Daveo99
Newbie
- Joined
- Jan 31, 2023
- Messages
- 6
- Reaction score
- 1
- Points
- 33
- Location
- Calamus Iowa
- Country
- USA
- Snowmobile
- Arctic Cat f7
What are some mistakes people make when engine dynoing and track dynoing that cause false reading? That will cause you to go down a path that you shouldn't have gone. I'm guessing the V-Max 800 made 135-140 hp to the track.Allen,
I know way back when I'd dyno these machines on the track dyno, (actually only used a track dyno twice really) but we'd use .57 as a factor from engine to track dyno figures. I remember having my brand new zero mile turbo Apex on Jeff Simons engine dyno, it was right about 264-265 HP, we'd hooked it right to the track dyno within minutes that same day and it showed first stab at the clutching of 144 Track HP and improved it to 149-150 Track HP with clutch refinements at that engine HP level. Why are people now using .5 as a factor on the track dyno? I always laughed at TD for using this figure.
According to that .5 factor, my old Apex turbo should have been 300 HP and it really wasn't that much at the engine, although I've always said that was the fastest turbo sled I have owned & trail rode too, till this tuned Winder, I feel they would be pretty close power wise in actuality, the Apex was 265 HP and the Winder is "supposed to be 300". I feel they must be very close to actual track HP thru my butt dyno. I know all that matters it what it really makes to the track. Just wondering if something has changed in the factors being used. I'm guessing its because people are not actually making the engine power they really say they are making. Engine numbers seem to be pretty inflated vs actual in this snowmobile world. Imagine that....
I also had my old V-Max 800 on the Wheelock's track dyno one day. Same thing, the factor I arrived at was .57 as I knew the real engine HP of that one too.
- Joined
- Apr 17, 2003
- Messages
- 5,473
- Reaction score
- 1,266
- Points
- 2,003
- Location
- Menno, SD
- Website
- www.ulmerracing.com
- Country
- USA
- Snowmobile
- 2014 Yamaha SR Viper LTX, 2014 Yamaha SR Viper RTX SE, 2015 Yamaha SR Viper MTX SE 162 (turbo), 2015 Yamaha SR Viper MTX SE 153
- LOCATION
- Menno, SD
- WEBSITE
- www.ulmerracing.com
What are some mistakes people make when engine dynoing and track dynoing that cause false reading? That will cause you to go down a path that you shouldn't have gone. I'm guessing the V-Max 800 made 135-140 hp to the track.
Big start angle on a helix will show a big dyno number on a track dyno.
A really quick acceleration rate on an engine dyno and how & where you start the run can fool an engine dyno as well.
Simplespeed
TY 4 Stroke Junkie
- Joined
- Jan 8, 2022
- Messages
- 644
- Reaction score
- 445
- Points
- 368
- Location
- 1191 Sauk Lane , Saginaw, Mi. 48638
- Country
- USA
- Snowmobile
- 2006 Apex , 2017 Sidewinder LTX -LE
interesting……good subject……
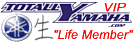

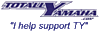
earthling
Lifetime Member
- Joined
- Dec 1, 2017
- Messages
- 2,022
- Reaction score
- 1,976
- Points
- 1,183
- Location
- Ontario
- Country
- Canada
- Snowmobile
- 2021 SRX
2006 ATTAK
Anything past 250 hp on the Sidewinder and the tongue is hanging out on the small turbo. I don't know that anyones horsepower claims are 100% accurate, also track pitch plays a factor too. 2.52 is the best for horsepower to the ground, bar none, the 2.86 or 3.0 pitch don't lay nearly the horsepower down as what 2.52 pitch will (even in the same lug height). I spent a week on a sled last season that showed 2 track hp increase from a 240 tune to a 270 tune. The 240 tune was an over achiever and the 270 was a under achiever. I also took a Sidewinder and added a MC Xpress upgrade kit (larger intercooler, larger turbo, different muffler to fit the MC Xpress turbo) and gained 20+ hp to the track set at identical boost numbers.
Theoretically the correction factor will make the weather a non-factor when dynoing, but a colder charge temp will certainly make more horsepower.
