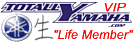

1nc 2000
Lifetime Member Tim
- Joined
- Feb 26, 2010
- Messages
- 3,058
- Location
- Marquette, MI
- Country
- USA
- Snowmobile
- Yamaha FX Nytro RTX SE
What i am seeing is the pin bore in the secondary clutch (aluminum piece) that holds the steel roller pin is wearing egg shaped.
Pin will then sit at an angle and wider aftermarket roller will bind between ears due to sag of pin.
The roller will be sticky and hard to turn.
In a pinch the stock rollers will still turn due to being narrower.
Time to look for a replacement secondary clutch then.

Pin will then sit at an angle and wider aftermarket roller will bind between ears due to sag of pin.
The roller will be sticky and hard to turn.
In a pinch the stock rollers will still turn due to being narrower.
Time to look for a replacement secondary clutch then.

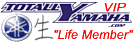

1nc 2000
Lifetime Member Tim
- Joined
- Feb 26, 2010
- Messages
- 3,058
- Location
- Marquette, MI
- Country
- USA
- Snowmobile
- Yamaha FX Nytro RTX SE
Another temporary fix would be to sand down the flat area of the wider rollers at an angle so it will not bind on the inner lug.

KnappAttack
24X ISR World Drag Racing Champion
- Joined
- Feb 19, 2004
- Messages
- 4,686
- Location
- Welch MN
- Country
- USA
- Snowmobile
- 2023 Sidewinder LTX-LE
2017 Sidewinder LTX-LE
Posted this in the other three where you were talking about this.....
So yours has the pin holes egged out? Let me ask what rollers are you running on there?
I've got many thousands of miles on the what I believe to be the best rollers out there, the Hi-Torques and have no pins rolling in the sheave. They roll supper easy when new but get a bit more sticky with time. I test a lot of setups that roll thru here on my drill press scale and have yet to find anything that rolls as smooth and easily as the Hi-Torques. Might want to try some. I've seen some really poor and crunchy rollers, the worst offenders are the factory rollers!
I've been researching putting a sealed roller bearing on the stock pins to reduce the resistance and get more consistency yet. Thinking about boring out an old set of hi-torques and epoxying and pressing in a greased & sealed roller bearing so there still a soft roller on the alum helix.
FYI I have also run the Viper button secondary on the Winder with great success too, It just doesn't backshift quite as quick as the winder roller secondary, but it isn't far behind, plus I was running a light spring in the Viper secondary when I was testing it, I bet a wee bit stiffer spring would even that up. I'd run the Viper secondary on a trail sled over the STM or the Pro-4 myself, but thats just me. Seen many switch over to billet secondaries and don't see the reason or need myself. The STM secondaries crack on a trail sled I know that, seen it first hand with very low miles on it.... Pro-4 seems to be the better ticket here, but not going to be better performance than the stock secondary IMO.
So yours has the pin holes egged out? Let me ask what rollers are you running on there?
I've got many thousands of miles on the what I believe to be the best rollers out there, the Hi-Torques and have no pins rolling in the sheave. They roll supper easy when new but get a bit more sticky with time. I test a lot of setups that roll thru here on my drill press scale and have yet to find anything that rolls as smooth and easily as the Hi-Torques. Might want to try some. I've seen some really poor and crunchy rollers, the worst offenders are the factory rollers!
I've been researching putting a sealed roller bearing on the stock pins to reduce the resistance and get more consistency yet. Thinking about boring out an old set of hi-torques and epoxying and pressing in a greased & sealed roller bearing so there still a soft roller on the alum helix.
FYI I have also run the Viper button secondary on the Winder with great success too, It just doesn't backshift quite as quick as the winder roller secondary, but it isn't far behind, plus I was running a light spring in the Viper secondary when I was testing it, I bet a wee bit stiffer spring would even that up. I'd run the Viper secondary on a trail sled over the STM or the Pro-4 myself, but thats just me. Seen many switch over to billet secondaries and don't see the reason or need myself. The STM secondaries crack on a trail sled I know that, seen it first hand with very low miles on it.... Pro-4 seems to be the better ticket here, but not going to be better performance than the stock secondary IMO.
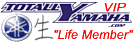

