In your tunnel mock-up with aluminum, have you thought about using pyramidal framing like the photo below? It's just an example, but you might be able to do something similar and still position the tubing far enough behind the running boards to be out of your way. The front half of the tunnel could be wrapped over the top tubes.

Nikolai
TY 4 Stroke God
I have not thought about that. It’s an interesting idea. I’m open to whatever design is the strongest and lightest haha.
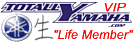

Snowman871
Lifetime Member
- Joined
- Feb 9, 2010
- Messages
- 278
- Reaction score
- 67
- Points
- 1,028
- Location
- Woodville, WI
- Country
- USA
- Snowmobile
- 2024 Polaris Assault 850
Thanks for sharing all this, it's a lot of fun to see it go together! I'm really hoping to have the time and ability to do custom fab work inside of my motorsports hobbies at some point a few years out.
I've been so busy with my own construction projects I can't even seem to make time for my float skid swap!
I've been so busy with my own construction projects I can't even seem to make time for my float skid swap!

Nikolai
TY 4 Stroke God
Finally used the bender for the first time since converting it to air/hydraulic and it’s worth every penny and then some. For anyone with a JD2 bender I’d highly recommend it.
You can slowly bump the ram until the tube just barely gets tight in the dies, and then position the tube to whatever angle you want and bend it. It also holds the tube tight throughout bending so if you want to stop and check the bend against a protractor you can. You also have the ability to literally bend in 1/4 degree increments while watching the degree finder since you don’t have to hold onto the bender. Really can’t explain how awesome it is over manual bending which is all I’ve done in the past.
I got the lower tubes bent tonight. Should have them notched and fit tomorrow.
You can slowly bump the ram until the tube just barely gets tight in the dies, and then position the tube to whatever angle you want and bend it. It also holds the tube tight throughout bending so if you want to stop and check the bend against a protractor you can. You also have the ability to literally bend in 1/4 degree increments while watching the degree finder since you don’t have to hold onto the bender. Really can’t explain how awesome it is over manual bending which is all I’ve done in the past.
I got the lower tubes bent tonight. Should have them notched and fit tomorrow.
Nikolai
TY 4 Stroke God
Got the lower 1 x .058 tubes fit and tacked. The tubing at the rear bend was left long. That will get cut tomorrow when I tack the cross tube behind the compressor.
These joints will be gusseted at a later date.
The tube is lower than the chaincase so the chaincase should be protected from any kind damage in the event I hit something. This is one of the reasons the bottom tube is .058. I also used thicker wall tube as my running boards won’t have much outer support and I wanted to keep the tunnel tubing to a minimum.
I need to get some more 1 x .035 tomorrow and I’ll do the tube behind the compressor next. I have no idea what I’m going to do for rear suspension mounts yet but I’ll worry about that after the steering hoop and drivetrain are done.
These joints will be gusseted at a later date.
The tube is lower than the chaincase so the chaincase should be protected from any kind damage in the event I hit something. This is one of the reasons the bottom tube is .058. I also used thicker wall tube as my running boards won’t have much outer support and I wanted to keep the tunnel tubing to a minimum.
I need to get some more 1 x .035 tomorrow and I’ll do the tube behind the compressor next. I have no idea what I’m going to do for rear suspension mounts yet but I’ll worry about that after the steering hoop and drivetrain are done.
Nikolai
TY 4 Stroke God
I got the tunnel height set exactly where I wanted and then tacked my 1 x .035 rear tube in place. I’m going to use a .050 tunnel skin so I placed a scrap of .050 aluminum on top of the header mount and then a heavy piece of square tube on top of that to simulate the top of the tunnel. I then bolted a tab to the motor mount and ran a string line and adjusted it until the string line was parallel with the header mount. The header will bolt directly to the skin.
Getting a rough idea of where it needed to go.
Fit and tacked. String line will be the finished top of the tunnel. It looks tall(and it is) but it’s the same as my Nytro and this tunnel will be narrower and still have angled corners like the oem tunnel.
