for 340, 440 or 500cc sleds lightly ridden with short lug tracks. Anything more and you will probably want the larger shank.
When you have a modern sled with a decent amount of horsepower you will want the 5/16" thread studs. The next thing you will want to decide on is the material. You will find steel and stainless steel studs to choose from. If you absolutely have to have corrosion resistance, go with the stainless steel. A hardened alloy steel stud will be stronger due to the nature of the materials used. One short ride is all that is generally needed to take a set of lightly rusted steel studs and have them looking shiny again. Don't let appearance make your mind up for you.
Next you will have to determine what length you will need for your track. This is by far the most confusing part. The big key is knowing exactly what your track lug height is. You are trying to pick studs that extend over the tips of your lugs by 1/4-3/8". Always ask for the exact overall length of the stud you are buying and compare that to the overall thickness of your track. Due to the differences in manufacturers measuring systems, that is the only way you can be sure you are getting the right length.
Here is a scenario that may help. Say you have a 1" lug track on your sled. The lug sticks out almost 1" but the overall thickness of the track ends up at about 1-1/8" (which is typical and common). When you ask the seller what size you need you are told 1.075" (which is the recommend SPEC size). You ask yourself, "How am I supposed to have .25-.375 above my lug when my track is 1" lug (1-1/8" overall)?" What you need to confirm is the overall length. The major manufacturers, Accord Racing (formerly Saber), Woody's and Stud Boy all measure from the top of a typical backer plate. This is a system which was derived from the two-piece stud and was meant to be less confusing (go figure). Other measuring systems exist, which only add to the confusion. Anyhow, a 1.075 stud is indeed, 1-1/2" in overall length. When you subtract your 1-1/8" overall track thickness you have a difference of 3/8", which is your penetration. Confused yet? Hope not. Basically, always ask the overall length to avoid damage to your sled, a waste of money or return shipping charges.
Once you know the size you need and the basic type you want, you can start deciding between the 30-50 product lines available for different types of studs. Don't get exotic here. Carefully compare the top sellers for each manufacturer. Each manufacturer generally has premium studs, value line studs and the rest considered specialty application studs. Here is where you need to consider how long you intend to use them, whether you would replace them if they were to wear out, and if you have a special application that would prevent you from running the most popular studs. If you put on 500 miles a year and plan on having the sled 4 years, a value line stud might be fine for you. If you put on 2000 miles per year and intend on running it into the ground you would want only the highest quality studs because of the time lost every year you might spend replacing inferior products.
Once you have a quantity, you can choose a pattern to fit your sled and riding style. USE A TEMPLATE. All manufacturers have them available. It will make a huge difference in the amount of time it takes to stud your sled and how well your scratch lines line up. USE A TRACK DRILL. It is a hollowed piece of sharpened steel that works great spinning in a drill. It will make a clean hole very fast. DO NOT MELT THROUGH YOUR TRACK WITH ANYTHING. Heat, other than the heat naturally created from the spinning drill, is strongly discouraged. Heat applied to the holes, or creating holes with a hot object wrecks the vulcanizing of the rubber in the area around the stud where you need strength the most. For track drills, all manufacturers sell them and they have the same basic function and design. Make sure you have the right size drill for your traction products, there are a couple different sizes for different studs. You should be able to insert a push through style stud through the track with just the pressure from your hands. Any tighter is un-necessary and usually means you have the wrong drill or your drill is dull.
The most popular pattern for mid-low horsepower applications has been 96 or 144 in the center belt. These patterns have proven to give longer track life than most tracks with an inside/outside pattern. Studding outside the rails has proven less reliable for most, simply because the outside studs tend to be held in by fewer cords, less track area, and are subject to more abuse than the center cords. This is not to say that studding the outside cannot be done or shouldn't be done, it is almost necessary on some applications, especially higher horsepower sleds, where there isn't enough area to install the required amount of studs in the center belt alone.
The all center belt stud patterns will give you a looser feel in the corners, making it easier to steer. You can normally keep a higher speed through the turns because sled will push less. Typically, an inside/outside pattern will require longer carbide length on the skis to compensate for the added cornering traction. Because the sled requires more effort to turn, (studs covering wider/larger surface area) cornering normally becomes slower, though you may feel more control over the sled. Braking and accelerating are improved with inside/outside patterns, which is another reason they lend themselves more heavily to racing or performance trail applications. The reliability of an "up the middle" pattern normally outweighs any accelerating/braking performance difference on the average trail sled. Stud patterns have been an arguing point in the snowmobiling world, and are usually explained terribly. Hopefully this information has been easy enough to understand.
