
DigitalFusion
VIP Member
- Joined
- Jan 19, 2011
- Messages
- 1,152
- Reaction score
- 123
- Points
- 988
- Location
- Chisago City, MN
- Country
- USA
- Snowmobile
- 14 Viper LTX, 10 Turbo Phazer MTX, 08 Phazer, 88 SnoScoot
We received well over a foot of snow in two days between Friday and Saturday. As much as I needed to get this sled together, I really needed to get out and ride to remind myself what this is all about. Saturday night a friend and I went out to play. It was snowing so heavily that when I rode over to meet him, I got completely lost on the lake. I could drive by a truck with its lights on sitting outside an ice fishing shack and 100' later I could turn around and not be able to see it any more. I ended up having to pull my phone out and drive by GPS on the Polaris Ride Command app! Eventually the snow lightened up and we had a great time in the fresh snow.
On Sunday I tackled the intake manifold issue. The Boondocker intake was screwed onto the manifold with one rusty machine screw and two self-tapping screws that were not holding very well at all. It was also extremely hard to get to the heads of two top screws to remove. I dug through my bolt collection and found three anodized philips head machine screws. I tapped the throttle body mounting locations to allow a more secure connection, and easier installation/removal of the screws. After the 3 bar map sensor from the PCV-VTI was mounted, I put some RTV around the o-ring for the Boondocker intake, and secured it to the throttle bodies.
I ended up wrapping one more coolant line in DEI reflective tape, even though it wasnt originally wrapped and did not show any signs of heat distress. I figured as long as I had such easy access to it, I might as well do it now. After installing the intake and tightening up the goody turnbuckle connections, the engine was ready to bolt in. It may look like a giant mess, but its a huge milestone for me to have a motor back in this thing!
I was about to bolt the front sub-frame back into place when I realized I have a lot of electrical to do, and it might be easier to tackle that without the sub-frame in the way. After wrestling the front end around I was curious as to what it actually weighed. Granted, this is complete with skis and the oil can for the boondockers kit, but its heavy!
I also needed some type of roll-over-valve system. I wasnt sure if any of the kits out there would actually work with the boondockers oil can. Bill (@Mtnviper ) responded to a thread I created about it, and it seems like his Four Stroke Solutions kit for the Phazer might just work. The biggest concern is mounting the actual valve, since the room under the intercooler is limited and the valve is best mounted at a 45 degree angle. Bill says a few 90* fittings should be fine, so I ordered up one of his ROV kits and some misc 90* fittings, hoping to be able to mount it right behind the filler neck.
In doing some research, I found that the only way to do any datalogging with the PCV is via the POD300 display unit. Considering I wont be able to get this thing dyno tuned, and I am shooting in the dark as far as figuring out if I can get 550cc injectors to work, I made the decision to pick up one of the displays as I know I would end up sitting out in the mountains on our trip regretting that it if I didnt do it and was having issues (if I actually have this thing together in time for it!). I already have enough stuff to cram in my avalanche pack and tunnel bag, having to drag a laptop with doesnt sound too appealing!
As much as I would prefer true gauges over an LCD display, I decided to pull the wideband and (brand spanking new) boost gauge since the POD300 will display those values, and can be programmed to show warning lights for just about any value. Now I get to try and put all this stuff, plus the POD300, into the already very crammed and messy wiring of this thing.
The pod is supposed to arrive today, so last night I decided to just hold off on the electrical stuff until I had everything. I took the opportunity to clean off all the belt dust on the clutch side.
On Sunday I tackled the intake manifold issue. The Boondocker intake was screwed onto the manifold with one rusty machine screw and two self-tapping screws that were not holding very well at all. It was also extremely hard to get to the heads of two top screws to remove. I dug through my bolt collection and found three anodized philips head machine screws. I tapped the throttle body mounting locations to allow a more secure connection, and easier installation/removal of the screws. After the 3 bar map sensor from the PCV-VTI was mounted, I put some RTV around the o-ring for the Boondocker intake, and secured it to the throttle bodies.
I ended up wrapping one more coolant line in DEI reflective tape, even though it wasnt originally wrapped and did not show any signs of heat distress. I figured as long as I had such easy access to it, I might as well do it now. After installing the intake and tightening up the goody turnbuckle connections, the engine was ready to bolt in. It may look like a giant mess, but its a huge milestone for me to have a motor back in this thing!
I was about to bolt the front sub-frame back into place when I realized I have a lot of electrical to do, and it might be easier to tackle that without the sub-frame in the way. After wrestling the front end around I was curious as to what it actually weighed. Granted, this is complete with skis and the oil can for the boondockers kit, but its heavy!
I also needed some type of roll-over-valve system. I wasnt sure if any of the kits out there would actually work with the boondockers oil can. Bill (@Mtnviper ) responded to a thread I created about it, and it seems like his Four Stroke Solutions kit for the Phazer might just work. The biggest concern is mounting the actual valve, since the room under the intercooler is limited and the valve is best mounted at a 45 degree angle. Bill says a few 90* fittings should be fine, so I ordered up one of his ROV kits and some misc 90* fittings, hoping to be able to mount it right behind the filler neck.
