Nikolai said:Plaschem gave my dad a bunch of scraps who in turn gave them to me for the hood.swelly said:Only about 75 bucks worth of Davinacil there.
Those guys rock down there.
The new build thread, Hope to see all of you over on the dark side.
Turbo Nytro/IQR tube chassis build
http://www.backcountryrebels.com/showthread.php?t=15484

Turbo Nytro/IQR tube chassis build
http://www.backcountryrebels.com/showthread.php?t=15484
Ruckus
TY 4 Stroke Master
Can you send the link to the Yamaha engineers?
Nikolai
TY 4 Stroke God
99% done now. Pic was taken right after applying the second coat of resin. I added the brown pigment to be able to see any defects but so far so good. Tomorrow I should be able to sand it smooth and pull the mold off. I'm going to make a quick one out of fiberglass to see if it fits a stock sled and if it does, I'll make another stronger one out of carbon that will become the finished female mold. From there I'll vacuum bag the finished products.
My next project will be narrower side panels. I think I can knock 2" off each side. Not only will it help with the fat look, but it should allow the sled to cut steeper sidehills without wanting to wash out as much.
My next project will be narrower side panels. I think I can knock 2" off each side. Not only will it help with the fat look, but it should allow the sled to cut steeper sidehills without wanting to wash out as much.

Nikolai
TY 4 Stroke God
Since I'm fairly new to carbon fiber and I've never used it for chassis parts, I think I'm just going to build a couple tunnels for now. If they hold up then I'll do a complete chassis in 2012. I've been hearing sketchy things about C3's product so I really want to stick with using a foam core. The problem is that side from boats and small aircraft, there's virtually no information on the net that fits my application. Boats and aircraft just don't see the immediate stresses and impacts that sleds do. This means I'll have to do my own destructive testing this summer and throughout next winter.
My current tunnel weighs about 35 lbs including the bumper(but not cooler), so even a heavily reinforced foam core CF tunnel should still drop at least 15 pounds. Other plans will include a chromoly subframe(guessing -8 lbs), and BDX skid arms (-5 lbs). Should put me under 430 lbs dry. Plus the new CF hood and skinny side panels.
Here's a drawing of the tunnel. It's basic but I want to keep a strong, relatively easy to build design. I'll start making the mold from 1/2" plywood this next week.
My current tunnel weighs about 35 lbs including the bumper(but not cooler), so even a heavily reinforced foam core CF tunnel should still drop at least 15 pounds. Other plans will include a chromoly subframe(guessing -8 lbs), and BDX skid arms (-5 lbs). Should put me under 430 lbs dry. Plus the new CF hood and skinny side panels.
Here's a drawing of the tunnel. It's basic but I want to keep a strong, relatively easy to build design. I'll start making the mold from 1/2" plywood this next week.

