
DGZRT
VIP Member
- Joined
- Feb 23, 2006
- Messages
- 1,181
- Location
- Stevens Point Wisconsin
- Country
- USA
- Snowmobile
- 2008 Vector shorty, 17 Shitdoo 1200X, 2000- pullmyass-340 for Grandkids
The amount of dedication to detail for this type of build is amazing!! Keep up the good work
Nikolai
TY 4 Stroke God
Thanks Cannondale, that helps a lot!
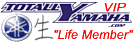

That link goes the wrong place now. Try this
https://ty4stroke.com/threads/crash-damage-and-repair-info-and-pics.145856/page-2#post-1333958
https://ty4stroke.com/threads/crash-damage-and-repair-info-and-pics.145856/page-2#post-1333958
Nikolai
TY 4 Stroke God
Welded up the shock mounts and double checked everything afterwards and they were crooked. The lower front PTO a-arm mount is slightly off as well(1/16 low). These pics will show what I did to double check them and how they are off. It’s dissapointing to waste that much time but it needs to be fixed. The previous setup I used to locate the shock mounts just wasn’t accurate or strong enough.
First two pics are the Mag side. This one came out vertically parallel, but not in the same plan horizontally.
Second two pics are the PTO side. This one came out the opposite. Parallel horizontally, but not vertically.
I’m going to completely redo the shock mounts and fix the front a-arm mount. I’m currently in the process of building an a-arm/shock jig to use in my jig. It will take a few days but I’m confident it will be my third and final solution.
First two pics are the Mag side. This one came out vertically parallel, but not in the same plan horizontally.
Second two pics are the PTO side. This one came out the opposite. Parallel horizontally, but not vertically.
I’m going to completely redo the shock mounts and fix the front a-arm mount. I’m currently in the process of building an a-arm/shock jig to use in my jig. It will take a few days but I’m confident it will be my third and final solution.
Last edited:
Nikolai
TY 4 Stroke God
Made some progress. Took awhile to make all the brackets(1.5 x .25 flatbar) and all the tube spacers (1.625 x .058) to fit over the 1/2” threaded rod. I still have some plating to do but the time consuming stuff is done.
Made a couple new a-arm bushings with .5” ID so I could install the a-arm over the threaded rod as a third way to check the shock mount positioning.
Made a couple new a-arm bushings with .5” ID so I could install the a-arm over the threaded rod as a third way to check the shock mount positioning.
You sure have alot of talent!
Nikolai
TY 4 Stroke God
Anchorage, Alaska had a 7.0 earthquake on Friday November 30th. I’m a service technician for the natural gas supplier and we pretty much worked non stopped for a week. Finally had today off to clean up the garage and get back to the sled. I didn’t make a lot of progress but I got my 2” x 1/4” pieces welded in.
You can see here the PTO side a-arm mount needs to be raised a little.
Double checking the shock mount position. It lines up with the one I had previously welded on so I’m calling it good.
Either Sunday or Monday I’ll fix the lower a-arm mounts on the PTO side and then redo the shock mounts.
You can see here the PTO side a-arm mount needs to be raised a little.
Double checking the shock mount position. It lines up with the one I had previously welded on so I’m calling it good.
Either Sunday or Monday I’ll fix the lower a-arm mounts on the PTO side and then redo the shock mounts.
Nikolai
TY 4 Stroke God
Fixed the PTO side a-arm mounts so they match the Mag side. They are now level left to right.
Made spacers to position the shock mount in the correct location.
Cut the old shock mounts short, got my frames swung out into the correct position and a brace tacked in place to hold them. I have a lot of bracing left to do before I tackle the shock mounts but I feel like I’m making forward process again. Right now everything is perfectly level and measures the same side to side.
Made spacers to position the shock mount in the correct location.
Cut the old shock mounts short, got my frames swung out into the correct position and a brace tacked in place to hold them. I have a lot of bracing left to do before I tackle the shock mounts but I feel like I’m making forward process again. Right now everything is perfectly level and measures the same side to side.
