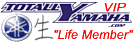

jonlafon1
Lifetime Member
- Joined
- Aug 18, 2014
- Messages
- 4,106
- Age
- 50
- Country
- USA
- Snowmobile
- 2022 Sidewinder LTX_SE
2024 Catalyst RXC
2017 Sidewinder LTX-SE. 11750 miles (SOLD)
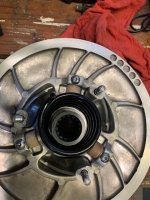
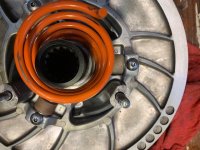
snowbeast
TY 4 Stroke God
- Joined
- Apr 13, 2003
- Messages
- 5,498
- Age
- 69
- Location
- E waterboro,maine
- Country
- USA
- Snowmobile
- 2015 apex xtx traded for a 2017 sidewinder L-tx-le
- yes
- YOUTUBE
- yes
Ya,i to have seen this. It sure would make me feel better if they were flat as well.

KnappAttack
24X ISR World Drag Racing Champion
- Joined
- Feb 19, 2004
- Messages
- 4,695
- Location
- Welch MN
- Country
- USA
- Snowmobile
- 2023 Sidewinder LTX-LE
2017 Sidewinder LTX-LE
Compress them in the clutch and have a look, it makes no difference. It cant sit flat with the tang on it. Compression spring can sit flat because they are ground and tapered ends, torsion can't do that with the tang.
Don't over think it.
Don't over think it.
It has to do with getting the required rates desired during the design.
If,..for example, ..spring design dictated that you need 4.5 coils for example, of a certain wire size and a certain free length, etc....all of that changes when you adjust pitch of the coils.
Some coils are "active" coils....some coils are not effecting compression when squared flat on the ends , etc.
the exact number of coils will dictate torsional forces, no matter if they are full active coils or not, but the compression side of things gets very different results on load pressure because of the amount of " active " or "inactive" coils are there.
If you need the exact number of coils for other reasons like torsion forces etc...and you say "square the end coils" on that say, 4.5 coil spring...then you do two things.
If you keep that same free length and square the ends then the PITCH of the 2.5 remaining center coils gets very steep. The very steep coils will increase the load pressure a lot as it compresses, and the stress shows up in design software. If you try to get 2.5 coils to do all the work it will "sack out" sooner if it is outside acceptable stress limits.
Basically you may not get the desired load from the design that you are looking for and the stress may increase.
As you can tell, often a shorter spring has less of that effect if it has even coil spacing. ( the same number of coils with a shorter free length will be like that.
You could easily square the ends if you could simply add more wire to the spring ( more coils and possibly different wire diameters, etc)...and probably still get what you want for load with the right combination when you design the spring. ..BUT, dont forget we have a limitation here....nobody wants coil bind right?...you cant just add more coils in this application.
The longest lasting springs are always the right combination of a larger wire available to get you the rates...and more coils is always less stress. Larger wires and more coils is way down on stress, and the rates dont change over time because less stress.....but if you are limited on closed pocket height like in this overdrive clutch, you need to factor in coil stacking total height ( coil bind)
Hope that helps
If,..for example, ..spring design dictated that you need 4.5 coils for example, of a certain wire size and a certain free length, etc....all of that changes when you adjust pitch of the coils.
Some coils are "active" coils....some coils are not effecting compression when squared flat on the ends , etc.
the exact number of coils will dictate torsional forces, no matter if they are full active coils or not, but the compression side of things gets very different results on load pressure because of the amount of " active " or "inactive" coils are there.
If you need the exact number of coils for other reasons like torsion forces etc...and you say "square the end coils" on that say, 4.5 coil spring...then you do two things.
If you keep that same free length and square the ends then the PITCH of the 2.5 remaining center coils gets very steep. The very steep coils will increase the load pressure a lot as it compresses, and the stress shows up in design software. If you try to get 2.5 coils to do all the work it will "sack out" sooner if it is outside acceptable stress limits.
Basically you may not get the desired load from the design that you are looking for and the stress may increase.
As you can tell, often a shorter spring has less of that effect if it has even coil spacing. ( the same number of coils with a shorter free length will be like that.
You could easily square the ends if you could simply add more wire to the spring ( more coils and possibly different wire diameters, etc)...and probably still get what you want for load with the right combination when you design the spring. ..BUT, dont forget we have a limitation here....nobody wants coil bind right?...you cant just add more coils in this application.
The longest lasting springs are always the right combination of a larger wire available to get you the rates...and more coils is always less stress. Larger wires and more coils is way down on stress, and the rates dont change over time because less stress.....but if you are limited on closed pocket height like in this overdrive clutch, you need to factor in coil stacking total height ( coil bind)
Hope that helps
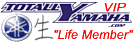

jonlafon1
Lifetime Member
- Joined
- Aug 18, 2014
- Messages
- 4,106
- Age
- 50
- Country
- USA
- Snowmobile
- 2022 Sidewinder LTX_SE
2024 Catalyst RXC
2017 Sidewinder LTX-SE. 11750 miles (SOLD)
Thank You. This helps my brain! Maybe overthinking it some. But I was hoping you might give some insight.It has to do with getting the required rates desired during the design.
If,..for example, ..spring design dictated that you need 4.5 coils for example, of a certain wire size and a certain free length, etc....all of that changes when you adjust pitch of the coils.
Some coils are "active" coils....some coils are not effecting compression when squared flat on the ends , etc.
the exact number of coils will dictate torsional forces, no matter if they are full active coils or not, but the compression side of things gets very different results on load pressure because of the amount of " active " or "inactive" coils are there.
If you need the exact number of coils for other reasons like torsion forces etc...and you say "square the end coils" on that say, 4.5 coil spring...then you do two things.
If you keep that same free length and square the ends then the PITCH of the 2.5 remaining center coils gets very steep. The very steep coils will increase the load pressure a lot as it compresses, and the stress shows up in design software. If you try to get 2.5 coils to do all the work it will "sack out" sooner if it is outside acceptable stress limits.
Basically you may not get the desired load from the design that you are looking for and the stress may increase.
As you can tell, often a shorter spring has less of that effect if it has even coil spacing. ( the same number of coils with a shorter free length will be like that.
You could easily square the ends if you could simply add more wire to the spring ( more coils and possibly different wire diameters, etc)...and probably still get what you want for load with the right combination when you design the spring. ..BUT, dont forget we have a limitation here....nobody wants coil bind right?...you cant just add more coils in this application.
The longest lasting springs are always the right combination of a larger wire available to get you the rates...and more coils is always less stress. Larger wires and more coils is way down on stress, and the rates dont change over time because less stress.....but if you are limited on closed pocket height like in this overdrive clutch, you need to factor in coil stacking total height ( coil bind)
Hope that helps
You bet.
basically, You could do ,for example, what you desire and make that spring with squared ends, ...but you would have to shorten it to get the stress down on the active center coils. This would result in less compression on load one and load two of that spring, which may not be what you want. You may want that higher initial compression that it has now.
basically, You could do ,for example, what you desire and make that spring with squared ends, ...but you would have to shorten it to get the stress down on the active center coils. This would result in less compression on load one and load two of that spring, which may not be what you want. You may want that higher initial compression that it has now.