brendan.9
Pro
Is it true if you go on ice or hard pack and heat up your sliders, than go in deep snow and than let them cool off, which they say it hardens them to make them last longer is the true or not?
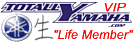

Super Sled
Lifetime Member
- Joined
- Feb 25, 2009
- Messages
- 3,631
- Location
- Riding on the North Shore, MN
- Country
- USA
- Snowmobile
- Summit X
I say it's true if you do it right. I've heard drive for 10 - 20 miles fast on hardpack/ trail and heat them up until really hot/melting. Then go into the powder and bury the skid or push snow over the skid and cool it for a while. If done right the melty sliders will harden really fast and become very, very smooth. Then the sliders will last much longer. The key is finding the exact right conditions to accomplish this with......
Mike
Mike
arteeex
TY 4 Stroke Master
It's baloney
fergdog93
Expert
Yeah, I call wives tail. Plastic melts at the same temp, no matter what. Its not like a wood or steel. Hyfaxs are mostly polly which melts at a lower temp than say a nylon, or ABS. The reason they make them out of the softer, lower melt temp polly is due to the fact that an ABS, or nylon material is harder which makes it brittle. The best way to get the most out of your hyfax is proper track adjustment, and/or an add-a-wheel kit. Or just ride the pow.
Swiss Sledder
TY 4 Stroke God
SnowTech described this process in a recent issue on how to get more wear out of you hyfax but I am skeptical. I agree with fergdog93 on the best way to get more out of hyfax on a Yamaha.

Yamaha Sled Talk Blog
VIP Member
I believe there is some truth to this...
"Because UHMW-PE is a semi-crystalline polymer, it must be sintered by either compression molding or ram extrusion. Annealing, prior to machining, helps remove the processing stresses caused by sintering. Finished machined parts can also be annealed, but such parts must be fixtured during the cooling process to allow for shrinkage during annealing. Rough machining should be done prior to stress-relieving so dimensional changes can be accommodated during final machining."
Hyfax sliders are not annealed during manufacturing, the heat / cooling cycle will shrink the plastic which becomes slightly denser and harder... it's all about shrinkage! ;-) cr
"Because UHMW-PE is a semi-crystalline polymer, it must be sintered by either compression molding or ram extrusion. Annealing, prior to machining, helps remove the processing stresses caused by sintering. Finished machined parts can also be annealed, but such parts must be fixtured during the cooling process to allow for shrinkage during annealing. Rough machining should be done prior to stress-relieving so dimensional changes can be accommodated during final machining."
Hyfax sliders are not annealed during manufacturing, the heat / cooling cycle will shrink the plastic which becomes slightly denser and harder... it's all about shrinkage! ;-) cr
woolyviper
TY 4 Stroke Master
- Joined
- Mar 24, 2006
- Messages
- 1,151
- Location
- hibbing,mn
- Country
- USA
- Snowmobile
- 2009 Yamaha Phazer RTX
it takes 5-10 cycles to properly do it - you can not get the slides hot enough to melt tho. my slides last longest when I put them on when there is lots of snow and can do the cooling process properly. I've had slides last 1500 miles and then only about 400, so it definitely makes a difference.
ScottyD
Expert
i know a guy that used to put a series of dimples in the bottom of the slider, the theory was to hold ice/snow to keep the slider cool, he would set up his drill press and set a depth to drill, then spend a few hrs putting holes in the sliders

