Nytro_Dave
Newbie
- Joined
- Nov 5, 2018
- Messages
- 5
- Reaction score
- 0
- Points
- 151
- Location
- Minocqua, Wisconsin
- Country
- USA
- Snowmobile
- Boosted 2009 Nytro XTX
Done 4 of them now. Some we've even had to drill out all the rivets and just take the whole mount off. We call them muffler bearings now. Lol. Get the copper ones and forget about it.
Deeppow16
TY 4 Stroke Master
- Joined
- Oct 19, 2015
- Messages
- 1,159
- Reaction score
- 550
- Points
- 928
- Location
- Montrose, Minnesota
- Country
- USA
- Snowmobile
- 2016 Arctic Cat M8000
2009 Yamaha Nytro MTX (Totaled)
2002 Polaris 600 XCSP (Sold)
1999 Ski-doo Formula 500 (Totaled)
I'm glad I don't have to think about this any more haha!
Josh Drews
Newbie
- Joined
- Nov 27, 2018
- Messages
- 8
- Reaction score
- 0
- Points
- 31
- Location
- Wisconsin
- Country
- USA
- Snowmobile
- 2008 Yamaha Apex GT 40th
- LOCATION
- southern WI
- WEBSITE
- http://www.djtipster.com
Yup, just like the PowerValve bolts on the SRX's. PITAAlan heads are the dumbest bolts to ever be invented IMO. If that get stuff they will most likely always round out.

Gone Blue
VIP Member
- Joined
- Oct 11, 2006
- Messages
- 1,628
- Reaction score
- 209
- Points
- 1,278
- Location
- Howell, Michigan
- Country
- USA
- Snowmobile
- 08' Nytro RTX 40th Anniversary - Stretched
I got one of the allen head bolts off no problem. The other was a PITA and I spent hours trying to get it out after I rounded out the recess. After no luck, I then decided to drill the head off the bolt and once I did that I was able to grab the threaded shank of the bolt from below that was sticking out of the nut with vise grips and easily spun the bolt out. It was so easy that I could kick myself for all the time I spent trying to get the stripped allen recess bolt out. G.B.
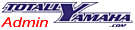

- Joined
- Apr 13, 2003
- Messages
- 21,671
- Reaction score
- 9,282
- Points
- 2,103
- Location
- Schofield, WI
- Website
- www.totallyamaha.com
- Country
- USA
- Snowmobile
- 2020 Sidewinder SRX
I got one of the allen head bolts off no problem. The other was a PITA and I spent hours trying to get it out after I rounded out the recess. After no luck, I then decided to drill the head off the bolt and once I did that I was able to grab the threaded shank of the bolt from below that was sticking out of the nut with vise grips and easily spun the bolt out. It was so easy that I could kick myself for all the time I spent trying to get the stripped allen recess bolt out. G.B.
Did you try adding heat before you went crazy on it?

Last edited:

