
74Nitro
VIP Member
- Joined
- Feb 18, 2013
- Messages
- 5,333
- Age
- 52
- Location
- Dublin Ontario
- Country
- Canada
- Snowmobile
- 2019 Sidewinder LTX
I made the mistake of putting 4 studs per bar(with nylon double backers) in the center of my track on my 19 LTX that has the SRX 1 inch ripsaw(I switched it). I thought my track was more than tight enough, but when doing top speed pulls I could feel something wrong in the running boards.
Turns out, the studs were hitting the ribs on the front heat exchanger! I was surprised given how much clearance exists up there. Amazing how much the track shoots ahead of the drivers.
Turns out, the studs were hitting the ribs on the front heat exchanger! I was surprised given how much clearance exists up there. Amazing how much the track shoots ahead of the drivers.
Your dreaming in a perfect world as if the forces on the track are even across the board.
Uneven track tension, track changing directions around the wheels, studs and stretch all play a part in the force on the track.
Dont forget tracks balloon up in the middle not just in a circle.
Run a 2 ply track on a sidewinder.
Not dreaming, I understand what the forces are. Yes, I am discounting uneven or unbalanced weight distribution, track alignment, sticking or blown bearings, uneven or damaged wheels in any part of the drive train because all of those things can make the problem worse but they are not the root of the problem and mitigation is similar. Again, none of that is or was my point.
The rest of this is a general reply to the thread, not anything you said.
Maybe I am caught up in the descriptions of ballooning because many (ty4stroke, hcs, facebook groups, etc) most commonly refer to the effect as coming from centrifugal force. There is no centrifugal force expanding the track. That is not the way it works. I realize it is somewhat semantics really as saying 'centrifugal' is really just a convenient description of an observable phenomenon that everyone understands from a visual perspective in the same way calling it ballooning is. It is shorthand for 'force moving outward'. Track expansion or deviation from its linear path is neither the result of centrifugal force or anything that should be described as ballooning (even though I hypocritically do so), which has connotations of equal outward expansion as in filling a balloon full of air, but more importantly using those terms is a bit misleading.
I use 'ballooning' simply because it is a commonly accepted description, not because it is technically correct (it isn't) in any kind of analytical or literal sense.
Its not centrifugal force because there is no central axis, to have centrifugal force you have to have a circle. There is no circle. Centrifugal force can only be measured from the perspective of the central axis. Since the track is wrapped around a quasi parallelogram there is no central frame of reference. That may seem pedantic but trust me it isn't and if you discount centrifugal force source (which you can do little about) it forces you to look for the real source of track deviation which is angular momentum and tension with a side helping of track elasticity.
Here is a reasonable visual example.
What is happening at the level of the track is the same as it is in the video example. You have a driving force, the driver, there is tension in the track, as the track makes its way around the idlers, linear momentum gets converted into angular momentum and back to linear. In essence, your track is being 'thrown' in a direction as it exits each wheel in the same way that swinging anything around and letting it go sends the object off in one direction. What changes this from just headed thataway to an arc which everyone describes as ballooning is the fact that the driver is still providing tension, modifying the vector of travel by pulling into an arc and changing the direction of the track. This all works out because the driver is constantly pulling in the same way that the wheels in the string example are constantly 'throwing' string out. The mitigating force to the track simply flying off is tension (and its a loop) which I have attempted to describe. The balance between tension and the angular momentum is what causes the deviation of the track from its linear path. Its important to understand the difference since centrifugal forces imply a force pushing equally across the tracks surface outwards. Its not that. The other issue is track elasticity and resulting deformation but even it is a byproduct of the first two. My only point in my original comment is that ballooning as described and visualized by the track on the stand (and the string in the video) is very, very different than track deviation from its linear path while under load, none of this is speculation or dreaming, its physics. The difference between being in free space and being on the ground driving the sled forward is tension as I described it. Without tension you have a much different problem. And with tension as a major component and understanding that tension is the difference allows you to approach the real problem which is 'what happens when the tension changes'. This is where all of the problems @KnappAttack describe come from. Like the string in the video, the track will reach a stability at any given speed and its only when stability is disrupted that all kinds of nasty things take place as waves of force travel through the track. These waves of force are a direct result of changes in tension and a side dish of track elasticity.