Flex joint clearance is tight but there will be a separate piece covering the flex joints and I can raise it a little.
Parallel with the header mount.
Turbo will sit in the tunnel about the same amount as it did on my Nytro.
Compressor clearance. Just enough to still have some aluminum left behind it after cutting the hole in the skin.
Getting a rough idea of where it needed to go.
Fit and tacked. String line will be the finished top of the tunnel. It looks tall(and it is) but it’s the same as my Nytro and this tunnel will be narrower and still have angled corners like the oem tunnel.
Flex joint clearance is tight but there will be a separate piece covering the flex joints and I can raise it a little.
Parallel with the header mount.
Turbo will sit in the tunnel about the same amount as it did on my Nytro.
Compressor clearance. Just enough to still have some aluminum left behind it after cutting the hole in the skin.
Nikolai
TY 4 Stroke God
I’m happy the tunnel height is all figured out and set, that was another big hurdle to be done with. Next thing I’m going to work on are the 1” tubes that will be the back of the steering hoop.
I crunched some numbers again and I don’t think I’ll be under 40 lbs with the tunnel and inner chaincase half. I’m trying to build it as light as possible(while strong) but I think I’ll be closer to 45 lbs. Still should get me close to 400 lbs finished.
I crunched some numbers again and I don’t think I’ll be under 40 lbs with the tunnel and inner chaincase half. I’m trying to build it as light as possible(while strong) but I think I’ll be closer to 45 lbs. Still should get me close to 400 lbs finished.
Nikolai
TY 4 Stroke God
I was curious if I could run a couple straight 3/4 x .035 tubes from the rear 1” joint to the steering hoop without hitting my legs so I made some plywood running boards. My legs actually clear pretty well. I’m going to think about it for a few days before I weld anything in place. It would make the entire structure incredibly strong, just a matter of making sure they won’t be annoying while riding.
If I welded those in, then I would not do the 1 x 1/2 rectangle on the side of the tunnel. If I don’t do the 3/4 round tubes, then I would weld in the 1 x 1/2 rectangle on the sides. I would rather do the round tubes to keep the sides of the tunnel clean. The 3/4 round tubes would also make doing a turbo support easy.
But then for the gas tank, I’d have to weld a gas tank that could slide in from the side under the 3/4 tubes.
So many decisions
If I welded those in, then I would not do the 1 x 1/2 rectangle on the side of the tunnel. If I don’t do the 3/4 round tubes, then I would weld in the 1 x 1/2 rectangle on the sides. I would rather do the round tubes to keep the sides of the tunnel clean. The 3/4 round tubes would also make doing a turbo support easy.
But then for the gas tank, I’d have to weld a gas tank that could slide in from the side under the 3/4 tubes.
So many decisions

Nikolai
TY 4 Stroke God
After riding the sled some more I decided to go ahead and run the 3/4 x .035 tubes. Luckily it’s just steel so if I find it annoying after a few rides I can cut and modify them. I only had enough tube to do one side for now. I ran the string lines so I would know where the corner of the tunnel would be so I could lower the rear part of the 3/4 tube as much as possible.
This will make supporting the turbo super easy. I’m going to run a 3/4 x .035 tube in front of the exhaust flange which will also tie in the long tubes. I’m going to utilize an exhaust flange bolt and weld a tab to the 3/4 tube. So the turbo will be supported by the flange and I get to eliminate 1 additional fastener. This tube will also help support a seat.
I was originally going to do the steering hoop in 1 x .058 but since I added those long tubes I’m going to reduce the hoop and all chaincase/clutch support tubes down to 3/4 x .049. And since the tunnel will no longer be structural at all, I can use a .040 skin instead of .050 and save more weight. All these changes should get me close to a 40 lb chassis again.
I think I spend more time thinking then fabbing
This will make supporting the turbo super easy. I’m going to run a 3/4 x .035 tube in front of the exhaust flange which will also tie in the long tubes. I’m going to utilize an exhaust flange bolt and weld a tab to the 3/4 tube. So the turbo will be supported by the flange and I get to eliminate 1 additional fastener. This tube will also help support a seat.
