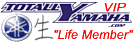

Dusty Dan
Lifetime Member
- Joined
- Jan 24, 2015
- Messages
- 211
- Country
- Canada
- Snowmobile
- 2016 SRViper LTX LE
2012 Vector
I have yet to replace my original M20 hyfax and I have close to 4000 miles on them.![]()
That's really good to hear. Man, I'm just itching to get at it, patience has never been one of my virtues.
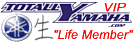

Redbeard
Lifetime Member
- Joined
- Oct 14, 2011
- Messages
- 1,662
- Location
- IN
- Country
- USA
- Snowmobile
- 2012 Apex, 136 M20, PB80
2008 Vector, 136 M20, PB80
Post your work as you go! 

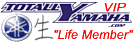

Dusty Dan
Lifetime Member
- Joined
- Jan 24, 2015
- Messages
- 211
- Country
- Canada
- Snowmobile
- 2016 SRViper LTX LE
2012 Vector
Post your work as you go!![]()
I'll do my best NS, but it will not be the quality or as extensive as you have done. I purposely went for the easy setup for at least the first year so that the installation would be simple. My snowmobiling is too important to me to waste time in the shop doing repairs during the season. I even put off a Cat Scan that I was supposed to do in February......delayed it until late March. Kinda gives you an idea of my passion, although it doesn't say a lot for my brains.
After next year I will rethink how far I want to take it.
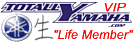

Redbeard
Lifetime Member
- Joined
- Oct 14, 2011
- Messages
- 1,662
- Location
- IN
- Country
- USA
- Snowmobile
- 2012 Apex, 136 M20, PB80
2008 Vector, 136 M20, PB80
Here’s another update regarding an issue I’ve had with the external check valve mounted to my Viair 90 compressor:
Since trip one (December 2013), I’ve had an issue with the check valve freezing at night and not allowing the compressor to build pressure (page 11, post 157). After some engine heat was generated, the valve would thaw out and let air pass through. This past winter, the problem got worse! We rode in some exceptionally cold weather and there were a few mornings I thought the valve would never open. All this got me thinking of ways to electrically heat the valve and thaw it out; maybe a thumb throttle or hand grip heater. Then spring came and the thought went on the back shelf.
A few weeks ago, I started experimenting with a thumb heater powered from my Apex battery. I placed the compressor in my freezer overnight to simulate winter temps. Speaker wire was used from the battery outside to the compressor and heater inside. Next morning, the valve was frozen and the compressor would not build pressure. I powered the heater for 5 minutes, but it wasn't enough to thaw the valve. I set everything outside to thaw for 15 minutes and then it would work. I ran the overnight test again without the valve and the compressor instantly started building pressure, but slowly leaked off air pressure. Finally, I disassembled the valve and discovered the inside was full of corrosion and the steel hose fitting had rust in it! The valve body is made from brass, so I imagine the corrosion is not only from moisture, but the marriage of dissimilar metals as well (brass valve, aluminum compressor, steel fittings).
After realizing the valve was finished, I started re-thinking my approach to the issue; my sled already has solenoids stacked together to hold air pressure, so why not run without a check valve this winter and see how I get along?! I still believe a secondary check valve is important, but maybe not as important for my particular application…time will tell.
For those of you having the same issue, I would recommend replacing the brass valve with a stainless steel valve; I’m keeping one with me just in case!
Since trip one (December 2013), I’ve had an issue with the check valve freezing at night and not allowing the compressor to build pressure (page 11, post 157). After some engine heat was generated, the valve would thaw out and let air pass through. This past winter, the problem got worse! We rode in some exceptionally cold weather and there were a few mornings I thought the valve would never open. All this got me thinking of ways to electrically heat the valve and thaw it out; maybe a thumb throttle or hand grip heater. Then spring came and the thought went on the back shelf.
A few weeks ago, I started experimenting with a thumb heater powered from my Apex battery. I placed the compressor in my freezer overnight to simulate winter temps. Speaker wire was used from the battery outside to the compressor and heater inside. Next morning, the valve was frozen and the compressor would not build pressure. I powered the heater for 5 minutes, but it wasn't enough to thaw the valve. I set everything outside to thaw for 15 minutes and then it would work. I ran the overnight test again without the valve and the compressor instantly started building pressure, but slowly leaked off air pressure. Finally, I disassembled the valve and discovered the inside was full of corrosion and the steel hose fitting had rust in it! The valve body is made from brass, so I imagine the corrosion is not only from moisture, but the marriage of dissimilar metals as well (brass valve, aluminum compressor, steel fittings).
After realizing the valve was finished, I started re-thinking my approach to the issue; my sled already has solenoids stacked together to hold air pressure, so why not run without a check valve this winter and see how I get along?! I still believe a secondary check valve is important, but maybe not as important for my particular application…time will tell.
For those of you having the same issue, I would recommend replacing the brass valve with a stainless steel valve; I’m keeping one with me just in case!
Last edited:
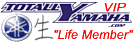

