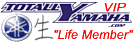

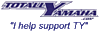
earthling
Lifetime Member
- Joined
- Dec 1, 2017
- Messages
- 2,044
- Reaction score
- 2,003
- Points
- 1,183
- Location
- Ontario
- Country
- Canada
- Snowmobile
- 2021 SRX
2006 ATTAK
IQS is just a replacement for the 3 way switch found on normal (non-iqs) shocks. The switch is replaced by the IQS servo motor and some electronics to make sure that everything is working. The IQS system can be adapted to other shocks but you are just moving the real problem to a different shock. The real problem is the valving is wrong for the spring rates required.
@2004yamahaviper
The firmness of setting 3, front and rear is known but all of that is in the valving of the shock, not the IQS itself. IQS just selects between 1,2,3 and its the valving that controls the damping internally. You can have your shocks revalved to act however you would like. Since you are in Ottawa, either Dean at Peakvelocity (claremont, on) or John at accelerated (buckhorn, on) can make those changes for you. I am not sure if there is someone closer to you but I have spoken to folks out your way who use Dean for shock rebuilds. IMO, unless you want a super high performance shock package the shocks you have can be easily adjusted to fit how you ride and for far cheaper than buying other shocks. (corrected by @cannondale27)
@2004yamahaviper
Last edited:
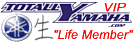

No. The IQS imitates the QS3 Mechanical valve which 2 is 20% stiffer than 1 and 3 is 50% stiffer than 1. So changing the valving of shock still leaves the 20 and 50% difference between 1,2 and 3. IQS could be modified with programming to change that ratio to whatever you want. QS3 valve itself can be modified to change the ratio along with valving of shocks. IQS no matter what valving is done unless someone hacks the program like has been done on DOO the ratio will always be the same no matter what valving is done to shock internally. So valve softer to use 3 more and 1 becomes useless because its too soft. Valve stiffer and 3 becomes useless because its stiff already.IQS is just a replacement for the 3 way switch found on normal (non-iqs) shocks. The switch is replaced by the IQS servo motor and some electronics to make sure that everything is working. The IQS system can be adapted to other shocks but you are just moving the real problem to a different shock. The real problem is the valving is wrong for the spring rates required.
@2004yamahaviper
The firmness of setting 3, front and rear is known but all of that is in the valving of the shock, not the IQS itself. IQS just selects between 1,2,3 and its the valving that controls the damping internally. You can have your shocks revalved to act however you would like. Since you are in Ottawa, either Dean at Peakvelocity (claremont, on) or John at accelerated (buckhorn, on) can make those changes for you. I am not sure if there is someone closer to you but I have spoken to folks out your way who use Dean for shock rebuilds. IMO, unless you want a super high performance shock package the shocks you have can be easily adjusted to fit how you ride and for far cheaper than buying other shocks.
To defeat the code thrown on IQS which had the valve replace with a Hi/Lo I just plugged the old stepper in and it was hidden in the sled. So sled thinks it was still adjusting the rear shock which is the one I put HiLo in. If all 3 were done you might be able to eliminate whole system.
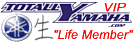

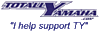
earthling
Lifetime Member
- Joined
- Dec 1, 2017
- Messages
- 2,044
- Reaction score
- 2,003
- Points
- 1,183
- Location
- Ontario
- Country
- Canada
- Snowmobile
- 2021 SRX
2006 ATTAK
No. The IQS imitates the QS3 Mechanical valve which 2 is 20% stiffer than 1 and 3 is 50% stiffer than 1. So changing the valving of shock still leaves the 20 and 50% difference between 1,2 and 3. IQS could be modified with programming to change that ratio to whatever you want. QS3 valve itself can be modified to change the ratio along with valving of shocks. IQS no matter what valving is done unless someone hacks the program like has been done on DOO the ratio will always be the same no matter what valving is done to shock internally. So valve softer to use 3 more and 1 becomes useless because its too soft. Valve stiffer and 3 becomes useless because its stiff already.
To defeat the code thrown on IQS which had the valve replace with a Hi/Lo I just plugged the old stepper in and it was hidden in the sled. So sled thinks it was still adjusting the rear shock which is the one I put HiLo in. If all 3 were done you might be able to eliminate whole system.
Interesting. In an earlier statement in this thread you stated you could re-valve for 3 without affecting 2. here My comment was based partially on that statement but also on comments from Fox themselves that IQS simply emulated the action of the mechanical clicker. The design of the QS3 shock has the adjuster sitting between the reservoir and the shock body, does this not mean that the control is simply choosing an orifice between the two, controlling flow somehow? Based on what we see from the EPS add on, it could be that there isn't any Gauge programming involved, it may be that simply unplugging the entire system will stop the IQS ECU from spitting codes out.