Here is a graph showing corrected vs uncorrected horsepower.
Not doubting your results but curious as to why you think this might be?
When you add driver lugs at any pitch, all you are doing is changing the number of times the drivers engage the track. On the one hand, more contact = more traction/friction between track surface and the driver. Given the same driver diameter, a 2.52 lug will contact the track more often than a 2.86, and a 3.0. Also in theory, you would make peak power with no cog on either the driver or the track. Two perfectly smooth surfaces and a tight track would have no gear meshing (no cogs on either driver or track) and you would make absolutely peak power. The size of the driver should have the biggest impact on losses as the translation in direction for the track as it goes around the dirver/wheels is where much of the energy is lost. To make peak power you would want to eliminate as many interference (friction/contact) points as possible and use large gears/drivers/idlers to avoid losses due to directional translations. I wonder if it just comes down to the fact that a 2.52 track is more flexible (more holes, less rubber).
- Joined
- Apr 17, 2003
- Messages
- 5,473
- Reaction score
- 1,266
- Points
- 2,003
- Location
- Menno, SD
- Website
- www.ulmerracing.com
- Country
- USA
- Snowmobile
- 2014 Yamaha SR Viper LTX, 2014 Yamaha SR Viper RTX SE, 2015 Yamaha SR Viper MTX SE 162 (turbo), 2015 Yamaha SR Viper MTX SE 153
- LOCATION
- Menno, SD
- WEBSITE
- www.ulmerracing.com
Not doubting your results but curious as to why you think this might be?
When you add driver lugs at any pitch, all you are doing is changing the number of times the drivers engage the track. On the one hand, more contact = more traction/friction between track surface and the driver. Given the same driver diameter, a 2.52 lug will contact the track more often than a 2.86, and a 3.0. Also in theory, you would make peak power with no cog on either the driver or the track. Two perfectly smooth surfaces and a tight track would have no gear meshing (no cogs on either driver or track) and you would make absolutely peak power. The size of the driver should have the biggest impact on losses as the translation in direction for the track as it goes around the dirver/wheels is where much of the energy is lost. To make peak power you would want to eliminate as many interference (friction/contact) points as possible and use large gears/drivers/idlers to avoid losses due to directional translations. I wonder if it just comes down to the fact that a 2.52 track is more flexible (more holes, less rubber).
Most of the 2.52 tracks are slightly heavier than the 2.86 or 3.0 equivalent (less track lugs in an equivalent 2.86 or 3.0 track).
120 2.86 track = 42 lugs
121 2.52 track = 48 lugs
128 2.52 track = 51 lugs
129 2.86 track = 45 lugs
136 2.52 track = 54 lugs
137 2.86 track = 48 lugs
141 3.0 track = 47 lugs
144 2.52 track = 57 lugs
146 2.82 track = 51 lugs
I do believe it has to do with the tracks ability to bend around the drivers and idlers and maintain it's shape.

PowderFalcon
Pinnin' it!
- Joined
- Jan 29, 2007
- Messages
- 990
- Reaction score
- 511
- Points
- 1,358
- Location
- Drumbo, ON
- Country
- Canada
- Snowmobile
- 2021 Sidewinder SRX
Not doubting your results but curious as to why you think this might be?
When you add driver lugs at any pitch, all you are doing is changing the number of times the drivers engage the track. On the one hand, more contact = more traction/friction between track surface and the driver. Given the same driver diameter, a 2.52 lug will contact the track more often than a 2.86, and a 3.0. Also in theory, you would make peak power with no cog on either the driver or the track. Two perfectly smooth surfaces and a tight track would have no gear meshing (no cogs on either driver or track) and you would make absolutely peak power. The size of the driver should have the biggest impact on losses as the translation in direction for the track as it goes around the dirver/wheels is where much of the energy is lost. To make peak power you would want to eliminate as many interference (friction/contact) points as possible and use large gears/drivers/idlers to avoid losses due to directional translations. I wonder if it just comes down to the fact that a 2.52 track is more flexible (more holes, less rubber).
Also worth noting the 2.52 is 3lbs heavier than 2.86. Additional rotating mass. No doubt, Allen's dyno doesn't lie!

