kennyspec
Expert
I would add something here. Its a pain cause o had to make mine removeable, however I bet it stiffens up A LOT if you try to lift up the rear of the sled again.

kinger
VIP Member
I don't see option 2 doing anything?? Is that bar flexing even after the "V" shaped tubes you added? I like #1 with a flat plate triangle vs tube. I think you would want to keep that space open in #2 for ancillaries like PCM, wiring, misc crap that goes with making it run. I would hate to have to block it off with another V shape that is only preventing that middle horizontal tube from flexing which I can't believe it even does right?
Last edited:
Nikolai
TY 4 Stroke God
There’s pretty much no flex when testing and that’s with all the gussets only tacked, it will stiffen even more when welded. I don’t think any additional tubing is needed aside from a tube or plate in the corner like you mentioned.

kinger
VIP Member
Then you are good, I did same tests on my steel dock frames trying to eliminate as much steel as possible. Lock one corner lift the other corner with a forklift and scale and welded so much metal in and lifted to 1000lbs, then cut out metal with a sawzall while under pressure to see what members did what. Once you have no flex, more metal is just wasted. The flat plate should add a lot of stiffness with the weld along the tube compared to the small tube you showed.There’s pretty much no flex when testing and that’s with all the gussets only tacked, it will stiffen even more when welded. I don’t think any additional tubing is needed aside from a tube or plate in the corner like you mentioned.
I think you are good!
Nikolai
TY 4 Stroke God
I bet that was interesting cutting the steel back out.
Once it’s welded I’ll do the test from the bumper as well as sticking a long lever thru the chassis to test torsional flex.
I’ll get some plates cut into that corner tonight.
Once it’s welded I’ll do the test from the bumper as well as sticking a long lever thru the chassis to test torsional flex.
I’ll get some plates cut into that corner tonight.
Nikolai
TY 4 Stroke God
Pulled it out of the jig to weld it and was anxious to get a weight. 33.5 lbs so far.
Nikolai
TY 4 Stroke God
Got it welded, took me about 5 hours and was an absolute nightmare. I totally screwed myself by changing the tube work up, it was really tough to get into some of the joints and I expect cracks down the road from excessive heat in a few of them.
I would do things so different next time. I wouldn’t even think about the tunnel until the front half was done. And I wouldn’t do any a-arm tabs, motor mounts or drivetrain plates until every tube was welded, all those things make it more difficult to weld the tubing.
Im not changing this one anymore but if I build a version 2.0 down the road I think I could make the tunnel look better and save a few pounds as well.
I would do things so different next time. I wouldn’t even think about the tunnel until the front half was done. And I wouldn’t do any a-arm tabs, motor mounts or drivetrain plates until every tube was welded, all those things make it more difficult to weld the tubing.
Im not changing this one anymore but if I build a version 2.0 down the road I think I could make the tunnel look better and save a few pounds as well.
Last edited:

