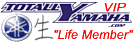

I agree but a chassis and suspension have to be designed from the beginning to be stiff and its obvious to me that this one isnt. Example Honda when they switched to Aluminum frames on Dirtbikes there were many redesigns because the frame was too stiff. My Cannondales are another example. It was very tough to setup for Flat track and TT because of how stiff the frame is. Even the Honda ATV. The very best was the 250R. That frame was as thin as a tin can. On a smooth surface suspension can work to overcome a stiff chassis but we are not riding on smooth surfaces. As for strength look at a Semi. They are made to Flex because to make them strong enough to not flex they would weigh way too much.I'm not meaning to bust your ballz here Steve but let's agree to disagree....
https://dsportmag.com/the-tech/chassis-101-performance-control-safety/
I'm sure that AC and Yamaha have engineers on their staff that are on a much higher pay grade than me but it's an interesting topic to consider.
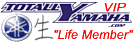

In either case I dont think anyone here can honestly say that this chassis does not flex. So we have to deal with it. Whether it was by design or just a consequence of lighter weight or cost saving measures.
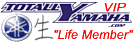

Turboflash
Lifetime Member
- Joined
- Mar 18, 2019
- Messages
- 2,749
- Reaction score
- 2,793
- Points
- 1,113
- Location
- Southern MN
- Country
- USA
- Snowmobile
- '17 ZR9000 Ltd. 137 - PEFI Stage 4
I've used the Skwezloc bearing for about 15 years. But, remember Cat and Polaris and many others used an eccentric locking bearing for 50 years and never had a problem w shaft spinning in bearing cuz the two were connected to each other.It seems like a bearing with a cocentric locking collar could solve these issues while still allowing for easy disassembly.... although due to the brake caliper location, the locking collar side of the bearing made need to be on the inside of the tunnel, not against the brake rotor.
https://www.timken.com/products/timken-engineered-bearings/housed-units/concentric-locking-collar/
View attachment 153966

twyztid
VIP Member
- Joined
- Feb 14, 2011
- Messages
- 982
- Reaction score
- 491
- Points
- 1,078
- Location
- Middleville, MI
- Country
- USA
- Snowmobile
- 2025 Sidewinder LTX LE EPS
2017 Sidewinder LTX SE
2012 Apex XTX
2012 RS Vector LTX
- LOCATION
- Middleville, MI
I think "twyztid" is on to something here. For decades Yamaha has used a concentric bearing with a locking collar on the driveshaft bearing and the jackshaft bearing. Has anyone ever heard of the bearing spinning on either shaft with this set up?
With the concentric bearing you've got a lot more surface area to make contact with the shaft along with locking it down to the shaft.
I'm sure that the Arctic bean counters have a lot to say in what components they use. It's too bad Yamaha doesn't step up to the plate with this seemingly tried and true set up.
Here's a diagram of the 2020 Yamaha RS Venture and VK 540 that are the sole surviving sleds still being made by Yamaha in Japan. It's interesting that Yamaha still uses the concentric bearing and locking collar on it's sleds:
View attachment 153974
Draw your own conclusions here but I think the answer is pretty obvious.
Thoughts?
I know of standard set screw locking collars on older Yamaha sleds but I am not aware of one using a cocentric locking collar like in the link I posted.
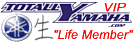

VX1R
Lifetime Member
- Joined
- Sep 19, 2004
- Messages
- 2,286
- Reaction score
- 4,723
- Points
- 1,603
- Location
- Inver Grove Heights, MN
- Country
- USA
- Snowmobile
- Ordered: 2025 SW LTX-LE Final Edition
Current Riders:
2018 SW LTX-LE
2002 SRX Custom
Rough Trail: 2023 Lynx Xterrian 900TurboR
Vintage Riders:
1980 Enticer 300 Twin
1986 Inviter
1998 Phazer Mt. Lite
1996 Phazer Mt. Lite Mod
I know of standard set screw locking collars on older Yamaha sleds but I am not aware of one using a cocentric locking collar like in the link I posted.
You are correct. Yamaha has used the standard set screw locking collars on the track drive axle as shown in the diagram I posted.
They have used the concentric locking collars in the link you posted on the jackshaft on some of their sleds, not on the drive shaft as I incorrectly stated.
Richard Hodgins
Expert
- Joined
- Mar 5, 2019
- Messages
- 266
- Reaction score
- 262
- Points
- 638
- Location
- Ottawa ontario
- Country
- Canada
- Snowmobile
- Yamaha powered CAT
It put it on at 4300kms and there was evidence it had just started to spin but no wear. torqued to 30ft/lbsBefore you put this on was the bearing spinning?
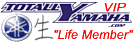