And if you look at it that way you can start to find ways to mitigate the problem. One example is that the distance between any two wheels where the track is in free space (free to resonate) defines the period of any wave that can travel through the track due to the natural dampening applied by the second or next wheel imparting another change in direction. Yes, a wave could blow right by the second idler if the wave is big enough but it won't last long. What if (hypothetical to make a point) there were 3,4,or 5 smaller idlers instead of one big one at the rear. While the track is making the same turn and ultimately ends up in the same direction each smaller idler is contributing less and the distance between them limits the period (less free space between them) and with that you have a natural dampening of amplitude. Will it work, I don't know but at least its is a meaningful experiment. Ultimately you still have to deal with massive changes in tension, one example is that the track breaks free under power (spins) then matches speed again when traction is regained, you have residual momentum flowing through the track as it changes velocity and this creates a lack of tension which in turn creates the wave in the track, nastiness ensues. The chain guide in the chaincase is an example. The distance between the gears defines the period of any chain deviation, slackness in the chain defines amplitude (ignoring chain bind etc) the tension mitigates amplitude, in order to eliminate chain skip and to deal with the inevitable chain stretch we add the guide/skate/bearing which acts as a dampener which is just another way of saying adding tension potential. Of course I could be wrong, but I like my explanation better than writing it off to some mysterious unjustifiable force and if I had to solve the issue, this is where I would start.
In any case, yes, run a 2-ply is the only thing that makes sense and run the track tight.
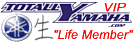

1nc 2000
Lifetime Member Tim
- Joined
- Feb 26, 2010
- Messages
- 3,173
- Location
- Marquette, MI
- Country
- USA
- Snowmobile
- Yamaha FX Nytro RTX SE

74Nitro
VIP Member
- Joined
- Feb 18, 2013
- Messages
- 5,333
- Age
- 52
- Location
- Dublin Ontario
- Country
- Canada
- Snowmobile
- 2019 Sidewinder LTX
Can you put that in one tweet?Not dreaming, I understand what the forces are. Yes, I am discounting uneven or unbalanced weight distribution, track alignment, sticking or blown bearings, uneven or damaged wheels in any part of the drive train because all of those things can make the problem worse but they are not the root of the problem and mitigation is similar. Again, none of that is or was my point.
The rest of this is a general reply to the thread, not anything you said.
Maybe I am caught up in the descriptions of ballooning because many (ty4stroke, hcs, facebook groups, etc) most commonly refer to the effect as coming from centrifugal force. There is no centrifugal force expanding the track. That is not the way it works. I realize it is somewhat semantics really as saying 'centrifugal' is really just a convenient description of an observable phenomenon that everyone understands from a visual perspective in the same way calling it ballooning is. It is shorthand for 'force moving outward'. Track expansion or deviation from its linear path is neither the result of centrifugal force or anything that should be described as ballooning (even though I hypocritically do so), which has connotations of equal outward expansion as in filling a balloon full of air, but more importantly using those terms is a bit misleading.
I use 'ballooning' simply because it is a commonly accepted description, not because it is technically correct (it isn't) in any kind of analytical or literal sense.
Its not centrifugal force because there is no central axis, to have centrifugal force you have to have a circle. There is no circle. Centrifugal force can only be measured from the perspective of the central axis. Since the track is wrapped around a quasi parallelogram there is no central frame of reference. That may seem pedantic but trust me it isn't and if you discount centrifugal force source (which you can do little about) it forces you to look for the real source of track deviation which is angular momentum and tension with a side helping of track elasticity.
Here is a reasonable visual example.