1nc 2000
Lifetime Member Tim
- Joined
- Feb 26, 2010
- Messages
- 3,058
- Location
- Marquette, MI
- Country
- USA
- Snowmobile
- Yamaha FX Nytro RTX SE
I have been running Hi-Torques rollers for several years now.
The pin design would be better if it was longer and bolt went thru it not allowing it to rotate.
The pin design would be better if it was longer and bolt went thru it not allowing it to rotate.

KnappAttack
24X ISR World Drag Racing Champion
- Joined
- Feb 19, 2004
- Messages
- 4,686
- Location
- Welch MN
- Country
- USA
- Snowmobile
- 2023 Sidewinder LTX-LE
2017 Sidewinder LTX-LE
I have been running Hi-Torques rollers for several years now.
The pin design would be better if it was longer and bolt went thru it not allowing it to rotate.
Interssting, how many miles on the secondary then? Ive seen no pin rotation in my 8000+ mile secondary. In fact, I had a hard time getting the pins out the last time as almost stuck in there.
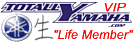

1nc 2000
Lifetime Member Tim
- Joined
- Feb 26, 2010
- Messages
- 3,058
- Location
- Marquette, MI
- Country
- USA
- Snowmobile
- Yamaha FX Nytro RTX SE
Over 13,000 miles.
I had a hard time getting the pins out also due to the wear in pin bore.
Even after cleaning everything up real good the pins are still tough to get out by them selves with no roller installed.
Just order new sheave , pins and bolts.
At least a month out for parts.
I had a hard time getting the pins out also due to the wear in pin bore.
Even after cleaning everything up real good the pins are still tough to get out by them selves with no roller installed.
Just order new sheave , pins and bolts.
At least a month out for parts.
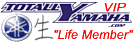

1nc 2000
Lifetime Member Tim
- Joined
- Feb 26, 2010
- Messages
- 3,058
- Location
- Marquette, MI
- Country
- USA
- Snowmobile
- Yamaha FX Nytro RTX SE
Just replaced the chaincase, jackshaft bearing and brake caliper with new. Well with a new secondary the driveline should be set for a while yet. With the tunnel beefed up and all the fixes done to this sled its a keeper. Might have to put power steering on it and run it. Been tuned since 2017.

KnappAttack
24X ISR World Drag Racing Champion
- Joined
- Feb 19, 2004
- Messages
- 4,686
- Location
- Welch MN
- Country
- USA
- Snowmobile
- 2023 Sidewinder LTX-LE
2017 Sidewinder LTX-LE
Over 13,000 miles.
I had a hard time getting the pins out also due to the wear in pin bore.
Even after cleaning everything up real good the pins are still tough to get out by them selves with no roller installed.
Just order new sheave , pins and bolts.
At least a month out for parts.
Mine were tight in there. I had to work real hard to get them in or out, I basically had to keep going in and out with them while cleaning to get them loosened up good enough to move in and out. I changed my rollers annually to keep them rolling freely, maybe thats the key I don't know.
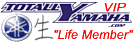

1nc 2000
Lifetime Member Tim
- Joined
- Feb 26, 2010
- Messages
- 3,058
- Location
- Marquette, MI
- Country
- USA
- Snowmobile
- Yamaha FX Nytro RTX SE
Same here. New rollers every year.
Had to use a Bent coat hanger to get them pushed out. Pick and magnet only got one out.
Had to use a Bent coat hanger to get them pushed out. Pick and magnet only got one out.
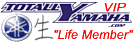