In doing some research, I found that the only way to do any datalogging with the PCV is via the POD300 display unit. Considering I wont be able to get this thing dyno tuned, and I am shooting in the dark as far as figuring out if I can get 550cc injectors to work, I made the decision to pick up one of the displays as I know I would end up sitting out in the mountains on our trip regretting that it if I didnt do it and was having issues (if I actually have this thing together in time for it!). I already have enough stuff to cram in my avalanche pack and tunnel bag, having to drag a laptop with doesnt sound too appealing!
As much as I would prefer true gauges over an LCD display, I decided to pull the wideband and (brand spanking new) boost gauge since the POD300 will display those values, and can be programmed to show warning lights for just about any value. Now I get to try and put all this stuff, plus the POD300, into the already very crammed and messy wiring of this thing.
The pod is supposed to arrive today, so last night I decided to just hold off on the electrical stuff until I had everything. I took the opportunity to clean off all the belt dust on the clutch side.
Last edited:
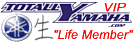

Wow I enjoy reading your builds!

DigitalFusion
VIP Member
- Joined
- Jan 19, 2011
- Messages
- 1,152
- Reaction score
- 123
- Points
- 988
- Location
- Chisago City, MN
- Country
- USA
- Snowmobile
- 14 Viper LTX, 10 Turbo Phazer MTX, 08 Phazer, 88 SnoScoot
The pod arrived, and it was time to get all this stuff crammed into the sled. One of my biggest pet-peeves is messy electrical and/or hacked harnesses. I knew this particular part of this project was going to test my ability to tolerate a rats-nest of wires. There just isnt a lot of room to work with on the phazer, and I dont have time to shorten, solder, and heat shrink dozens and dozens of connections with the clock ticking away before our trip. From here on out, the restoration-style of this project is going to transition into a get-it-done style until the off-season.
I started with installing the PCV-VTI, and ended up locating it on the opposite side of the recommendation from power commander. I re-purposed one of the quick connections I made for the gauges to provide power and ground to the Autotune module. Since I deleted reverse, the "drive" indicator needed to be grounded to force the sled into knowing its in forward gear. I couldnt bring myself to cut that connection, and I didnt have any bullet-style electrical connectors, so my solution was to open the case for that connection, wrap the wire around it, and drop a small amount of solder onto it. If there is ever any reason this will be converted back to having reverse, it will just require the person to unsolder the connection and pull the wire out.
The whole time I was working on electrical items, the skid was staring at me with this creepy, stalker-like look. It knows how much I want to get it installed, and its just taunting me. It reminded me of that "soon" meme. At one point I turned to it and yelled "STOP STARING AT ME SWAN!" I think I have been spending too much time alone in the garage without human contact...
Once the power commander items were installed/wired, I moved onto the ROV kit. The Four Stroke Solutions kit was very well made, and I can see that if I had a standard oil reservoir setup, it would be an extremely easy install. However, since I have that goofy Boondockers oil can with extremely limited space above it due to the intercooler, this became quite the chore. I must have tried at least 20 different variations of hoses, fittings, lengths, and placements. I ended up with this ugly mess of hose clamps, copper fittings, and hoses that allowed me to actually have a slope back to the oil resi, the valve as vertical as possible, and clearance for the intercooler to go over the top.
Before I bolted the sub-frame into place, I wanted to finalize the vacuum line connections just in case there was something that would be easier to route with out it installed. In doing so, I pulled the BOV off to see what fitting I would need to convert it to 90* so it wasn't sticking straight out the side of the sled. That is when I discovered that the piston in it was seized. I gently removed it by pounding it out and inspected the piston and spring. The piston could be polished and lubed, but the spring free length came out to 56mm. Replacement spec is 67mm!
After contacting Turbosmart, I found out that they discontinued this model a long time ago, and no longer have any parts for it. To top it off, the new models do not have compatible springs or the 38mm slip-fit, non v-band connection. They said I could get a Type5, with a v-band adaptor for $250-$350 depending on what model I wanted to go with. However, the Type5's are even longer than the Type1's, plus I never liked the idea of the ports just being open like that, subjected to snow and moisture.
After doing some research, I discovered I could get one of their smaller Kompact recirculating models with a 25mm intake, a 25mm to 35mm silicone transition hose, and the "green" spring for half the price. It will still stick out further than I would like, and a small bolt-on style would be half the size, but since I am trying to get this thing together for the trip, I went with the no-fab option. Going with a recirculating style will allow me to wrap some hydrophobic mesh over the port and keep the snow and moisture out and this model comes with a 90* vacuum line fitting already. With those items ordered, I proceeded with installing the sub-frame
Then it was time to start fitting all the turbo parts together. I realized I still didnt have the wrapped turbo pipes sprayed, so I started putting coats on in between doing other things. I ended up with 4 coats on the midpipe and downpipe. I still have yet to re-wrap the manifold and I am not looking forward to doing it. That stuff is itchy! I also clamped the tunnel cooler lines down. While doing so I realized there was no line for the gas tank overflow/vent at all! Considering that the vent is located right above the turbo manifold, this obviously isnt the safest situation. I once again stole something off the 08 and installed a vent/overflow line.
