powershot1
Extreme
has anybody check to see if the idle air control valve is leaking boost pressure back to atmosphere being that it vented to atmosphere.does anybody out there use a check valve on this allowing air only to come in.to stop boost pressure from leaking out the idle air control vent.
mbarryracing
TY 4 Stroke God
- Joined
- Aug 31, 2007
- Messages
- 1,923
- Age
- 52
- Location
- Springville NY
- Country
- USA
- Snowmobile
- 2006 Yamaha Attak Turbo
2015 SR Viper RTX-DX
1996 Vmax 600XT
powershot1
Extreme
I just went back and read the MPI install manual for the blower and they are venting to atmosphere
mbarryracing
TY 4 Stroke God
- Joined
- Aug 31, 2007
- Messages
- 1,923
- Age
- 52
- Location
- Springville NY
- Country
- USA
- Snowmobile
- 2006 Yamaha Attak Turbo
2015 SR Viper RTX-DX
1996 Vmax 600XT
Sorry to hear that..
I suppose dont pay any attention to it since the trend seems to be to make as many intentional boost leaks as possible with the SCs, BOVs that open at part throttle, all to reduce boost and improve fuel mileage.
Probably why i dont own one.
I suppose dont pay any attention to it since the trend seems to be to make as many intentional boost leaks as possible with the SCs, BOVs that open at part throttle, all to reduce boost and improve fuel mileage.
Probably why i dont own one.
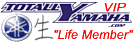

nate007
Lifetime Member
- Joined
- Dec 25, 2006
- Messages
- 2,770
- Location
- Iowa City, Iowa
- Country
- USA
- Snowmobile
- 1. '06 Apex -twin screw
2. '04 Redline Revolt 800
3. '09 Nytro XTX - twin screw
On other applications that use an idle set up like this, a check valve will do the trick as well. For most centrifugal blowers and turbos that blow through the throttle bodies, you can run it into the pressure side, but depending on your boost levels, a couple things could happen.
1. When drawing from the atmosphere, rapid boost level changes can actually force the idle valve open causing a fuel/air mixture out of the hose. This could ultimately wear out your idle system causing idle and driveability issues that are pretty hard to diagnose.
2. Depending on your system setup, piping it into the pressure side of your boost system can also cause it's own issues. This however is not very likely, but.. If you are running a basic piggy back system, and have tuned your sled from a gauge only and the valve was closed correctly at operating temps, boost pressure could force it open (or cause it to stick) resulting in a lean condition. It's far easier for the boost to act on the larger intake tube than on the 4 individual smaller tubes, so there's a chance for some "authority" there as well. If you have a WB feedback system like the auto tune style, your system can compensate better for it if necessary.
The theory is also there that boost on both sides of the idle valve will let it equalize as well, but it could still cause some hickups.
It's more likely on the Nytro motors to have issues with it since it's a stepper motor system, and the EBRS adds it's own set of issues. The motor can usually hold boost pressure if it's not actually operating, but once it's moving, boost pressure going the wrong way through it can easilly force it open, causing leaks.
Most issues you'll see with it though will be in the transition phase, from decel or steady cruise to WOT, or WOT to fully closed throttle. The idle system wasn't designed for a boosted system.
My personal prefference is a check valve, but you'll have to experimant with what works best for you. It's a great question though, as I think this is a largely overlooked topic. I'd bet there's a lot of little hiccups caused by this that many people stuggle with.
1. When drawing from the atmosphere, rapid boost level changes can actually force the idle valve open causing a fuel/air mixture out of the hose. This could ultimately wear out your idle system causing idle and driveability issues that are pretty hard to diagnose.
2. Depending on your system setup, piping it into the pressure side of your boost system can also cause it's own issues. This however is not very likely, but.. If you are running a basic piggy back system, and have tuned your sled from a gauge only and the valve was closed correctly at operating temps, boost pressure could force it open (or cause it to stick) resulting in a lean condition. It's far easier for the boost to act on the larger intake tube than on the 4 individual smaller tubes, so there's a chance for some "authority" there as well. If you have a WB feedback system like the auto tune style, your system can compensate better for it if necessary.
The theory is also there that boost on both sides of the idle valve will let it equalize as well, but it could still cause some hickups.
It's more likely on the Nytro motors to have issues with it since it's a stepper motor system, and the EBRS adds it's own set of issues. The motor can usually hold boost pressure if it's not actually operating, but once it's moving, boost pressure going the wrong way through it can easilly force it open, causing leaks.
Most issues you'll see with it though will be in the transition phase, from decel or steady cruise to WOT, or WOT to fully closed throttle. The idle system wasn't designed for a boosted system.
My personal prefference is a check valve, but you'll have to experimant with what works best for you. It's a great question though, as I think this is a largely overlooked topic. I'd bet there's a lot of little hiccups caused by this that many people stuggle with.

