scooterwj
Pro
OK even more questions. So I have a belt deflection adjuster from BOP. That isnt the issue. I am noticing that my secondary when I let off the throttle does not return to completely open. The belt stays down about 2mm or so and if you just bump the throttle it then opens up completely and allows the belt to sit just a hair over level. Shouldnt the secondary open completely when you decelerate?
I'm curious about this as well....

KnappAttack
24X ISR World Drag Racing Champion
- Joined
- Feb 19, 2004
- Messages
- 4,674
- Location
- Welch MN
- Country
- USA
- Snowmobile
- 2023 Sidewinder LTX-LE
2017 Sidewinder LTX-LE
OK even more questions. So I have a belt deflection adjuster from BOP. That isnt the issue. I am noticing that my secondary when I let off the throttle does not return to completely open. The belt stays down about 2mm or so and if you just bump the throttle it then opens up completely and allows the belt to sit just a hair over level. Shouldnt the secondary open completely when you decelerate?
Sorry for all of the questions, I am just trying to make this perfect this year so I dont have belt issues. I bought the Hurricane alignment tool a clutch kit with new Primary and Secondary springs the belt deflection tool checked my rollers in the secondary, everything in the primary looks good. I ended up taking all of my washers out as I believe from what I can tell from measuring with a straight edge I am about 59mm right now. That is as close as I can get without machining some off the stub shaft.
59mm is not near low enough to get into alignment using the bar. I took off the circlip from the bearing on the shaft and bolted the driven down solid to pick up another 1.5mm without machining. This will hold the bearing where it belongs without the circlip. I then used 1.5" ID shims inside the driven halves to set the belt deflection, Cat used them back in all the reverse cam secondary clutches and it works great, but you need to take the secondary apart to set deflection, which is not a big deal to me. Bolt the driven solid using washers and shims over the alum spacer and a washer only big enough to hold the secondary on the shaft itself, not the helix. More like an old Apex. In fact I used shims from the Apex to set this up, the bolt just tightens down on the secondary shaft perfectly holding it to the bearing for NO FLOAT at all.
The stock secondary spring is not stout enough to get the belt back up in the secondary IMO for actual trail usage in snow. Might be fine for ice or hardpack conditions but doesn't work for gripping the belt when hooking and spinning in snow or trail use. It is too weak when the belt is trying to get back into low gear.
I'm going to start the season testing with 41-37 and purple EPI Cat secondary spring I got from Hurricane, set at 1-0 using the 8DN belt. This spring takes all the whip and ballooning out of the belt and was used in most all the high HP boosted Apexs, Nytros and machines with big HP. It has quite a bit more side pressure than any of the Yamaha springs. I'm also going to be trying a Dalton Black/Lime Cat spring, which has even more side pressure. With the EPI purple and the 8DN, the belt comes right back to the top of the driven like it should. It should backshift much better and keep ahold of the belt in actual trail conditions or conditions where we're running in snow.
I will let people know how it works once I get some snow to test, but I have expectations that the belt will last and work like it should and am hoping for.

ROCKERDAN
OCD Sledhead
- Joined
- Oct 8, 2005
- Messages
- 7,503
- Location
- Huntsville Ontario & Niagara NY
- Country
- Other
- Snowmobile
- '18 RTX 50th "Winder"
If your sled is like 95% of them, you will need HUB machined and that is why you have the play. But get the bar straight first and check again....I haven't machined any off yet. I wanted to see how much I was going to need with no washers first
Dan

ROCKERDAN
OCD Sledhead
- Joined
- Oct 8, 2005
- Messages
- 7,503
- Location
- Huntsville Ontario & Niagara NY
- Country
- Other
- Snowmobile
- '18 RTX 50th "Winder"
I use these often for work, and always clean up clutches with these then acetone them down(or brake clean)I will get a new scrubby pad. I used to use the ones you use to scruff up a car for paint. Is the green one more fine or more coarse? I wont leave the belt on again in the summer. I didnt even think of that.I replace it with new at the start of every year, but leaving it on there can cause that? I have never hauled it on an open trailer.
These are not a sponge for kitchen sink, find them near sandpaper at depot(Paint section) typically.
We used to used steel wool in old days, but real steel wool falls apart and leaves tiny pieces all over, this is basically synthetic steel wool, I just call em green pads.
Dan