Dusty Dan
Lifetime Member
- Joined
- Jan 24, 2015
- Messages
- 211
- Country
- Canada
- Snowmobile
- 2016 SRViper LTX LE
2012 Vector
Another great post NS. I guess I will be looking for a stainless check valve.Here’s another update regarding an issue I’ve had with the external check valve mounted to my Viair 90 compressor:
Since trip one (December 2013), I’ve had an issue with the check valve freezing at night and not allowing the compressor to build pressure (page 11, post 157). After some engine heat was generated, the valve would thaw out and let air pass through. This past winter, the problem got worse! We rode in some exceptionally cold weather and there were a few mornings I thought the valve would never open. All this got me thinking of ways to electrically heat the valve and thaw it out; maybe a thumb throttle or hand grip heater. Then spring came and the thought went on the back shelf.
A few weeks ago, I started experimenting with a thumb heater powered from my Apex battery. I removed the compressor from my sled and placed it in a freezer overnight to try and simulate winter temps. Speaker wire was used from the battery outside the freezer to the compressor and heater inside. Next morning, I could not get the compressor to make pressure, so I powered the heater for 5 minutes and it still would not make pressure. Guessing the thumb heater was not hot enough, I set everything outside to thaw for 15 minutes and it would work. I didn't have a spare hand grip heater, so I ran the test again without the valve and the compressor would build pressure after being frozen all night. Finally, I disassembled the valve and discovered the inside was full of corrosion and rust! The valve body is made from brass, so I imagine the corrosion is not only from moisture, but the marriage of dissimilar metals as well (brass valve, aluminum compressor, steel fittings).
After realizing the valve was finished, I started re-thinking my approach to the issue; my sled already has solenoids stacked together to hold air pressure, so why not run without a check valve this winter and see how I get along?! I still believe a secondary check valve is important, but maybe not as important for my particular application…time will tell.
For those of you having the same issue, I would recommend replacing the brass valve for a stainless steel valve and move it next to a good heat source inside the engine compartment...not too hot though! I’m keeping a stainless valve with me just in case.
View attachment 108832 View attachment 108833 View attachment 108834 View attachment 108835 View attachment 108836 View attachment 108838
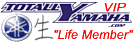

Redbeard
Lifetime Member
- Joined
- Oct 14, 2011
- Messages
- 1,662
- Location
- IN
- Country
- USA
- Snowmobile
- 2012 Apex, 136 M20, PB80
2008 Vector, 136 M20, PB80
Another great post NS. I guess I will be looking for a stainless check valve.
Maybe my corroded valve is an isolated case, but either way, I think a stainless check valve is a good idea!
When I reworked my broken compressor a few weeks ago, the check valve in head was corroded as well...and it had never been on the snow! That's probably why it quit holding air just sitting in the shop. I just don't trust that valve by itself without a secondary valve.
Last edited:
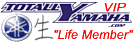

Dusty Dan
Lifetime Member
- Joined
- Jan 24, 2015
- Messages
- 211
- Country
- Canada
- Snowmobile
- 2016 SRViper LTX LE
2012 Vector
For sure I will get one, thanks.Maybe my corroded valve is an isolated case, but either way, I think a stainless check valve is a good idea!
When I reworked my old, broken compressor a few weeks ago, the check valve in head was corroded as well...and it had never been on the snow! That's probably why it quit holding air just sitting in the shop. I just don't trust that valve by itself without a secondary valve.
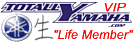

Soldier'spapa
Lifetime Member
- Joined
- Mar 21, 2006
- Messages
- 729
- Location
- Naperville, IL
- Country
- USA
- Snowmobile
- 2018 Sidewinder Ltx LE 50th Anniversary
Guys, just to add to the "frozen check valve" problem... I too have experienced the stuck valve in the morning syndrome. My check valve is a stainless one supplied by Fast. I opened it up to find no corrosion. I have no solenoids inline so will need to keep it in place. I found that a few warm breaths would be enough to thaw it in the mornings. Hope this helps.
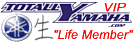