Nikolai
TY 4 Stroke God
Tack welded 2 more braces in place.
And FINALLY got to remove the old shock mounts and clean everything up.
Next step is to weld in the new shock mount towers.
And FINALLY got to remove the old shock mounts and clean everything up.
Next step is to weld in the new shock mount towers.
Nikolai
TY 4 Stroke God
Wrapped up the shock mounts tonight.
Welded my spacers to some 1” x 1/8” square tube
Somehow the shock mounts ended up an 1/8” high when I built the subframe. To fix this I used a combination of 1” and 1-1/4” square tube and some stainless steel shim stock, welded and braced the 1-1/4”, removed the subframe, them hammered down the 1” until it was the correct height and welded it to the 1-1/4”.
Getting the 1-1/4” positioned into the same spot on both sides.
So much work for a couple shock mounts.
And done!
Next up is jigging the steering arm location & running board angle.
Welded my spacers to some 1” x 1/8” square tube
Somehow the shock mounts ended up an 1/8” high when I built the subframe. To fix this I used a combination of 1” and 1-1/4” square tube and some stainless steel shim stock, welded and braced the 1-1/4”, removed the subframe, them hammered down the 1” until it was the correct height and welded it to the 1-1/4”.
Getting the 1-1/4” positioned into the same spot on both sides.
So much work for a couple shock mounts.
And done!
Next up is jigging the steering arm location & running board angle.
Last edited:
Nikolai
TY 4 Stroke God
I was going to copy the factory running board angle, but wanted to avoid having to put an extra bend in the lower tube after the rear suspension mount. One of my goals with this sled is the fewest amount of bends/cuts/welds necessary.
So I increased the running board angle a few degrees. I lowered it a little over stock up front so the rear wouldn’t be too high. You can see in these two pics how it will compare to a stock tunnel.
Tacked it up in the jig to take the guess work out when building the sled. The reason the 1” angle ends where it does is so I can weld in the bottom V-shaped tube for the rear suspension rear arm mount. I basically ended it where the factory rear bracket ties into the tunnel in the pic above.
The tunnel will be easy to fabricate just being a straight tube. I clamped a piece of 1” aluminum tube in place to give an idea of the taper. For some reason it looks steeper in the picture.
With the tunnel done, I started on the driveshaft. I’m building a removable jig support for the driveshaft so I can get the chaincase on and off that side.
Hoping to get the driveshaft locked in tomorrow.
So I increased the running board angle a few degrees. I lowered it a little over stock up front so the rear wouldn’t be too high. You can see in these two pics how it will compare to a stock tunnel.
Tacked it up in the jig to take the guess work out when building the sled. The reason the 1” angle ends where it does is so I can weld in the bottom V-shaped tube for the rear suspension rear arm mount. I basically ended it where the factory rear bracket ties into the tunnel in the pic above.
The tunnel will be easy to fabricate just being a straight tube. I clamped a piece of 1” aluminum tube in place to give an idea of the taper. For some reason it looks steeper in the picture.
With the tunnel done, I started on the driveshaft. I’m building a removable jig support for the driveshaft so I can get the chaincase on and off that side.
Hoping to get the driveshaft locked in tomorrow.
Last edited:
Nikolai
TY 4 Stroke God
Got the driveshaft position jigged today. It’s located exactly where it will end up in the tube chassis(both vertically and horizontally) and perfectly straight/parallel with the rear suspension mounts. Made the chaincase side mount removable so the chaincase can be installed/removed while the tube chassis is being put together.
After setting my mocked up drivetrain at 15.5625” (This will be the ID of the tube chassis) I pulled my measurements & made a spacer on the lathe out of 1-1/4” pipe and tack welded it to some 1/4” flatstock. I had to tack weld an additional piece of 1/4” flatstock to the top because the gear is recessed in about 1/8” from the outside of the inner chaincase half. The whole idea is to be able to remove the mount, install the chaincase and gear, tighten everything down, and have it be in the correct spot.