STAIN
Lifetime Member
- Joined
- Feb 29, 2004
- Messages
- 4,387
- Reaction score
- 3,646
- Points
- 1,713
- Location
- Vermont
- Country
- USA
- Snowmobile
- 2024 Arctic Cat Riot 9000
- LOCATION
- Vermont
If you lock that bearing to the shaft you open another can of worms. What happens when the bearing fails or seizes then? You destroy your caliper possibly compromising brake function. Which is worse?I've used the Skwezloc bearing for about 15 years. But, remember Cat and Polaris and many others used an eccentric locking bearing for 50 years and never had a problem w shaft spinning in bearing cuz the two were connected to each other.
While I agree the bearing should be tighter I am guessing it is not locked to the shaft for a purpose.
I have seen the old style bearings that lock on the shaft seize and ruin the tunnel, again which is worse, new shaft or tunnel repair??
If the tolerance was tighter you could warm the bearing OR cool the shaft for installation, or both, not too hard to do.
It looks to me that the BOP wedge is the best answer so far
Sevey
TY 4 Stroke God
- Joined
- Feb 15, 2011
- Messages
- 1,784
- Reaction score
- 620
- Points
- 1,228
- Location
- Collingwood, ON
- Website
- www.ty4stroke.com
- Country
- Canada
- Snowmobile
- 2018 Sidewinder RTX
If you lock that bearing to the shaft you open another can of worms. What happens when the bearing fails or seizes then? You destroy your caliper possibly compromising brake function. Which is worse?
While I agree the bearing should be tighter I am guessing it is not locked to the shaft for a purpose.
I have seen the old style bearings that lock on the shaft seize and ruin the tunnel, again which is worse, new shaft or tunnel repair??
If the tolerance was tighter you could warm the bearing OR cool the shaft for installation, or both, not too hard to do.
It looks to me that the BOP wedge is the best answer so far
I have a sled where that bearing does not like to be sealed on the shaft and will flex the tunnel - something is out of true. Had to pull it apart and clean the loctite off. Convinced they are made with this loose fit for a reason. It doesn't mean I like it though
MS

KnappAttack
24X ISR World Drag Racing Champion
- Joined
- Feb 19, 2004
- Messages
- 4,847
- Reaction score
- 6,111
- Points
- 1,733
- Location
- Welch MN
- Country
- USA
- Snowmobile
- 2023 Sidewinder LTX-LE
2017 Sidewinder LTX-LE
I have a sled where that bearing does not like to be sealed on the shaft and will flex the tunnel - something is out of true. Had to pull it apart and clean the loctite off. Convinced they are made with this loose fit for a reason. It doesn't mean I like it though
MS
If the shaft was the same size as the bearing, and runs true and shaft's not bent, the tunnel will not flex or wobble. Tight fit is not an issue as long as properly assembled. Tight is right and the way it should be.
If the bearing is locked down cocked on a worn shaft, its bound to wobble and flex the tunnel. Shouldn't be done like that. Extra precautions must be done to insure the bearing runs true on the shaft before locking it down, and it can't happen with just loctite. That would be like chucking a short piece up in the lathe and watching it wobble without trueing it up before machining. True the bearing on the shaft like you chuck it up in a lathe and it won't wobble, but you must use the BOP wedge to tighten it up, not loctite or any other hokey way to hold the bearing on the shaft. It has to be tightened, rotated and trued as it gets locked down so the wobble does not happen.
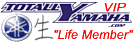