blown apex
VIP Member
iac valve apex
ok so on my supercharged apex at 12 psi how much boost am i loosing
and were do you get the check valve
ok so on my supercharged apex at 12 psi how much boost am i loosing
and were do you get the check valve
MRFUSION
Pro
- Joined
- May 19, 2008
- Messages
- 162
- Location
- Peace River Alberta
- Country
- Canada
- Snowmobile
- 2011 Custom Built Nypex
2008 Custom Union Bay 980 MM Chassis
I made my life easy and just took the valve assy off. Works great.
Shad
Shad
powershot1
Extreme
If you removed the IAC valve how do you control idle speed. If you crack the air doors open does that work Ok on a efi system.
The IAC valve also has stall saver capability.
that's one of the good things about EFI it has good drivability and the IAC is one of the reasons.
The IAC valve also has stall saver capability.
that's one of the good things about EFI it has good drivability and the IAC is one of the reasons.
MRFUSION
Pro
- Joined
- May 19, 2008
- Messages
- 162
- Location
- Peace River Alberta
- Country
- Canada
- Snowmobile
- 2011 Custom Built Nypex
2008 Custom Union Bay 980 MM Chassis
Works just fine, the Idle valve is essentially out of play once the unit is at operation temp. I just nippled off the barbs at each throttle body and adjust the idle with the small adjustable allen stop screw between the throttle bodies. Ive been running it on my Nypex like that for 3 years now. Zero change in quality running, only issue I had was one reallllly cold morning I had to keep it running at first start up with the throttle for about a minute then it was good. I just didnt have the real estate for my stand up intercooler. Eliminates the problems. Shad
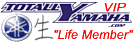

nate007
Lifetime Member
- Joined
- Dec 25, 2006
- Messages
- 2,770
- Location
- Iowa City, Iowa
- Country
- USA
- Snowmobile
- 1. '06 Apex -twin screw
2. '04 Redline Revolt 800
3. '09 Nytro XTX - twin screw
That's another way to do it, but I would guess that there's not a lot of people that would want to hassle with the cold start issues unless their sleds are never outside in the cold..
I wouldn't assume that you are automatically losing boost by venting to the atmosphere, just be aware that the valve could be the culprit if you start having low rpm issues.
I wouldn't assume that you are automatically losing boost by venting to the atmosphere, just be aware that the valve could be the culprit if you start having low rpm issues.
powershot1
Extreme
Will I found using two brake booster check valves on a tee supplied enough air to get a clean idle.
noted the check valves I used has 1/2 inlet fitting not 3/8 the 3/8 inlet did not work.
starved the engine for air at idle.
I will put a post out after driving the Machine and let you know if I makes higher than 8 psi iam running 24 top/24 bottom combo.which will normally yield 8 psi.I will also report back on the Driveability.
noted the check valves I used has 1/2 inlet fitting not 3/8 the 3/8 inlet did not work.
starved the engine for air at idle.
I will put a post out after driving the Machine and let you know if I makes higher than 8 psi iam running 24 top/24 bottom combo.which will normally yield 8 psi.I will also report back on the Driveability.
Accentstripe1
Extreme
Iac valve
This is a very interesting topic. I'm running a impulse turbo with their standalone system and I too have my iac vented to the atmosphere. I have the sensor plugged in and zip tied out of the way. Please let us know your findings when you get out for a rip. Thanks
This is a very interesting topic. I'm running a impulse turbo with their standalone system and I too have my iac vented to the atmosphere. I have the sensor plugged in and zip tied out of the way. Please let us know your findings when you get out for a rip. Thanks
powershot1
Extreme
I went from 8.1 to 8.7 psi using a check valve on the IAC vent. Now I have it hooked to the intercooler. Will give it a try this weekend.

87gtNOS
VIP Member
- Joined
- Nov 30, 2005
- Messages
- 1,892
- Age
- 50
- Location
- Toronto
- Country
- Canada
- Snowmobile
- 12 Apex XTX MCX powered
so I have that 90 deg elbow just turned down open to the atmosphere...
and I assume the check valve is preventing any air from escaping the IAC?
and yes, I am aware I prolly wouldn't gain anything!! LOL
and I assume the check valve is preventing any air from escaping the IAC?
and yes, I am aware I prolly wouldn't gain anything!! LOL
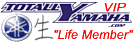

nate007
Lifetime Member
- Joined
- Dec 25, 2006
- Messages
- 2,770
- Location
- Iowa City, Iowa
- Country
- USA
- Snowmobile
- 1. '06 Apex -twin screw
2. '04 Redline Revolt 800
3. '09 Nytro XTX - twin screw
I think realisticaly it's still a small ammount of air purging out if it is, and if your afr's are ok, it's not likely something to lose a ton of sleep over, but I know how picky we all can be! lol
The brake booster check valve idea is a good one, and those are definitely pretty air tight, but what about just using a pcv valve?
Other than a possibility of wear in the valve from being forced open, I can see the issue being more prevalant on the Nytro's, since they have an iac motor and not a temp valve.
Has anyone ever tested to see if there is air blowing back? I wonder if taping a whistle to the hose or something would work?
I would do it on my sleds, but I'm set up totally different than other boosted systems, and finishing some testing on a few other things,
I don't really want to mess with it, or have time to at this point. I would like to see what is happening though if someone has an idea to try and see if there is actually air coming back out.
The brake booster check valve idea is a good one, and those are definitely pretty air tight, but what about just using a pcv valve?
Other than a possibility of wear in the valve from being forced open, I can see the issue being more prevalant on the Nytro's, since they have an iac motor and not a temp valve.
Has anyone ever tested to see if there is air blowing back? I wonder if taping a whistle to the hose or something would work?
I would do it on my sleds, but I'm set up totally different than other boosted systems, and finishing some testing on a few other things,

Similar threads
- Replies
- 210
- Views
- 45K
- Replies
- 17
- Views
- 4K
-
This site uses cookies to help personalise content, tailor your experience and to keep you logged in if you register.
By continuing to use this site, you are consenting to our use of cookies.