Dave has responded to this on this site. He recommends using the tool as shown in the video with the wide end of the gauge facing up.

KnappAttack
24X ISR World Drag Racing Champion
- Joined
- Feb 19, 2004
- Messages
- 4,695
- Location
- Welch MN
- Country
- USA
- Snowmobile
- 2023 Sidewinder LTX-LE
2017 Sidewinder LTX-LE
I agree, that's why I wanted to ask around here. I would give Dave a call but my work hours makes that difficult. Thanks.
If the bar is indeed straight, its not possible that the reading would be different. I've checked mine both ways and it reads exactly the same.
The best way to do this is to take off the belt guard which requires drilling out two rivets in the tunnel and removing four screws or so from it to get a real good look at it when measuring. I believe people are not being real accurate with their measurements because they can't see things with the guard in place. The bar also flexes a bit when using the go-no go tool, which can not be seen unless looking from straight above.
Also the tools being used, and how they are used will give to different measurements. Some people are more adept at using these tools than others. It is common sense stuff, but one has to be perfect in using the tool and doing the measurements properly getting repeatable results on measurements.
No offense, but If you have to ask questions here and/or call Dave and can't figure it out, you may not be qualified to perform this task properly, it may be best to phone a friend that is qualified to perform this task. I see you are in Southern MN, I'd be available to help you get the proper numbers for machining. I've even been doing them without machining by removing the circlip and bolting the driven down solid against the bearing. I've been setting them up without float and will not run any float.
Do yourself a favor and after you drill out the rivets holding the belt guard in place install riv-nuts instead of rivets, so you will be able to remove the guard easily in the future!
john10toe
Pro
What is the dimension/thickness of the go-no go gauge where you insert it on the primary?
Like Shagnos asked......can anyone comment on the dimensions of the go-no-go gauge?
SPM
Pro
- Joined
- Nov 18, 2018
- Messages
- 150
- Age
- 57
- Location
- so. mn
- Country
- USA
- Snowmobile
- 2018 Sidewinder L-TX LE
No offense, but I'm more than qualified to perform this task. After owning a engine machine shop 0ver 25 years I have more calipers, dial bore gauges,micrometers, depth mics,ect then most people will ever see. With my schedule, playing phone tag with Dave was not my first choice as it would waste our time. I thought I would consult the pros on here first. I agree flipping the bar shouldn't make a bit of difference but it was for me and I checked it many times, after all it's just common sense right? The tools and gauge are fine it's something else causing the different readings and most people maybe would not have double checked it. Well..I machined up everything today and set up for no float. I guess I'll see if I know how to use my tools after all. Thanks for the offer to help.If the bar is indeed straight, its not possible that the reading would be different. I've checked mine both ways and it reads exactly the same.
The best way to do this is to take off the belt guard which requires drilling out two rivets in the tunnel and removing four screws or so from it to get a real good look at it when measuring. I believe people are not being real accurate with their measurements because they can't see things with the guard in place. The bar also flexes a bit when using the go-no go tool, which can not be seen unless looking from straight above.
Also the tools being used, and how they are used will give to different measurements. Some people are more adept at using these tools than others. It is common sense stuff, but one has to be perfect in using the tool and doing the measurements properly getting repeatable results on measurements.
No offense, but If you have to ask questions here and/or call Dave and can't figure it out, you may not be qualified to perform this task properly, it may be best to phone a friend that is qualified to perform this task. I see you are in Southern MN, I'd be available to help you get the proper numbers for machining. I've even been doing them without machining by removing the circlip and bolting the driven down solid against the bearing. I've been setting them up without float and will not run any float.
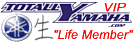

