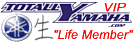

Crewchief47
Lifetime Member
- Joined
- Jan 16, 2006
- Messages
- 2,830
- Reaction score
- 32
- Points
- 1,333
- Location
- McGregor, ON Canada
- Country
- Canada
- Snowmobile
- 2008 Nytro MTX 45th
Without looking at my sled, why can't you just put the valve into the existing line going to the airbox?
towerrigger
TY 4 Stroke Junkie
Has anyone looked at this moroso oil/air seperator it's a bit pricey.

Yellowknife
TY 4 Stroke Master
- Joined
- Jan 25, 2004
- Messages
- 1,105
- Reaction score
- 54
- Points
- 988
- Location
- Yellowknife, NT, Canada
- Website
- www.youtube.com
Bamboo said:Yellowknife said:Okay well, I'm going to take idea's forward to Yamaha Canada and get something approved through my dealer. I think they are willing to work towards a solution, but I need them on board.
Sorry to hijack your thread. But if your already going to your dealer for a fix, add a hand warmer fix. I know you have great influence with Yamaha Canada.
I don't have any special pull with them really, they just work well with my dealer and i've been able to speak to them directly on issues and they have been receptive. I think with a good dealer, anyone could build a good relationship with them. The key is good constructive feedback.
The handwarmers are weak I know. I don't know why.
Mtnviper
TY 4 Stroke Master
- Joined
- Aug 19, 2003
- Messages
- 1,476
- Reaction score
- 340
- Points
- 1,288
- Location
- Burlington Wa.
- Website
- fourstrokesolutionsllc.com
Here's mine. Valve is a normally open EVAP vent valve. Controlled by a switching relay. Key on engine off (either by kill switch, or fuel pump time out), power is supplied to the vent valve so it closes. As soon as the engine is started, power is fed to the switching relay via the fuel pump curcuit. Relay then cuts the power to the valve and it opens.
A tether could also be wired in as long as it's wired in series with the kill switch. System works automaticlly, pretty much turn key and ride.
For saftey, the red LED will flash anytime there is voltage applied to the valve (closed).
In addition there is also a pressure switch that closes when ever there is a pressure build up in the tank. For example if the valve was stuck closed mechaniclly or frozen. The pressure switch would close and turn on the flashing LED. Pressure switch closes at 2 psi. There should never be a flashing LED while the engine is running.
I also thought about using a 3 terminal pressure switch that could be wired into the kill switch curcuit. Then if the pressure switch detected pressure,it would shut off the engine. Just a matter of finding someone who makes such a switch, that activates at very low pressure and is resistant to oil and extreme temps.
The additional tee'd in plumbing is for a pressure/vacuum gauge mounted on the dash for testing purposes.
BTW, I did some patent searches, turns out Doo already has some similiar for watercraft applications
Which could explian why Yamaha dosn't have a electronic vent shut off on their sleds.
Dosn't mean that we can't build our own though!
A tether could also be wired in as long as it's wired in series with the kill switch. System works automaticlly, pretty much turn key and ride.
For saftey, the red LED will flash anytime there is voltage applied to the valve (closed).
In addition there is also a pressure switch that closes when ever there is a pressure build up in the tank. For example if the valve was stuck closed mechaniclly or frozen. The pressure switch would close and turn on the flashing LED. Pressure switch closes at 2 psi. There should never be a flashing LED while the engine is running.
I also thought about using a 3 terminal pressure switch that could be wired into the kill switch curcuit. Then if the pressure switch detected pressure,it would shut off the engine. Just a matter of finding someone who makes such a switch, that activates at very low pressure and is resistant to oil and extreme temps.
The additional tee'd in plumbing is for a pressure/vacuum gauge mounted on the dash for testing purposes.
BTW, I did some patent searches, turns out Doo already has some similiar for watercraft applications

Dosn't mean that we can't build our own though!