When I first got the sled, the IC was sitting at a strangle angle and the front of it wasnt even bolted down. The PO said it was like that because he did a crappy job aligning all the hoses and connections after replacing the starter. That seemed feasible enough. I loosely bolted the battery box and turbo back onto the side of the machine after cleaning up the bulkhead a bit, and started doing some test fitting. It was really hard to measure and get pictures of, but the flanges where the IC connects to the intake are just too damn wide. Even with them completely touching, the IC sat off to one side a over 1/2"! In order to see it in pictures you need to look at the sides of the IC in relation to the sub-frame rails, and the front mounting bracket in relation to the center of the cooler.
I really wanted to take it over to my buddies place and cut some of the flange down on his bandsaw, but it was out of commission with a severely bent blade. My other buddy with one has to get up very early in the morning, and since it was starting to get late, I didnt want to bug him. I ended up stuffing the intake with paper towels, installing a clamp around the flange and marking it with a sharpie all the way around. I then took a grinder and worked my way around until there was only a hairline of a mark remaining. I sure hope that will be enough surface to clamp to! Its still 1/4" off-center, but there isnt any more I can do short of trying to find if anyone makes some specialty skinny-width clamps or something.
If I set the cooler into place and lined up the intake, the connection to the turbo was off by about a 1/2" (it was impossible to measure). The quality/quality control on this 'kit' was horrible. Its bad enough that the IC makes the Phazer have a face only a mother could love, couldn't they at least make it fit?!?! I placed yet another order for a 1/2" offset silicone hose, and while I was at it I tossed in a black replacement for the baby-blue cooler-to-intake connection.
I'm not a big sticker guy, and it seems pretty damned obvious to me that this thing is turbocharged considering the intake towering out from the body and the giant intercooler sitting where an airbox would normally be, so I pulled out some of my old sign shop supplies and removed the sticker that advertised the method of induction.
With that stuff bolted on, and the IC set in place, its really starting to look like a snowmobile again... again. I wish I would have had time to powder coat the a-arms in blue, and I am very tempted to swap the white Curves for the black curves on my Viper, but I need to prioritize my time. The most important thing is to just get this damn thing ready for the trip.
I started with installing the PCV-VTI, and ended up locating it on the opposite side of the recommendation from power commander. I re-purposed one of the quick connections I made for the gauges to provide power and ground to the Autotune module. Since I deleted reverse, the "drive" indicator needed to be grounded to force the sled into knowing its in forward gear. I couldnt bring myself to cut that connection, and I didnt have any bullet-style electrical connectors, so my solution was to open the case for that connection, wrap the wire around it, and drop a small amount of solder onto it. If there is ever any reason this will be converted back to having reverse, it will just require the person to unsolder the connection and pull the wire out.
The whole time I was working on electrical items, the skid was staring at me with this creepy, stalker-like look. It knows how much I want to get it installed, and its just taunting me. It reminded me of that "soon" meme. At one point I turned to it and yelled "STOP STARING AT ME SWAN!" I think I have been spending too much time alone in the garage without human contact...
Once the power commander items were installed/wired, I moved onto the ROV kit. The Four Stroke Solutions kit was very well made, and I can see that if I had a standard oil reservoir setup, it would be an extremely easy install. However, since I have that goofy Boondockers oil can with extremely limited space above it due to the intercooler, this became quite the chore. I must have tried at least 20 different variations of hoses, fittings, lengths, and placements. I ended up with this ugly mess of hose clamps, copper fittings, and hoses that allowed me to actually have a slope back to the oil resi, the valve as vertical as possible, and clearance for the intercooler to go over the top.
Before I bolted the sub-frame into place, I wanted to finalize the vacuum line connections just in case there was something that would be easier to route with out it installed. In doing so, I pulled the BOV off to see what fitting I would need to convert it to 90* so it wasn't sticking straight out the side of the sled. That is when I discovered that the piston in it was seized. I gently removed it by pounding it out and inspected the piston and spring. The piston could be polished and lubed, but the spring free length came out to 56mm. Replacement spec is 67mm!
After contacting Turbosmart, I found out that they discontinued this model a long time ago, and no longer have any parts for it. To top it off, the new models do not have compatible springs or the 38mm slip-fit, non v-band connection. They said I could get a Type5, with a v-band adaptor for $250-$350 depending on what model I wanted to go with. However, the Type5's are even longer than the Type1's, plus I never liked the idea of the ports just being open like that, subjected to snow and moisture.
After doing some research, I discovered I could get one of their smaller Kompact recirculating models with a 25mm intake, a 25mm to 35mm silicone transition hose, and the "green" spring for half the price. It will still stick out further than I would like, and a small bolt-on style would be half the size, but since I am trying to get this thing together for the trip, I went with the no-fab option. Going with a recirculating style will allow me to wrap some hydrophobic mesh over the port and keep the snow and moisture out and this model comes with a 90* vacuum line fitting already. With those items ordered, I proceeded with installing the sub-frame
Then it was time to start fitting all the turbo parts together. I realized I still didnt have the wrapped turbo pipes sprayed, so I started putting coats on in between doing other things. I ended up with 4 coats on the midpipe and downpipe. I still have yet to re-wrap the manifold and I am not looking forward to doing it. That stuff is itchy! I also clamped the tunnel cooler lines down. While doing so I realized there was no line for the gas tank overflow/vent at all! Considering that the vent is located right above the turbo manifold, this obviously isnt the safest situation. I once again stole something off the 08 and installed a vent/overflow line.
