Nikolai
TY 4 Stroke God
So I wanted to the get the rear section of the tunnel done next, but I want to figure out the cooling first so I can build the tunnel around the cooler and vise versa. I want to try and minimize redundant parts as much as possible.
Ive been thinking about the cooling the last few days and ways to simplify it. I’ve decided to run coolant thru the my 1” lower running board tubes so I don’t have to run tubes inside the tunnel. Less weight and parts. My plan is to use as much as the frame tubing as possible. This is what I’m thinking right now but nothing is set in stone.
Coolant will go thru the rear cooler, down the clutch side running board into the water pump. Where the running board tube meets the cross tube under the motor, I’ll weld a short tube on a 45 degree angle and put holes in the tubes so coolant can flow thru. The blue tape represents the tube and the aluminum stub would be where the coolant hose attaches to feed the water pump.
I’m going to use the factory T-stat
I have two ways of the doing the chaincase side. The hose to the running board from the top of the T-stat will be the same either way. The bypass hose going from the bottom of the t-stat can be done two ways.
#1 I just weld a 1” stub to the cross tube and run a hose down along the front angled tube
#2 I put holes in both the lower cross tube and the angled tube and then weld a fitting joining the tubes and weld a stub to the top of the angled tube by the a-arm mount and use the angled tube to supply coolant instead of a long hose. Definitely a lot more work to eliminate this one hose.
Coolant routing. Blue would be with the T-stat open. Orange would be T-stat closed using the frame tubes for the bypass.
It would be more work to weld all the stubs in vs using coolant hoses everywhere but it would be significantly cleaner and less weight. Anyway, that’s where I’m at. Still trying to make a decision.
Ive been thinking about the cooling the last few days and ways to simplify it. I’ve decided to run coolant thru the my 1” lower running board tubes so I don’t have to run tubes inside the tunnel. Less weight and parts. My plan is to use as much as the frame tubing as possible. This is what I’m thinking right now but nothing is set in stone.
Coolant will go thru the rear cooler, down the clutch side running board into the water pump. Where the running board tube meets the cross tube under the motor, I’ll weld a short tube on a 45 degree angle and put holes in the tubes so coolant can flow thru. The blue tape represents the tube and the aluminum stub would be where the coolant hose attaches to feed the water pump.
I’m going to use the factory T-stat
I have two ways of the doing the chaincase side. The hose to the running board from the top of the T-stat will be the same either way. The bypass hose going from the bottom of the t-stat can be done two ways.
#1 I just weld a 1” stub to the cross tube and run a hose down along the front angled tube
#2 I put holes in both the lower cross tube and the angled tube and then weld a fitting joining the tubes and weld a stub to the top of the angled tube by the a-arm mount and use the angled tube to supply coolant instead of a long hose. Definitely a lot more work to eliminate this one hose.
Coolant routing. Blue would be with the T-stat open. Orange would be T-stat closed using the frame tubes for the bypass.
It would be more work to weld all the stubs in vs using coolant hoses everywhere but it would be significantly cleaner and less weight. Anyway, that’s where I’m at. Still trying to make a decision.
Last edited:
It's been done before, and it works fairly well. check UP Bushman's posts on this forum. I think he's done something similar to a Phazer MTX, but I can't remember if he ran coolant through the tubing in the running boards or just installed heat exchangers underneath the running boards. In any event, I think your idea will work.
You could run an even smaller exchanger if you could find some moly tubing extrusions with built-in heat sinks. Here's a couple examples of aluminum extrusions:
You could run an even smaller exchanger if you could find some moly tubing extrusions with built-in heat sinks. Here's a couple examples of aluminum extrusions:




Last edited:
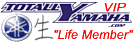

mysledblows
Lifetime Member
- Joined
- Jan 23, 2007
- Messages
- 371
- Location
- Central MN
- Country
- USA
- Snowmobile
- Sidewinder, mcx phazer, phazer, apex
- LOCATION
- Jenkins, MN
I have an apex with the extrusion/coolant running in the running board edge. Works great but after sliding down the tar road on its side for a bit I did burn a hole through the extrusion and need to weld up the leak. Something to keep in mind if you occasionally find yourself in such situations
Nikolai
TY 4 Stroke God
OVR40D, I will look for his post, thanks.