Good luck trueing it up while in tunnel. I agree would be ideal but how? Thats and tunnel flex is why I set my BOP wedge to just barely hold the inner race even with the good welded shafts which takes very little torque and the brand new undersize shaft which takes way more torque than I like. Neither of my sleds have a flexing tunnel ever that I could see so either some shafts are being used really wore or shafts themselves are bent or machined off center. Would be interesting to know which because before I got by with just peening the wore shafts and still no flex of tunnel. Sevey is not the only one to report this though so it must be another issue with quality.If the shaft was the same size as the bearing, and runs true and shaft's not bent, the tunnel will not flex or wobble. Tight fit is not an issue as long as properly assembled. Tight is right and the way it should be.
If the bearing is locked down cocked on a worn shaft, its bound to wobble and flex the tunnel. Shouldn't be done like that. Extra precautions must be done to insure the bearing runs true on the shaft before locking it down, and it can't happen with just loctite. That would be like chucking a short piece up in the lathe and watching it wobble without trueing it up before machining. True the bearing on the shaft like you chuck it up in a lathe and it won't wobble, but you must use the BOP wedge to tighten it up, not loctite or any other hokey way to hold the bearing on the shaft. It has to be tightened, rotated and trued as it gets locked down so the wobble does not happen.
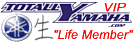

Turboflash
Lifetime Member
- Joined
- Mar 18, 2019
- Messages
- 2,749
- Reaction score
- 2,793
- Points
- 1,113
- Location
- Southern MN
- Country
- USA
- Snowmobile
- '17 ZR9000 Ltd. 137 - PEFI Stage 4
As I previously stated, my caliper-side bearing failed in early March. I did have a BOP wedge installed but that doesn't help if the bearing fails. New track shafts were on backorder for delivery later in March or even April. I decided to make the repair by getting my shaft spray welded and have the bearing journals sized for interference fit to the bearing (bearing journal is .0005" bigger than bearing ID). I did that. This last weekend I made the repair. Since I could not just slide the caliper housing onto the shaft, OR slide the shaft into the chain case bearing, I had to build a press tool. Below are pics. It's a threaded rod cut into pieces so it can be assembled piece by piece as it is slid into the track shaft. Then I made a press cup which barely fit over the splines on both sides of shaft. Cup presses on the inner race of the bearing. On chain case side, I inserted the track shaft into the new bearing (after first installing new seal), then put the cup onto the shaft, a washer on outside, and nut. The caliper side had a little plug that just fit the ID of the shaft, then a washer and nut. All I had to do was turn the nut on chain case side and it pulled the shaft right into bearing until I had it in the right place (both lower gears and retaining ring on snug with no play). Then, went to caliper side and used the same cup to press housing (with new bearing) onto track shaft (moved the little plug to chain case side). I pressed the caliper housing on until it was in right place (basically no side load either way on bearing - housing snug against outside of tunnel). It worked perfect. If you're wondering how I would get caliper housing off, I have a puller (Travis from BOP previously published a drawing of it and I made one) that uses the same 3 holes that holds the housing on to pull housing off. Puller is just a flat plate with 3 holes. Puller presses on end of track shaft and pulls housing.
Big question: is press fit ok? Bearing are C3 internal clearance (=loose fit - intended for press fit). Shaft can no longer float side to side at all (but it can't with BOP wedge in either). Time will tell if this will work. I plan on re-greasing or replacing caliper-side bearing every year anyway.
Big question: is press fit ok? Bearing are C3 internal clearance (=loose fit - intended for press fit). Shaft can no longer float side to side at all (but it can't with BOP wedge in either). Time will tell if this will work. I plan on re-greasing or replacing caliper-side bearing every year anyway.
Attachments
-
track shaft repair6.1.jpg45.4 KB · Views: 233
-
track shaft repair7.1.jpg55.4 KB · Views: 230
-
track shaft repair5.1.jpg54.9 KB · Views: 234
-
track shaft repair4.1.jpg25.4 KB · Views: 244
-
track shaft repair3.1.jpg22.3 KB · Views: 227
-
track shaft repair2.1.jpg21.3 KB · Views: 249
-
track shaft repair1.1.jpg38.8 KB · Views: 226
-
Caliper puller template R0.pdf1.9 KB · Views: 143
-
track shaft spray weld1.1.jpg30.6 KB · Views: 225
-
track shaft spray weld2.1.jpg38.3 KB · Views: 243