Gone Blue
VIP Member
- Joined
- Oct 11, 2006
- Messages
- 1,628
- Reaction score
- 209
- Points
- 1,278
- Location
- Howell, Michigan
- Country
- USA
- Snowmobile
- 08' Nytro RTX 40th Anniversary - Stretched
Haha after the fact. I tried to get the one bolt out with heat and an impact screw driver after I had already stripped the allen drive recess. I only soaked the bolts with penetrating fluid before I tried to break them loose. But I have to say it was so easy to drill the head off the bolt and spin the bolt threaded shank out of the nut with vise grips that I would do it again that way in a heart beat. It was no big deal. G.B.Did you try adding heat before you went crazy on it?![]()
Sevey
TY 4 Stroke God
- Joined
- Feb 15, 2011
- Messages
- 1,787
- Reaction score
- 620
- Points
- 1,228
- Location
- Collingwood, ON
- Website
- www.ty4stroke.com
- Country
- Canada
- Snowmobile
- 2018 Sidewinder RTX
I cringed reading your story. Felt the pain......
If they have never seize added the first time they were removed, that makes a huge difference.
I had always ran the sled before working on it to get it good and hot before taking that stuff off, which helped. Mr Sleds comment about the heat gun is bang on.
At least it worked out in the end.
MS
If they have never seize added the first time they were removed, that makes a huge difference.
I had always ran the sled before working on it to get it good and hot before taking that stuff off, which helped. Mr Sleds comment about the heat gun is bang on.
At least it worked out in the end.
MS
jbern58
Newbie
- Joined
- Jan 10, 2021
- Messages
- 13
- Reaction score
- 1
- Points
- 33
- Location
- Wisconsin
- Country
- USA
- Snowmobile
- 2011 Nytro XTX
2008 Phazer FX
I just did this job on my 2011 Nytro with 5500 miles. All donuts were completely MIA. I figured I’d post my personal tips and tricks after not seeing them mentioned in this thread. 1.) Grind the very tip off of your allen socket flat using a bench grinder. If you look at the tip of the bit, it has a convex shape to help the bit go into the bolt head/fastener, but this concave end GREATLY decreases the “bite” of the bit. 2.) Use heat (this was mentioned multiple times, but it is a necessity). I used a regular propane torch. IMO, penetrant isn’t going to help much. Use heat and get it pretty hot. 3.) and likely biggest tip/trick. Use an impact gun of some sort! I used an older Snap-On 3/8ths Nicad cordless impact with 18V battery and it got the job done. My Milwaukee Fuel 3/8 lithium impact would have got it done much better but I was too lazy to walk to the other garage. That Milwaukee 3/8th impact is so worthy buying if you don’t have a cordless impact. I used it at a professional level working on cars day in and day out and it’s tough. A normal 1/2” pneumatic impact might be too aggressive and break bolts too easy. I like the cordless ones as to not overdo it. But the key is the impact action part. It “rattles” the fasteners loose. 4.) If you are using a cordless impact, toggle between tight and loose if it’s not coming free. Sometimes a crusty bolt will tighten a bit first to crack it free and to help it come loose. My grandpa taught me that trick 30 years ago and I have used it so many times since. Sounds crazy but if you have stubborn bolts, go TIGHT first and listen for the “crack”, then they will loosen right out. I know there are bolts I would have stripped out had I not been rattling on them with the impact but I got all necessary, rusty & crusty bolts out that were needed for this job. Feels good to get it done successfully!
Ohiokm
Veteran
- Joined
- Nov 24, 2020
- Messages
- 31
- Reaction score
- 6
- Points
- 28
- Location
- Ohio
- Country
- USA
- Snowmobile
- Yamaha Nytro RTX
I just completed this project too. As a machinist by trade...I decided to not use rivets in the factory exhaust hanger / bracket. I tapped them out with a M5 tap and used stainless steel button head cap screws for installation and used a light amount of medium thread lock on the threads . See picture
Last edited:
Scoobyvroom
Newbie
- Joined
- Feb 24, 2019
- Messages
- 1
- Reaction score
- 2
- Points
- 63
- Location
- Rockford, MN
- Country
- USA
- Snowmobile
- 09 XTX
Did the poor mans flex section replacement. Seen the kit that was 300-400?? something like that. I found 35mm diameter flex section on Ebay for 30 each. Only killer was shipping from the UK.
But it was 130 to my door. Also had a hard time finding clamps. I found 36-39mm and 32-35. The 36 where to big and the barrels would touch before it got tight. The other wheres I couldn't even get over the pipe. I magically found some 1.5 T-bolt clamps from Fastenal.
The flex sections look like decent quality. The wire portion (fat middle) was a 300 series stainless. The ends where some other stainless. I cut the y-pipe just behind where the donuts go. The front shorties I cut where it is straight in front of the accordion part.
Good: Cheapish, looks good. The flex sections where a perfect fit. I got the 8" long ones(2" pipe, 4" flex, 2" pipe). They slid tightly over the header tubes. Think this should last for quite a while.
Cons: Broke off two exhaust header bolts. Had the engine kind of warm, maybe should have gotten it hotter. Removed the rear engine mount and tipped the engine up. Took about 10 minutes to drill out and re-tap the holes. Not sure but trying to get the right clamps was the biggest pain.
Had my minion help me.
Where I cut the tubing. On the flex section I cut at the mark closest to the end. About 1/2" (12mm) Also cut 4X slits in the end of each pipe just slightly wider than the T-bolt clamps.
Think it turned out pretty good!
The heat insulation was flaking off, I had some header wrap so go it taken care of. Not the greatest but no one is gonna see it, right?
But it was 130 to my door. Also had a hard time finding clamps. I found 36-39mm and 32-35. The 36 where to big and the barrels would touch before it got tight. The other wheres I couldn't even get over the pipe. I magically found some 1.5 T-bolt clamps from Fastenal.
The flex sections look like decent quality. The wire portion (fat middle) was a 300 series stainless. The ends where some other stainless. I cut the y-pipe just behind where the donuts go. The front shorties I cut where it is straight in front of the accordion part.
Good: Cheapish, looks good. The flex sections where a perfect fit. I got the 8" long ones(2" pipe, 4" flex, 2" pipe). They slid tightly over the header tubes. Think this should last for quite a while.
Cons: Broke off two exhaust header bolts. Had the engine kind of warm, maybe should have gotten it hotter. Removed the rear engine mount and tipped the engine up. Took about 10 minutes to drill out and re-tap the holes. Not sure but trying to get the right clamps was the biggest pain.
Had my minion help me.
Where I cut the tubing. On the flex section I cut at the mark closest to the end. About 1/2" (12mm) Also cut 4X slits in the end of each pipe just slightly wider than the T-bolt clamps.
Think it turned out pretty good!
The heat insulation was flaking off, I had some header wrap so go it taken care of. Not the greatest but no one is gonna see it, right?
jbern58
Newbie
- Joined
- Jan 10, 2021
- Messages
- 13
- Reaction score
- 1
- Points
- 33
- Location
- Wisconsin
- Country
- USA
- Snowmobile
- 2011 Nytro XTX
2008 Phazer FX
I have done so many I can do them with my eyes closed or sleeping..LOL
MrSled, What are your thoughts on grinding material off of the exhaust clamp stopper/spacer and cranking clamp bolts down tighter? Have you seen cracked flanges as a result? I ground a good 1/8th inch off the stopper/spacer barrel and really cranked the bolts down tight. Now I have been talking with a Yamaha factory guy who says that will crack the flanges where they meet the copper donuts I put in. Of course, I found this out after everything was back together. Thanks for any advice you have
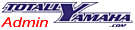