What is happening at the level of the track is the same as it is in the video example. You have a driving force, the driver, there is tension in the track, as the track makes its way around the idlers, linear momentum gets converted into angular momentum and back to linear. In essence, your track is being 'thrown' in a direction as it exits each wheel in the same way that swinging anything around and letting it go sends the object off in one direction. What changes this from just headed thataway to an arc which everyone describes as ballooning is the fact that the driver is still providing tension, modifying the vector of travel by pulling into an arc and changing the direction of the track. This all works out because the driver is constantly pulling in the same way that the wheels in the string example are constantly 'throwing' string out. The mitigating force to the track simply flying off is tension (and its a loop) which I have attempted to describe. The balance between tension and the angular momentum is what causes the deviation of the track from its linear path. Its important to understand the difference since centrifugal forces imply a force pushing equally across the tracks surface outwards. Its not that. The other issue is track elasticity and resulting deformation but even it is a byproduct of the first two. My only point in my original comment is that ballooning as described and visualized by the track on the stand (and the string in the video) is very, very different than track deviation from its linear path while under load, none of this is speculation or dreaming, its physics. The difference between being in free space and being on the ground driving the sled forward is tension as I described it. Without tension you have a much different problem. And with tension as a major component and understanding that tension is the difference allows you to approach the real problem which is 'what happens when the tension changes'. This is where all of the problems @KnappAttack describe come from. Like the string in the video, the track will reach a stability at any given speed and its only when stability is disrupted that all kinds of nasty things take place as waves of force travel through the track. These waves of force are a direct result of changes in tension and a side dish of track elasticity.
And if you look at it that way you can start to find ways to mitigate the problem. One example is that the distance between any two wheels where the track is in free space (free to resonate) defines the period of any wave that can travel through the track due to the natural dampening applied by the second or next wheel imparting another change in direction. Yes, a wave could blow right by the second idler if the wave is big enough but it won't last long. What if (hypothetical to make a point) there were 3,4,or 5 smaller idlers instead of one big one at the rear. While the track is making the same turn and ultimately ends up in the same direction each smaller idler is contributing less and the distance between them limits the period (less free space between them) and with that you have a natural dampening of amplitude. Will it work, I don't know but at least its is a meaningful experiment. Ultimately you still have to deal with massive changes in tension, one example is that the track breaks free under power (spins) then matches speed again when traction is regained, you have residual momentum flowing through the track as it changes velocity and this creates a lack of tension which in turn creates the wave in the track, nastiness ensues. The chain guide in the chaincase is an example. The distance between the gears defines the period of any chain deviation, slackness in the chain defines amplitude (ignoring chain bind etc) the tension mitigates amplitude, in order to eliminate chain skip and to deal with the inevitable chain stretch we add the guide/skate/bearing which acts as a dampener which is just another way of saying adding tension potential. Of course I could be wrong, but I like my explanation better than writing it off to some mysterious unjustifiable force and if I had to solve the issue, this is where I would start.
In any case, yes, run a 2-ply is the only thing that makes sense and run the track tight.
THEPASMAN
Expert
- Joined
- Mar 25, 2019
- Messages
- 450
- Age
- 57
- Location
- The Pas Manitoba
- Country
- Canada
- Snowmobile
- 2017 Sidewinder LTX LE
I can’t believe I read that whole thingNot dreaming, I understand what the forces are. Yes, I am discounting uneven or unbalanced weight distribution, track alignment, sticking or blown bearings, uneven or damaged wheels in any part of the drive train because all of those things can make the problem worse but they are not the root of the problem and mitigation is similar. Again, none of that is or was my point.
The rest of this is a general reply to the thread, not anything you said.
Maybe I am caught up in the descriptions of ballooning because many (ty4stroke, hcs, facebook groups, etc) most commonly refer to the effect as coming from centrifugal force. There is no centrifugal force expanding the track. That is not the way it works. I realize it is somewhat semantics really as saying 'centrifugal' is really just a convenient description of an observable phenomenon that everyone understands from a visual perspective in the same way calling it ballooning is. It is shorthand for 'force moving outward'. Track expansion or deviation from its linear path is neither the result of centrifugal force or anything that should be described as ballooning (even though I hypocritically do so), which has connotations of equal outward expansion as in filling a balloon full of air, but more importantly using those terms is a bit misleading.
I use 'ballooning' simply because it is a commonly accepted description, not because it is technically correct (it isn't) in any kind of analytical or literal sense.
Its not centrifugal force because there is no central axis, to have centrifugal force you have to have a circle. There is no circle. Centrifugal force can only be measured from the perspective of the central axis. Since the track is wrapped around a quasi parallelogram there is no central frame of reference. That may seem pedantic but trust me it isn't and if you discount centrifugal force source (which you can do little about) it forces you to look for the real source of track deviation which is angular momentum and tension with a side helping of track elasticity.
