This is great post and I'm sure if my driveshaft fails i will to be going this route no doubt. I think Justin brings up a great point in the fact that we've seen so many failures along the way that we tend to dismiss the OEM upgrades without giving them a chance to succeed. I'll be the first to admit i pull out many parts without thinking twice that end up in the dumpster. We'll put the bandaid aftermarket quick fix in just as preventative maintenance and quite frankly how can you blame us since our time on these sleds is so limited with warm winters and marginal conditions. Unfortunately we've been conditioned to expect failures and we as a whole have found ways to remove doubt and instill confidence in the machines that we pay dearly for. Will we ever get a brand we can have full confidence in that gives us the power and ride we have come to love?
No
No
Last edited:
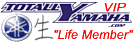

justinator
Lifetime Member
- Joined
- Mar 25, 2007
- Messages
- 1,476
- Reaction score
- 1,178
- Points
- 1,438
- Location
- Maine
- Country
- USA
- Snowmobile
- 2023 Arctic Cat Riot 9000
Thats exactly it, I decided to try it out with no protective measures after reading the results from the metallurgy testing on the newer updated shafts. I figured id try it out and see what happens. Im pretty observant so its not like I would of ran a driveshaft to the point of causing other issues but much to my surprise every time I inspect it…….its same as new. I am certainly not trying to discourage anyone from the other fixes available but if you got a new sled or new shaft and not sure what to do or havent had the best luck with previous fixes I wouldnt stress much about it and just go enjoy the sled.
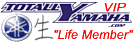

Turboflash
Lifetime Member
- Joined
- Mar 18, 2019
- Messages
- 2,756
- Reaction score
- 2,798
- Points
- 1,113
- Location
- Southern MN
- Country
- USA
- Snowmobile
- '17 ZR9000 Ltd. 137 - PEFI Stage 4
For those who may not have seen it, Travis H at BOP created a template for a puller for the caliper housing (with bearing in it) for use when one presses the bearing on. No need for a center bolt because the plate just pushes on the end of the track shaft. If you print this template at 100% scale, you can just lay it on your chosen piece of 1/4 thick steel and make one easily. PDF for template is attached.
For some reason, Arctic Cat also makes one. Since their design doesn't use a bearing that's pressed on, I'm not sure why they have this tool. Cat p/n is 0744-067. Country Cat now shows this tool as no longer available. Since plate pushes on end of track shaft, the center threaded bolt isn't necessary.
For those who may not want to have to remove the belly pan plastics to use press tool BP shows, I made my press tool threaded rod in 3 pieces so I can install one piece at a time (without having to remove any plastics) and they thread together to create the rod length needed. The hexagonal nuts are threaded all the way through. I welded one end to threaded rod to keep them from turning so I could thread the next piece on. See pic attached.
For some reason, Arctic Cat also makes one. Since their design doesn't use a bearing that's pressed on, I'm not sure why they have this tool. Cat p/n is 0744-067. Country Cat now shows this tool as no longer available. Since plate pushes on end of track shaft, the center threaded bolt isn't necessary.
For those who may not want to have to remove the belly pan plastics to use press tool BP shows, I made my press tool threaded rod in 3 pieces so I can install one piece at a time (without having to remove any plastics) and they thread together to create the rod length needed. The hexagonal nuts are threaded all the way through. I welded one end to threaded rod to keep them from turning so I could thread the next piece on. See pic attached.
Attachments
Big Pussy
Extreme
- Joined
- Apr 12, 2016
- Messages
- 95
- Reaction score
- 73
- Points
- 453
- Location
- Woodstock, Ont
- Country
- Canada
- Snowmobile
- 2015 XF7000 LXR
The long threaded rod is to put the shaft together, not take it apart. I push on a shouldered round plate as well to get the caliper off. This can be done with the chaincase fully assembled to simply service the left bearing.For those who may not have seen it, Travis H at BOP created a template for a puller for the caliper housing (with bearing in it) for use when one presses the bearing on. No need for a center bolt because the plate just pushes on the end of the track shaft. If you print this template at 100% scale, you can just lay it on your chosen piece of 1/4 thick steel and make one easily. PDF for template is attached.
For some reason, Arctic Cat also makes one. Since their design doesn't use a bearing that's pressed on, I'm not sure why they have this tool. Cat p/n is 0744-067. Country Cat now shows this tool as no longer available. Since plate pushes on end of track shaft, the center threaded bolt isn't necessary.
View attachment 177019
For those who may not want to have to remove the belly pan plastics to use press tool BP shows, I made my press tool threaded rod in 3 pieces so I can install one piece at a time (without having to remove any plastics) and they thread together to create the rod length needed. The hexagonal nuts are threaded all the way through. I welded one end to threaded rod to keep them from turning so I could thread the next piece on. See pic attached.
Once you take the plastic off and replace the rivets with screws, you can pull the plastic in 5 minutes with 9 screws a side. It is far easier to drain engine oil and take the chaincase apart. A lot less messy too.
No long threaded rod used here. BTW, the shouldered push plug also works on the chaincase side with a regular 3-jaw puller to pull the bearing off. Double use of the same piece. If you are going to make some jigs, make them versatile.

