
kinger
VIP Member
- Joined
- Jan 17, 2005
- Messages
- 7,403
- Reaction score
- 1,539
- Points
- 1,963
- Location
- Clear Lake, IA
- Website
- www.piergenius.com
So to summarize, I’ve added a second Tial 44 mm wastegate, I purchased the 1.06 ratio turbine housing that will help exhaust flow and slow the response of the turbo. I’m excited to try this out.

kinger
VIP Member
- Joined
- Jan 17, 2005
- Messages
- 7,403
- Reaction score
- 1,539
- Points
- 1,963
- Location
- Clear Lake, IA
- Website
- www.piergenius.com
I am also on the hunt for a 2nd BOV that will go between the turbo and SC. I don't have a problem as of yet but I think with the way I chop the throttle in tight trails the way I like to, it would be good to alleviate the pressure from both blowers instead of just up post IC. Also noticed when I let off even at low boost (17psi) it really spiked the MAP so with plans of being near 28 psi on meth I figure this is a smart move to help keep boots and stuff from blowing off. I am worried about the head intake boots blowing off, I did use yamabond on them when I put the new motor in and that trick does work. The rest will have quality clamps on it and should hold up fine.
Leaning towards this one:
www.turbosmart.com
Curious on the vacuum to pop it off, looking at the data logs from my sled and I only register about 20 inHG and this looks like it needs more vacuum at 18 inHG and that is the most sensitive spring you can get.
But then I look at my current BOV:
vortechsuperchargers.com
And its saying it opens at 10-11 inHG which I am not even close to (according to the data logs but maybe I am not sampling my MAP sensor fast enough to see the low numbers) and it opens just fine.
Any thoughts?
Leaning towards this one:

GenV RacePort BOV - (Black)
The Turbosmart RacePort is famous for being an amazingly small and light BOV for turbocharged competition level engines. Featuring our unique collar design and internal flow structures, it is 50% lighter and 25% smaller than the competition while flowing 330 CFM – making it the highest flowing...
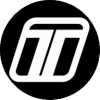
Curious on the vacuum to pop it off, looking at the data logs from my sled and I only register about 20 inHG and this looks like it needs more vacuum at 18 inHG and that is the most sensitive spring you can get.
But then I look at my current BOV:
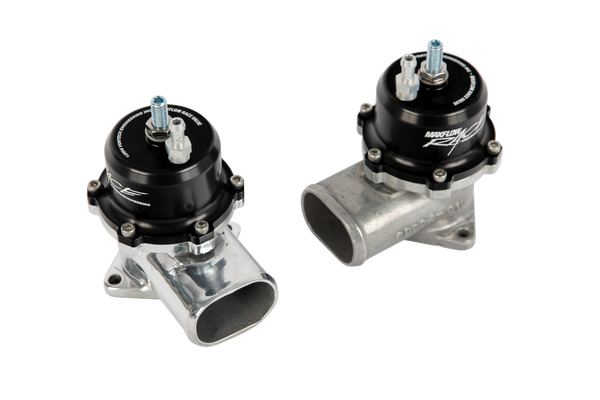
Maxflow Race Bypass Valve
Our Maxflow® Race Bypass Valves flow 320 CFM @ 8 PSIG and feature a compact design that is ideal for sport compacts and other applications with tight engine compartments

And its saying it opens at 10-11 inHG which I am not even close to (according to the data logs but maybe I am not sampling my MAP sensor fast enough to see the low numbers) and it opens just fine.
Any thoughts?

kinger
VIP Member
- Joined
- Jan 17, 2005
- Messages
- 7,403
- Reaction score
- 1,539
- Points
- 1,963
- Location
- Clear Lake, IA
- Website
- www.piergenius.com
Quick update on Winder:
After being in the shop since FEB 2021! Yes '21! I got a call that I am getting a Yamaha longblock not parts and have the dealer assemble it but a factory assembled long block. Yay! I have hated that sled and its 3 motors its gone through.
I 'think' the problem was the flash and I am going back to stock with it. Then not sure if I will keep it assuming it runs after that. One part says sell that POS and another is like validate it was the flash and run it for 1000 miles. I still have warranty on it. First world problems...
After being in the shop since FEB 2021! Yes '21! I got a call that I am getting a Yamaha longblock not parts and have the dealer assemble it but a factory assembled long block. Yay! I have hated that sled and its 3 motors its gone through.
I 'think' the problem was the flash and I am going back to stock with it. Then not sure if I will keep it assuming it runs after that. One part says sell that POS and another is like validate it was the flash and run it for 1000 miles. I still have warranty on it. First world problems...