I was originally going to do the steering hoop in 1 x .058 but since I added those long tubes I’m going to reduce the hoop and all chaincase/clutch support tubes down to 3/4 x .049. And since the tunnel will no longer be structural at all, I can use a .040 skin instead of .050 and save more weight. All these changes should get me close to a 40 lb chassis again.
I think I spend more time thinking then fabbing

Nikolai
TY 4 Stroke God
Got the other 3/4 x .035 tube tacked in place and also the 3/4 x .035 tube that will help support the turbo.
For the turbo, I’ll probably make a thin 4130 plate that will bolt to a couple of the exhaust flange bolts and tie the two 3/4 tubes together. This will not get made until the chassis is fully welded. Same with the motor mounts, drivetrain plates, steering post mount, rear suspension mounts and a few other items. Plan is to weld what I can in the jig, pull the chassis and finish weld it, then put it back in the jig and complete the above items.
I’m going to start on the steering hoop tubes next which will be 3/4 x .049
For the turbo, I’ll probably make a thin 4130 plate that will bolt to a couple of the exhaust flange bolts and tie the two 3/4 tubes together. This will not get made until the chassis is fully welded. Same with the motor mounts, drivetrain plates, steering post mount, rear suspension mounts and a few other items. Plan is to weld what I can in the jig, pull the chassis and finish weld it, then put it back in the jig and complete the above items.
I’m going to start on the steering hoop tubes next which will be 3/4 x .049
Nikolai
TY 4 Stroke God
Figured out where the steering hoop tubes needed to go(as far forward as possible) and then added to the jig to hold the tubes in place. This took a bit to level both sides to make sure the tubes would be perpendicular to the drive and jack shafts as well as staying 15-9/16 between the tubes. I wanted to jig the hoop tubes to keep everything straight and the same right to left.
This is my plan for the tubes for now. The bend will be as low as possible while still clearing the string line which is the edge of the first bend of my tunnel.
There will also be a 3/4 tube that runs across the tunnel behind the flex joints that will tie the steering hoop tubes together and also give me something to rivet the front of the tunnel to.
This is my plan for the tubes for now. The bend will be as low as possible while still clearing the string line which is the edge of the first bend of my tunnel.
There will also be a 3/4 tube that runs across the tunnel behind the flex joints that will tie the steering hoop tubes together and also give me something to rivet the front of the tunnel to.

kinger
VIP Member
- Joined
- Jan 17, 2005
- Messages
- 7,410
- Reaction score
- 1,547
- Points
- 1,963
- Location
- Clear Lake, IA
- Website
- www.piergenius.com
Awesome! I want to build my own 4cyl powered someday so I plan on using this thread as a reference!
Nikolai
TY 4 Stroke God
Hoop tubes fit and tacked.
3/4” tube is offset on the 1” tube at the bottom so everything will be flush on the inside.
I’m using a buddies really nice mandrel bender for the 3/4. It has bullets for bending .035 and .049 and does a tight radius with almost no wrinkling.
3/4” tube is offset on the 1” tube at the bottom so everything will be flush on the inside.
I’m using a buddies really nice mandrel bender for the 3/4. It has bullets for bending .035 and .049 and does a tight radius with almost no wrinkling.
Last edited:
Nikolai
TY 4 Stroke God
A few pics from setting up for the 3/4 x .035 tube. I bolted a piece of .040 aluminum sheet to the header so I could get the height of the 3/4 tube correct.
Tacked in place.
The tunnel skin will end at and rivet to the tube. Eventually I’ll end up bending aluminum sheet similar to the Nytro to enclose the flex joints.
I’ll probably start thinking about how I’m going to run the tubes around the clutch and chaincase next.
Tacked in place.
The tunnel skin will end at and rivet to the tube. Eventually I’ll end up bending aluminum sheet similar to the Nytro to enclose the flex joints.
I’ll probably start thinking about how I’m going to run the tubes around the clutch and chaincase next.