ROCKERDAN
OCD Sledhead
- Joined
- Oct 8, 2005
- Messages
- 7,503
- Location
- Huntsville Ontario & Niagara NY
- Country
- Other
- Snowmobile
- '18 RTX 50th "Winder"
Sledroll
TY 4 Stroke Master
- Joined
- Dec 19, 2005
- Messages
- 1,226
- Location
- Muskoka , Ontario
- Country
- Canada
- Snowmobile
- 2022 SRX LE
2017 SW LTX LE
OMG !!!!!!@race24x....
If you want, I can give you a call if you need anything. So much easier to talk over all this then type sometimes.
Dan
I have been reading all the SW posts , and just remembered that I have a SW sitting in my trailer that has not been serviced from last use in April 2018 !!!
So , I kept saying , I have 4 months before I need it , and 3months, and so on , and now Dan is back in Muskoka , and ready to ride with almost anyone and anywhere , and I am taking my sled to the dealer for servicing TODAY !
Now I realized why I kept my Apex !
As it has been waiting since late 2016 to win my heart back.
I really didn't rush to get it serviced , as there was nothing apparently broken .
From what I recall , I put on 4,000 +/- klms last year on a used original belt with no issues .
Oh ya , I forgot , a hose and elbow came apart at 100 miles an hour.
Gives new meaning to a Golden shower ! ( can I say that on here ?)
Capable riding partners had it put back together , topped up ,and on our way in 15 mins +/-.
Based on losing most our snow , yesterday, I am sure I won't miss any riding time anytime soon .
Lake is frozen back up today , SO, let it snow , let it snow , let it snow !
Last edited:
race24x
TY 4 Stroke Master
Thanks Dan and everyone.
I have a snowmobile lift and the sled was up in the air. I put the secondary with the tool on and turn the track to get it on the primary. I can try it the other way with the go no go gauge, but I was trying to copy Daves video. What I was trying to show was that even flat on the primary with one side of the large piece of tool it was close, but with the other side out I had about 1/4 in. One I straighten the tool I will try again. I think like Dan said I will have to machine off 2mm. How are you guys doing this? I have a friend that works at a machine shop.
I have a snowmobile lift and the sled was up in the air. I put the secondary with the tool on and turn the track to get it on the primary. I can try it the other way with the go no go gauge, but I was trying to copy Daves video. What I was trying to show was that even flat on the primary with one side of the large piece of tool it was close, but with the other side out I had about 1/4 in. One I straighten the tool I will try again. I think like Dan said I will have to machine off 2mm. How are you guys doing this? I have a friend that works at a machine shop.
Put it in a lathe and have him remove how much you want. I took .120 off mine
jeffgilbert
Expert
- Joined
- Dec 17, 2007
- Messages
- 216
- Location
- Newfoundland
- Country
- Canada
- Snowmobile
- 2019 Sidewinder BTX LE
59mm is not near low enough to get into alignment using the bar. I took off the circlip from the bearing on the shaft and bolted the driven down solid to pick up another 1.5mm without machining. This will hold the bearing where it belongs without the circlip. I then used 1.5" ID shims inside the driven halves to set the belt deflection, Cat used them back in all the reverse cam secondary clutches and it works great, but you need to take the secondary apart to set deflection, which is not a big deal to me. Bolt the driven solid using washers and shims over the alum spacer and a washer only big enough to hold the secondary on the shaft itself, not the helix. More like an old Apex. In fact I used shims from the Apex to set this up, the bolt just tightens down on the secondary shaft perfectly holding it to the bearing for NO FLOAT at all.
The stock secondary spring is not stout enough to get the belt back up in the secondary IMO for actual trail usage in snow. Might be fine for ice or hardpack conditions but doesn't work for gripping the belt when hooking and spinning in snow or trail use. It is too weak when the belt is trying to get back into low gear.
I'm going to start the season testing with 41-37 and purple EPI Cat secondary spring I got from Hurricane, set at 1-0 using the 8DN belt. This spring takes all the whip and ballooning out of the belt and was used in most all the high HP boosted Apexs, Nytros and machines with big HP. It has quite a bit more side pressure than any of the Yamaha springs. I'm also going to be trying a Dalton Black/Lime Cat spring, which has even more side pressure. With the EPI purple and the 8DN, the belt comes right back to the top of the driven like it should. It should backshift much better and keep ahold of the belt in actual trail conditions or conditions where we're running in snow.
I will let people know how it works once I get some snow to test, but I have expectations that the belt will last and work like it should and am hoping for.
i was aligning mine with the bar and when i removed the circlip and bolted it down i was bang on. I figured the secondary bolted down against the bearing would be fine but i was advised from a few including hurricane not to do that but to go get the shaft machined as well as the aluminum plug. Whats your thoughts?