kinger
VIP Member
- Joined
- Jan 17, 2005
- Messages
- 7,403
- Reaction score
- 1,539
- Points
- 1,963
- Location
- Clear Lake, IA
- Website
- www.piergenius.com

kinger
VIP Member
- Joined
- Jan 17, 2005
- Messages
- 7,403
- Reaction score
- 1,539
- Points
- 1,963
- Location
- Clear Lake, IA
- Website
- www.piergenius.com
I will do a vid soon but big update for the Twincharged!
I pieced together a DIRECT PORT 50/50 methanol injection kit! I will have 4 nozzles spraying right at each throttle body. I used the following and it was a challenge because of different companies out of different parts.
1. Pro Meth direct port nylon kit with inline distribution block and solenoid. Hopefully this helps someone someday but I went with a solenoid vs a check valve because I am going to use the Motec to control the PWM output to the solenoid and it takes MUCH less current then sending a PWM signal to the pump and trying to run the pump as a progressive kit. Both work but I think the solenoid will be faster response and more accurate for my application. This kit does NOT come with nozzles, pump, filter, or tube, I just like the nozzle holders as they are low profile. $~280
2. Nozzles I wanted Devils Own but their web site stinks and wouldn't take my order then I see they are out of stock. So I went with Snow performance 2.5 GPH nozzles. This will flow enough for around 600hp. Basically if you want 600hp you need 600 cc/min injector, if you do the math converison from 2.5 GPH to cc/min you get around 157 *4 injectors = 628 cc/min. This will take some trial and error here I may need much larger nozzles I am not sure, with the DO kit those nozzles were 370 cc EACH and I know at least one person running that on a RX1 so I either need more or he is injecting way to much water/meth. So I got the Snow Perfomance nozzles (4), pump, filter, tank tap and some 1/4" nylon tubing for $~380. This will be everything I need but a Tank.
3. I am going to add a flow Sensor from AEM this uses a turbine in it to measure actual flow. I can set up tables in my Motec software to respond to this. So if it sees NO flow it will cut all turbo boost out, and I will run on 91 with just the blower and be safe. This will also let me see how much the progressive system is actually pumping. I can also link it to knock and make sure if adds more as a compensation if it sees any knock.
Lastly specific to my sled and the Motec M400 engine management I am out of inputs and outputs so I had to purchase a I/O expander called a Motec E888 which connects via the 2 wire canbus. This will allow me to connect literally anything I want and I can control 8 outputs. I will use up 2 for the meth. Current plan for this expander:
PWM output 1 will turn on meth pump at 12 psi by sending a signal to my PDM which will then power the pump with NO relay. Pretty cool!
PWM output 2 will then send a ground signal to the solenoid at varying rates per my table. I am thinking something like 20% at 15 psi, 50% at 20 psi, 75% at 22 psi and 100% at 25+ psi. What is cool here is I can configure this based on ANY signal in from the Motec. So I can do it by speed, or on a timer, or RPM, etc. I can also set up a knock compensation table to add some if it sees knock no matter what. Motec life rules!
More cool things the E888 allows me to do is it has 8 thermo couple inputs and someday I may add 4 EGTs for each cylinder to keep an eye on problem ones like #3 which like to get hot. I am already adding more fuel to #3 to help cool it so this would be a good validation. I would do it immediately but the Race header from impulse is a FRICKEN bear to get on and off with engine in the sled. I may wait until the engine is out then I can properly install the header and 4 EGTs about 1.5" away from the valves. In the mean time I am going to add 1 post turbo near my O2 sensor to see if my O2 is getting too hot and that is why I can't make them last more than a year. I need the O2 to last so I can run closed loop fuel, right not it's too unreliable and I run open loop. That sensor needs to be reliable so this EGT will help me. In addition once I have a good sensor and good EGT temp correlations I will be able to make a closed loop table that uses BOTH O2 and EGT as a safeguard in case one goes out.
Lastly I am going to get the Motec 5hz GPS module and test if its fast enough and good enough signal in the northwoods to enable some sort of traction control for launching. I am going to turn on my Launch control this year finally and play with acceleration testing. I REALLY wanted to get an accelerometer sensor and use that maximizing G force in the forward direction but they are like $500-1000 and I don't think it will matter on snow. That is just me geeking out on all this newfound data