KnappAttack
24X ISR World Drag Racing Champion
- Joined
- Feb 19, 2004
- Messages
- 4,847
- Reaction score
- 6,111
- Points
- 1,733
- Location
- Welch MN
- Country
- USA
- Snowmobile
- 2023 Sidewinder LTX-LE
2017 Sidewinder LTX-LE
Good luck trueing it up while in tunnel. I agree would be ideal but how? Thats and tunnel flex is why I set my BOP wedge to just barely hold the inner race even with the good welded shafts which takes very little torque and the brand new undersize shaft which takes way more torque than I like. Neither of my sleds have a flexing tunnel ever that I could see so either some shafts are being used really wore or shafts themselves are bent or machined off center. Would be interesting to know which because before I got by with just peening the wore shafts and still no flex of tunnel. Sevey is not the only one to report this though so it must be another issue with quality.
How? Well, its a bit like chucking a narrow piece up in a three jaw chuck in the lathe. You need to rotate the shaft while tightening up the wedge bolt on to the bearing a bit at a time, so the bearing does not end up cocked on the shaft. This will allow the shaft to expand where its supposed to while letting the bearing true itself up onto the shaft as it goes around. You want to make the wedge the last thing you do after everything else is bolted down in the suspension and circlips on the shafts on both ends as well, so all the tension and side force is not causing bind in the bearings. This will allow it to run true and with no side force on the bearings and such.
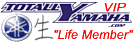

Thank you! Makes senseHow? Well, its a bit like chucking a narrow piece up in a three jaw chuck in the lathe. You need to rotate the shaft while tightening up the wedge bolt on to the bearing a bit at a time, so the bearing does not end up cocked on the shaft. This will allow the shaft to expand where its supposed to while letting the bearing true itself up onto the shaft as it goes around. You want to make the wedge the last thing you do after everything else is bolted down in the suspension and circlips on the shafts on both ends as well, so all the tension and side force is not causing bind in the bearings. This will allow it to run true and with no side force on the bearings and such.
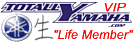

We will see. Great job either way! I assume no tunnel flex was observed ?As I previously stated, my caliper-side bearing failed in early March. I did have a BOP wedge installed but that doesn't help if the bearing fails. New track shafts were on backorder for delivery later in March or even April. I decided to make the repair by getting my shaft spray welded and have the bearing journals sized for interference fit to the bearing (bearing journal is .0005" bigger than bearing ID). I did that. This last weekend I made the repair. Since I could not just slide the caliper housing onto the shaft, OR slide the shaft into the chain case bearing, I had to build a press tool. Below are pics. It's a threaded rod cut into pieces so it can be assembled piece by piece as it is slid into the track shaft. Then I made a press cup which barely fit over the splines on both sides of shaft. Cup presses on the inner race of the bearing. On chain case side, I inserted the track shaft into the new bearing (after first installing new seal), then put the cup onto the shaft, a washer on outside, and nut. The caliper side had a little plug that just fit the ID of the shaft, then a washer and nut. All I had to do was turn the nut on chain case side and it pulled the shaft right into bearing until I had it in the right place (both lower gears and retaining ring on snug with no play). Then, went to caliper side and used the same cup to press housing (with new bearing) onto track shaft (moved the little plug to chain case side). I pressed the caliper housing on until it was in right place (basically no side load either way on bearing - housing snug against outside of tunnel). It worked perfect. If you're wondering how I would get caliper housing off, I have a puller (Travis from BOP previously published a drawing of it and I made one) that uses the same 3 holes that holds the housing on to pull housing off. Puller is just a flat plate with 3 holes. Puller presses on end of track shaft and pulls housing.
Big question: is press fit ok? Bearing are C3 internal clearance (=loose fit - intended for press fit). Shaft can no longer float side to side at all (but it can't with BOP wedge in either). Time will tell if this will work. I plan on re-greasing or replacing caliper-side bearing every year anyway.
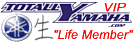

Turboflash
Lifetime Member
- Joined
- Mar 18, 2019
- Messages
- 2,749
- Reaction score
- 2,793
- Points
- 1,113
- Location
- Southern MN
- Country
- USA
- Snowmobile
- '17 ZR9000 Ltd. 137 - PEFI Stage 4
No tunnel flex at all. It ran perfectly true. Held my hand on it while running and it's like it's balanced; no vibration in tunnel at all. When I was done, I could move the track shaft a tiny bit back and forth (it's the clearance in the bearings) thus proving they were not preloaded either way (in neutral position).
Similar threads
- Replies
- 26
- Views
- 9K
-
This site uses cookies to help personalise content, tailor your experience and to keep you logged in if you register.
By continuing to use this site, you are consenting to our use of cookies.