Here is a reasonable visual example.
What is happening at the level of the track is the same as it is in the video example. You have a driving force, the driver, there is tension in the track, as the track makes its way around the idlers, linear momentum gets converted into angular momentum and back to linear. In essence, your track is being 'thrown' in a direction as it exits each wheel in the same way that swinging anything around and letting it go sends the object off in one direction. What changes this from just headed thataway to an arc which everyone describes as ballooning is the fact that the driver is still providing tension, modifying the vector of travel by pulling into an arc and changing the direction of the track. This all works out because the driver is constantly pulling in the same way that the wheels in the string example are constantly 'throwing' string out. The mitigating force to the track simply flying off is tension (and its a loop) which I have attempted to describe. The balance between tension and the angular momentum is what causes the deviation of the track from its linear path. Its important to understand the difference since centrifugal forces imply a force pushing equally across the tracks surface outwards. Its not that. The other issue is track elasticity and resulting deformation but even it is a byproduct of the first two. My only point in my original comment is that ballooning as described and visualized by the track on the stand (and the string in the video) is very, very different than track deviation from its linear path while under load, none of this is speculation or dreaming, its physics. The difference between being in free space and being on the ground driving the sled forward is tension as I described it. Without tension you have a much different problem. And with tension as a major component and understanding that tension is the difference allows you to approach the real problem which is 'what happens when the tension changes'. This is where all of the problems @KnappAttack describe come from. Like the string in the video, the track will reach a stability at any given speed and its only when stability is disrupted that all kinds of nasty things take place as waves of force travel through the track. These waves of force are a direct result of changes in tension and a side dish of track elasticity.
And if you look at it that way you can start to find ways to mitigate the problem. One example is that the distance between any two wheels where the track is in free space (free to resonate) defines the period of any wave that can travel through the track due to the natural dampening applied by the second or next wheel imparting another change in direction. Yes, a wave could blow right by the second idler if the wave is big enough but it won't last long. What if (hypothetical to make a point) there were 3,4,or 5 smaller idlers instead of one big one at the rear. While the track is making the same turn and ultimately ends up in the same direction each smaller idler is contributing less and the distance between them limits the period (less free space between them) and with that you have a natural dampening of amplitude. Will it work, I don't know but at least its is a meaningful experiment. Ultimately you still have to deal with massive changes in tension, one example is that the track breaks free under power (spins) then matches speed again when traction is regained, you have residual momentum flowing through the track as it changes velocity and this creates a lack of tension which in turn creates the wave in the track, nastiness ensues. The chain guide in the chaincase is an example. The distance between the gears defines the period of any chain deviation, slackness in the chain defines amplitude (ignoring chain bind etc) the tension mitigates amplitude, in order to eliminate chain skip and to deal with the inevitable chain stretch we add the guide/skate/bearing which acts as a dampener which is just another way of saying adding tension potential. Of course I could be wrong, but I like my explanation better than writing it off to some mysterious unjustifiable force and if I had to solve the issue, this is where I would start.
In any case, yes, run a 2-ply is the only thing that makes sense and run the track tight.

RobX-1
VIP Member
- Joined
- Apr 13, 2003
- Messages
- 2,229
- Location
- Coldwater, OH
- Country
- USA
- Snowmobile
- 18 50th Apex XT-X, 08 40th Apex LTX GT, 08 40th Nytro RTX, & 03 RX-1
Well, if the goal was to write a 1,000 word rebuttal, well done sir!
Jvji24
Pro
?!!?!
Last edited:
Thanks for all the feedback. Ya definitely a lot to consider safety wise and with potential cost of damages. Sadly the least of my worries as both rails split on the trail yesterday. I had to use reverse several times to get back to the main trail (only way it would move). Luckily wasn't to far cause like you all know these sidewinders get hot fast. Back to the topic I am only interested in acceleration so if change ratios or do a driver change I will let off throttle early. Love this site.
Similar threads
- Replies
- 7
- Views
- 2K
- Replies
- 14
- Views
- 1K
- Replies
- 91
- Views
- 44K