ROCKERDAN
OCD Sledhead
- Joined
- Oct 8, 2005
- Messages
- 7,503
- Location
- Huntsville Ontario & Niagara NY
- Country
- Other
- Snowmobile
- '18 RTX 50th "Winder"
ScottyD said:i know a guy that used to put a series of dimples in the bottom of the slider, the theory was to hold ice/snow to keep the slider cool, he would set up his drill press and set a depth to drill, then spend a few hrs putting holes in the sliders
Ive been drilling out my sliders my whole life,just got done doing a new pair last week!....I have always felt it helped,i like every little edge i can get.
the best way to make a yammie slider last is by moving up to 135mm idlers with 2 bolts mounts,and then adding small wheel kits at bend,and mid areas where they wear hard.
with that setup,you will never wear out a set of sliders.
Dan
SledFreak
TY 4 Stroke God
- Joined
- Feb 7, 2005
- Messages
- 5,514
- Location
- Ontario. Canada
- Country
- Canada
- Snowmobile
- Current 2020 ThunderCat. - SOLD!
x2... Do the wheel kits... They only wear so much and then they stop. Sold my sled with 5000 miles on it and I only changed the sliders once and I shouldn't off. The wheels also help increase top end, especially the one at the bend. That's the important one.
Yamaha Sled Talk Blog said:I believe there is some truth to this...
"Because UHMW-PE is a semi-crystalline polymer, it must be sintered by either compression molding or ram extrusion. Annealing, prior to machining, helps remove the processing stresses caused by sintering. Finished machined parts can also be annealed, but such parts must be fixtured during the cooling process to allow for shrinkage during annealing. Rough machining should be done prior to stress-relieving so dimensional changes can be accommodated during final machining."
Hyfax sliders are not annealed during manufacturing, the heat / cooling cycle will shrink the plastic which becomes slightly denser and harder... it's all about shrinkage! ;-) cr
AHHHHHHH....What did he say I soory soooo sleepy
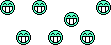
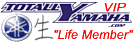

Riceburner
Lifetime Member
- Joined
- Apr 14, 2003
- Messages
- 1,760
- Location
- N.B. Canada eh
- Country
- Canada
- Snowmobile
- SideWinder LTX 50th
He said " TRUE " .
And backed up his opinion with facts and rationale.

And backed up his opinion with facts and rationale.

arteeex
TY 4 Stroke Master
For sliders UHMWPE is extruded, not sintered. Annealing the material would only remove internal stresses induced during the extrusion process or subsequent machining but not change its mechanical characteristics. Molecular cross-linking with radiation is used in medical applications (hip sockets) to improve wear resistance, but would be an expensive and unnecessary process for slides.
Below is the process for annealing UHMWPE and it does not include heat cycles on a sled rail.
To anneal UHMWPE, the material should be heated to 135 °C to 138 °C in an oven or a liquid bath of silicone oil or glycerin. The material must then be cooled down at a rate of 5 °C/h to at least 65 °C. Finally, the material should be wrapped in an insulating blanket for 24 hours to bring to room temperature.
Drilling holes or dimples in the sliders is just as like to hold sand and rocks as snow. Plus, this practice reduces the surface area of the slider and since surface area is a factor affecting wear response, this is unlikely to provide any real benefit.
Below is the process for annealing UHMWPE and it does not include heat cycles on a sled rail.
To anneal UHMWPE, the material should be heated to 135 °C to 138 °C in an oven or a liquid bath of silicone oil or glycerin. The material must then be cooled down at a rate of 5 °C/h to at least 65 °C. Finally, the material should be wrapped in an insulating blanket for 24 hours to bring to room temperature.
Drilling holes or dimples in the sliders is just as like to hold sand and rocks as snow. Plus, this practice reduces the surface area of the slider and since surface area is a factor affecting wear response, this is unlikely to provide any real benefit.
I have annealed, tried graphite, wide style and high preoformance. The only thing that works is lots of snow, lots of boagies and proper track tension.
When I pu the bender proaction mono upgrade in my 03 it did not have the inner rear wheels in it and I ate a set of graphites ever 100 miles. I tried everything. I added 2 inner and 2 outer wheels and the small savers in the front and was getting 1500 miles out of a stock set.
When I pu the bender proaction mono upgrade in my 03 it did not have the inner rear wheels in it and I ate a set of graphites ever 100 miles. I tried everything. I added 2 inner and 2 outer wheels and the small savers in the front and was getting 1500 miles out of a stock set.
arteeex
TY 4 Stroke Master
There sure is a lot of heartburn over $30 worth of plastic.
Similar threads
- Replies
- 42
- Views
- 5K
-
This site uses cookies to help personalise content, tailor your experience and to keep you logged in if you register.
By continuing to use this site, you are consenting to our use of cookies.