When I first got the sled, the IC was sitting at a strangle angle and the front of it wasnt even bolted down. The PO said it was like that because he did a crappy job aligning all the hoses and connections after replacing the starter. That seemed feasible enough. I loosely bolted the battery box and turbo back onto the side of the machine after cleaning up the bulkhead a bit, and started doing some test fitting. It was really hard to measure and get pictures of, but the flanges where the IC connects to the intake are just too damn wide. Even with them completely touching, the IC sat off to one side a over 1/2"! In order to see it in pictures you need to look at the sides of the IC in relation to the sub-frame rails, and the front mounting bracket in relation to the center of the cooler.
I really wanted to take it over to my buddies place and cut some of the flange down on his bandsaw, but it was out of commission with a severely bent blade. My other buddy with one has to get up very early in the morning, and since it was starting to get late, I didnt want to bug him. I ended up stuffing the intake with paper towels, installing a clamp around the flange and marking it with a sharpie all the way around. I then took a grinder and worked my way around until there was only a hairline of a mark remaining. I sure hope that will be enough surface to clamp to! Its still 1/4" off-center, but there isnt any more I can do short of trying to find if anyone makes some specialty skinny-width clamps or something.
If I set the cooler into place and lined up the intake, the connection to the turbo was off by about a 1/2" (it was impossible to measure). The quality/quality control on this 'kit' was horrible. Its bad enough that the IC makes the Phazer have a face only a mother could love, couldn't they at least make it fit?!?! I placed yet another order for a 1/2" offset silicone hose, and while I was at it I tossed in a black replacement for the baby-blue cooler-to-intake connection.
I'm not a big sticker guy, and it seems pretty damned obvious to me that this thing is turbocharged considering the intake towering out from the body and the giant intercooler sitting where an airbox would normally be, so I pulled out some of my old sign shop supplies and removed the sticker that advertised the method of induction.
With that stuff bolted on, and the IC set in place, its really starting to look like a snowmobile again... again. I wish I would have had time to powder coat the a-arms in blue, and I am very tempted to swap the white Curves for the black curves on my Viper, but I need to prioritize my time. The most important thing is to just get this damn thing ready for the trip.
Last edited:
MikeWalters
TY 4 Stroke Master
- Joined
- Feb 21, 2010
- Messages
- 1,323
- Reaction score
- 145
- Points
- 888
- Location
- Saskatchewan
- Country
- Canada
- Snowmobile
- 2007 Phazer
Righteous
Mtnviper
TY 4 Stroke Master
- Joined
- Aug 19, 2003
- Messages
- 1,476
- Reaction score
- 340
- Points
- 1,288
- Location
- Burlington Wa.
- Website
- fourstrokesolutionsllc.com
Looks like she's coming right along! I suspect that there have been a few long nights in the garage!
BTW the ROV valve placement should work just fine.
BTW the ROV valve placement should work just fine.

kallholmen
Pro
A friendly advise, take it slow, do it the tight way the first time. All hacks and half done will give you gremlins. And from life experience, you will not find time to go back and do it right.

DigitalFusion
VIP Member
- Joined
- Jan 19, 2011
- Messages
- 1,152
- Reaction score
- 123
- Points
- 988
- Location
- Chisago City, MN
- Country
- USA
- Snowmobile
- 14 Viper LTX, 10 Turbo Phazer MTX, 08 Phazer, 88 SnoScoot
That is great advise. I have no intention to hack anything, or do anything half-assed 
My comments regarding the switch from restoration-style, to a get-it-done-style are in regards to doing things with the intention of getting the machine usable versus how I would normally do them. For example, I would have normally created some brackets to mount the PCV and Autotune modules to, and then drilled and tapped the metal plate they are above to bolt them down instead of just mounting them with zip ties. I would have cut all the electrical wires to length, then soldered, heat shrinked, and wire loomed them all. I would have welded the nuts for the control arms to the subframe to allow removal without pulling it. etc.
There is no way I would take the Viper out west to try and keep up with my buddies. They are all riding anything from 154" to 163" RMKs and Summits/Freerides (one of which is a 240hp turbo). With all the money I have sunk into this thing, I cant afford to do a rental sled if this machine isn't done in time, so I have to choose between doing things how I would like to do them, or cancelling my non-refundable trip. Even if I do get this thing buttoned up, I still don't even know if I will make it because of the tuning situation or any unforeseen setbacks/screw ups.
Perfection can be the enemy of progress.