Your backer selection should work in conjunction with your pattern. The backer is a washer that sandwiches the track, using the head of the stud on the inside; they go under the nut on the outside of the track. Individual backers are by far the easiest to install, however double backers (a washer with two holes side by side) are also available. The backers should have properties that lend themselves to your riding style. For instance, steel, nylon, hard plastic and aluminum are normal materials backers are typically made out of.
Steel is normally reserved for applications where weight is not a concern or where serious punishment is typical. Because of the increasing strength, and lower weight of new aluminum backer designs, steel backers have fallen by the wayside in popularity.
Aluminum backers have become very popular for aggressive trail riding and racing due to their relative light weight, and design adaptability. These should be used where maximum rigidity and penetration are required. The only drawback to running aluminum backers is, when the stud is held rigidly, damage to the stud, backer, or track is more likely than when the stud is fastened less rigidly. This is normally an acceptable risk for the performance minded rider.
Nylon backers lend themselves perfectly to trail riding and any application where stud life is a major concern. The nylon backers allow a bit of flex and resiliency when compared to aluminum, making them perfect for trail riding where debris in the trail, uneven terrain and a host of other unknowns stress tracks and studs beyond normal limits for brief periods. Ice traction will be reduced when compared to an aluminum backer application, due to the studs ability to deflect under load, however longevity of both the stud and backer are improved under trail conditions.
Hard plastic backers aren't as popular and can typically be found sold with generic stud sets due to low cost it takes to produce them. I haven't found a hard plastic backer that provides outstanding support or resiliency, at least enough to bother offering them as well as nylon and aluminum.
For single backers, the latest designs of round backers tend to be the easiest to install and the least hassle to maintain. You'll want a backer that provides equal squish around the entire perimeter of the stud head area, and normally a round backer does that the best. Square backers transfer the stud-load more equally into the track cords, however if they rotate (which they normally do over time) the results are less desirable than a round, since the tip of the backer is now pressing harder than the rest of the backer. Backer shape is normally a matter of personal preference as long as they are well suited to the studs you want to run.
You will want to drill a pattern that offers about 1/4" spacing between each studs' position and the position next to it. These are called scratch lines and allow each row of studs to bite into a specific area under the track. Why not just make a couple of neat rows all in the same places and repeat all the way around the track? If you line up too many studs in a row in the track, the first stud to hit the ice will carve a narrow trench. The next studs to come by will fit right in that trench and keep you from carving any new ice until you start to get moving. For instance, when installing 96 studs up the middle (two per row on a 48 lug track), if you start with a pair of studs close to the slide rails, and move 1/4" in on each side for the next row and again for the subsequent rows, once you get to the 8th row you will have a pattern with 16 different positions (scratch lines) and a pattern that only repeats every 20". This is ideal for that situation. 144 up the center gets a bit more crowded, forcing you to make more scratch lines and move closer to the center of the track to keep an 8 lug repeating pattern. For instance, you might need 20 or 24 different scratch lines to keep the pattern repeating every 8 rows. This is the reason 192 up the middle doesn't work so great, you end up either crowding the scratch lines, or repeating the pattern every 4 or 6 lugs which eliminates any benefit the added studs would have provided. A 3-4-3-4 pattern (168 on a 121" track) is usually the limit for effective stud placement in the center belt of a normal snowmobile track. Again, some may argue with this information, however this is simply knowledge gained from thousands of miles of trail riding, and thousands of conversations on the phone and in person with snowmobilers who have tried everything imaginable.
To drill your track out, you will want to remove the drive belt to allow you to spin the track easily by hand. You can either hoist the rear of the sled up and work under the snow flap or turn the snowmobile on it's side and work on the bottom of the track. If you hoist the machine in the air, you might want to consider removing the rear suspension bolts to let the suspension hang down, allowing you better access at the now loosened track. Mark out the entire pattern with a paint marker and make sure your backers won't interfere with each other and make sure the pattern looks correct for your style of track. Also make sure that there won't be any interference with the bulkhead and tunnel when you install the studs. It is a good idea to drill the first hole and install one stud, cycling it around the entire track, watching for any close clearance areas between the stud and the snowmobile. Once everything looks alright, go ahead and drill the rest of the holes using the drill tool previously mentioned.
