
hibshman25
Vendor
- Joined
- Sep 25, 2005
- Messages
- 2,865
- Age
- 40
- Location
- Lebanon, PA 17042
- Country
- USA
- Snowmobile
- 2017 sidewinder ltx dx
2018 snoscoot
A customer/vendor that uses the Yamaha engines in another application has developed a new water pump impeller. After oem failed in 10 hrs on his Turbo 998, he tried an aftermarket one only to have it fail within 2 hrs. This design uses a billet impeller like others but with fewer vanes for less MMOI. In addition the shaft design also sets it apart from the others. The pin holes weaken the shaft, so he integrated a key into the shaft to eliminate the pin concept altogether. These will be available at a promotion price of $180 initially to get a bunch out in circulation.
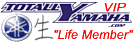

STAIN
Lifetime Member
- Joined
- Feb 29, 2004
- Messages
- 4,197
- Location
- Vermont
- Country
- USA
- Snowmobile
- 2022 SIDEWINDER LTX GT
- LOCATION
- Vermont
How long has this one been tested for?
Do the fewer vanes equal less coolant flow?
Do the fewer vanes equal less coolant flow?
Snowbound98
Expert
- Joined
- Mar 11, 2019
- Messages
- 268
- Age
- 47
- Location
- Chicagoland
- Country
- USA
- Snowmobile
- 2015 SR Viper M-TX 153
Figures this would pop up a mere week after I bought a new billet impeller. I would have bought it and tried it.

KnappAttack
24X ISR World Drag Racing Champion
- Joined
- Feb 19, 2004
- Messages
- 4,695
- Location
- Welch MN
- Country
- USA
- Snowmobile
- 2023 Sidewinder LTX-LE
2017 Sidewinder LTX-LE
How long has this one been tested for?
Do the fewer vanes equal less coolant flow?
Cutting half the vanes off the impeller was a trick I employed to cut pumping losses on my drag sled engines. Lots of guys ran with no pumps or circulation for one blast, but I wanted SOME coolant flowing thru the engine.
Not going to speak for the manufacturer of this piece, but I wouldn’t want reduced flow of coolant thru thie 998. Coolant flow is extremely important to prevent deto and keeping the head and block cool, especially on a boosted trail sled. I’d prefer a factory duplication of the impeller in my 998. Coolant flow is key to preventing hot spots and keeping things cool.

hibshman25
Vendor
- Joined
- Sep 25, 2005
- Messages
- 2,865
- Age
- 40
- Location
- Lebanon, PA 17042
- Country
- USA
- Snowmobile
- 2017 sidewinder ltx dx
2018 snoscoot
Vendor has 39 flight hours on this impeller and about 4 hours of flow and pressure testing on a stand. He builds for aviation applications and is very meticulous with his work. I will try and get ahold of his test data to see how it compares to stock pump capacity.How long has this one been tested for?
Do the fewer vanes equal less coolant flow?

kinger
VIP Member
The number of vanes has no impact on flow this could be 1 vane if was designed right and still flow the same amount. I would not put any stake in fewer vanes means less flow, if you know anything about fluid dynamics there are a lot of ways to make this work.
Kuddos to the engineer on this, if it's used in aviation you can bet he needs more flow as the load on the engine is consistent vs in a sled with the on/off we are on the throttle. Imagine being on a lake at 70-90mph for 34 hours...This thing is circulating coolant.
Kuddos to the engineer on this, if it's used in aviation you can bet he needs more flow as the load on the engine is consistent vs in a sled with the on/off we are on the throttle. Imagine being on a lake at 70-90mph for 34 hours...This thing is circulating coolant.
The number of vanes has no impact on flow this could be 1 vane if was designed right and still flow the same amount. I would not put any stake in fewer vanes means less flow, if you know anything about fluid dynamics there are a lot of ways to make this work.
Kuddos to the engineer on this, if it's used in aviation you can bet he needs more flow as the load on the engine is consistent vs in a sled with the on/off we are on the throttle. Imagine being on a lake at 70-90mph for 34 hours...This thing is circulating coolant.
Sure, you could use 1 vane but you don't see too many single vaned turbo impellers for a reason
Planes are not snowmobiles, they have more natural room for cooling, and probably due to reasons of efficiency, they tend to run in a narrow(er) RPM range. More cooling surface, less variance in RPM, and just differing environmental conditions can all lead to a solution that works well for one use case and not so much for another.
I suspect that the reason the OEM design exists is because an engineer decided to prioritize low to cruising RPM performance, which is why the stock impeller has a complete backing surface and more vanes (semi-closed vane design), and maximized vane surface area so that from idle on up it will grab and move more coolant and provide adequate head pressure and volumetric flow. Intuitively, you will probably not get as much efficiency from a semi-open vane design which are primarily used for higher RPM applications or pumping coarse materials. A lower vane count coupled to an semi-open vane design (the design in question) will be most efficient at higher RPMs.
It may be a wholly adequate design and any improvement on strength would be welcome but on the surface, and judging only by the pictures, I would certainly like to see the new design compared to the old one across varying RPM, that would put all of the questions to bed.
Last edited:
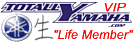