My comments regarding the switch from restoration-style, to a get-it-done-style are in regards to doing things with the intention of getting the machine usable versus how I would normally do them. For example, I would have normally created some brackets to mount the PCV and Autotune modules to, and then drilled and tapped the metal plate they are above to bolt them down instead of just mounting them with zip ties. I would have cut all the electrical wires to length, then soldered, heat shrinked, and wire loomed them all. I would have welded the nuts for the control arms to the subframe to allow removal without pulling it. etc.
There is no way I would take the Viper out west to try and keep up with my buddies. They are all riding anything from 154" to 163" RMKs and Summits/Freerides (one of which is a 240hp turbo). With all the money I have sunk into this thing, I cant afford to do a rental sled if this machine isn't done in time, so I have to choose between doing things how I would like to do them, or cancelling my non-refundable trip. Even if I do get this thing buttoned up, I still don't even know if I will make it because of the tuning situation or any unforeseen setbacks/screw ups.
Perfection can be the enemy of progress.

Macheater
VIP Member
- Joined
- Feb 7, 2006
- Messages
- 758
- Reaction score
- 288
- Points
- 1,228
- Location
- Niles, Ohio
- Country
- USA
- Snowmobile
- 2006 Apex GT, 2002 SRX700, 2023 Polaris Boost VR-129
- LOCATION
- Niles, Oh
Hey DF u r doing a phenomenal job man keep er goin! Very anxious to see the finished product and hear how it runs. I'm sure you are as well. Man I've been wanting to mod my 09 for several years but, as you alluded to, there is only so much cash to go around. And I'm still dumping $$$ into my 06 Apex.
If I were ever to go forced induction on my phazer it would be an s/c though. With MP no longer making the kits, a used one is almost impossible to find. At least I would know how to source all the mod components since you've done all the hard work.
BTW, even though I'm not the biggest fan of turbo's that intercooler on there makes that thing look TOTALLY SICK!
If I were ever to go forced induction on my phazer it would be an s/c though. With MP no longer making the kits, a used one is almost impossible to find. At least I would know how to source all the mod components since you've done all the hard work.
BTW, even though I'm not the biggest fan of turbo's that intercooler on there makes that thing look TOTALLY SICK!
Last edited:

DigitalFusion
VIP Member
- Joined
- Jan 19, 2011
- Messages
- 1,152
- Reaction score
- 123
- Points
- 988
- Location
- Chisago City, MN
- Country
- USA
- Snowmobile
- 14 Viper LTX, 10 Turbo Phazer MTX, 08 Phazer, 88 SnoScoot
My buddy made a mount for my dynojet pod and dropped it off on Friday. It was a totally backwards deal because he did me a massive favor and HE brought over a case of beer along with it. We installed the mount and pod onto the sled
Feeling like I hadnt accomplished anything, and with the support of my buddy, we swapped the black skis from my Viper onto the Phazer (now those silver control arms stand out even more and make me wish I could have had time to get those done in blue!). Later, a few of the guys came over. We stayed up way too late eating pizza, drinking beer, laughing, BS'ing, and hearing stories about their recent trip all while snowmobile videos were playing on the big screen in the background. It was a great night.
On Saturday I started halfway through the day because of the late night on Friday, but I managed to finish the setback. I did the front at back 3.5" and down 1". In the rear I made two sets of brackets just because it seemed like a good idea. I did one at 3.5" and one at 3" because I have seen both used, and my buddy whipped up 2 sets of plates for me from some templates from @Lashcat. Eventually, I pulled the setback plates back out. I started putting several layers of satin black paint on them in a makeshift paint booth of sorts while re-wrapping the manifold, cleaning up the garage, and organizing parts.
On Sunday, I figured the plates had about 18 hours to dry, so I would install them with some M12 x 30mm bolts and nyloc nuts. Not only did I realize I put all those layers of paint on the wrong plates (the 3"), but it also turned out that my 10-minutes-before-the-store-closed run to Menards to grab some M12 nylocs to mount them the night before ended with me getting one m12 nut with the right pitch, and 3 that were the wrong pitch but stocked in the same bin.

Knowing that I wouldn't be able to 'finish' the setback, as I wanted as many coats as I could put on the plates with as much dry time as possible, I figured I could juggle applying coats of paint with getting the manifold and turbo installed. This is where things went a bit south. I never posted the pic, because it was blurry AF. But the IC was crooked as all hell when I got this machine. This is important as it sets up how the rest of my day went. As I mentioned earlier, the PO said the it was crooked due to hastily installed clamps. I thought I found the real reason being the IC-to-intake connection being off. That was only the preface to cascading effects. Once that was corrected the issue of the crooked cooler continued.
I got the right plates onto the hanger and slapped some primer and the first coat of paint on them. Then I ran up town to pick up 3 more of the correct pitch nuts, as well as some studs for the exhaust manifold. I found that 38mm studs from Dorman that would work pretty well, and according to the website, the local auto parts place had them in stock. Once I got there I found out they only had 1 package (with two studs and nuts), so I ended up picking up a 10 pack that was also M8 x 1.25 for about the same price, but they were 54mm and longer on both sides. I cut the head side down and installed the studs and new gasket
I didnt take a lot of pictures from here on out. Not only would it be boring to look at, but it was hours on end of me installing, removing, reinstalling, and then repeating the entire process all over again. I ended up discovering that the flanges on the manifold didnt match the gasket, and therefore the head. That was only after trying desperately to get the manifold installed, which included me ripping off nearly all the heat wrap because I couldnt see what the issue was. I ended up having to drill the hole on the stator side on the manifold a bit larger to match the gasket.