RobX-1
VIP Member
- Joined
- Apr 13, 2003
- Messages
- 2,303
- Reaction score
- 1,488
- Points
- 1,583
- Location
- Coldwater, OH
- Country
- USA
- Snowmobile
- 18 50th Apex XT-X, 08 40th Apex LTX GT, 08 40th Nytro RTX, & 03 RX-1
Umm, here's his actual comment:
I can change Position 3 on Qs3 and Qs3r to be close to 2 and not effect 2 and 2 but not on IQS since it’s a Servo with infinite adjustability controlled by an Ecu that Cat/Yamaha haven’t taken advantage of. It’s a shame.
Simplespeed
TY 4 Stroke Junkie
- Joined
- Jan 8, 2022
- Messages
- 644
- Reaction score
- 445
- Points
- 368
- Location
- 1191 Sauk Lane , Saginaw, Mi. 48638
- Country
- USA
- Snowmobile
- 2006 Apex , 2017 Sidewinder LTX -LE
Hate any suspension that uses a wire to control any shock .. Love having adjustment on the fly but just wish they could do it with bluetooth…
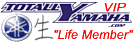

That’s not revalving that is by modifying the adjuster.Interesting. In an earlier statement in this thread you stated you could re-valve for 3 without affecting 2. here My comment was based partially on that statement but also on comments from Fox themselves that IQS simply emulated the action of the mechanical clicker. The design of the QS3 shock has the adjuster sitting between the reservoir and the shock body, does this not mean that the control is simply choosing an orifice between the two, controlling flow somehow? Based on what we see from the EPS add on, it could be that there isn't any Gauge programming involved, it may be that simply unplugging the entire system will stop the IQS ECU from spitting codes out.
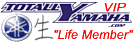

There is no way possible to effect the ratio of 1-2-3 except to modify the valve itself and that’s only possible on Qs3 and Qs3r. Iqs is a stepper motor CanBus controlled. Nobody is modifying them yet. With 3 steps any shock Valving on either will make either position 1 or 3 unusable without modifying the valve itself. This is only being done to position 3 by me because I will not use epoxy to fill the other two orfices like I have seen others do. Too risky in my opinion.
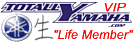

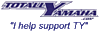
earthling
Lifetime Member
- Joined
- Dec 1, 2017
- Messages
- 2,044
- Reaction score
- 2,003
- Points
- 1,183
- Location
- Ontario
- Country
- Canada
- Snowmobile
- 2021 SRX
2006 ATTAK
.
Ahh, that makes sense, I thought your reference to 2/3 was at the valve stack, not at the adjuster.
That’s not revalving that is by modifying the adjuster.
Ahh, that makes sense, I thought your reference to 2/3 was at the valve stack, not at the adjuster.
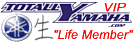

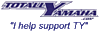
earthling
Lifetime Member
- Joined
- Dec 1, 2017
- Messages
- 2,044
- Reaction score
- 2,003
- Points
- 1,183
- Location
- Ontario
- Country
- Canada
- Snowmobile
- 2021 SRX
2006 ATTAK
There is no way possible to effect the ratio of 1-2-3 except to modify the valve itself and that’s only possible on Qs3 and Qs3r. Iqs is a stepper motor CanBus controlled. Nobody is modifying them yet. With 3 steps any shock Valving on either will make either position 1 or 3 unusable without modifying the valve itself. This is only being done to position 3 by me because I will not use epoxy to fill the other two orfices like I have seen others do. Too risky in my opinion.
That makes sense to me now, thank you.
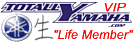

Yeah like you said on Qs3 and Qs3r the valve is just a rotating cylinder with a big hole for 1 a smaller hole for 2 and no hole for 3. On IQs it’s a needle valve with infinite range but limited by the system. I could possibly modify the valve itself by changing needle depth like a carb or hole size like jet in carb but I am betting the system bottoms the needle to find home so height change would be useless. Jet size would change all settings equally once again making either 1 or 3 useless no matter. The shock Valving. Need to hack the ecu. Applying 12 v does give one movement then nothing. I really have not researched how CanBus system works but I thought it would be like electric emergency brakes on car but it’s not that simple to defeat. Must be something in the valve motor that prevents full movement with just 12 v applied. I know some shock builders have scavenged whole system from wrecked sled to accomplish adjustments on bench for service and testing. I still defeat it by opening port and vacuum bleeding. It’s impossible to bleed shock by stroking it if inadvertently set on 3 before removal from sled. And stroking is absolutely needed even with vacuum bleed system to get air out during service. I will get a whole system from sled also someday if demand increases.That makes sense to me now, thank you.
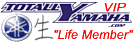