Nikolai
TY 4 Stroke God
Got the drivetrain tubes and motor mount tacked in place. I used 3/4 x .049 for all three tubes. Main priority was getting a motor mount tube in without any bends in it. Narrowing the chassis made things a little complicated so I’ll try my best to explain.
Before I get too in depth, weight comparison of factory Nytro bolt, spacer, rubber things to hold the spacer, nut & washer.
And two 12mm bolts. I’ll probably end up getting 4 Ti bolts when the sled is done just to say I have some Ti bolts on the sled.
First thing was to make some aluminum tabs to hold the motor mount tube so I could check track clearance and verify tube positioning. I will cut the aluminum tabs off later and weld on 4130 tabs. Since I have a tube above the header, I wanted to keep the motor mount tube as far apart as possible to help with chassis stiffness. I also wanted the tube low to make removing the motor easier. End of the ruler is the bottom of the jackshaft so lots of clearance.
Chaincase side was fairly easy. I kept the tube vertical(flush with tunnel) until the top bolt and then bent it in.
Clutch side was more difficult. Because I narrowed the chassis so much, there’s not enough room behind the secondary sheave (when clutch is fully open) to run a 3/4 tube behind it. And because the tunnel width is only 15-9/16, the 3/4 tube cannot protrude into where the track would be. So I made the tube large enough that it will clear the track paddles with ample clearance. It’s angled all the way from the lower tube into the steering hoop. It will make doing the jackshaft and driveshaft bearing holder plate slightly more complex but that’s easy at this point.
Clearance to sheave with sheave fully open. I double checked my motor alignment and clutch alignment before running the tube. Yamaha spec for offset is 13.5-16.5 mm and I’m sitting right at 15 mm. I don’t have much room to bring the clutch in but I shouldn’t need to shim it inward at all.
I won’t be doing any of the chaincase or clutch side bearings holders/tabs until what I have now is fully welded so I can make sure the drivetrain ends up straight.
I’ve had a lot of late nights recently, I’m going to take a break for a couple days to refresh and then start thinking about the running boards.
Before I get too in depth, weight comparison of factory Nytro bolt, spacer, rubber things to hold the spacer, nut & washer.
And two 12mm bolts. I’ll probably end up getting 4 Ti bolts when the sled is done just to say I have some Ti bolts on the sled.
First thing was to make some aluminum tabs to hold the motor mount tube so I could check track clearance and verify tube positioning. I will cut the aluminum tabs off later and weld on 4130 tabs. Since I have a tube above the header, I wanted to keep the motor mount tube as far apart as possible to help with chassis stiffness. I also wanted the tube low to make removing the motor easier. End of the ruler is the bottom of the jackshaft so lots of clearance.
Chaincase side was fairly easy. I kept the tube vertical(flush with tunnel) until the top bolt and then bent it in.
Clutch side was more difficult. Because I narrowed the chassis so much, there’s not enough room behind the secondary sheave (when clutch is fully open) to run a 3/4 tube behind it. And because the tunnel width is only 15-9/16, the 3/4 tube cannot protrude into where the track would be. So I made the tube large enough that it will clear the track paddles with ample clearance. It’s angled all the way from the lower tube into the steering hoop. It will make doing the jackshaft and driveshaft bearing holder plate slightly more complex but that’s easy at this point.
Clearance to sheave with sheave fully open. I double checked my motor alignment and clutch alignment before running the tube. Yamaha spec for offset is 13.5-16.5 mm and I’m sitting right at 15 mm. I don’t have much room to bring the clutch in but I shouldn’t need to shim it inward at all.
I won’t be doing any of the chaincase or clutch side bearings holders/tabs until what I have now is fully welded so I can make sure the drivetrain ends up straight.
I’ve had a lot of late nights recently, I’m going to take a break for a couple days to refresh and then start thinking about the running boards.
Similar threads
- Replies
- 623
- Views
- 215K
- Replies
- 29
- Views
- 6K
- Replies
- 466
- Views
- 120K
-
This site uses cookies to help personalise content, tailor your experience and to keep you logged in if you register.
By continuing to use this site, you are consenting to our use of cookies.