Thats when things started to make sense. The stator side was the one that was cracking so much and was the worst of the warping on the flange. Obviously the cracking was from the heat of the crappy design of the manifold. However, the extra stress that would have had to be applied to that side would have contributed. I think the discoloration of the head and the condition of the bolt hole on the head of the 2010 motor speaks to this.
I spent the entirety of the night from there on out trying to get everything to line up. I quite literally shed blood trying to do so, and have yet to succeed. I ended up having to cut the bulk head even more (which pained me to do) only because I realized if I mounted the turbo where it was supposed to be, ignoring the mid-pipe completely, only barely left room for the connection, and only then if the IC was mounted at the crazy angle it was when I got the sled. I think that is partially why the IC was so crooked. The person who originally installed this cut the hole in the wrong place. It was also a lot harder to cut a clean circle without being able to use a hole saw since it was already cut. I did the best I could with a combination of a cut off wheel, a jig saw, and a carbide bit in a die grinder. It looks like crap and its going to bug me forever.
I tried every variation of order of operation, twisting/turning the mid pipe, tightening the bolts on the connections in various steps... nothing was working. Its a really odd setup with this kit. The slip-fit connection doesnt seem to want to completely seat if I have the inlet flange at the proper angle to the turbo, and if the flange is at the proper angle to the turbo, either the slip fit isnt right or the turbo is way off of alignment with the inlet to the IC. I threw in the towel, feeling pretty discouraged, hoping for a win tomorrow night.
Its starting to feel like I might have to accept the inevitable. I am not going to make the last trip this year. I missed all of them last year because of a broken wrist. I might end up missing all of them this year because I'm too damned trusting and have this horrible habit of trusting that sellers are like me, and don't feel right if there isn't full disclosure when selling something. Hopefully tomorrow (or I guess later today since I am posting this past midnight) is a more successful day!
Feeling like I hadnt accomplished anything, and with the support of my buddy, we swapped the black skis from my Viper onto the Phazer (now those silver control arms stand out even more and make me wish I could have had time to get those done in blue!). Later, a few of the guys came over. We stayed up way too late eating pizza, drinking beer, laughing, BS'ing, and hearing stories about their recent trip all while snowmobile videos were playing on the big screen in the background. It was a great night.
On Saturday I started halfway through the day because of the late night on Friday, but I managed to finish the setback. I did the front at back 3.5" and down 1". In the rear I made two sets of brackets just because it seemed like a good idea. I did one at 3.5" and one at 3" because I have seen both used, and my buddy whipped up 2 sets of plates for me from some templates from @Lashcat. Eventually, I pulled the setback plates back out. I started putting several layers of satin black paint on them in a makeshift paint booth of sorts while re-wrapping the manifold, cleaning up the garage, and organizing parts.
On Sunday, I figured the plates had about 18 hours to dry, so I would install them with some M12 x 30mm bolts and nyloc nuts. Not only did I realize I put all those layers of paint on the wrong plates (the 3"), but it also turned out that my 10-minutes-before-the-store-closed run to Menards to grab some M12 nylocs to mount them the night before ended with me getting one m12 nut with the right pitch, and 3 that were the wrong pitch but stocked in the same bin.

Knowing that I wouldn't be able to 'finish' the setback, as I wanted as many coats as I could put on the plates with as much dry time as possible, I figured I could juggle applying coats of paint with getting the manifold and turbo installed. This is where things went a bit south. I never posted the pic, because it was blurry AF. But the IC was crooked as all hell when I got this machine. This is important as it sets up how the rest of my day went. As I mentioned earlier, the PO said the it was crooked due to hastily installed clamps. I thought I found the real reason being the IC-to-intake connection being off. That was only the preface to cascading effects. Once that was corrected the issue of the crooked cooler continued.
I got the right plates onto the hanger and slapped some primer and the first coat of paint on them. Then I ran up town to pick up 3 more of the correct pitch nuts, as well as some studs for the exhaust manifold. I found that 38mm studs from Dorman that would work pretty well, and according to the website, the local auto parts place had them in stock. Once I got there I found out they only had 1 package (with two studs and nuts), so I ended up picking up a 10 pack that was also M8 x 1.25 for about the same price, but they were 54mm and longer on both sides. I cut the head side down and installed the studs and new gasket
I didnt take a lot of pictures from here on out. Not only would it be boring to look at, but it was hours on end of me installing, removing, reinstalling, and then repeating the entire process all over again. I ended up discovering that the flanges on the manifold didnt match the gasket, and therefore the head. That was only after trying desperately to get the manifold installed, which included me ripping off nearly all the heat wrap because I couldnt see what the issue was. I ended up having to drill the hole on the stator side on the manifold a bit larger to match the gasket.