Attachments
Yellowknife
TY 4 Stroke Master
- Joined
- Jan 25, 2004
- Messages
- 1,105
- Reaction score
- 54
- Points
- 988
- Location
- Yellowknife, NT, Canada
- Website
- www.youtube.com
So - I might be confused here, is the valve drawing power when the kill switch is OFF or the key is OFF? (Drawing power whenever the sled isn't running to keep the valve closed?)
Koeckman
Extreme
Most should be (better be) normally powered open and manually (spring) operated closed when there is no power keeping it open. Those running them may want to double check the operation of the particular valve they are using to ensure or they will end up with a dead battery when they go to ride.
Great idea, I was looking for a valve to do the same thing. If we can find out what kind of pressure the tank is producing, we will then be able to potentially install a simple non-powered check valve. One that by the pressure produced in the tank would be able to open the valve and vent as normal, yet not enough pressure by simple fluid dynamics to open and allow the fluid to stay in the tank. I kind of think the manual will not a be an option as I don't think there is very much pressure in the tank, maybe a couple PSI. It also will allow a small amount of back pressure to build before enough pressure builds to overcome the spring tension. Not sure it is worth it, just depends on the amount of pressure the tank builds.
I'm going to go with the trusty old bottle set-up for now, as it is simple with no worries in the world, if it fails the worst is you loose your oil and have to replace, where as if a valve fails, you potentially loose your motor.
In the mean time, when I'm not riding with my wife (my pack mule, who hauls all my c$%^/gear as she is not nearly as aggressive of a rider) I mounted a little oil bottle caddy under my hood to hold a quart of oil in the event I ever lost any, or needed any while way out where I would not normally have access otherwise. I think it was made by PowerMadd but don't remember, it's been laying around in the garage forever, I almost threw it out a couple times but never did. Always said....."I'll use that some day". works like a champ.
r0tax, how did you attach the bottle cap to the hose? Did you plastic weld it or just cut a really tight hole in the bottle top? Any help would be greatly appreciated.
Great idea, I was looking for a valve to do the same thing. If we can find out what kind of pressure the tank is producing, we will then be able to potentially install a simple non-powered check valve. One that by the pressure produced in the tank would be able to open the valve and vent as normal, yet not enough pressure by simple fluid dynamics to open and allow the fluid to stay in the tank. I kind of think the manual will not a be an option as I don't think there is very much pressure in the tank, maybe a couple PSI. It also will allow a small amount of back pressure to build before enough pressure builds to overcome the spring tension. Not sure it is worth it, just depends on the amount of pressure the tank builds.
I'm going to go with the trusty old bottle set-up for now, as it is simple with no worries in the world, if it fails the worst is you loose your oil and have to replace, where as if a valve fails, you potentially loose your motor.
In the mean time, when I'm not riding with my wife (my pack mule, who hauls all my c$%^/gear as she is not nearly as aggressive of a rider) I mounted a little oil bottle caddy under my hood to hold a quart of oil in the event I ever lost any, or needed any while way out where I would not normally have access otherwise. I think it was made by PowerMadd but don't remember, it's been laying around in the garage forever, I almost threw it out a couple times but never did. Always said....."I'll use that some day". works like a champ.
r0tax, how did you attach the bottle cap to the hose? Did you plastic weld it or just cut a really tight hole in the bottle top? Any help would be greatly appreciated.
r0tax
Pro
- Joined
- Apr 9, 2008
- Messages
- 182
- Reaction score
- 0
- Points
- 226
- Location
- Whitefish, MT
- Website
- rotax.shorturl.com
Koeckman said:r0tax, how did you attach the bottle cap to the hose? Did you plastic weld it or just cut a really tight hole in the bottle top? Any help would be greatly appreciated.
hehe nothing fancy at all..
drilled a hole, screwed the 'screw-on nipple' into the cap/hole, gooped some epoxy/sealant around the hole, screwed on the bottle.
could be a mess when it finally does fill/drain..but it can't be worse than just dumping all the oil straight into the side panel..
i've had a couple rides on it since, but theres no sign of oil in the hoses or bottle..so I guess I haven't had it far enough on its side.
will update once i actually have seen it work...or have rolled it...etc
Mtnviper
TY 4 Stroke Master
- Joined
- Aug 19, 2003
- Messages
- 1,476
- Reaction score
- 340
- Points
- 1,288
- Location
- Burlington Wa.
- Website
- fourstrokesolutionsllc.com
Yellowknife said:So - I might be confused here, is the valve drawing power when the kill switch is OFF or the key is OFF? (Drawing power whenever the sled isn't running to keep the valve closed?)
Draws power when the key is on, but the engine is off (kill switch down) . When the key is off, there is no power draw, everything is off.
When the engine is running it only draws a few milliamps to power the switching relay.
Valve/flashing LED only draws 1/2 of an amp. So far the longest I've had sled on it's side and valve powered is 1/2 hour. Sled fired right up afterwards, with zero oil loss!
Main reason I went with a normally open valve, is because if the valve ever fails, it will stay open. Also being a EVAP valve it is designed to withstand fuel/oil vapors.
Yellowknife
TY 4 Stroke Master
- Joined
- Jan 25, 2004
- Messages
- 1,105
- Reaction score
- 54
- Points
- 988
- Location
- Yellowknife, NT, Canada
- Website
- www.youtube.com
ahhh got it. I like that idea best.
I don't know how much a GPS draws, but I have that on my sled all day and never had problems - wired directly to battery, ride out, sled sits for 8 hours sometimes with GPS drawing power, fires up for ride back.
I don't know how much a GPS draws, but I have that on my sled all day and never had problems - wired directly to battery, ride out, sled sits for 8 hours sometimes with GPS drawing power, fires up for ride back.
DamonJones
Extreme
I have a couple thoughts on this problem. First the solution that r0tax has. It would seem to me that from what the others are saying about this problem that the catch can is a bit on the samll size. Also a shorter breather hose would minimize the amount of fluid lost when righted. My thought would be to eliminate the catch can and run a short hose directly down the front of the oil tank past the bottom maybe even hooking slightly back under it. When the sled over turns this will fill with oil but a smaller amount will be lost. Another thought would be to run the hose to the outside(left side) of the oil can. Then if possible when righting the sled do it in a clockwise rotation, looking from the back of the sled. Most of the oil would then drain back into the tank.
On the electronic valve idea I would think a system that fails into a safe mode would be best. Meaning if the electronics fail the valve would be open. How about triggering the valve to close only if the sled is upside down. I believe I've seen roll over switches before or use multiple large mercury switches. Only close the valve when it needs to close.
The last idea would be a heavy ball check valve installed upside down. Blow by would not close it but gravity and oil wiegth would when overturned.
The last two idea would work for non-boosted sleds as well. I've seen what happens when these sleds stay upside down for long times. I was riding with a new Phazer that lost a huge amount of oil before it was turned back over. They must have the same issue.
Lastly on the boosted sled, shouldn't this vent into the air intake system before the pump. That is how it's done on auto's anyway, it vents to the outside of the air filter. Obviously you's want a valve to stop oil saturation when overturned. This would meet the emissions issue and screen the breather from dirt. In addition it would keep oil slatter from getting all over.
Thoughts?
On the electronic valve idea I would think a system that fails into a safe mode would be best. Meaning if the electronics fail the valve would be open. How about triggering the valve to close only if the sled is upside down. I believe I've seen roll over switches before or use multiple large mercury switches. Only close the valve when it needs to close.
The last idea would be a heavy ball check valve installed upside down. Blow by would not close it but gravity and oil wiegth would when overturned.
The last two idea would work for non-boosted sleds as well. I've seen what happens when these sleds stay upside down for long times. I was riding with a new Phazer that lost a huge amount of oil before it was turned back over. They must have the same issue.
Lastly on the boosted sled, shouldn't this vent into the air intake system before the pump. That is how it's done on auto's anyway, it vents to the outside of the air filter. Obviously you's want a valve to stop oil saturation when overturned. This would meet the emissions issue and screen the breather from dirt. In addition it would keep oil slatter from getting all over.
Thoughts?
Mtnviper
TY 4 Stroke Master
- Joined
- Aug 19, 2003
- Messages
- 1,476
- Reaction score
- 340
- Points
- 1,288
- Location
- Burlington Wa.
- Website
- fourstrokesolutionsllc.com
The bouncing/pounding that sleds go though, makes it kind of tough to come up with a true roll over sensor for a sled. I believe some watercraft have a type of roll-over sensor. They can bounce around pretty good, so it might be possible to adapt something from a PWC?
I gave mine a longer test. Left the valve on while I had the sled on it's side(s) to pull the sway bar out. So far so good!
Was out riding/carving with it, and fell off. Had to quickly reach for the kill switch, as the motor was still running and the valve would be open. Although the oil wouldn't leak out any faster then if the breather was stock, I think I'll wire in a teather switch.
Edit: system will work with a teather switch, if it is wired as per Allen's method. http://www.ty4stroke.com/viewtopic.php?t=46889
I gave mine a longer test. Left the valve on while I had the sled on it's side(s) to pull the sway bar out. So far so good!
Was out riding/carving with it, and fell off. Had to quickly reach for the kill switch, as the motor was still running and the valve would be open. Although the oil wouldn't leak out any faster then if the breather was stock, I think I'll wire in a teather switch.

