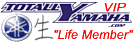

1nc 2000
Lifetime Member Tim
- Joined
- Feb 26, 2010
- Messages
- 3,050
- Location
- Marquette, MI
- Country
- USA
- Snowmobile
- Yamaha FX Nytro RTX SE
The sidewinder also has a vent hose off the valve cover to the airbox. That hose i just leave open and hanging in the engine bay since the air box is removed and a k&n intake filter is used.
Oh right I forgot about the valve cover hose. In this case I’m wondering why I can’t vent the apex valve cover, then plug the 2 vents on the crankcaseThe sidewinder also has a vent hose off the valve cover to the airbox. That hose i just leave open and hanging in the engine bay since the air box is removed and a k&n intake filter is used.

kinger
VIP Member
1.5OD is to small of a header. Check out my latest vid and shows you what my impulse header measures.
deng, already ordered my 90 bends.1.5OD is to small of a header. Check out my latest vid and shows you what my impulse header measures.
Will move up to 1.75 inch 0.65. that gives a 1.62 wall.
Added bellmouths to the plenum
just a test fit of the printed boots
Turbo placement. what do you prefer? With the compressor backwards I was going to route my intake into my cabin, under the hood.
With the compressor forwards, I am thinking of adding the nytro oil tank to the front above the engine, then I will remove the stock oil tank which will alllow for more room for the quiet muffler at the back.
View attachment 169186
Added bellmouths to the plenum
View attachment 169187
just a test fit of the printed boots
View attachment 169188
Turbo placement. what do you prefer? With the compressor backwards I was going to route my intake into my cabin, under the hood.
With the compressor forwards, I am thinking of adding the nytro oil tank to the front above the engine, then I will remove the stock oil tank which will alllow for more room for the quiet muffler at the back.
View attachment 169189
View attachment 169190
Curious.. Why add extruded flutes (bellmouths) for a pressure vessel? This is a question, not a criticism. Intuitively (meaning I have no justification other than experience, and have not added CFD to F360 to model it myself), flutes are nominally better for low pressure/vacuum systems or where the flute itself acts to create high(er) pressure within the intake tube when more pressure is desired than is statically available (like a cold air intake horn acting to create ram-air like effects). If the flutes are there to create more laminar flow then you probably want to backfill the entire area behind the flutes or connect them together to fill in the gaps as having pressurized air back there may cause turbulent flows during pressure gradients. Better to think of the intakes as drains for the high pressure vessel. Again, this is intuition talking and my experience comes from experience with jet/V-drive boats and drones (winged) not intake systems.
Curious.. Why add extruded flutes (bellmouths) for a pressure vessel? This is a question, not a criticism. Intuitively (meaning I have no justification other than experience, and have not added CFD to F360 to model it myself), flutes are nominally better for low pressure/vacuum systems or where the flute itself acts to create high(er) pressure within the intake tube when more pressure is desired than is statically available (like a cold air intake horn acting to create ram-air like effects). If the flutes are there to create more laminar flow then you probably want to backfill the entire area behind the flutes or connect them together to fill in the gaps as having pressurized air back there may cause turbulent flows during pressure gradients. Better to think of the intakes as drains for the high pressure vessel. Again, this is intuition talking and my experience comes from experience with jet/V-drive boats and drones (winged) not intake systems.
No criticism taken... It would appear your knowledge is much more vast than mine regarding this. What do you reccomend? Remove them completely? I had been told extending them into the plenum would help alleviate turbulence by keeping them off the back wall, but what do i know? I also noticed that the TD intercooler ran bellmouths inside their plenum, so I was taking from that design.
Any other changes i should make to this plenum other than making the internal volume as large as possible?
No criticism taken... It would appear your knowledge is much more vast than mine regarding this. What do you reccomend? Remove them completely? I had been told extending them into the plenum would help alleviate turbulence by keeping them off the back wall, but what do i know? I also noticed that the TD intercooler ran bellmouths inside their plenum, so I was taking from that design.
Any other changes i should make to this plenum other than making the internal volume as large as possible?
As I said, I don't have specific experience with this but it seems to me that the intake itself should have as much of the air contained within the intake tubes as possible. The longer the intake runners, the more laminar the flow. I think too large a volume in the manifold itself will create pumping effects especially at low rpm. Keeping the volume tight and making the intake runners longer would allow air to straighten out and move more efficiently. Its always a tradeoff between the ideal and the amount of space you have to work with. For your design, I would move the flutes to the bottom so that they are flush with the bottom/back of the intake, then where your prototype stops, I would probably limit the total volume to that space, meaning I would eliminate the big transition you have from the tube coming in and where the prototype ends today. Think of it as an exhaust header in reverse. You want some transition from the individual header tubes to the main tube that carries the combined volume of air because you want velocity to be as high and as controlled as possible until you hit the exhaust can where the gasses can expand (and slow).
What you consistently see in high performance manifolds is long equal length runners with the minimum number of bends, and a short transition between the manifold and the rest of the system.
I cannot think of a reason to make the internal volume of the manifold larger than necessary and taking a quick look at what has been done in the automotive world, I don't see any examples of large manifold volumes in a pressurized system. You see large volume manifolds where the intake is also the air source (ambient pressure) and there is a filter involved.
Looking at your F-360 shaded model, you could eliminate the rounded parts from the main tube to the intakes making the profile shorter, triangular, and more direct.
Are you printing this yourself? What material? I tried printing myself and some of those parts have lasted, some have not. I had to go back on those failed parts and redesign them understanding the weakness of the materials I was working with (all the standard ABS/PLA/etc). I always wanted to get my original designs (sans extra thickness and supports) printed by a third party in better materials but never got around to it.
Are you printing this yourself? What material? I tried printing myself and some of those parts have lasted, some have not. I had to go back on those failed parts and redesign them understanding the weakness of the materials I was working with (all the standard ABS/PLA/etc). I always wanted to get my original designs (sans extra thickness and supports) printed by a third party in better materials but never got around to it.