Thats when things started to make sense. The stator side was the one that was cracking so much and was the worst of the warping on the flange. Obviously the cracking was from the heat of the crappy design of the manifold. However, the extra stress that would have had to be applied to that side would have contributed. I think the discoloration of the head and the condition of the bolt hole on the head of the 2010 motor speaks to this.
I spent the entirety of the night from there on out trying to get everything to line up. I quite literally shed blood trying to do so, and have yet to succeed. I ended up having to cut the bulk head even more (which pained me to do) only because I realized if I mounted the turbo where it was supposed to be, ignoring the mid-pipe completely, only barely left room for the connection, and only then if the IC was mounted at the crazy angle it was when I got the sled. I think that is partially why the IC was so crooked. The person who originally installed this cut the hole in the wrong place. It was also a lot harder to cut a clean circle without being able to use a hole saw since it was already cut. I did the best I could with a combination of a cut off wheel, a jig saw, and a carbide bit in a die grinder. It looks like crap and its going to bug me forever.
I tried every variation of order of operation, twisting/turning the mid pipe, tightening the bolts on the connections in various steps... nothing was working. Its a really odd setup with this kit. The slip-fit connection doesnt seem to want to completely seat if I have the inlet flange at the proper angle to the turbo, and if the flange is at the proper angle to the turbo, either the slip fit isnt right or the turbo is way off of alignment with the inlet to the IC. I threw in the towel, feeling pretty discouraged, hoping for a win tomorrow night.
Its starting to feel like I might have to accept the inevitable. I am not going to make the last trip this year. I missed all of them last year because of a broken wrist. I might end up missing all of them this year because I'm too damned trusting and have this horrible habit of trusting that sellers are like me, and don't feel right if there isn't full disclosure when selling something. Hopefully tomorrow (or I guess later today since I am posting this past midnight) is a more successful day!
Last edited:
MikeWalters
TY 4 Stroke Master
- Joined
- Feb 21, 2010
- Messages
- 1,323
- Reaction score
- 145
- Points
- 888
- Location
- Saskatchewan
- Country
- Canada
- Snowmobile
- 2007 Phazer
I would use construction adhesive (pl400 or something like that) and glue a block of plywood behind your hole thats already cut. clamp it and let it cure. Once cured then you have a surface to start your holesaw if you want to clean it up. Then knock off the plywood.
Good luck man this looks awesome!! Very nice work!!
Good luck man this looks awesome!! Very nice work!!

DigitalFusion
VIP Member
- Joined
- Jan 19, 2011
- Messages
- 1,152
- Reaction score
- 123
- Points
- 988
- Location
- Chisago City, MN
- Country
- USA
- Snowmobile
- 14 Viper LTX, 10 Turbo Phazer MTX, 08 Phazer, 88 SnoScoot
Good tip. I think in the off season I will pull this bulkhead out and deal with it then. I have an extra bulkhead, but i think I will fill the hole, then cut and reinforce. My biggest concern is how nothing wants to line up at all now. My current theory is that this was installed improperly for so long that everything warped due to heat and too thin of material. Now that I have squared the manifold, and am aligning things correctly, its all outta whack.

DigitalFusion
VIP Member
- Joined
- Jan 19, 2011
- Messages
- 1,152
- Reaction score
- 123
- Points
- 988
- Location
- Chisago City, MN
- Country
- USA
- Snowmobile
- 14 Viper LTX, 10 Turbo Phazer MTX, 08 Phazer, 88 SnoScoot
With nearly 24 hours of cure time on the paint for the right setback plates, I got the skid completely installed. I didn't install the 2 wheels that go on the outside at the tip-up, still not sure if that is a bad idea or not.
The turbo install was kicking my arse. With a fresh head, I realized I need to start from the head and get the manifold bolted on tight, let the mid-pipe end up where ever it ended up, and work my way forward. In doing so, the turbo ends up no where near where it would need to be for the bracket to bolt to the frame, and the bracket is part of what holds the turbine housing on. Frustrated with dealing with this situation I decided to just move onto something else for now. The adaptor for the BOV arrived, and I wanted to see just how much I need to cut it down. In order to do so I would have to set the tank & panels in place, which provided a much needed motivating tease of how it will look once I can finally bolt things in place!
If I get those arms coated in blue, slap some floats in place of the stock shocks, and treat the IC with heat dispersant black coating (and maybe the sides of the cooler in blue as well) this thing would actually look pretty damn cool IMHO.
This is when the Curse of the Crooked Cooler© and turbo alignment issues once again reared its ugly head. If the intercooler is centered on the machine, it sits too high to mount the headlight!
I took a step back in frustration of how absolutely lousy this particular Boondocker kit is, vowing to never ever purchase one of their products as long as I live, when I noticed there seemed something off with the tierod.
That is a different part number than the tie rod from the 08 (I assume its shorter), so I cant swap them. I found the closest place that had one in-stock and ordered it up, then took a night off of wrenching and took the wife and kids out to dinner and a show, only to return to this email.