Once the entire track is drilled, go ahead and start putting a small batch of studs through the track. Before cycling the track to add more, tighten these into the track with the backers until the heads have pulled up to the back face of the track which will allow them to travel around the suspension and drive cogs without causing damage or getting stuck. Work on about 4-8 at a time until all of the studs are installed and ready for final tightening. You will want to do the final tightening with a torque wrench. Most 5/16" studs with steel nuts and aluminum backers require 15 ft lbs of torque. Nylon backers may require less, check with the manufacturer of the traction products. Exceeding this torque specification will not bring the stud heads in any tighter, it will only put you at risk for stripped threads or broken studs. Torquing the nut actually stretches the stud just enough to keep it tight, any less, and it could loosen, and more and it could break. You should re-torque the nyloc nuts on your studs after the first ride and periodically afterward. Loose studs cause pull throughs, less studs pulled through is obviously better for your tracks life.
Tunnel protectors are absolutely necessary when using studs. Tunnel protectors (or heat exchanger protectors) stop the outer tips of the rubber lugs on the track from getting so close to the tunnel that the studs would hit and damage another part of the snowmobile, like the tunnel or a heat exchanger. Some snowmobiles come with tunnel protectors built in, others require them to be added if you want to run studs.
Here is what you need to consider when picking out your traction products and installing them:
What is your riding style and where are you riding?
The same snowmobile lightly ridden by a lightweight rider will normally require up to half as many studs as one ridden all-out by a heavier rider. Only you can determine exactly the type and quantity of studs you will need for your exact application. Manufacturers guides are a great place to get a ballpark figure of what you will need to get started. The goal is to have just enough studs to keep the track from spinning uncontrollably under normal maximum acceleration in your normal areas conditions. Any more and you risk chattering from lack of penetration, any less you risk damage to the studs and track from over stressing the studs and track holes.
Myth: "Running a larger number of studs weakens the track, so running less is better"
Fact: Absolutely wrong. If it takes you 192 studs to keep you from spinning uncontrollably in normal conditions, it is far better than over stressing 144 studs and destroying them by accidentally doing a burnout over a gravel bed. The extra weight is a small price you will have to pay for your aggressive riding. Yes, it will cut your top end speed down, but if you are going 105, wouldn't you rather have 192 studs stopping you when the deer jumps out into the trail, or your friend stops in front of you suddenly. I know I do. When you under stud you are over stressing the rubber in the track around the studs. This causes bent backers, cord damage and tear outs. Also, stud head size has a lot less to do with tear-outs than properly tightened nuts and correct length studs do.
With that being said, you have a snowmobile with the stock track in good or new condition and you want to select the proper type, size, length, and pattern to install. This is easier than you think.
This guide is geared toward trail riding with possibly a little fun lake racing against friends occasionally. If you are setting up for racing you probably know what you need anyway so we will concentrate only with carbide studs. Carbide tipped studs have shafts of super-hard Tungsten Carbide brazed into the alloy steel body of the stud. If the entire stud were made from carbide, it would fracture immediately because it offers very little fracture resistance as a whole. It does offer excellent abrasion resistance when you need to cross a road or travel through gravel. If you are trail riding you want carbide tipped studs. A solid steel, aluminum, or titanium stud will be worthlessly dull after the first ride on anything but ice.
The next thing you will want to consider is type. Conventional studs are generally two-piece or push thru. On lower horsepower sleds, you can get away with the older design of the two-piece, stud and t-nut. These are less reliable than the one-piece push through design that has come about and taken over the market of studs. Since push through studs are the most popular, I will concentrate on those primarily. You will typically find two sizes of push through studs, 7mm thread and 5/16" thread (about 8mm). 7mm, the smaller of the two, are used again, on the smaller or lower horsepower sleds. They are lighter but more fragile than the 5/16" thread studs and can't take near the amount of punishment. Normally just the thing for 340, 440 or 500cc sleds lightly ridden with short lug tracks. Anything more and you will probably want the larger shank.
When you have a modern sled with a decent amount of horsepower you will want the 5/16" thread studs. The next thing you will want to decide on is the material. You will find steel and stainless steel studs to choose from. If you absolutely have to have corrosion resistance, go with the stainless steel. A hardened alloy steel stud will be stronger due to the nature of the materials used. One short ride is all that is generally needed to take a set of lightly rusted steel studs and have them looking shiny again. Don't let appearance make your mind up for you.
Next you will have to determine what length you will need for your track. This is by far the most confusing part. The big key is knowing exactly what your track lug height is. You are trying to pick studs that extend over the tips of your lugs by 1/4-3/8". Always ask for the exact overall length of the stud you are buying and compare that to the overall thickness of your track. Due to the differences in manufacturers measuring systems, that is the only way you can be sure you are getting the right length.