KnappAttack
24X ISR World Drag Racing Champion
- Joined
- Feb 19, 2004
- Messages
- 4,674
- Location
- Welch MN
- Country
- USA
- Snowmobile
- 2023 Sidewinder LTX-LE
2017 Sidewinder LTX-LE
i was aligning mine with the bar and when i removed the circlip and bolted it down i was bang on. I figured the secondary bolted down against the bearing would be fine but i was advised from a few including hurricane not to do that but to go get the shaft machined as well as the aluminum plug. Whats your thoughts?
Well as long as you have the driven bolted solid to the bearing I don't see an issue. Here is the problem. Many are going to think that using the stock washer or the adjustment plug they have it bolted down solid just because it doesn't move.
Some people are not smart when it come to this stuff and they will have issues, because the driven can still float if not done properly. They can't figure it out that bolted solid means machining the alum plug or spacing it solid means the bolt has to hold only on the driven shaft and not the helix like it does from the factory. You can show them and they still don't understand how this works. So many, I'd even say the majority that need pictures and instructions still won't get it done properly. So not done properly and there will be many issues.
There is a shoulder behind the bearing, if the driven is indeed bolted down solid to it, it remains the same as the circlip holding the bearing on, but you must be certain to use a washer the size of the shaft of the driven outside and not the size of the helix, also the proper shimming for the outside of this assembly so it "DOES NOT FLOAT" OR "APPLY TOO MUCH PRESSURE TO THE JACKSHAFT" pushing against the bearing or trying to bend the washer. It takes so time and the proper shims to get this part spot on. If you make the effort to get this done properly it will be fine. It will also require shimming for deflection inside the driven sheave halves which most will not understand as well. If you have the know how to do it, great, but for most they will need pictures and need to explaining than people have time for.
If one does not understand the principle, or you feel the need to ask questions, they probably should not be doing it, even though its quite simple.
Washer size needs to be as below with proper Apex style shim washer below it, and belt deflection needs to be set inside the Driven like the old Cat reverse cam drivens. Or, you need to shim tight against the driven shaft and use your outside adjuster accordingly. Its simple if you understand the reasoning behind all of it. Machining the driven becomes easier for those that don't understand at that point.
jeffgilbert
Expert
- Joined
- Dec 17, 2007
- Messages
- 216
- Location
- Newfoundland
- Country
- Canada
- Snowmobile
- 2019 Sidewinder BTX LE
I get what you are saying i remember setting deflection on older cats with washers on the inside of the sheaves. I seen the float that was there when fooling with the aligment bar. Is it beneficial to have a few mm of float or to have it solid?

