Sevey
TY 4 Stroke God
- Joined
- Feb 15, 2011
- Messages
- 1,742
- Location
- Collingwood, ON
- Website
- www.ty4stroke.com
- Country
- Canada
- Snowmobile
- 2018 Sidewinder RTX
Anyone have ideas how to hold the drive shaft from turning when tightening the BOP wedge.
Up until now, I have always had the brake assembled and used the brake to hold it. Obviously if the brake is assembled it denies you the ability to check the tightness of bearing on the shaft.
The old yamaha's had a hex or octagon shaped shaft so you could get ahold of it with a crescent wrench.
Thanks
MS
Up until now, I have always had the brake assembled and used the brake to hold it. Obviously if the brake is assembled it denies you the ability to check the tightness of bearing on the shaft.
The old yamaha's had a hex or octagon shaped shaft so you could get ahold of it with a crescent wrench.
Thanks
MS
Turboflash
TY 4 Stroke God
- Joined
- Mar 18, 2019
- Messages
- 2,445
- Location
- Southern MN
- Country
- USA
- Snowmobile
- '17 ZR9000 Ltd. 137 - PEFI Stage 4
-Large screwdriver inserted across cogs in plastic track drive wheels?
-Maybe put brake rotor on spline and clamp a vice grip onto it somewhere near outer diameter? Rotate disc until vice grip is contacting something solid?
-Band/strap type pipe wrench tightened onto track shaft somewhere?
-Wait to install BOP wedge until you have the brake caliper put back together and bled?
-Maybe put brake rotor on spline and clamp a vice grip onto it somewhere near outer diameter? Rotate disc until vice grip is contacting something solid?
-Band/strap type pipe wrench tightened onto track shaft somewhere?
-Wait to install BOP wedge until you have the brake caliper put back together and bled?
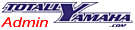

- Joined
- Apr 13, 2003
- Messages
- 21,322
- Age
- 54
- Location
- Schofield, WI
- Website
- www.totallyamaha.com
- Country
- USA
- Snowmobile
- 2020 Sidewinder SRX
Why would you need to hold it,? the wedge has a place to put a wrench on it and you tighten it with another wrench to pull wedge in place.
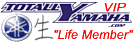

Those flats are supposed to go in shaft last I heard. Lines up wedge with bearing. That may have changed with his new batch.Why would you need to hold it,? the wedge has a place to put a wrench on it and you tighten it with another wrench to pull wedge in place.
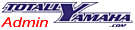