1nc 2000
Lifetime Member Tim
- Joined
- Feb 26, 2010
- Messages
- 3,058
- Location
- Marquette, MI
- Country
- USA
- Snowmobile
- Yamaha FX Nytro RTX SE
Just put the pin in by itself and push down on it.
If it has wear in the bore it will move.
If it has wear in the bore it will move.
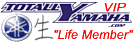

1nc 2000
Lifetime Member Tim
- Joined
- Feb 26, 2010
- Messages
- 3,058
- Location
- Marquette, MI
- Country
- USA
- Snowmobile
- Yamaha FX Nytro RTX SE
I pull my clutch back apart and throw up some pictures of the worn out areas.
Trussman
JAFO
- Joined
- Mar 18, 2007
- Messages
- 247
- Location
- WI
- Country
- USA
- Snowmobile
- 2004 Viper S
2017 'Winder
2022 SRX
I did just this on my 2017, found a rusty pin when I replaced the factory rollers .......with very few miles on it. Made new stainless pins long enough to run the bolts thru the pins.....I have been running Hi-Torques rollers for several years now.
The pin design would be better if it was longer and bolt went thru it not allowing it to rotate.
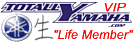

STAIN
Lifetime Member
- Joined
- Feb 29, 2004
- Messages
- 4,190
- Location
- Vermont
- Country
- USA
- Snowmobile
- 2022 SIDEWINDER LTX GT
- LOCATION
- Vermont
How about a brass bushing or sleeve?I've been researching putting a sealed roller bearing on the stock pins to reduce the resistance and get more consistency yet. Thinking about boring out an old set of hi-torques and epoxying and pressing in a greased & sealed roller bearing so there still a soft roller on the alum helix.
How may miles are you getting out of a set of Hi-torque rollers? Are you changing them just as a matter of preventive maintenance or are you seeing a difference between new and used on the scale/press?I changed my rollers annually to keep them rolling freely,
I installed a set of Hi-torque rollers when the my sled was new but haven't seen any signs of wear yet. I tested the rollers new in my press/scale but did not test them after a couple of thousand miles.

KnappAttack
24X ISR World Drag Racing Champion
- Joined
- Feb 19, 2004
- Messages
- 4,686
- Location
- Welch MN
- Country
- USA
- Snowmobile
- 2023 Sidewinder LTX-LE
2017 Sidewinder LTX-LE
How about a brass bushing or sleeve?
How may miles are you getting out of a set of Hi-torque rollers? Are you changing them just as a matter of preventive maintenance or are you seeing a difference between new and used on the scale/press?
I installed a set of Hi-torque rollers when the my sled was new but haven't seen any signs of wear yet. I tested the rollers new in my press/scale but did not test them after a couple of thousand miles.
I change them when the pressure gets high on the scale. 1500 miles or so on a set. They are still in good shape but get a little bit of play on the pin.
Sealed roller bearing rollers would be the ticket, and there are sealed roller bearings out that would work well, just need to build a set.
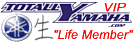

STAIN
Lifetime Member
- Joined
- Feb 29, 2004
- Messages
- 4,190
- Location
- Vermont
- Country
- USA
- Snowmobile
- 2022 SIDEWINDER LTX GT
- LOCATION
- Vermont
I mentioned a brass bushing to possibly insert in the current Hi torque roller to make it last longer, but a small bearing inserted in the roller would be insanely smooth.
I can only imagine how quickly the secondary would respond.
Do you think consistency would be a problem? I know it hard to beat the consistency of a button clutch, even if they don't shift as quickly as a roller.
You got me thinking now.
I can only imagine how quickly the secondary would respond.
Do you think consistency would be a problem? I know it hard to beat the consistency of a button clutch, even if they don't shift as quickly as a roller.
You got me thinking now.
Similar threads
- Replies
- 21
- Views
- 35K
- Replies
- 25
- Views
- 48K
-
This site uses cookies to help personalise content, tailor your experience and to keep you logged in if you register.
By continuing to use this site, you are consenting to our use of cookies.