Edit: system will work with a teather switch, if it is wired as per Allen's method. http://www.ty4stroke.com/viewtopic.php?t=46889
rfabro
TY 4 Stroke Junkie
Damon, turbos don't have airboxes and the whole intake system is under boost pressure.
Mtnviper, if you get a tether, your system will be the bomb. I recommend getting one from Ulmer. I got like 6 other ones(normally open and closed) from other vendors, that were all wrong, before getting the right one from Ulmer.
Mtnviper, if you get a tether, your system will be the bomb. I recommend getting one from Ulmer. I got like 6 other ones(normally open and closed) from other vendors, that were all wrong, before getting the right one from Ulmer.
DamonJones
Extreme
rfabro said:Damon, turbos don't have airboxes and the whole intake system is under boost pressure..
The system is still a vacuum on the intake side of the turbo. It could vent into the air cleaner or the tube between the air cleaner and the turbo. Read my post carefully "air intake system BEFORE the pump"
woodsrider
TY 4 Stroke Junkie
- Joined
- Feb 17, 2005
- Messages
- 669
- Reaction score
- 11
- Points
- 893
- Location
- Lewiston, ID
- Country
- USA
- Snowmobile
- 2017 YZ450FX1 Moto-Trax 137 Mountain Kit
why would you want to dump the vent back into the turbo intake?
rfabro
TY 4 Stroke Junkie
A turbo is a pump how? I would think just about everyone would consider it a compressor.
Ya, I read the post carefully the first time, but thanks for instructing me to do so again.
Ya, I read the post carefully the first time, but thanks for instructing me to do so again.
Similar threads
- Replies
- 18
- Views
- 2K
- Replies
- 23
- Views
- 8K
-
This site uses cookies to help personalise content, tailor your experience and to keep you logged in if you register.
By continuing to use this site, you are consenting to our use of cookies.