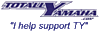
earthling
Lifetime Member
- Joined
- Dec 1, 2017
- Messages
- 2,044
- Reaction score
- 2,003
- Points
- 1,183
- Location
- Ontario
- Country
- Canada
- Snowmobile
- 2021 SRX
2006 ATTAK
Yeah like you said on Qs3 and Qs3r the valve is just a rotating cylinder with a big hole for 1 a smaller hole for 2 and no hole for 3. On IQs it’s a needle valve with infinite range but limited by the system. I could possibly modify the valve itself by changing needle depth like a carb or hole size like jet in carb but I am betting the system bottoms the needle to find home so height change would be useless. Jet size would change all settings equally once again making either 1 or 3 useless no matter. The shock Valving. Need to hack the ecu. Applying 12 v does give one movement then nothing. I really have not researched how CanBus system works but I thought it would be like electric emergency brakes on car but it’s not that simple to defeat. Must be something in the valve motor that prevents full movement with just 12 v applied. I know some shock builders have scavenged whole system from wrecked sled to accomplish adjustments on bench for service and testing. I still defeat it by opening port and vacuum bleeding. It’s impossible to bleed shock by stroking it if inadvertently set on 3 before removal from sled. And stroking is absolutely needed even with vacuum bleed system to get air out during service. I will get a whole system from sled also someday if demand increases.
If it is a servo, it likely doesn't bottom out but rather seeks 'home' which is its neutral position, which could be any of the available positions. For instance 2 could be neutral with 1 being a negative move and 3 being a positive move (neg and pos are directions away from neutral). Home could be 1 and 2 and 3 could be positive increasing offsets from 1. That is if it is a servo. It is likely a servo because fox would want the system to self manage its position, meaning it would not want the needle to move because of hydraulic pressure pushing against the needle but they could also use a worm gear and get the same mechanical outcome. A servo mechanism would be the simple way to do it.
To get the servo to move you send a PWM style of signal, a simple voltage won't work except to probably bump it in one direction. I asked one of the local guys that buys sleds from insurance companies if he had one I could play with and no dice. If it is a PWM signal, then intercepting it and re-writing it would be the simple 'hack' although it requires a lot of physical intervention, at minimum you have to replace the output harness of the shock ECU with one in the middle that piggybacks the first one. Hacking the ECU itself would be the far more elegant way to manage it but longer to accomplish as you would have to figure out their control scheme. First step however would be to put an oscilloscope on the control wires for one servo and look at the control signals.
As you say, you could also modify the needle/seat and I think it would be safe to do that. If it is looking for some home position based on the needle bottoming out that can only happen in position three (fully closed). The other positions would be offsets. I think however that it is likely that it is calibrated such that position 3 (closed) is just a logical position. Even if position 3 was a physical home sensed by bottoming out the needle you could modify the home position with a small bypass giving you some control over position 3. I can probably look at the control scheme and might this weekend if I get my other two projects done but would not go so far as to take my shock apart to see how it physically works.
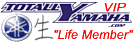

You sound way more qualified to figure this out electronically than me. I will give you all the assistance I can. We need to talk perhaps with my parts and your knowledge of electronics we can beat this system! Thank you!If it is a servo, it likely doesn't bottom out but rather seeks 'home' which is its neutral position, which could be any of the available positions. For instance 2 could be neutral with 1 being a negative move and 3 being a positive move (neg and pos are directions away from neutral). Home could be 1 and 2 and 3 could be positive increasing offsets from 1. That is if it is a servo. It is likely a servo because fox would want the system to self manage its position, meaning it would not want the needle to move because of hydraulic pressure pushing against the needle but they could also use a worm gear and get the same mechanical outcome. A servo mechanism would be the simple way to do it.
To get the servo to move you send a PWM style of signal, a simple voltage won't work except to probably bump it in one direction. I asked one of the local guys that buys sleds from insurance companies if he had one I could play with and no dice. If it is a PWM signal, then intercepting it and re-writing it would be the simple 'hack' although it requires a lot of physical intervention, at minimum you have to replace the output harness of the shock ECU with one in the middle that piggybacks the first one. Hacking the ECU itself would be the far more elegant way to manage it but longer to accomplish as you would have to figure out their control scheme. First step however would be to put an oscilloscope on the control wires for one servo and look at the control signals.
As you say, you could also modify the needle/seat and I think it would be safe to do that. If it is looking for some home position based on the needle bottoming out that can only happen in position three (fully closed). The other positions would be offsets. I think however that it is likely that it is calibrated such that position 3 (closed) is just a logical position. Even if position 3 was a physical home sensed by bottoming out the needle you could modify the home position with a small bypass giving you some control over position 3. I can probably look at the control scheme and might this weekend if I get my other two projects done but would not go so far as to take my shock apart to see how it physically works.
Pm me your address I will send a known working Servo.

ManhattanMike
VIP Member
- Joined
- Jan 29, 2008
- Messages
- 148
- Reaction score
- 86
- Points
- 1,003
- Location
- Mokena, IL
- Country
- USA
- Snowmobile
- 2020 Sidewinder SRX LE, 2018 Snoscoot
I’m following this thread for sure. Would love to get something better out of my IQS.
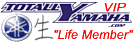

BADSLED
Lifetime Member
- Joined
- May 13, 2004
- Messages
- 1,362
- Reaction score
- 19
- Points
- 1,073
- Location
- Syracuse, NY
- Country
- USA
- Snowmobile
- 2025 Sidewinder XTX LE EPS
2012 Nytro MC Xpress 270
Has anyone been able to successfully hack the IQS canbus controller to modify adjustability of the shocks? I am leaning towards ditching IQS and going with Custom Axis.
Last edited:
Similar threads
- Replies
- 39
- Views
- 5K
-
This site uses cookies to help personalise content, tailor your experience and to keep you logged in if you register.
By continuing to use this site, you are consenting to our use of cookies.