100MPH
VIP Member
- Joined
- Oct 11, 2024
- Messages
- 14
- Reaction score
- 6
- Points
- 133
- Location
- Badger State
- Country
- USA
- Snowmobile
- 2020 Yamaha SRX LE
2004 Yamaha RX-1 L
2003 Yamaha 700 SX Viper ER
1997 Yamaha 700 SX
1994 Yamaha V-Max4
1991 Yamaha Exciter2 LE
1983 Yamaha Bravo
This post keeps getting more and more informative thanks again for sharing all of your knowledge.
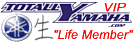

Turboflash
Lifetime Member
- Joined
- Mar 18, 2019
- Messages
- 2,756
- Reaction score
- 2,798
- Points
- 1,113
- Location
- Southern MN
- Country
- USA
- Snowmobile
- '17 ZR9000 Ltd. 137 - PEFI Stage 4
Yes, long threaded rod is to assemble. Presses caliper housing (with bearing) onto track shaft (have to have deep cup to go over track shaft and sized to contact inner race of bearing). Push caliper housing onto shaft until bearing contacts inner snap ring. Can be done with chain case fully assembled. Just remove speedo magnet plug. I do this annually when I'm inspecting chain case components, etc. So, chain case is removed.
Been using original track shaft since day one (2017). No sign of slipping. Change bearing about every 2-3 years "just because" although I'm confident just regreasing it is enough. I took out what I consider low-end bearing Cat uses (Peer) at my first maintenance cycle and installed an electric motor quality SKF even though the Peer seemed OK.
The whole key to this is spray weld, grind track shaft to interference fit with bearing so track shaft can never spin in bearing. Will last "forever." And, since there is no driveshaft saver, the shaft is exactly centered in bearing so no vibration, no centering needed, no having to carefully tighten shaft saver to keep concentricity. Shaft turns smoothly, freely, and on center. No rotor wobbling, no tunnel flexing. Ad BP posted, it's the ultimate fix for this major design flaw in procross chassis.
Been using original track shaft since day one (2017). No sign of slipping. Change bearing about every 2-3 years "just because" although I'm confident just regreasing it is enough. I took out what I consider low-end bearing Cat uses (Peer) at my first maintenance cycle and installed an electric motor quality SKF even though the Peer seemed OK.
The whole key to this is spray weld, grind track shaft to interference fit with bearing so track shaft can never spin in bearing. Will last "forever." And, since there is no driveshaft saver, the shaft is exactly centered in bearing so no vibration, no centering needed, no having to carefully tighten shaft saver to keep concentricity. Shaft turns smoothly, freely, and on center. No rotor wobbling, no tunnel flexing. Ad BP posted, it's the ultimate fix for this major design flaw in procross chassis.

twyztid
VIP Member
- Joined
- Feb 14, 2011
- Messages
- 986
- Reaction score
- 494
- Points
- 1,078
- Location
- Middleville, MI
- Country
- USA
- Snowmobile
- 2025 Sidewinder LTX LE EPS
2017 Sidewinder LTX SE
2012 Apex XTX
2012 RS Vector LTX
- LOCATION
- Middleville, MI
I would possibly be interested in this... but I don't think I would want stainless steel bolts.We have to talk about it. What parts would you all like to buy ?
CNC seal plate with gasket and stainless bolts and thick washers.
Richard Hodgins
Expert
- Joined
- Mar 5, 2019
- Messages
- 266
- Reaction score
- 262
- Points
- 638
- Location
- Ottawa ontario
- Country
- Canada
- Snowmobile
- Yamaha powered CAT
Interesting thread for sure and a lot of work to make these parts. The Hi-Tech Mechanical kit has been my choice recently as it adds a second bearing to the brake caliper side and also has a re-inforcing plate similar to the design here. I have to say that I'm not sure the chaincase side has been an issue in the past, yes that bearing MAY not have the same clearance but I dont think we've seen any failures because of this even if it does occasionally spin.
I have seen another fix that someone else did where they cut up an old caliper and used it in on the inside of the tunnel to add a second bearing as well and this was also a fix in the sense that it re-inforced the tunnel and spread the load over 2 bearings so the shaft never had wearing afterwards.
Anyways, kudos to coming up with this!
I have seen another fix that someone else did where they cut up an old caliper and used it in on the inside of the tunnel to add a second bearing as well and this was also a fix in the sense that it re-inforced the tunnel and spread the load over 2 bearings so the shaft never had wearing afterwards.
Anyways, kudos to coming up with this!
Similar threads
- Replies
- 40
- Views
- 3K