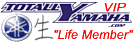

thor452
Because I can
- Joined
- Jan 5, 2010
- Messages
- 3,029
- Location
- Shawano,WI 54166
- Country
- USA
- Snowmobile
- 2012 Apex XTX 2017 Sidewinder LTX-LE
Is it safe to drill thru in the front corners of the alum under the engine as I started to drill thru i went thru the first layer of alum (the thin outer plate and is the only part i had to drill thru on the rear holes) but up front there is anouther layer of alum and i just want to be certian that it is okay to proceed before i finish the holes. 2012 apex XTX
vodoo child
Expert
- Joined
- Oct 29, 2005
- Messages
- 464
- Location
- Palmerton Pa.
- Country
- USA
- Snowmobile
- 2018 Sidewinder LTX/LE 50th
Wrap a good amount of duct tape around the drill bit 3/8th of an inch down from the tip. That will keep you from damaging anything when you break through the second layer.
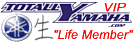

thor452
Because I can
- Joined
- Jan 5, 2010
- Messages
- 3,029
- Location
- Shawano,WI 54166
- Country
- USA
- Snowmobile
- 2012 Apex XTX 2017 Sidewinder LTX-LE
okay but there is an air gap up there correct?

Winderallday!
VIP Member
Yes there is clearance but not too much, this is why its a good idea to put a limiter on drill depth so when the drill breaks through it doesnt jam through and damage something.
A buddy just did this to his sled and punctured the coolant hose, then he drank beer while it drained all the coolant out!!
A buddy just did this to his sled and punctured the coolant hose, then he drank beer while it drained all the coolant out!!
4Fighter
TY 4 Stroke God
YIKES! That's not a good spot to do that to at all.Yes there is clearance but not too much, this is why its a good idea to put a limiter on drill depth so when the drill breaks through it doesnt jam through and damage something.
A buddy just did this to his sled and punctured the coolant hose, then he drank beer while it drained all the coolant out!!

Winderallday!
VIP Member
If its the Yamaha skid plate, the holes usually line up with 4 existing rivets in the bulkhead and you simply drill the heads off and tap the rivets out.
I usually just tap the rivet holes with a 6mm tap and install the plate, if they strip out eventually I will use the riv-nuts supplied. There is room for the riv-nuts in there, I'm estimating maybe 10mm or so clearance. The key is to control the depth you allow the drill to pass through the bulkhead, 3/8-1/2" of drill exposure is lots.
I use a random collar or a stack of washers over the drill to act as a hard stop so you cant go too deep and damage anything.
I usually just tap the rivet holes with a 6mm tap and install the plate, if they strip out eventually I will use the riv-nuts supplied. There is room for the riv-nuts in there, I'm estimating maybe 10mm or so clearance. The key is to control the depth you allow the drill to pass through the bulkhead, 3/8-1/2" of drill exposure is lots.
I use a random collar or a stack of washers over the drill to act as a hard stop so you cant go too deep and damage anything.
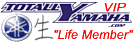

thor452
Because I can
- Joined
- Jan 5, 2010
- Messages
- 3,029
- Location
- Shawano,WI 54166
- Country
- USA
- Snowmobile
- 2012 Apex XTX 2017 Sidewinder LTX-LE
I am useing well nuts and the holes dont line up with the rivits i bought it used and it is off an older apex mountain but it fits. thanks for your reply I think i will put a collar on the drill bit then
Last edited:

CaptCaper
VIP Member
- Joined
- Jan 1, 2007
- Messages
- 2,183
- Location
- Northern N.H.
- Country
- USA
- Snowmobile
- 2016 RS Vector XTX 1.25 Lug wifes..2013 RS Vector LTX.. 2003 600 VMax Past Machines 3-2007 Attaks 1-2010 Vector LTX.. sorry no Stinkdoos or poo's cats.
On 3 different Apex's I've done skid plates I made the holes i the skid larger to make it easier to put on during installation but most important putting on after oil changes. I used SS fender washers and SS Hex head bolts so it's real easy to on and off. I used Rivnuts from McMasters and a homemade rivnut tool to secure them.
If you use the aluminum rivnuts from McMasters order the 25 pak part # ALA1-610-6.6, 4 or 5 bucks. the 6.6 means they are 6.6mm long which is better than the 4.4mm that they used to give
you in the kit with the skidplate. The 6.6 will not pull out. You have to use the 6.6 because of exactly the reason this thread was started, there are two layers of metal. Now the good news, if you are using these rivnuts, you can use the same bolt(Yamaha part # 90154-06009) that holds your lower body panel on. It is a flat and wide head that you tighten with a Philips to 27 inch lbs. torque. Used these after a rock ripped off the traditional bolt head. If you get your rivnuts somewhere else, check that they match up to whatever bolt you are using, I believe the body panel bolts are metric.
Last edited:
Similar threads
- Replies
- 21
- Views
- 6K
- Replies
- 12
- Views
- 2K
-
This site uses cookies to help personalise content, tailor your experience and to keep you logged in if you register.
By continuing to use this site, you are consenting to our use of cookies.