Here is a scenario that may help. Say you have a 1" lug track on your sled. The lug sticks out almost 1" but the overall thickness of the track ends up at about 1-1/8" (which is typical and common). When you ask the seller what size you need you are told 1.075" (which is the recommend SPEC size). You ask yourself, "How am I supposed to have .25-.375 above my lug when my track is 1" lug (1-1/8" overall)?" What you need to confirm is the overall length. The major manufacturers, Accord Racing (formerly Saber), Woody's and Stud Boy all measure from the top of a typical backer plate. This is a system which was derived from the two-piece stud and was meant to be less confusing (go figure). Other measuring systems exist, which only add to the confusion. Anyhow, a 1.075 stud is indeed, 1-1/2" in overall length. When you subtract your 1-1/8" overall track thickness you have a difference of 3/8", which is your penetration. Confused yet? Hope not. Basically, always ask the overall length to avoid damage to your sled, a waste of money or return shipping charges.
Once you know the size you need and the basic type you want, you can start deciding between the 30-50 product lines available for different types of studs. Don't get exotic here. Carefully compare the top sellers for each manufacturer. Each manufacturer generally has premium studs, value line studs and the rest considered specialty application studs. Here is where you need to consider how long you intend to use them, whether you would replace them if they were to wear out, and if you have a special application that would prevent you from running the most popular studs. If you put on 500 miles a year and plan on having the sled 4 years, a value line stud might be fine for you. If you put on 2000 miles per year and intend on running it into the ground you would want only the highest quality studs because of the time lost every year you might spend replacing inferior products.
Once you have a quantity, you can choose a pattern to fit your sled and riding style. USE A TEMPLATE. All manufacturers have them available. It will make a huge difference in the amount of time it takes to stud your sled and how well your scratch lines line up. USE A TRACK DRILL. It is a hollowed piece of sharpened steel that works great spinning in a drill. It will make a clean hole very fast. DO NOT MELT THROUGH YOUR TRACK WITH ANYTHING. Heat, other than the heat naturally created from the spinning drill, is strongly discouraged. Heat applied to the holes, or creating holes with a hot object wrecks the vulcanizing of the rubber in the area around the stud where you need strength the most. For track drills, all manufacturers sell them and they have the same basic function and design. Make sure you have the right size drill for your traction products, there are a couple different sizes for different studs. You should be able to insert a push through style stud through the track with just the pressure from your hands. Any tighter is un-necessary and usually means you have the wrong drill or your drill is dull.
The most popular pattern for mid-low horsepower applications has been 96 or 144 in the center belt. These patterns have proven to give longer track life than most tracks with an inside/outside pattern. Studding outside the rails has proven less reliable for most, simply because the outside studs tend to be held in by fewer cords, less track area, and are subject to more abuse than the center cords. This is not to say that studding the outside cannot be done or shouldn't be done, it is almost necessary on some applications, especially higher horsepower sleds, where there isn't enough area to install the required amount of studs in the center belt alone.
The all center belt stud patterns will give you a looser feel in the corners, making it easier to steer. You can normally keep a higher speed through the turns because sled will push less. Typically, an inside/outside pattern will require longer carbide length on the skis to compensate for the added cornering traction. Because the sled requires more effort to turn, (studs covering wider/larger surface area) cornering normally becomes slower, though you may feel more control over the sled. Braking and accelerating are improved with inside/outside patterns, which is another reason they lend themselves more heavily to racing or performance trail applications. The reliability of an "up the middle" pattern normally outweighs any accelerating/braking performance difference on the average trail sled. Stud patterns have been an arguing point in the snowmobiling world, and are usually explained terribly. Hopefully this information has been easy enough to understand.
Your backer selection should work in conjunction with your pattern. The backer is a washer that sandwiches the track, using the head of the stud on the inside; they go under the nut on the outside of the track. Individual backers are by far the easiest to install, however double backers (a washer with two holes side by side) are also available. The backers should have properties that lend themselves to your riding style. For instance, steel, nylon, hard plastic and aluminum are normal materials backers are typically made out of.
Steel is normally reserved for applications where weight is not a concern or where serious punishment is typical. Because of the increasing strength, and lower weight of new aluminum backer designs, steel backers have fallen by the wayside in popularity.
Aluminum backers have become very popular for aggressive trail riding and racing due to their relative light weight, and design adaptability. These should be used where maximum rigidity and penetration are required. The only drawback to running aluminum backers is, when the stud is held rigidly, damage to the stud, backer, or track is more likely than when the stud is fastened less rigidly. This is normally an acceptable risk for the performance minded rider.