The turbo install was kicking my arse. With a fresh head, I realized I need to start from the head and get the manifold bolted on tight, let the mid-pipe end up where ever it ended up, and work my way forward. In doing so, the turbo ends up no where near where it would need to be for the bracket to bolt to the frame, and the bracket is part of what holds the turbine housing on. Frustrated with dealing with this situation I decided to just move onto something else for now. The adaptor for the BOV arrived, and I wanted to see just how much I need to cut it down. In order to do so I would have to set the tank & panels in place, which provided a much needed motivating tease of how it will look once I can finally bolt things in place!
If I get those arms coated in blue, slap some floats in place of the stock shocks, and treat the IC with heat dispersant black coating (and maybe the sides of the cooler in blue as well) this thing would actually look pretty damn cool IMHO.
This is when the Curse of the Crooked Cooler© and turbo alignment issues once again reared its ugly head. If the intercooler is centered on the machine, it sits too high to mount the headlight!
I took a step back in frustration of how absolutely lousy this particular Boondocker kit is, vowing to never ever purchase one of their products as long as I live, when I noticed there seemed something off with the tierod.
That is a different part number than the tie rod from the 08 (I assume its shorter), so I cant swap them. I found the closest place that had one in-stock and ordered it up, then took a night off of wrenching and took the wife and kids out to dinner and a show, only to return to this email.
Snowmixer
Pro
- Joined
- Oct 29, 2010
- Messages
- 188
- Reaction score
- 79
- Points
- 733
- Location
- Snohomish, Washington
- Country
- USA
- Snowmobile
- 2007 Phazer Mountain Lite
2008 Phazer MTX
2012 Arctic Cat M800 153
Sounds like you could use a lathe at the moment! A new tie rod would be an easy one to machine (as long as you can get left and right hand taps) though you may be able to straighten the original enough to be functional, since the bend is rather slight.
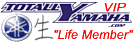

- Joined
- Jun 1, 2004
- Messages
- 7,835
- Reaction score
- 2,034
- Points
- 2,103
- Location
- sudbury on
- Country
- Canada
- Snowmobile
- 2016 apex xtx
2011 apex xtx
2009 phaser rtx/x
1997 et410t/r
1988 vk 540
With nearly 24 hours of cure time on the paint for the right setback plates, I got the skid completely installed. I didn't install the 2 wheels that go on the outside at the tip-up, still not sure if that is a bad idea or not.
View attachment 138934
View attachment 138935
The turbo install was kicking my arse. With a fresh head, I realized I need to start from the head and get the manifold bolted on tight, let the mid-pipe end up where ever it ended up, and work my way forward. In doing so, the turbo ends up no where near where it would need to be for the bracket to bolt to the frame, and the bracket is part of what holds the turbine housing on. Frustrated with dealing with this situation I decided to just move onto something else for now. The adaptor for the BOV arrived, and I wanted to see just how much I need to cut it down. In order to do so I would have to set the tank & panels in place, which provided a much needed motivating tease of how it will look once I can finally bolt things in place!
If I get those arms coated in blue, slap some floats in place of the stock shocks, and treat the IC with heat dispersant black coating (and maybe the sides of the cooler in blue as well) this thing would actually look pretty damn cool IMHO.
View attachment 138933
This is when the Curse of the Crooked Cooler© and turbo alignment issues once again reared its ugly head. If the intercooler is centered on the machine, it sits too high to mount the headlight!
View attachment 138932
View attachment 138931
I took a step back in frustration of how absolutely lousy this particular Boondocker kit is, vowing to never ever purchase one of their products as long as I live, when I noticed there seemed something off with the tierod.
View attachment 138930
View attachment 138929
That is a different part number than the tie rod from the 08 (I assume its shorter), so I cant swap them. I found the closest place that had one in-stock and ordered it up, then took a night off of wrenching and took the wife and kids out to dinner and a show, only to return to this email.
View attachment 138928
looking good!
when i converted my 09 rtx into an xtx rear suspension i used a kimpex kit for adding wheels and axle to an older enticer suspension that i modded to go in between the rails instead of the outer wheels. it held the plastic off of the floor about 1/4" and the slider wear looked good at the kick up the last time i looked at it. without them i bet you will wear through.

DigitalFusion
VIP Member
- Joined
- Jan 19, 2011
- Messages
- 1,152
- Reaction score
- 123
- Points
- 988
- Location
- Chisago City, MN
- Country
- USA
- Snowmobile
- 14 Viper LTX, 10 Turbo Phazer MTX, 08 Phazer, 88 SnoScoot
Sounds like you could use a lathe at the moment! A new tie rod would be an easy one to machine (as long as you can get left and right hand taps) though you may be able to straighten the original enough to be functional, since the bend is rather slight.
I wish I had a lathe and skills to use it. Metal fab has always been a weakness of mine. I tried cancelling the order by replying to their email, and time stamps show that I sent my reply 6 minutes after they sent the inital email, but sure enough, I had a 'your item has been shipped' confirmation in my in box this morning, making it so I cannot just cancel the order.
I might just try and bend it back at this point. Its such a low priority item for me at the moment.
Similar threads
- Replies
- 13
- Views
- 1K
- Replies
- 175
- Views
- 64K
-
This site uses cookies to help personalise content, tailor your experience and to keep you logged in if you register.
By continuing to use this site, you are consenting to our use of cookies.