So upcoming episode will be installing 2nd gate, and laying out my meth and bench testing everything to see that it works the way I want.
Lastly I want to FINALLY try the Ski doo Xp trail tank I got for it and XP seat I have. There is a lot to swap the tank and I will go into detail on that in a separate thread and vid. I have a 2 up seat for the XP tank LOL How funny would that be! More to come!
I pieced together a DIRECT PORT 50/50 methanol injection kit! I will have 4 nozzles spraying right at each throttle body. I used the following and it was a challenge because of different companies out of different parts.
1. Pro Meth direct port nylon kit with inline distribution block and solenoid. Hopefully this helps someone someday but I went with a solenoid vs a check valve because I am going to use the Motec to control the PWM output to the solenoid and it takes MUCH less current then sending a PWM signal to the pump and trying to run the pump as a progressive kit. Both work but I think the solenoid will be faster response and more accurate for my application. This kit does NOT come with nozzles, pump, filter, or tube, I just like the nozzle holders as they are low profile. $~280
2. Nozzles I wanted Devils Own but their web site stinks and wouldn't take my order then I see they are out of stock. So I went with Snow performance 2.5 GPH nozzles. This will flow enough for around 600hp. Basically if you want 600hp you need 600 cc/min injector, if you do the math converison from 2.5 GPH to cc/min you get around 157 *4 injectors = 628 cc/min. This will take some trial and error here I may need much larger nozzles I am not sure, with the DO kit those nozzles were 370 cc EACH and I know at least one person running that on a RX1 so I either need more or he is injecting way to much water/meth. So I got the Snow Perfomance nozzles (4), pump, filter, tank tap and some 1/4" nylon tubing for $~380. This will be everything I need but a Tank.
3. I am going to add a flow Sensor from AEM this uses a turbine in it to measure actual flow. I can set up tables in my Motec software to respond to this. So if it sees NO flow it will cut all turbo boost out, and I will run on 91 with just the blower and be safe. This will also let me see how much the progressive system is actually pumping. I can also link it to knock and make sure if adds more as a compensation if it sees any knock.
Lastly specific to my sled and the Motec M400 engine management I am out of inputs and outputs so I had to purchase a I/O expander called a Motec E888 which connects via the 2 wire canbus. This will allow me to connect literally anything I want and I can control 8 outputs. I will use up 2 for the meth. Current plan for this expander:
PWM output 1 will turn on meth pump at 12 psi by sending a signal to my PDM which will then power the pump with NO relay. Pretty cool!
PWM output 2 will then send a ground signal to the solenoid at varying rates per my table. I am thinking something like 20% at 15 psi, 50% at 20 psi, 75% at 22 psi and 100% at 25+ psi. What is cool here is I can configure this based on ANY signal in from the Motec. So I can do it by speed, or on a timer, or RPM, etc. I can also set up a knock compensation table to add some if it sees knock no matter what. Motec life rules!
More cool things the E888 allows me to do is it has 8 thermo couple inputs and someday I may add 4 EGTs for each cylinder to keep an eye on problem ones like #3 which like to get hot. I am already adding more fuel to #3 to help cool it so this would be a good validation. I would do it immediately but the Race header from impulse is a FRICKEN bear to get on and off with engine in the sled. I may wait until the engine is out then I can properly install the header and 4 EGTs about 1.5" away from the valves. In the mean time I am going to add 1 post turbo near my O2 sensor to see if my O2 is getting too hot and that is why I can't make them last more than a year. I need the O2 to last so I can run closed loop fuel, right not it's too unreliable and I run open loop. That sensor needs to be reliable so this EGT will help me. In addition once I have a good sensor and good EGT temp correlations I will be able to make a closed loop table that uses BOTH O2 and EGT as a safeguard in case one goes out.
Lastly I am going to get the Motec 5hz GPS module and test if its fast enough and good enough signal in the northwoods to enable some sort of traction control for launching. I am going to turn on my Launch control this year finally and play with acceleration testing. I REALLY wanted to get an accelerometer sensor and use that maximizing G force in the forward direction but they are like $500-1000 and I don't think it will matter on snow. That is just me geeking out on all this newfound data