With the chaincase side done, I had to remake the spacer for the clutch side. Once the chaincase is bolted in I’ll have to make a new narrower spacer for the clutch side as the lower gear doesn’t sit flush on the end of the driveshaft which will push the driveshaft over alittle. I did account for this, so i should have said that once the chaincase is installed, then the driveshaft will be in the right spot L to R.
More to come...
After setting my mocked up drivetrain at 15.5625” (This will be the ID of the tube chassis) I pulled my measurements & made a spacer on the lathe out of 1-1/4” pipe and tack welded it to some 1/4” flatstock. I had to tack weld an additional piece of 1/4” flatstock to the top because the gear is recessed in about 1/8” from the outside of the inner chaincase half. The whole idea is to be able to remove the mount, install the chaincase and gear, tighten everything down, and have it be in the correct spot.
With the chaincase side done, I had to remake the spacer for the clutch side. Once the chaincase is bolted in I’ll have to make a new narrower spacer for the clutch side as the lower gear doesn’t sit flush on the end of the driveshaft which will push the driveshaft over alittle. I did account for this, so i should have said that once the chaincase is installed, then the driveshaft will be in the right spot L to R.
More to come...
Last edited:
Nikolai
TY 4 Stroke God
Got the drivetrain finished tonight. I was off a 1/16 on my width so I had to cut the welds and swap my 1/4” spacer for a 3/16 washer I had.
Cut the 1/8” aluminum pieces to the shape I wanted for now. I made them small so they’d be out of the way for mocking up the rear motor mounts.
Clamped square tube to the jig to make sure chaincase was properly set and width was correct. Did the clutch side after the chaincase side. As posted before, it’s set at 15.5625” between the tube work which is also the OD of the alu plates.
And done
Installed the secondary to check clearance to the bearing. I have a different bearing retainer coming that will center the bearing in the plate.
Probably won’t do much for a few days. I need to dig out my flex connectors and header and get the motor prepped for placement in the jig.
Cut the 1/8” aluminum pieces to the shape I wanted for now. I made them small so they’d be out of the way for mocking up the rear motor mounts.
Clamped square tube to the jig to make sure chaincase was properly set and width was correct. Did the clutch side after the chaincase side. As posted before, it’s set at 15.5625” between the tube work which is also the OD of the alu plates.
And done
Installed the secondary to check clearance to the bearing. I have a different bearing retainer coming that will center the bearing in the plate.
Probably won’t do much for a few days. I need to dig out my flex connectors and header and get the motor prepped for placement in the jig.
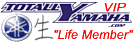

sxr70001
Lifetime Member
- Joined
- Dec 4, 2010
- Messages
- 1,129
- Location
- Michigan
- Country
- USA
- Snowmobile
- Sidewinder LTX SE
SR Viper RTX SE
Nice work! It's starting to look recognizable to the average joe, like me.
Nikolai
TY 4 Stroke God
Spent the last couple days doing a big clean and reorganize of the garage. Today I made a cardboard rear tunnel section the length of a 153 and clamped it at the same taper and height as the swidewinder tunnel. I did this so when positioning the motor I can make sure the header is angled up enough.
Then I cleaned the motor and set it in place. It’s not exactly where it needs to be but it’s close. I need about 7” from the center of the driveshaft to the oil filter. Once I get that then I’ll angle the motor until the header angle is correct. Then roll the chaincase for/aft until I get the correct clutch centers(10.5” I believe). Should be pretty straight forward.
Then I cleaned the motor and set it in place. It’s not exactly where it needs to be but it’s close. I need about 7” from the center of the driveshaft to the oil filter. Once I get that then I’ll angle the motor until the header angle is correct. Then roll the chaincase for/aft until I get the correct clutch centers(10.5” I believe). Should be pretty straight forward.
Similar threads
- Replies
- 4
- Views
- 4K
- Replies
- 32
- Views
- 5K
-
This site uses cookies to help personalise content, tailor your experience and to keep you logged in if you register.
By continuing to use this site, you are consenting to our use of cookies.