I have a coworker who’s a mechanical engineer and I’ve been picking his brain a lot. He suggested only making the holes 3/4 and still using 1” tube for the connections to retain the strength in the tube so I think that’s what I’ll do. I’ll probably start on them tonight and try to get the cooling system done next.
I have a coworker who’s a mechanical engineer and I’ve been picking his brain a lot. He suggested only making the holes 3/4 and still using 1” tube for the connections to retain the strength in the tube so I think that’s what I’ll do. I’ll probably start on them tonight and try to get the cooling system done next.
Nikolai
TY 4 Stroke God
I got the rear tunnel section done and it absolutely whooped my butt. Too many late nights.
I was originally going to build it all using 3/4 x .035 round tube but decided to use some left over 1 x 1/2 x .035 rectangle since it’s so much stiffer. Got all the tubes notched and cut, everything clamped and welded it. The 1/2” square was for riveting the cooler to.
Everything went great until it was fully welded and I went to install it and realized I swapped the rectangle left to right so my notches were off. The notches are offset in the 1x1/2 so they were specific to each side. I was able to re-notch it but it now put my 1/2” square tube too close to the 1” round tube. Since I’m riveting the cooler extrusion to the top, this would not work, no room to pull rivets. Huge bummer at this point.
So after thinking about it awhile, I decided to replace the 1/2” square tube with 1x1/2” rectangle, and just remove the 1” tube all together. This saved me about .2 lbs and I can now rivet both the cooler extrusion and tunnel skin to it. Bumper is nothing fancy, I wanted to keep it as strong as possible so I went the ugly route and just welded in a straight 3/4 x .035 tube.
I’m going a little light on the tubework on purpose as I’m trying to get strength out of multiple parts. The gas tank will be .080 welded aluminum and be structural to the upper pyramid. I’d rather build the chassis on the light side and add bracing later, than build it unnecessarily heavy to begin with.
For the cooler, I decided to scrap the idea of 2 small coolers stacked on top of each other, and instead will make about a 24” long double pass cooler. The extrusion will rivet directly to the top of the 1x1/2 rectangle on the front and both sides. The extrusion will be semi structural and the cooler will take up the entire space which saves weight not having to use tunnel skin on the back.
Took forever to get the rear section secured so it was straight with the rest of the chassis. I over welded and slightly warped my jig so I have to account for few things being slightly off as I build. Definitely learning a lot.
I’ve got the tubing for the rear suspension mounts and running boards to do next.
I was originally going to build it all using 3/4 x .035 round tube but decided to use some left over 1 x 1/2 x .035 rectangle since it’s so much stiffer. Got all the tubes notched and cut, everything clamped and welded it. The 1/2” square was for riveting the cooler to.
Everything went great until it was fully welded and I went to install it and realized I swapped the rectangle left to right so my notches were off. The notches are offset in the 1x1/2 so they were specific to each side. I was able to re-notch it but it now put my 1/2” square tube too close to the 1” round tube. Since I’m riveting the cooler extrusion to the top, this would not work, no room to pull rivets. Huge bummer at this point.
So after thinking about it awhile, I decided to replace the 1/2” square tube with 1x1/2” rectangle, and just remove the 1” tube all together. This saved me about .2 lbs and I can now rivet both the cooler extrusion and tunnel skin to it. Bumper is nothing fancy, I wanted to keep it as strong as possible so I went the ugly route and just welded in a straight 3/4 x .035 tube.
I’m going a little light on the tubework on purpose as I’m trying to get strength out of multiple parts. The gas tank will be .080 welded aluminum and be structural to the upper pyramid. I’d rather build the chassis on the light side and add bracing later, than build it unnecessarily heavy to begin with.
For the cooler, I decided to scrap the idea of 2 small coolers stacked on top of each other, and instead will make about a 24” long double pass cooler. The extrusion will rivet directly to the top of the 1x1/2 rectangle on the front and both sides. The extrusion will be semi structural and the cooler will take up the entire space which saves weight not having to use tunnel skin on the back.
Took forever to get the rear section secured so it was straight with the rest of the chassis. I over welded and slightly warped my jig so I have to account for few things being slightly off as I build. Definitely learning a lot.
I’ve got the tubing for the rear suspension mounts and running boards to do next.