So upcoming episode will be installing 2nd gate, and laying out my meth and bench testing everything to see that it works the way I want.
Lastly I want to FINALLY try the Ski doo Xp trail tank I got for it and XP seat I have. There is a lot to swap the tank and I will go into detail on that in a separate thread and vid. I have a 2 up seat for the XP tank LOL How funny would that be! More to come!
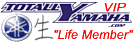

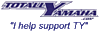
earthling
Lifetime Member
- Joined
- Dec 1, 2017
- Messages
- 2,003
- Reaction score
- 1,953
- Points
- 1,183
- Location
- Ontario
- Country
- Canada
- Snowmobile
- 2021 SRX
2006 ATTAK
I will do a vid soon but big update for the Twincharged!
[snip]
Lastly I am going to get the Motec 5hz GPS module and test if its fast enough and good enough signal in the northwoods to enable some sort of traction control for launching. I am going to turn on my Launch control this year finally and play with acceleration testing. I REALLY wanted to get an accelerometer sensor and use that maximizing G force in the forward direction but they are like $500-1000 and I don't think it will matter on snow. That is just me geeking out on all this newfound data![]()
You mean like active traction control or selectable maps for acceleration management?

kinger
VIP Member
- Joined
- Jan 17, 2005
- Messages
- 7,403
- Reaction score
- 1,539
- Points
- 1,963
- Location
- Clear Lake, IA
- Website
- www.piergenius.com
Active. When track speed is faster then ground speed pull timing, etc. I don’t think it will work but be nice to have real speed. I think I need more of a 20hz speed cam this won’t react quick enough. Ill try it. Worst thing I get intermittent data.You mean like active traction control or selectable maps for acceleration management?
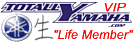

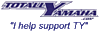
earthling
Lifetime Member
- Joined
- Dec 1, 2017
- Messages
- 2,003
- Reaction score
- 1,953
- Points
- 1,183
- Location
- Ontario
- Country
- Canada
- Snowmobile
- 2021 SRX
2006 ATTAK
Active. When track speed is faster then ground speed pull timing, etc. I don’t think it will work but be nice to have real speed. I think I need more of a 20hz speed cam this won’t react quick enough. Ill try it. Worst thing I get intermittent data.
I think you will find that GPS, even if you can get the sampling rate up, just isn't fast enough for what you are trying to do. GPS was just never designed to understand acceleration and its low sampling rate means that positional change (difference in location) would have to run at very high sampling to be accurate at all. Even at that, the locations are based on probabilities, not absolutes. You need absolutes and a reliable source of high frequency data samples.
Accelerometers can give you acceleration by themselves but they won't tell you anything about how you are getting there. To an accelerometer, the only thing it 'knows' is that something is happening (you are accelerating) it cannot tell you why or how. You could work out some kind of map by using some combination of pitch/forward motion but its going to be a set of fairly coarse numbers and as soon as you change anything (or lose traction) you are going to have a bunch of noise in the system (e.g. negative g-forces) which have to be filtered out.
Take all of the below at face value (thinking out loud) and as thinking through approaches to traction control.
You have engine RPM and you could get secondary RPM. Given that the ratio between them is a reflection of expected track speed once you factor in the track length I think you would have a crude understanding of idealized (linear-forward) velocity which, when mapped against time would provide you with an expectation of targeted acceleration as a map. I am sure there are other ways to look at it but this would be my intuitive approach. You could then apply modifications to that curve based on actual conditions and real world tests. The good news here is that engine dyno performance will give you the input curves you need to map into the idealized throttle map. Your modulation system (throttle demand) would be structured to keep you as close to that curve as possible without exceeding it at any given point in time. You would ideally position yourself between the throttle input and application of throttle. Basically, you put the sled in launch control mode and physically pin the throttle and the system releases throttle demand to the engine along the idealized curve until it exceeds the curve and then backs off, and then ramps back to the curve. I am sure a race engineer with experience in the field would poke a lot of holes in the approach but I think it has to be an improvement over the GPS only or even GPS plus accelerometer approach.
KTM on traction control