Nylon backers lend themselves perfectly to trail riding and any application where stud life is a major concern. The nylon backers allow a bit of flex and resiliency when compared to aluminum, making them perfect for trail riding where debris in the trail, uneven terrain and a host of other unknowns stress tracks and studs beyond normal limits for brief periods. Ice traction will be reduced when compared to an aluminum backer application, due to the studs ability to deflect under load, however longevity of both the stud and backer are improved under trail conditions.
Hard plastic backers aren't as popular and can typically be found sold with generic stud sets due to low cost it takes to produce them. I haven't found a hard plastic backer that provides outstanding support or resiliency, at least enough to bother offering them as well as nylon and aluminum.
For single backers, the latest designs of round backers tend to be the easiest to install and the least hassle to maintain. You'll want a backer that provides equal squish around the entire perimeter of the stud head area, and normally a round backer does that the best. Square backers transfer the stud-load more equally into the track cords, however if they rotate (which they normally do over time) the results are less desirable than a round, since the tip of the backer is now pressing harder than the rest of the backer. Backer shape is normally a matter of personal preference as long as they are well suited to the studs you want to run.
You will want to drill a pattern that offers about 1/4" spacing between each studs' position and the position next to it. These are called scratch lines and allow each row of studs to bite into a specific area under the track. Why not just make a couple of neat rows all in the same places and repeat all the way around the track? If you line up too many studs in a row in the track, the first stud to hit the ice will carve a narrow trench. The next studs to come by will fit right in that trench and keep you from carving any new ice until you start to get moving. For instance, when installing 96 studs up the middle (two per row on a 48 lug track), if you start with a pair of studs close to the slide rails, and move 1/4" in on each side for the next row and again for the subsequent rows, once you get to the 8th row you will have a pattern with 16 different positions (scratch lines) and a pattern that only repeats every 20". This is ideal for that situation. 144 up the center gets a bit more crowded, forcing you to make more scratch lines and move closer to the center of the track to keep an 8 lug repeating pattern. For instance, you might need 20 or 24 different scratch lines to keep the pattern repeating every 8 rows. This is the reason 192 up the middle doesn't work so great, you end up either crowding the scratch lines, or repeating the pattern every 4 or 6 lugs which eliminates any benefit the added studs would have provided. A 3-4-3-4 pattern (168 on a 121" track) is usually the limit for effective stud placement in the center belt of a normal snowmobile track. Again, some may argue with this information, however this is simply knowledge gained from thousands of miles of trail riding, and thousands of conversations on the phone and in person with snowmobilers who have tried everything imaginable.
To drill your track out, you will want to remove the drive belt to allow you to spin the track easily by hand. You can either hoist the rear of the sled up and work under the snow flap or turn the snowmobile on it's side and work on the bottom of the track. If you hoist the machine in the air, you might want to consider removing the rear suspension bolts to let the suspension hang down, allowing you better access at the now loosened track. Mark out the entire pattern with a paint marker and make sure your backers won't interfere with each other and make sure the pattern looks correct for your style of track. Also make sure that there won't be any interference with the bulkhead and tunnel when you install the studs. It is a good idea to drill the first hole and install one stud, cycling it around the entire track, watching for any close clearance areas between the stud and the snowmobile. Once everything looks alright, go ahead and drill the rest of the holes using the drill tool previously mentioned.
Once the entire track is drilled, go ahead and start putting a small batch of studs through the track. Before cycling the track to add more, tighten these into the track with the backers until the heads have pulled up to the back face of the track which will allow them to travel around the suspension and drive cogs without causing damage or getting stuck. Work on about 4-8 at a time until all of the studs are installed and ready for final tightening. You will want to do the final tightening with a torque wrench. Most 5/16" studs with steel nuts and aluminum backers require 15 ft lbs of torque. Nylon backers may require less, check with the manufacturer of the traction products. Exceeding this torque specification will not bring the stud heads in any tighter, it will only put you at risk for stripped threads or broken studs. Torquing the nut actually stretches the stud just enough to keep it tight, any less, and it could loosen, and more and it could break. You should re-torque the nyloc nuts on your studs after the first ride and periodically afterward. Loose studs cause pull throughs, less studs pulled through is obviously better for your tracks life.
Tunnel protectors are absolutely necessary when using studs. Tunnel protectors (or heat exchanger protectors) stop the outer tips of the rubber lugs on the track from getting so close to the tunnel that the studs would hit and damage another part of the snowmobile, like the tunnel or a heat exchanger. Some snowmobiles come with tunnel protectors built in, others require them to be added if you want to run studs.
Similar threads
- Replies
- 21
- Views
- 5K