Last edited:
Nikolai
TY 4 Stroke God
Couldn’t decide what to do for drop brackets so I kept it simple and did 3/4 x .035 straight tubes. I cut two pieces of 1” bar stock, drilled 3/8 holes and bolted them to the jig. The 3/4 is held to it by two tack welds each. I did this to hold the chassis while welding. Once it’s fully welded, I’ll cut the tack welds and remove the pieces of bar stock, put the chassis in the jig and use 1-1/4” x .058 tubing for the mounts. The larger tube will allow me to notch into the 3/4 tube joint another 1/8” to correct for any misalignment/warping from welding.
I’m going to add gussets to brace the 3/4 and rectangle together. Paper is not the final template, still working on a design. So far I’m meeting my weight goal, I have .28 lbs allotted for both gussets.
I will do gussets and the running boards next.
I’m going to add gussets to brace the 3/4 and rectangle together. Paper is not the final template, still working on a design. So far I’m meeting my weight goal, I have .28 lbs allotted for both gussets.
I will do gussets and the running boards next.

zx4ever
VIP Member
- Joined
- Apr 14, 2011
- Messages
- 331
- Location
- Northern BC canada
- Country
- Canada
- Snowmobile
- 08 nytro ty4stroke customized
Nikolai
TY 4 Stroke God
For now I’m not going to, I don’t think it will look good with how I ran the rest of the tubing. The 1x1/2 rectangle is pretty strong stuff and with the extrusion riveted to it I think it will be ok. The weak point will be where it is welded to the 1” tube which I’ll gusset.
That being said, when the sled is completely done and sitting on the shop floor, I’ll lift up/push down on the rear and twist it and depending on how much it flexes I may add a tube. I’m just not ready to do it yet.
That being said, when the sled is completely done and sitting on the shop floor, I’ll lift up/push down on the rear and twist it and depending on how much it flexes I may add a tube. I’m just not ready to do it yet.
Nikolai
TY 4 Stroke God
I’ve got a bunch of extra .090 4130 plate, so I think I’m going to make the gusset larger and cut out out the center to keep the weight down. Thinking something like this...
Nikolai
TY 4 Stroke God
Weight is for both .090 gussets. Definitely heavier than the .28 lbs I wanted. Either going to have to live with it, drill some holes in the portion of the gusset that lays against the rectangle, or do something else. Leaning towards living with it since they took a few hours to make.
Nikolai
TY 4 Stroke God
Got them a little lighter, going to call it good. I have no idea how much strength they really add and how well the rear bumper will hold up but I’ll find out when I ride.
Going to work on the running boards next.
Going to work on the running boards next.
Nikolai
TY 4 Stroke God
Old running board cut up. I originally planned 3 lbs for the running boards. If I can make them for 2.5 lbs then that will help make up for the rear tunnel coming out heavier and put me back on track.
My weight goal was sub 20 lbs from the steering hoop forward(including drivetrain mounts, motor mounts, and steering post mount). And sub 20 lbs for the tunnel(including tunnel skin, exhaust shields and seat).
My weight goal was sub 20 lbs from the steering hoop forward(including drivetrain mounts, motor mounts, and steering post mount). And sub 20 lbs for the tunnel(including tunnel skin, exhaust shields and seat).
Last edited:

kinger
VIP Member
How about try a foot peg or two and call it good? One for sitting one for standing. Awhile back you made some flat stock and ran them as grips in the board, what if you took two of them ran them parallel to the tunnel maybe the length of your boot one or two of them on the foot pegs to give you a little traction and leverage.
Do you need the strength for the tunnel?
Do you need the strength for the tunnel?
Nikolai
TY 4 Stroke God
I don’t believe I need the strength from running boards but I don’t think it would hurt either since the 1” tube is unsupported for so long.
Nikolai
TY 4 Stroke God
Started building a jig for the boards. Looking at doing them a couple ways.
1. Lightest option that ties into the lower rear suspension mount tube.
2. Slightly heavier but outer board will taper in and tie into the upper rear suspension mount tube. If I did the boards this way then I’d probably run a small tube to help brace the suspension mount(if necessary)
1. Lightest option that ties into the lower rear suspension mount tube.
2. Slightly heavier but outer board will taper in and tie into the upper rear suspension mount tube. If I did the boards this way then I’d probably run a small tube to help brace the suspension mount(if necessary)
Similar threads
- Replies
- 4
- Views
- 5K
- Replies
- 32
- Views
- 5K
-
This site uses cookies to help personalise content, tailor your experience and to keep you logged in if you register.
By continuing to use this site, you are consenting to our use of cookies.