ROCKERDAN
OCD Sledhead
- Joined
- Oct 8, 2005
- Messages
- 7,503
- Location
- Huntsville Ontario & Niagara NY
- Country
- Other
- Snowmobile
- '18 RTX 50th "Winder"
Well as long as you have the driven bolted solid to the bearing I don't see an issue. Here is the problem. Many are going to think that using the stock washer or the adjustment plug they have it bolted down solid just because it doesn't move.
Some people are not smart when it come to this stuff and they will have issues, because the driven can still float if not done properly. They can't figure it out that bolted solid means machining the alum plug or spacing it solid means the bolt has to hold only on the driven shaft and not the helix like it does from the factory. You can show them and they still don't understand how this works. So many, I'd even say the majority that need pictures and instructions still won't get it done properly. So not done properly and there will be many issues.
There is a shoulder behind the bearing, if the driven is indeed bolted down solid to it, it remains the same as the circlip holding the bearing on, but you must be certain to use a washer the size of the shaft of the driven outside and not the size of the helix, also the proper shimming for the outside of this assembly so it "DOES NOT FLOAT" OR "APPLY TOO MUCH PRESSURE TO THE JACKSHAFT" pushing against the bearing or trying to bend the washer. It takes so time and the proper shims to get this part spot on. If you make the effort to get this done properly it will be fine. It will also require shimming for deflection inside the driven sheave halves which most will not understand as well. If you have the know how to do it, great, but for most they will need pictures and need to explaining than people have time for.
If one does not understand the principle, or you feel the need to ask questions, they probably should not be doing it, even though its quite simple.
Washer size needs to be as below with proper Apex style shim washer below it, and belt deflection needs to be set inside the Driven like the old Cat reverse cam drivens. Or, you need to shim tight against the driven shaft and use your outside adjuster accordingly. Its simple if you understand the reasoning behind all of it. Machining the driven becomes easier for those that don't understand at that point.
Yeah Mike its hard for alot guys to grasp it. I know Dave runs into this stuff alot, so he tries to keep it simple when explaining...lol
Got mine setup nicely without float awhile back, and bang on with Daves bar. Alot of you out there can grab some old apex shims, which fit overtop of the stock alum float plug. To dial down your float. Makes things simpler when trimming back float plug.
Wont be long now til some riding/testing....sure hoping for good things from these changes.
Dan

KnappAttack
24X ISR World Drag Racing Champion
- Joined
- Feb 19, 2004
- Messages
- 4,674
- Location
- Welch MN
- Country
- USA
- Snowmobile
- 2023 Sidewinder LTX-LE
2017 Sidewinder LTX-LE
I get what you are saying i remember setting deflection on older cats with washers on the inside of the sheaves. I seen the float that was there when fooling with the aligment bar. Is it beneficial to have a few mm of float or to have it solid?
IMO solid is the only way to go. Float could allow for driven to "stick" outward and not line up.
Plus, you can not remove the circlip and allow any float or jackshaft outboard bearing will NOT be held in place.
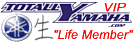

1nc 2000
Lifetime Member Tim
- Joined
- Feb 26, 2010
- Messages
- 3,048
- Location
- Marquette, MI
- Country
- USA
- Snowmobile
- Yamaha FX Nytro RTX SE
I got some trail time in yesterday with my secondary locked down solid. Running EPI purple spring and 41-37 helix. Pulls super hard and clutches were not super hot. Could put my hand on clutch sheaves anywhere. Both clutches felt the same. Wish I had a temp gun. Did not get any top end runs over 110 mph due to no room for long pulls. Time to start playing with the amount of wrap on secondary spring to see what I like the best for the trails I ride.
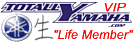

- Joined
- Nov 29, 2009
- Messages
- 1,230
- Age
- 49
- Location
- sabattus, maine
- Country
- USA
- Snowmobile
- 76 exciter, 87 phazer, 89 bravo, 00 srx x3, 01 srx, 02/04 viper, 06 ape
What are you running in the primary?I got some trail time in yesterday with my secondary locked down solid. Running EPI purple spring and 41-37 helix. Pulls super hard and clutches were not super hot. Could put my hand on clutch sheaves anywhere. Both clutches felt the same. Wish I had a temp gun. Did not get any top end runs over 110 mph due to no room for long pulls. Time to start playing with the amount of wrap on secondary spring to see what I like the best for the trails I ride.
Similar threads
- Replies
- 0
- Views
- 2K
- Replies
- 1
- Views
- 243
- Replies
- 21
- Views
- 2K
-
This site uses cookies to help personalise content, tailor your experience and to keep you logged in if you register.
By continuing to use this site, you are consenting to our use of cookies.