Dusty Dan
Lifetime Member
- Joined
- Jan 24, 2015
- Messages
- 211
- Country
- Canada
- Snowmobile
- 2016 SRViper LTX LE
2012 Vector
Guys, just to add to the "frozen check valve" problem... I too have experienced the stuck valve in the morning syndrome. My check valve is a stainless one supplied by Fast. I opened it up to find no corrosion. I have no solenoids inline so will need to keep it in place. I found that a few warm breaths would be enough to thaw it in the mornings. Hope this helps.
I think I might add a couple of drops of light oil occasionally, should not hurt anything and might help. Compressors are notorious for picking up moisture, especially in mild weather.
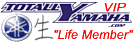

Redbeard
Lifetime Member
- Joined
- Oct 14, 2011
- Messages
- 1,662
- Location
- IN
- Country
- USA
- Snowmobile
- 2012 Apex, 136 M20, PB80
2008 Vector, 136 M20, PB80
Doug, is your check valve from FAST 1/8" NPT threads? The new stainless valve I purchased is 1/4". I was hoping the larger diameter would be more forgiving? Also, the cracking pressure on the stainless valve is 2 psi. I can blow through it and it will open. I can't do that with the original valve. I'm still going to run without it to start with.Guys, just to add to the "frozen check valve" problem... I too have experienced the stuck valve in the morning syndrome. My check valve is a stainless one supplied by Fast. I opened it up to find no corrosion. I have no solenoids inline so will need to keep it in place. I found that a few warm breaths would be enough to thaw it in the mornings. Hope this helps.
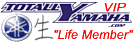

Soldier'spapa
Lifetime Member
- Joined
- Mar 21, 2006
- Messages
- 729
- Location
- Naperville, IL
- Country
- USA
- Snowmobile
- 2018 Sidewinder Ltx LE 50th Anniversary
Doug, is your check valve from FAST 1/8" NPT threads? The new stainless valve I purchased is 1/4". I was hoping the larger diameter would be more forgiving? Also, the cracking pressure on the stainless valve is 2 psi. I can blow through it and it will open. I can't do that with the original valve. I'm still going to run without it to start with.
Joe, yes my valve is 1/8".
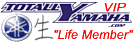

Redbeard
Lifetime Member
- Joined
- Oct 14, 2011
- Messages
- 1,662
- Location
- IN
- Country
- USA
- Snowmobile
- 2012 Apex, 136 M20, PB80
2008 Vector, 136 M20, PB80
I finally drug my Apex out to get it ready for the season. Everything was in pieces from my freezer experiment, and it was...well...still laying next to the freezer! LOL
I re-installed the pump without an external check valve for now. I had to stack some extra fittings in place to make up for the air line not being long enough to reach. As mentioned earlier, I don't think running without an external check valve would be possible without the solenoids I have stacked together. I'll know after the first ride.
If this passes the test, I'll have my local hydraulic shop make a new, correct length hose so I can get rid of the extra fittings on the pump.
I re-installed the pump without an external check valve for now. I had to stack some extra fittings in place to make up for the air line not being long enough to reach. As mentioned earlier, I don't think running without an external check valve would be possible without the solenoids I have stacked together. I'll know after the first ride.
If this passes the test, I'll have my local hydraulic shop make a new, correct length hose so I can get rid of the extra fittings on the pump.
rossow1
Newbie
I am still running 2004 M10. It has been in 5 different sleds before I installed it this fall in my 07. Nothing compares to ride quality!
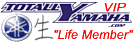

Redbeard
Lifetime Member
- Joined
- Oct 14, 2011
- Messages
- 1,662
- Location
- IN
- Country
- USA
- Snowmobile
- 2012 Apex, 136 M20, PB80
2008 Vector, 136 M20, PB80
I am still running 2004 M10. It has been in 5 different sleds before I installed it this fall in my 07. Nothing compares to ride quality!
Would you mind posting any pictures of your sled and/or pictures of your installation?
I've got an m20 in my nytro and can't keep up with dusty Dan on the trails! Mine is a 121" and I'm wondering where people are at for psi.. I was trying 60lbs, it feels like I could go lower but the set in is too much if I do I think.. I'm 180lbs anyone have any feedback/tips for me?
Similar threads
- Replies
- 20
- Views
- 8K
- Replies
- 46
- Views
- 150K
- Replies
- 4
- Views
- 33K
-
This site uses cookies to help personalise content, tailor your experience and to keep you logged in if you register.
By continuing to use this site, you are consenting to our use of cookies.