- Joined
- Apr 13, 2003
- Messages
- 21,671
- Reaction score
- 9,282
- Points
- 2,103
- Location
- Schofield, WI
- Website
- www.totallyamaha.com
- Country
- USA
- Snowmobile
- 2020 Sidewinder SRX
MrSled, What are your thoughts on grinding material off of the exhaust clamp stopper/spacer and cranking clamp bolts down tighter? Have you seen cracked flanges as a result? I ground a good 1/8th inch off the stopper/spacer barrel and really cranked the bolts down tight. Now I have been talking with a Yamaha factory guy who says that will crack the flanges where they meet the copper donuts I put in. Of course, I found this out after everything was back together. Thanks for any advice you have
1/8 is a lot, usually do 1/16, but we have never had an issue. What Yamaha factory guy? Most reps dont have a clue.
jbern58
Newbie
- Joined
- Jan 10, 2021
- Messages
- 13
- Reaction score
- 1
- Points
- 33
- Location
- Wisconsin
- Country
- USA
- Snowmobile
- 2011 Nytro XTX
2008 Phazer FX
1/8 is a lot, usually do 1/16, but we have never had an issue. What Yamaha factory guy? Most reps dont have a clue.
Thanks for the quick reply MrSled. It may have been closer to 1/16th actually. But I was not scientific in how I ground it. Just went hog-wild on the grinding wheel. I thought it would be fine if there was extra removed. I never thought those flanges could crack from being over tightened and I wanted to ensure that it never came loose at those joints if the copper seated in or whatever. Those bolts definitely got the "farmer twist" on install also. He's an X factory guy but has his own Yamaha shop. He actually makes these copper donuts so I do think he knows what he is talking about! Just looking for some additional thoughts on it. I would rather tear back in there and make it right than have flanges cracking shortly down the trail:/
Similar threads
- Replies
- 7
- Views
- 1K
- Replies
- 118
- Views
- 83K
-
This site uses cookies to help personalise content, tailor your experience and to keep you logged in if you register.
By continuing to use this site, you are consenting to our use of cookies.