Beerman
I can actually hear myself getting fatter
- Joined
- Nov 22, 2004
- Messages
- 1,093
- Location
- Plymouth, MN
- Website
- www.loyalshepherd.com
- Country
- USA
- Snowmobile
- Sidewinder LTX-SE
- YOUTUBE
- arttyszka
I don't think it's anything you're doing - I know of 2 others on this board that have found the same thing, different readings depending which way the bar is in. You're in the right place and "welcome". Sorry no one has the answer yet on what you and others are seeing. The net seems to be use it like Dave shows in the video and most all guys are ending up close to the same final settings. This season will be VERY telling with belt life reports. Many of us are outright praying the code has finally been cracked.No offense, but I'm more than qualified to perform this task. After owning a engine machine shop 0ver 25 years I have more calipers, dial bore gauges,micrometers, depth mics,ect then most people will ever see. With my schedule, playing phone tag with Dave was not my first choice as it would waste our time. I thought I would consult the pros on here first. I agree flipping the bar shouldn't make a bit of difference but it was for me and I checked it many times, after all it's just common sense right? The tools and gauge are fine it's something else causing the different readings and most people maybe would not have double checked it. Well..I machined up everything today and set up for no float. I guess I'll see if I know how to use my tools after all. Thanks for the offer to help.
SPM
Pro
- Joined
- Nov 18, 2018
- Messages
- 150
- Age
- 57
- Location
- so. mn
- Country
- USA
- Snowmobile
- 2018 Sidewinder L-TX LE
I took an average of several of the readings and machined accordingly. I plan to recheck things after I get a few miles on and things find their home. Maybe the I.D of the bar that has to locate on a slight radius cast surface in secondary is just enough to change my readings. I'm sure these clutches vary a little and is why we're checking all this anyway.I don't think it's anything you're doing - I know of 2 others on this board that have found the same thing, different readings depending which way the bar is in. You're in the right place and "welcome". Sorry no one has the answer yet on what you and others are seeing. The net seems to be use it like Dave shows in the video and most all guys are ending up close to the same final settings. This season will be VERY telling with belt life reports. Many of us are outright praying the code has finally been cracked.
ClutchMaster
HUGE Member
- Joined
- Jan 18, 2016
- Messages
- 2,996
- Location
- tomahawk
- Country
- USA
- Snowmobile
- 2015 Viper 270 hurricane,
2002 Viper W/162 A.C. skid, SRX pipes &CDI, 780 BB
- LOCATION
- Wisconsin
Try taking a reading then rotating the secondary 180 degrees making the tool slip so it rotates also. Then take another reading at 180 degrees, is it the same?
SPM
Pro
- Joined
- Nov 18, 2018
- Messages
- 150
- Age
- 57
- Location
- so. mn
- Country
- USA
- Snowmobile
- 2018 Sidewinder L-TX LE
Yep, did that too and readings were pretty close until I flip the tool and check. Acts like the tool is not flat but it is. It doesn't change a lot, about .020 the alignment is off about 1mm and didn't have a shim from factory.Try taking a reading then rotating the secondary 180 degrees making the tool slip so it rotates also. Then take another reading at 180 degrees, is it the same?
Hammer70
GRIPNRIP
- Joined
- Sep 6, 2015
- Messages
- 824
- Location
- Niagara, Ontario.
- Country
- Canada
- Snowmobile
- 82SS440/96VMAX/02SRX/08APE/15SRVIPER/17SIDEWINDER
Welcome back I missed your infoTry taking a reading then rotating the secondary 180 degrees making the tool slip so it rotates also. Then take another reading at 180 degrees, is it the same?
Try taking a reading then rotating the secondary 180 degrees making the tool slip so it rotates also. Then take another reading at 180 degrees, is it the same?
Glad to see you returned.
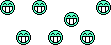
ClutchMaster
HUGE Member
- Joined
- Jan 18, 2016
- Messages
- 2,996
- Location
- tomahawk
- Country
- USA
- Snowmobile
- 2015 Viper 270 hurricane,
2002 Viper W/162 A.C. skid, SRX pipes &CDI, 780 BB
- LOCATION
- Wisconsin
Glad to be back! Just in time for the Holidays.Glad to see you returned.![]()

34pontiac
Expert
X2Welcome back I missed your info![]()
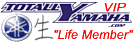

Beerman
I can actually hear myself getting fatter
- Joined
- Nov 22, 2004
- Messages
- 1,093
- Location
- Plymouth, MN
- Website
- www.loyalshepherd.com
- Country
- USA
- Snowmobile
- Sidewinder LTX-SE
- YOUTUBE
- arttyszka
Hang on boys, it's gonna be a bumpy ride! The Cluchmaster is back!Glad to be back! Just in time for the Holidays.
![]()
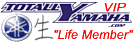

- Joined
- Nov 29, 2009
- Messages
- 1,230
- Age
- 49
- Location
- sabattus, maine
- Country
- USA
- Snowmobile
- 76 exciter, 87 phazer, 89 bravo, 00 srx x3, 01 srx, 02/04 viper, 06 ape
Welcome back ClutchmasterGlad to be back! Just in time for the Holidays.
![]()
Similar threads
- Replies
- 11
- Views
- 1K
- Replies
- 5
- Views
- 1K
- Replies
- 36
- Views
- 9K
-
This site uses cookies to help personalise content, tailor your experience and to keep you logged in if you register.
By continuing to use this site, you are consenting to our use of cookies.