PowderFalcon
Pinnin' it!
- Joined
- Jan 29, 2007
- Messages
- 990
- Reaction score
- 511
- Points
- 1,358
- Location
- Drumbo, ON
- Country
- Canada
- Snowmobile
- 2021 Sidewinder SRX
Not doubting your results but curious as to why you think this might be?
When you add driver lugs at any pitch, all you are doing is changing the number of times the drivers engage the track. On the one hand, more contact = more traction/friction between track surface and the driver. Given the same driver diameter, a 2.52 lug will contact the track more often than a 2.86, and a 3.0. Also in theory, you would make peak power with no cog on either the driver or the track. Two perfectly smooth surfaces and a tight track would have no gear meshing (no cogs on either driver or track) and you would make absolutely peak power. The size of the driver should have the biggest impact on losses as the translation in direction for the track as it goes around the dirver/wheels is where much of the energy is lost. To make peak power you would want to eliminate as many interference (friction/contact) points as possible and use large gears/drivers/idlers to avoid losses due to directional translations. I wonder if it just comes down to the fact that a 2.52 track is more flexible (more holes, less rubber).
Also worth noting the 2.52 is 3lbs heavier than 2.86. Additional rotating mass. No doubt, Allen's dyno doesn't lie!
Ahhh Allen beat me to it! ha
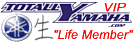

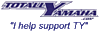
earthling
Lifetime Member
- Joined
- Dec 1, 2017
- Messages
- 2,022
- Reaction score
- 1,976
- Points
- 1,183
- Location
- Ontario
- Country
- Canada
- Snowmobile
- 2021 SRX
2006 ATTAK
Allen,
I know way back when I'd dyno these machines on the track dyno, (actually only used a track dyno twice really) but we'd use .57 as a factor from engine to track dyno figures. I remember having my brand new zero mile turbo Apex on Jeff Simons engine dyno, it was right about 264-265 HP, we'd hooked it right to the track dyno within minutes that same day and it showed first stab at the clutching of 144 Track HP and improved it to 149-150 Track HP with clutch refinements at that engine HP level. Why are people now using .5 as a factor on the track dyno? I always laughed at TD for using this figure.
According to that .5 factor, my old Apex turbo should have been 300 HP and it really wasn't that much at the engine, although I've always said that was the fastest turbo sled I have owned & trail rode too, till this tuned Winder, I feel they would be pretty close power wise in actuality, the Apex was 265 HP and the Winder is "supposed to be 300". I feel they must be very close to actual track HP thru my butt dyno. I know all that matters it what it really makes to the track. Just wondering if something has changed in the factors being used. I'm guessing its because people are not actually making the engine power they really say they are making. Engine numbers seem to be pretty inflated vs actual in this snowmobile world. Imagine that....
I also had my old V-Max 800 on the Wheelock's track dyno one day. Same thing, the factor I arrived at was .57 as I knew the real engine HP of that one too.
The .5 factor works the other way, it is a definition of losses from crank HP to final drive HP (track on snow). At .5, your apex would be .5*264 or 132 HP at the track. Any number used should be the sum of losses through the drivetrain. If TD is using .5 then it could be because the winder is less efficent at transfering power to the track. That may explain your butt dyno, if your winder doesn't feel that much stronger than your old vmax, the correction factors may be... correct. .5*300 = 150HP, .57*265=151HP. 1HP at that level is .6% (.006) change in power (you cannot feel 1HP) so they would feel similar. What would not feel similar is the area under the power curve, the 4s turbo will make power earlier and longer but an instantaneous response to a stab of the throttle (which is how a butt dyno works) will feel similar. The turbo gives the machine that feeling of relentless pull (area under the HP curve).