kinger
VIP Member
- Joined
- Jan 17, 2005
- Messages
- 7,403
- Reaction score
- 1,539
- Points
- 1,963
- Location
- Clear Lake, IA
- Website
- www.piergenius.com
Newer garage for builds complete.

kinger
VIP Member
- Joined
- Jan 17, 2005
- Messages
- 7,403
- Reaction score
- 1,539
- Points
- 1,963
- Location
- Clear Lake, IA
- Website
- www.piergenius.com
Couple vid updates:

kinger
VIP Member
- Joined
- Jan 17, 2005
- Messages
- 7,403
- Reaction score
- 1,539
- Points
- 1,963
- Location
- Clear Lake, IA
- Website
- www.piergenius.com
2nd gate fits! Barely

kinger
VIP Member
- Joined
- Jan 17, 2005
- Messages
- 7,403
- Reaction score
- 1,539
- Points
- 1,963
- Location
- Clear Lake, IA
- Website
- www.piergenius.com
Couple more updates, more of planning vids and looking for advice then working, I think I finally have everything ready to start installing. Hoping to finish from handle bar back, then I want to test the Meth system before popping off the IC and drilling into it. Going to be adding 5 EGTs for more data just because it will help me feel better then tuning the with Meth for my first time. If I get real ambitious I REALLY want to get my XP tank mounted and figure out all problems that causes with plumbing. I really want that nice XP seat feel and possibly get my 2 up seat on there for confusing aesthetics. HAHA

kinger
VIP Member
- Joined
- Jan 17, 2005
- Messages
- 7,403
- Reaction score
- 1,539
- Points
- 1,963
- Location
- Clear Lake, IA
- Website
- www.piergenius.com

kinger
VIP Member
- Joined
- Jan 17, 2005
- Messages
- 7,403
- Reaction score
- 1,539
- Points
- 1,963
- Location
- Clear Lake, IA
- Website
- www.piergenius.com
EGTs for days!

kinger
VIP Member
- Joined
- Jan 17, 2005
- Messages
- 7,403
- Reaction score
- 1,539
- Points
- 1,963
- Location
- Clear Lake, IA
- Website
- www.piergenius.com
Got the EGTs installed. Posted some vids on channel about that.
Ran into a couple issues that will create more work for me.
1. Exhaust the loudvalve is loose as a goose and I’m not sure what happened to it. Sent it to the company and they are going to warranty for FREE! It’s 6 years old! Crazy cool of them.
2. I noticed a lot of oil mist on the PTO side of the engine. Crankcase needs some more EVAC and I’m toying with welding in a Venturi tube and venting it that way to create some negative pressure.
So I may need to build a new exhaust to fix some of this. Toying with a new design that refines what I had.
Just a fun pict from the vid on YouTube
Ran into a couple issues that will create more work for me.
1. Exhaust the loudvalve is loose as a goose and I’m not sure what happened to it. Sent it to the company and they are going to warranty for FREE! It’s 6 years old! Crazy cool of them.
2. I noticed a lot of oil mist on the PTO side of the engine. Crankcase needs some more EVAC and I’m toying with welding in a Venturi tube and venting it that way to create some negative pressure.
So I may need to build a new exhaust to fix some of this. Toying with a new design that refines what I had.
Just a fun pict from the vid on YouTube

Similar threads
- Replies
- 6
- Views
- 5K
- Replies
- 5
- Views
- 889
-
This site uses cookies to help personalise content, tailor your experience and to keep you logged in if you register.
By continuing to use this site, you are consenting to our use of cookies.