1nc 2000
Lifetime Member Tim
- Joined
- Feb 26, 2010
- Messages
- 3,072
- Location
- Marquette, MI
- Country
- USA
- Snowmobile
- Yamaha FX Nytro RTX SE
This is an issue brought on by cat for Yamaha.
Same impeller in the japan sleds with no issues.
Coolant system is a closed system with the cap being the pressure relief for expansion into the overflow tank and vise versa when cooling.
Cat uses cheap worm clamps on the hoses that leak as where yamaha (jap sleds) use constant tension hose clamps.
Coolant leaks out and air leaks into the system not letting the system work as designed leaving air pockets in the coolant.
The air pockets and then coolant hitting the stock impeller damages them.
Keep all hose clamps tight and cold full level maintained also making sure no air under cap.
Best if maintained properly since new otherwise buy an aftermarket impeller....
Same impeller in the japan sleds with no issues.
Coolant system is a closed system with the cap being the pressure relief for expansion into the overflow tank and vise versa when cooling.
Cat uses cheap worm clamps on the hoses that leak as where yamaha (jap sleds) use constant tension hose clamps.
Coolant leaks out and air leaks into the system not letting the system work as designed leaving air pockets in the coolant.
The air pockets and then coolant hitting the stock impeller damages them.
Keep all hose clamps tight and cold full level maintained also making sure no air under cap.
Best if maintained properly since new otherwise buy an aftermarket impeller....
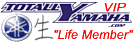

Turboflash
Lifetime Member
- Joined
- Mar 18, 2019
- Messages
- 2,508
- Location
- Southern MN
- Country
- USA
- Snowmobile
- '17 ZR9000 Ltd. 137 - PEFI Stage 4
Agree completely on coolant flow in head on 998, especially on boosted sleds. IMO, cooling capacity (the ability to absorb and carry away BTU's) is based on total surface area of cooling passages inside head (area of coolant contacting aluminum). There's a designed capacity with "safety margin". Also, surface area of heat exchangers is integral part of system's ability to shed heat. When we boost power (put in a tune) that adds heat to equation. We can only add so much heat before it exceeds the capacity of system. In our real works on snow, that means we can only run WOT for so much time. If engine is stock, that's one time. If engine is boosted, that means less time. Assuming water pump is functioning as designed (flow rate) we can still exceed the ability of total system to shed heat. Wr don't want coolant going through system too fast as then it will not have time to absorb heat in head. We don't want coolant circulating too slow as then it overheat (maybe boil) coolant in head. Detailed testing is needed to determine what right flow is at the designed/intended heat load. So without that testing, it's difficult to determine if impellers with less vanes, or more open or closed vanes are betterCutting half the vanes off the impeller was a trick I employed to cut pumping losses on my drag sled engines. Lots of guys ran with no pumps or circulation for one blast, but I wanted SOME coolant flowing thru the engine.
Not going to speak for the manufacturer of this piece, but I wouldn’t want reduced flow of coolant thru thie 998. Coolant flow is extremely important to prevent deto and keeping the head and block cool, especially on a boosted trail sled. I’d prefer a factory duplication of the impeller in my 998. Coolant flow is key to preventing hot spots and keeping things cool.
max rolph
Expert
- Joined
- Feb 10, 2021
- Messages
- 453
- Age
- 61
- Location
- horse shoe valley
- Country
- Canada
- Snowmobile
- 998 turbo
i changed mine last winter for insurance purpose to the ones used on desert race 998 turbos UTV, looks and worked perfect. like a piece of artwrk.

74Nitro
VIP Member
- Joined
- Feb 18, 2013
- Messages
- 5,265
- Age
- 52
- Location
- Dublin Ontario
- Country
- Canada
- Snowmobile
- 2019 Sidewinder LTX
I have yet to see one one fail, maybe just a matter of time. I don't even know of anyone that has had one fail, except for on this site.

twyztid
VIP Member
- Joined
- Feb 14, 2011
- Messages
- 861
- Location
- Middleville, MI
- Country
- USA
- Snowmobile
- 2017 Sidewinder LTX SE - TD Power Trail, CAI, 3" Super Quiet
2012 RS Vector
2006 Apex GT
- LOCATION
- Middleville, MI
I have one of the Dasa Racing bullet impellers in 17 LTX SE. I bought the sled used with 350 miles on it and installed the impeller before ever riding the sled (installed a PowerTrail Tune, CAI, and 3" Super Quiet muffler at the same time). My brother-in-law has had 2 of the stock impellers fail on his PEFI tuned 17 ZR9000. I have over 3000 miles on the sled now and haven't had any issues.
By the way, there is another on the market that is about twice the cost of the Dasa unit and also doesn't use pin holes drilled in the shaft... but the impeller part is basically the same as Dasa's.
By the way, there is another on the market that is about twice the cost of the Dasa unit and also doesn't use pin holes drilled in the shaft... but the impeller part is basically the same as Dasa's.
Similar threads
- Replies
- 15
- Views
- 7K
- Replies
- 2
- Views
- 2K
- Replies
- 327
- Views
- 55K
- Replies
- 21
- Views
- 36K
-
This site uses cookies to help personalise content, tailor your experience and to keep you logged in if you register.
By continuing to use this site, you are consenting to our use of cookies.