kinger
VIP Member
Compressor forward with bellmouth intake outside of hood for cool fresh air.View attachment 169186
Added bellmouths to the plenum
View attachment 169187
just a test fit of the printed boots
View attachment 169188
Turbo placement. what do you prefer? With the compressor backwards I was going to route my intake into my cabin, under the hood.
With the compressor forwards, I am thinking of adding the nytro oil tank to the front above the engine, then I will remove the stock oil tank which will alllow for more room for the quiet muffler at the back.
View attachment 169189
View attachment 169190

kinger
VIP Member
Larger manifolds are slowing the air down to keep it from heating up from supersonic speeds. I think Ulmer posted earlier.I cannot think of a reason to make the internal volume of the manifold larger than necessary and taking a quick look at what has been done in the automotive world, I don't see any examples of large manifold volumes in a pressurized system. You see large volume manifolds where the intake is also the air source (ambient pressure) and there is a filter involved.
@farmerz24 did I miss the Intercooler?
Larger manifolds are slowing the air down to keep it from heating up from supersonic speeds. I think Ulmer posted earlier.
@farmerz24 did I miss the Intercooler?
I don't think the air is moving that fast. I defer to Ulmers experience but I do not see how 'supersonic' becomes an issue at the pressures most people on this forum are running, in fact the only place I can see air getting to that velocity is where it enters the cylinder. Maybe I am missing some insight here. The temperature will increase simply because it is pressurized but that is why the intercooler is there, to offset that rise in temperature. Increasing the size of the manifold will only increase the volume that the turbo has to maintain pressure against, this works against you at low RPM. Anyone know what the air temperatures are pre-and-post compression?
Reading a bunch more today and thinking more about those supersonic speeds. I am sure they exist but I am not sure it is material to the discussion. I could not find a reference to when it becomes problematic but I am sure it exists somewhere. I did read a lot of discussion about the velocity stacks/bellmouth inside the manifold and it largely seems to be a way to control air distribution in NA engines. In a typical NA engine with the intake running longitudinally with the throttle body at one end. This creates uneven flows (distribution) across the intake ports with the rear ports getting more than the front ports due to air velocity. Even with the primary intake/throttle body being more centered relative to the intake ports the velocity stacks work to straighten out and draw air into the cylinders. In a pressurized vessel I don't see this as being nearly as important.
One great explanation of the need for an expansion chamber in the intake comes from engineering explained where he talks about how Porsche uses the cooling effect of the expansion chamber to increase combustion efficiency, but its a very highly tuned system, and my guess is that there are hard limits to how big the expansion chamber gets before it simply becomes problematic.
Last edited:
Thanks for the feedback and discussion guys.
The intercooler is a front mounted TD cooler, which connectes directly to the front of the plenum. I will be running the TD cooler this year until I make my own. Me and @kennyspec may make a water to air intercooler setup next year, using the extruded aluminum fin type material (what the apex runs under the running boards for its coolers), I may even take the apex ones and mod them to fit the sidewinder, but thats next year.
I am also going to be spraying water meth which will also cool the charge air.
So, you are saying make the plenum more like a straight 4-1 header?
The intercooler is a front mounted TD cooler, which connectes directly to the front of the plenum. I will be running the TD cooler this year until I make my own. Me and @kennyspec may make a water to air intercooler setup next year, using the extruded aluminum fin type material (what the apex runs under the running boards for its coolers), I may even take the apex ones and mod them to fit the sidewinder, but thats next year.
I am also going to be spraying water meth which will also cool the charge air.
So, you are saying make the plenum more like a straight 4-1 header?
yes, I am using PLA plus, an improved PLA, along with reinforncement ribs on the outside of it. 3.2mm walls.Looking at your F-360 shaded model, you could eliminate the rounded parts from the main tube to the intakes making the profile shorter, triangular, and more direct.
Are you printing this yourself? What material? I tried printing myself and some of those parts have lasted, some have not. I had to go back on those failed parts and redesign them understanding the weakness of the materials I was working with (all the standard ABS/PLA/etc). I always wanted to get my original designs (sans extra thickness and supports) printed by a third party in better materials but never got around to it.
Turn you current design into a shorter triangle and it should be good.Thanks for the feedback and discussion guys.
The intercooler is a front mounted TD cooler, which connectes directly to the front of the plenum. I will be running the TD cooler this year until I make my own. Me and @kennyspec may make a water to air intercooler setup next year, using the extruded aluminum fin type material (what the apex runs under the running boards for its coolers), I may even take the apex ones and mod them to fit the sidewinder, but thats next year.
I am also going to be spraying water meth which will also cool the charge air.
So, you are saying make the plenum more like a straight 4-1 header?
Similar threads
-
This site uses cookies to help personalise content, tailor your experience and to keep you logged in if you register.
By continuing to use this site, you are consenting to our use of cookies.