Last edited:
- Joined
- Apr 17, 2003
- Messages
- 5,473
- Reaction score
- 1,266
- Points
- 2,003
- Location
- Menno, SD
- Website
- www.ulmerracing.com
- Country
- USA
- Snowmobile
- 2014 Yamaha SR Viper LTX, 2014 Yamaha SR Viper RTX SE, 2015 Yamaha SR Viper MTX SE 162 (turbo), 2015 Yamaha SR Viper MTX SE 153
- LOCATION
- Menno, SD
- WEBSITE
- www.ulmerracing.com
The .5 factor works the other way, it is a definition of losses from crank HP to final drive HP (track on snow). At .5 correction factor, your apex would be .5*264 or 132 HP at the track. Any correction factor should be the sum of losses through the drivetrain. If TD is using .5 then it could be because the winder is less efficent at transfering power to the track. That may explain your butt dyno, if your winder doesn't feel that much stronger than your old vmax, the correction factors may be... correct. .5*300 = 150HP, .57*265=151HP. 1HP at that level is .6 of 1% (.006) change in power (you cannot feel 1HP) so they would feel similar. What would not feel similar is the area under the power curve, the turbo will make power earlier and longer but an instantaneous response to a stab of the throttle (which is how a butt dyno works) will feel similar. The turbo gives the machine that feeling of relentless pull (area under the HP curve).
I can't confirm it, only because I've never tried it, but I'm told that the Procross chassis twists & robs horsepower with the more power you put to it. A 400 hp Sidewinder in a stock chassis will only make 200 hp to the track, but put that same engine or power plant in a aftermarket rigid chassis and it'll make 210 + hp to the track. It may be (and it is more than likely) the fact that the Apex chassis was much more rigid than what the Procross chassis is.
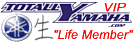

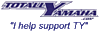
earthling
Lifetime Member
- Joined
- Dec 1, 2017
- Messages
- 2,022
- Reaction score
- 1,976
- Points
- 1,183
- Location
- Ontario
- Country
- Canada
- Snowmobile
- 2021 SRX
2006 ATTAK
I can't confirm it, only because I've never tried it, but I'm told that the Procross chassis twists & robs horsepower with the more power you put to it. A 400 hp Sidewinder in a stock chassis will only make 200 hp to the track, but put that same engine or power plant in a aftermarket rigid chassis and it'll make 210 + hp to the track. It may be (and it is more than likely) the fact that the Apex chassis was much more rigid than what the Procross chassis is.
That would explain a lot, thanks!

KnappAttack
24X ISR World Drag Racing Champion
- Joined
- Feb 19, 2004
- Messages
- 4,847
- Reaction score
- 6,113
- Points
- 1,733
- Location
- Welch MN
- Country
- USA
- Snowmobile
- 2023 Sidewinder LTX-LE
2017 Sidewinder LTX-LE
What are some mistakes people make when engine dynoing and track dynoing that cause false reading? That will cause you to go down a path that you shouldn't have gone. I'm guessing the V-Max 800 made 135-140 hp to the track.
I wouldn't know much about the track dyno because I've only spent a couple of days on them. Honestly, the track dyno never taught me anything other than I already had a prefect setup on the V-Max, which I knew already from the timers, but a grass dragger wanted to see if their clutch setup would be better, and it was a great winning grass racer that wanted to see if his theory's would be better. His setup would probably be great on the grass, but on ice not so much, my setup couldn't be improved upon on my V-Max 800 Pro-Stocker on the track dyno. I was able to gain knowledge on some different carburetor's & carb setups I had been working on. On the track dyno I was able to help confirm how the different carbs worked and reacted in the field. I spent 2 years making a set of new carbs work better than another set and making refinements to them before switching to them for racing. Like building my own clutch weight profiles too. Takes years to evolve things to make improvements on known setups. Track dyno can sure speed things up when testing things though vs running on the timers. It's a tool like many things are, but not the be all end all. Nothing is better than field testing, it just takes longer to do that.
I've have spent major time on engine dynos, many many days and dyno pulls on the engine dyno when developing parts and pieces, pipes ect. You can't fool an engine dyno unless you are off on the calibration or don't know what you are doing with it. Engine dyno however can fool you if you don't know what you are after or doing with it. A dyno operator can do any number of things to fool the public, but when the operator knows what they are doing and is honest with themselves, you cant mess it up.