- Joined
- Apr 13, 2003
- Messages
- 21,322
- Age
- 54
- Location
- Schofield, WI
- Website
- www.totallyamaha.com
- Country
- USA
- Snowmobile
- 2020 Sidewinder SRX
Those flats are supposed to go in shaft last I heard. Lines up wedge with bearing. That may have changed with his new batch.
Well thats news to me.. sounds like he needs to make them longer then.
hellflyer
TY 4 Stroke Master
- Joined
- Dec 2, 2008
- Messages
- 1,086
- Location
- Georgtown ONT. Canada
- Country
- Canada
- Snowmobile
- 2020 sidewinder ltx se
I snugged mine up then tapped it in flush and tightened to 35lbs. All good here! All lathered up with anti seize
Chris Rose
Expert
- Joined
- Jul 29, 2016
- Messages
- 288
- Age
- 69
- Location
- Powassan ONT
- Country
- Canada
- Snowmobile
- 2017 sidewinder stx-DX with TD/Max 16 stock muffler
- WEBSITE
- chrisjrose2018@@gmail.com
I installed mine with enough to put a wrench on the flats, torqued to 40ft lb and the rotor still has wiggle on the shaft. Travis I'm sure designed it for wrench access. Also greased the assembly prior to the installation.
If its installed with flats showing it tends to expand more around the caliper then where the bearing rides. Leave the flats exposed to get it snugged up then tap it in to get it flush and finish tightening.I believe Travis mentions this in one of his videos on his site. Im assuming your trying to find how much torque you need to tighten your bearing hence the reason your brake is off. If your skid is still in then maybe just someone sitting on the sled will keep enough pressure to keep track from turning. If skids out, maybe a rope tied to drive cog and other end to something solid so it stops turning when ropes tight??
Sevey
TY 4 Stroke God
- Joined
- Feb 15, 2011
- Messages
- 1,742
- Location
- Collingwood, ON
- Website
- www.ty4stroke.com
- Country
- Canada
- Snowmobile
- 2018 Sidewinder RTX
If its installed with flats showing it tends to expand more around the caliper then where the bearing rides. Leave the flats exposed to get it snugged up then tap it in to get it flush and finish tightening.I believe Travis mentions this in one of his videos on his site. Im assuming your trying to find how much torque you need to tighten your bearing hence the reason your brake is off. If your skid is still in then maybe just someone sitting on the sled will keep enough pressure to keep track from turning. If skids out, maybe a rope tied to drive cog and other end to something solid so it stops turning when ropes tight??
yes - want to be able to torque it up but still be able grab caliper assembly and see at what point it bites.
Like your comment - once you make the wedge flush with the end of the shaft you can’t get a hold of it and the shaft will spin as you apply torque.
this is easy to determine if the shaft is out on the bench but not taking all the guts out to do this.
up till now have always assembled the brake so it could grab the rotor and keep shaft from turning - then there is no way to get as the bearing
Ms
Turboflash
TY 4 Stroke God
- Joined
- Mar 18, 2019
- Messages
- 2,445
- Location
- Southern MN
- Country
- USA
- Snowmobile
- '17 ZR9000 Ltd. 137 - PEFI Stage 4
I believe Travis has stated that the next revision of his wedge will be longer so it can be installed with the whole flat still exposed. Most say they install wedge as far as they can to still be able to hold it with a thin wrench, which places the 3 fingers directly under the bearing.
hellflyer
TY 4 Stroke Master
- Joined
- Dec 2, 2008
- Messages
- 1,086
- Location
- Georgtown ONT. Canada
- Country
- Canada
- Snowmobile
- 2020 sidewinder ltx se
You don’t need to hold it really! The three fingers grabbing the shaft over come the thread resistance easily. You just snug it up until it starts to grip the shaft and tap it in flush with a plastic head mallet then torque it to desired setting. You just have get the bolt treads And wedge lubed well to let it slip together easy.
the problem hes having is when you get over a certain amount of torque the driveshaft wants to turn as you tighten the wedge.. He has the brake apart and is trying to find the torque spec required for his machine to keep bearing tight on the shaft.You don’t need to hold it really! The three fingers grabbing the shaft over come the thread resistance easily. You just snug it up until it starts to grip the shaft and tap it in flush with a plastic head mallet then torque it to desired setting. You just have get the bolt treads And wedge lubed well to let it slip together easy.
hellflyer
TY 4 Stroke Master
- Joined
- Dec 2, 2008
- Messages
- 1,086
- Location
- Georgtown ONT. Canada
- Country
- Canada
- Snowmobile
- 2020 sidewinder ltx se
Oh ya! Forgot the point of this thread. To long between postings! Lol
I put a wood wedge in between track and heat exchanger. To hold mine when tightening and impact to release.
I put a wood wedge in between track and heat exchanger. To hold mine when tightening and impact to release.
I ground an opened wrench till it was ~ .075 thick.
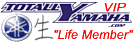

1nc 2000
Lifetime Member Tim
- Joined
- Feb 26, 2010
- Messages
- 3,049
- Location
- Marquette, MI
- Country
- USA
- Snowmobile
- Yamaha FX Nytro RTX SE
I always put the wedge in last and torque it so they is no extra side load on the bearings. Like to keep things free rolling.
Similar threads
- Replies
- 60
- Views
- 10K
-
This site uses cookies to help personalise content, tailor your experience and to keep you logged in if you register.
By continuing to use this site, you are consenting to our use of cookies.