Off Trail Mike
Gone Riding!
Caleb:
I've built a few CF things in my life, mostly foam cored and sandwiched windsurfers, and there are probably other guys on TY with way better aircraft experience than me, but I would offer a few things to think about.
Stress Points: Generally a foam cored CF tunnel should work really well due to its shape, but because of its configuration, you'll have to pay very close attention to your mounting locations. These are high-stress point loads and include the bulkhead and suspension mounts.
In these locations, you might want to abandon the foam core in favour of solid layups, and add additional layers of CF. Since both locations use fasteners (bolts/rivets) for the connection, you have to protect from fastener ripout which can happen easily especially if the layup isn't thick or strong enough, and from collapsing the foam core as you tighten bolts and rivits. I would say the most difficult area will be the suspension mounts because there are only 4 big bolts and they are going to want to rip thru the CF. You may want to include steel or aluminum in the layup to protect from such an event, or use bushings to increase the hole diameter. Kevlar is also a good ripstop....works for bullets right? If it was me, I'd also figure out a way to include the drop brackets in your tunnel mould, but that's not going to be easy.
To keep strength everywhere, I would radius ALL my tunnel bends as large as pratical. The original Nytro skid with its 40 degree bend 2/3rd's the way up the sides will also stiffen the tunnel alot. It makes the radius job easier, but complicates your mould and might be overkill.
Also at the running board radius, add more layers of fiberglass or carbon fiber to increase strength, or even thicken up the foam core as small changes do make a big difference.
I will be curious to see how the foam works in the tighter bends of the tunnel. My biggest single complaint using foam core was getting it to "stick" in the corners without crinkling or doing somethig to ruin up the layup. Divinycell looks like it works well, so hopefully technology and time have resolved this problem.
Best of luck
I've built a few CF things in my life, mostly foam cored and sandwiched windsurfers, and there are probably other guys on TY with way better aircraft experience than me, but I would offer a few things to think about.
Stress Points: Generally a foam cored CF tunnel should work really well due to its shape, but because of its configuration, you'll have to pay very close attention to your mounting locations. These are high-stress point loads and include the bulkhead and suspension mounts.
In these locations, you might want to abandon the foam core in favour of solid layups, and add additional layers of CF. Since both locations use fasteners (bolts/rivets) for the connection, you have to protect from fastener ripout which can happen easily especially if the layup isn't thick or strong enough, and from collapsing the foam core as you tighten bolts and rivits. I would say the most difficult area will be the suspension mounts because there are only 4 big bolts and they are going to want to rip thru the CF. You may want to include steel or aluminum in the layup to protect from such an event, or use bushings to increase the hole diameter. Kevlar is also a good ripstop....works for bullets right? If it was me, I'd also figure out a way to include the drop brackets in your tunnel mould, but that's not going to be easy.
To keep strength everywhere, I would radius ALL my tunnel bends as large as pratical. The original Nytro skid with its 40 degree bend 2/3rd's the way up the sides will also stiffen the tunnel alot. It makes the radius job easier, but complicates your mould and might be overkill.
Also at the running board radius, add more layers of fiberglass or carbon fiber to increase strength, or even thicken up the foam core as small changes do make a big difference.
I will be curious to see how the foam works in the tighter bends of the tunnel. My biggest single complaint using foam core was getting it to "stick" in the corners without crinkling or doing somethig to ruin up the layup. Divinycell looks like it works well, so hopefully technology and time have resolved this problem.
Best of luck
I am still trying to figure out when Caleb sleeps.
Nikolai
TY 4 Stroke God
All excellent points Off Trail Mike.
Where the tunnel fastens to the bulkhead there were two options I was thinking of using. One was boring out larger holes(once the tunnel was done), filling them with epoxy and setting sleeves in, just like they do for boats. The other option was using balsa wood for the bulkhead mount, and front and rear skid mounts. Balsa has an incredibly high shear strength and obviously much higher compression than foam. I was planning on 45ing the top inch of the tunnel and the running boards, I'm very aware that cloth doesn't like sharp corners. Hence why my hood is as smooth as possible, lol.
I'm still researching materials and have posted a similar thread on a composites website. My main focus for now is just going the wooden frame done. At that point I'll probably make a few 12" wide sections of tunnel with various layers of cloth to see what I think is needed.
Where the tunnel fastens to the bulkhead there were two options I was thinking of using. One was boring out larger holes(once the tunnel was done), filling them with epoxy and setting sleeves in, just like they do for boats. The other option was using balsa wood for the bulkhead mount, and front and rear skid mounts. Balsa has an incredibly high shear strength and obviously much higher compression than foam. I was planning on 45ing the top inch of the tunnel and the running boards, I'm very aware that cloth doesn't like sharp corners. Hence why my hood is as smooth as possible, lol.
I'm still researching materials and have posted a similar thread on a composites website. My main focus for now is just going the wooden frame done. At that point I'll probably make a few 12" wide sections of tunnel with various layers of cloth to see what I think is needed.
Off Trail Mike
Gone Riding!
Yeah, the 12 inch sections are the way to go, and it will be cool to do some distruction testing!
I was thinking balsa too, but its the whole water/rot issue. Pretty nasty environment under your tunnel, but if you can keep everything incased in epoxy, then it should work just fine.
If you bore out the foam around your mounts, what are you thinking for inserts? Sandwiched washers of CF and glass or something else? Just curious.
One other thing I forgot in the last post was vacuum bagging. Its is pretty easy to set up, but getting the excess resin out of your layup is sometimes a pain in the butt, as you need to absorb it into something.
Aircraft Spruce has all sorts of Release Ply and Bleeder plys, but if you have time, don't be afraid to try some of your own stuff.
I did mine on the cheap and ended up using a thin (but strong) shiny nylon drapery fabric I found at Walmart and sprayed with release agent. On top of that I had a loose woven carpet backing that was maybe 3/16" thick. It vacuumed great, but rather than let the epoxy dry to 100%, I started pulling off the release ply at maybe 80-90% cure, which was way easier to pull off.
It worked pretty well. I go a relatively smooth finish and didn't get any delaminations. Maybe it caused damage inside the laminate, but after using it for years, I doubt it......
Hope this helps.
OTM
I was thinking balsa too, but its the whole water/rot issue. Pretty nasty environment under your tunnel, but if you can keep everything incased in epoxy, then it should work just fine.
If you bore out the foam around your mounts, what are you thinking for inserts? Sandwiched washers of CF and glass or something else? Just curious.
One other thing I forgot in the last post was vacuum bagging. Its is pretty easy to set up, but getting the excess resin out of your layup is sometimes a pain in the butt, as you need to absorb it into something.
Aircraft Spruce has all sorts of Release Ply and Bleeder plys, but if you have time, don't be afraid to try some of your own stuff.
I did mine on the cheap and ended up using a thin (but strong) shiny nylon drapery fabric I found at Walmart and sprayed with release agent. On top of that I had a loose woven carpet backing that was maybe 3/16" thick. It vacuumed great, but rather than let the epoxy dry to 100%, I started pulling off the release ply at maybe 80-90% cure, which was way easier to pull off.
It worked pretty well. I go a relatively smooth finish and didn't get any delaminations. Maybe it caused damage inside the laminate, but after using it for years, I doubt it......
Hope this helps.
OTM
akvector
TY 4 Stroke Junkie
I envy the abilities some of you have and Nikolai for taking on such a project. I believe you should sell that tunnel when dialed in but of course I can not imagine it is very time friendly!!!
For those of you that have not made it over to check out the build thread. The tubie is starting to take shape.



This is going to be a stellar project! 

rlcofmn said:For those of you that have not made it over to check out the build thread. The tubie is starting to take shape.![]()
Having met you and seeing your passion about Yamaha sleds, I think that you should start your own thread about this build.
On TY

Not BCR

Just sayin'
Scott
Always a pleasure talkin to you Scott, I'll work on getting a thread going. It will take some time since I have so many pictures.
A lot of great guy's here!
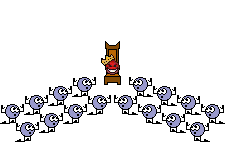
scmurs said:rlcofmn said:For those of you that have not made it over to check out the build thread. The tubie is starting to take shape.![]()
Having met you and seeing your passion about Yamaha sleds, I think that you should start your own thread about this build.
On TY![]()
Not BCR![]()
Just sayin'
Scott
Nikolai, So what ever happened with the build? Love to see a update.
Similar threads
- Replies
- 4
- Views
- 883
- Replies
- 91
- Views
- 42K
-
This site uses cookies to help personalise content, tailor your experience and to keep you logged in if you register.
By continuing to use this site, you are consenting to our use of cookies.