The thing with a engine dyno is you tune the engine for the conditions of the day. In other words, you can build a warm weather engine calibration or a cold weather engine calibration, (high or low altitude same thing). You don't want to build an engine for ice racing and try and run it in the hot summer air and visa versa, at least a race engine anyway. Thats one way a guy could get fooled if you dont know what you are doing, or if running at high altitude or something like that. You can think you gained power in the warm poor summer air showing high corrected HP, but take that engine back into good winter air and the power will be down. Typically engines dynoed at high altitude or hot summer air days will show higher corrected HP as the SAE calibration is showing more corrected power because you tuned for the poor conditions. One needs to look at actual observed HP, because that is what you are really dealing with and showing the clutches and track, observed HP is the REAL HP for that day. For instance, say you have an average engine making 150 HP observed in the cold air at say 20F, take that same engine to 100F air, and observed will say be down to 140 HP, but corrected will still show 150HP, now you can correct for the poor less dense air and put bigger carbs on, maybe change the porting to move more air, a little more compression and timing and that engine will now show 160HP Corrected in that 100F air, but it now really makes 150HP observed instead of the previous 140HP observed. All you did was tune to the poor air conditions, but the corrected shows higher HP.....
If it's an engine builder selling engines, he now wants to sell that 160HP engine to the public as a real 160HP because thats the corrected HP right. Now take that that same 160 Corrected HP engine back to a 20F ice race and its a absolute turd, its setup for that 100F air. Put it on the dyno again at 20F and the observed power is down to say 135 HP because you tuned it for bad air previously, corrected HP is also way way down. Observed HP is what really matters ultimately. Corrected HP is not relevant to the machine its in. You can't race corrected HP figures. You need to tune the edge for the conditions of the day to make it the most efficient it can be. People get all caught up on corrected HP, and corrected HP does not win races, only actual observed HP wins races.
There are also certain conditions where you will make super HP like when theres a fog in the air right around 32F also. The engine likes the conditions and you can tune for that cold moisture and see an extra 10 HP. Above or below that temp and the power drops that 10 back to normal. Its almost like having meth injection at that freezing point, and you can lean things out or increase timing to get that power increase. Thats the best I can explain that phenomena anyway.
Also, on a two stroke you could say run hot pipes and a cold engine or something too, that will give good power readings. It important to dyno and test in similar conditions you are going to be competing in to bae able to optimize the tune up and design the edge for those conditions. When I dynoed, I made similar runs on the den the way we'd race them in the field, any other way and you are not getting good direct results.
Example of tuning for conditions: Many years ago when I was coming off John Noard's Anoka-Ramsey Sports Center dyno on that foggy 32F morning, Rick Ward was going on with his Pro-Stock bike to finalize calibrations and try and pick up some added power on his Pro-Stock bike engine. I asked him why in the world he'd be doing that in December's cold MN air. Well, they were heading to Florida to run a race down there and wanted to "really dial things in for the race". I mentioned to him that whatever he learned there in that cold winter dyno room would be irrelevant. Keep in mind I'm talking to Rick Ward, a guy I consider an absolute genius. He was "the man", he built the Pro-Stock motorcycle engines previously for Vance & Hines, a guy that then started his own performance shop of Ward Performance, a guy who cast and built the heads all the Pro-Stock bike guys were using at that time. He was a world beater in the Pro-Stock bike world. Here I was, a lowly two-stroke snowmobile engine builder telling a guy I consider a true four stroke Pro-Stock bike genius, he was making a mistake in doing this on that cold MN day, go figure. I must have have some balls doing that or have no filter, all right I have no filter.... maybe even on the spectrum a bit.....
I met with Rick a couple years later about building 4-stroke RX-1's for an asphalt drag race program Yamaha was thinking about doing at that time, he said to me, "you remember you told me I was crazy for tuning the bike in that cold weather". I said yes I remember. He says "you were absolutely right, we lost that race and it was because I tuned it on the dyno for those cold conditions, and it hurt me in the warmer Florida conditions". He said he'd learned his lesson and would never again dyno a race engine that was not in its element and the general conditions and parameters in which it was going to run in. I knew this because I had done just that with the two-strokes, I built different engines for summer and winter racing, and had already made these mistakes in taking them into the different environments than they were going to run in. I pushed one of my engine designed so hard on the dyno in the environment it wasn't built for, and ended up blowing it up pushing these boundaries and learning the lesson the hard way. It seems I alway have to learn stuff the hard way like that. I call it the school of hard knocks.....
Last edited:

KnappAttack
24X ISR World Drag Racing Champion
- Joined
- Feb 19, 2004
- Messages
- 4,847
- Reaction score
- 6,113
- Points
- 1,733
- Location
- Welch MN
- Country
- USA
- Snowmobile
- 2023 Sidewinder LTX-LE
2017 Sidewinder LTX-LE
The .5 factor works the other way, it is a definition of losses from crank HP to final drive HP (track on snow). At .5, your apex would be .5*264 or 132 HP at the track. Any number used should be the sum of losses through the drivetrain. If TD is using .5 then it could be because the winder is less efficent at transfering power to the track. That may explain your butt dyno, if your winder doesn't feel that much stronger than your old vmax, the correction factors may be... correct. .5*300 = 150HP, .57*265=151HP. 1HP at that level is .6% (.006) change in power (you cannot feel 1HP) so they would feel similar. What would not feel similar is the area under the power curve, the 4s turbo will make power earlier and longer but an instantaneous response to a stab of the throttle (which is how a butt dyno works) will feel similar. The turbo gives the machine that feeling of relentless pull (area under the HP curve).
Oh, a 300 HP winder would never ever run with my old Pro-Stock 800, even a 350 HP winder wouldn't cut it. That not what I'm saying, you are not picking up what I'm putting down here....
I had a Simon turbo setup on a old Attak, we dynoed it on the engine dyno, it made 265 HP on a brand new zero mile engine with 11.8 lbs of boost on the engine dyno, took it right off the engine dyno, installed it right onto the track dyno and it made 150 Track HP with a bit less boost at 11.0 lbs. within an hour of running it on the engine dyno. So the Apex made 150 track HP not 132 track HP. The .5 would not work properly here.
Now, if you use a factor of .5 like there are using now that would be equal to a 300 HP Winder. We always used a .57 factor previously. Suddenly TD only has a track dyno at their facility and starts using a .5 factor. I'm just trying to figure out why as the .57 was always the most accurate in the past, not the .5 factor. Everyone and their brother used .56-.57 previously. Now I'm hearing .5 all the time. I just question why the change.
Last edited:
Stubbs
TY 4 Stroke Master
- Joined
- Nov 7, 2006
- Messages
- 1,163
- Reaction score
- 677
- Points
- 1,378
- Location
- Uxbridge, On, Can.
- Country
- Canada
- Snowmobile
- ‘16 Apex XTX with 137” Mono II
+ other gooodies
- LOCATION
- Uxbridge ON
This is one of the best threads I’ve seen on TY in a long time, learning a bunch, thanks guys.

JLR
VIP Member
- Joined
- Dec 6, 2006
- Messages
- 77
- Reaction score
- 14
- Points
- 958
- Location
- Winnipeg, Mb
- Country
- Canada
- Snowmobile
- Currently, 2017 Arctic cat thundercat 2018 sidewinder xtx se 137 precision stage 4, 2025 Yamaha Srx bone stock
have you dynoed any with a tapp clutch as compared to stock yamaha clutch?That's a question I can't answer. All the sleds I have run have had the PEFI billet intake.
- Joined
- Apr 17, 2003
- Messages
- 5,473
- Reaction score
- 1,266
- Points
- 2,003
- Location
- Menno, SD
- Website
- www.ulmerracing.com
- Country
- USA
- Snowmobile
- 2014 Yamaha SR Viper LTX, 2014 Yamaha SR Viper RTX SE, 2015 Yamaha SR Viper MTX SE 162 (turbo), 2015 Yamaha SR Viper MTX SE 153
- LOCATION
- Menno, SD
- WEBSITE
- www.ulmerracing.com
have you dynoed any with a tapp clutch as compared to stock yamaha clutch?
I have not, I've never been fortunate enough to have the opportunity to work with a TAPP clutch yet.
Similar threads
- Replies
- 23
- Views
- 5K
- Replies
- 8
- Views
- 1K
-
This site uses cookies to help personalise content, tailor your experience and to keep you logged in if you register.
By continuing to use this site, you are consenting to our use of cookies.