kinger
VIP Member
That is interesting, when you started this I liked the tunnel being integrated as one unit, you are still talking about that just in a different order right?
I would love to see a chassis like this available to make a roller out of a sled with a bolted in drivetrain and all geometry correct for the suspension. If you ever came up with a version 2.0 I can manufacture them for you here in the states and ship worldwide, you sell them I will make them
33.5lbs seems a little heavy no? For perspective, what would the oem chassis weigh in roughly the same state? I am in love with the cast bulkhead on the apex, I am going to weigh it this summer but I think its around 28lbs and has all motor mounts, front suspension/sway bar, chaincase mounts, and front cooler all in a tight package. I think yamaha did a solid there. I also have a winder front subframe I was going to attempt to graft onto the apex aluminum bulkhead just to see if it would be easier to make si-pex starting with an apex chassis rather than a cat chassis.
I would love to see a chassis like this available to make a roller out of a sled with a bolted in drivetrain and all geometry correct for the suspension. If you ever came up with a version 2.0 I can manufacture them for you here in the states and ship worldwide, you sell them I will make them
33.5lbs seems a little heavy no? For perspective, what would the oem chassis weigh in roughly the same state? I am in love with the cast bulkhead on the apex, I am going to weigh it this summer but I think its around 28lbs and has all motor mounts, front suspension/sway bar, chaincase mounts, and front cooler all in a tight package. I think yamaha did a solid there. I also have a winder front subframe I was going to attempt to graft onto the apex aluminum bulkhead just to see if it would be easier to make si-pex starting with an apex chassis rather than a cat chassis.
Nikolai
TY 4 Stroke God
As far as the weight goes…
A number of years ago a buddy weighed a stripped 2014 Pro Rmk 155 chassis. Tunnel, bulkhead, over structure and coolers. The running boards had been cut off. It weighed 56 lbs. Oem running boards are at least 2 lbs a side so 60 lbs for a Pro RMK chassis is about right.
However, even at 60 lbs the bulkheads will crumple, tunnels kink, even the new ones have issues with the foot wells. Same with Ski-Doos and their nuns. All of them require tunnel and bulkhead reinforcements that add weight.
When I tore my Nytro down, I weighed the chassis. Tunnel, die cast bulkhead, subframe, exhaust shields, seat and seat bracket, complete cooling system(every hose & clamp) and it was 72 lbs. That had a .040 tunnel skin.
My target has been 50 lbs for the essentially the same thing, complete frame, tunnel skins, heat shields, seat mount, and complete cooling system. Since the Nytro die cast sides include the inner case half I will weigh my chassis with the inner Apex chaincase half so it’s a fair comparison. I don’t think I’ll make 50 lbs anymore but be closer to 54 lbs.
My .040 tunnel skin on my old build wasn’t very big and still weighed 9.5 lbs. that requires a frame to help with strength. If you go .080 where you don’t need an additional structure you’re looking at nearly 20 lbs for a tunnel not including suspension mounts. You can go carbon fiber but even they seem to need additional structures to keep from cracking over time.
If you can get a complete frame with cooling system under 50 lbs I would super impressed and I want to see it so I can copy it haha.
A number of years ago a buddy weighed a stripped 2014 Pro Rmk 155 chassis. Tunnel, bulkhead, over structure and coolers. The running boards had been cut off. It weighed 56 lbs. Oem running boards are at least 2 lbs a side so 60 lbs for a Pro RMK chassis is about right.
However, even at 60 lbs the bulkheads will crumple, tunnels kink, even the new ones have issues with the foot wells. Same with Ski-Doos and their nuns. All of them require tunnel and bulkhead reinforcements that add weight.
When I tore my Nytro down, I weighed the chassis. Tunnel, die cast bulkhead, subframe, exhaust shields, seat and seat bracket, complete cooling system(every hose & clamp) and it was 72 lbs. That had a .040 tunnel skin.
My target has been 50 lbs for the essentially the same thing, complete frame, tunnel skins, heat shields, seat mount, and complete cooling system. Since the Nytro die cast sides include the inner case half I will weigh my chassis with the inner Apex chaincase half so it’s a fair comparison. I don’t think I’ll make 50 lbs anymore but be closer to 54 lbs.
My .040 tunnel skin on my old build wasn’t very big and still weighed 9.5 lbs. that requires a frame to help with strength. If you go .080 where you don’t need an additional structure you’re looking at nearly 20 lbs for a tunnel not including suspension mounts. You can go carbon fiber but even they seem to need additional structures to keep from cracking over time.
If you can get a complete frame with cooling system under 50 lbs I would super impressed and I want to see it so I can copy it haha.
Nikolai
TY 4 Stroke God
To add to that, I think a completely stock Nytro chassis is 80+ lbs, just the tunnels alone were over 50 lbs with all the steel brackets. With all the hardware the weight is probably closer to 85-90 lbs
And to answer the question about my tunnel, if I did it over again I would probably run a tube straight back from the chaincase to rear bumper instead of bending up like I did and use .049 instead of .058, maybe even 1” x .035, probably keep the lower tube 1” and do the rest of the tunnel in 3/4 x .035. Front half would stay similar aside with minor changes to design.
I’d love to see what you come up with for chassis. I’ve spent hours upon hours googling different sled build for ideas.
And to answer the question about my tunnel, if I did it over again I would probably run a tube straight back from the chaincase to rear bumper instead of bending up like I did and use .049 instead of .058, maybe even 1” x .035, probably keep the lower tube 1” and do the rest of the tunnel in 3/4 x .035. Front half would stay similar aside with minor changes to design.
I’d love to see what you come up with for chassis. I’ve spent hours upon hours googling different sled build for ideas.
Last edited:
Nikolai
TY 4 Stroke God
I’m putting my front end together to check the tie rod clearance and something is off. I think I maybe got 38” lower a-arms instead of 36”.
Edited. My ski stance is about 36” so I have the correct lowers. Is it normal on theses sled to have the lower ball joint boot looking like this?
Edited. My ski stance is about 36” so I have the correct lowers. Is it normal on theses sled to have the lower ball joint boot looking like this?
Last edited:
Nikolai
TY 4 Stroke God
I went back and read thru my thread, I’m pretty confident the jig is accurate. If my front end parts are correct I have a pretty big design flaw. Definitely going to have to make some changes to the front 1” tubes to clear the tie rods.
Hmm
Hmm
Last edited:
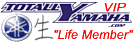

A 36" shock is 16.380in center to center. You sure you have the right length strut in there?I went back and read thru my thread, I’m pretty confident the jig is accurate. If my front end parts are correct I have a pretty big design flaw. Definitely going to have to make some changes to the front 1” tubes to clear the tie rods.
View attachment 167931
View attachment 167932
View attachment 167933
Hmm
View attachment 167934
View attachment 167935
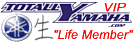

Mine is close to that. 38"I’m putting my front end together to check the tie rod clearance and something is off. I think I maybe got 38” lower a-arms instead of 36”.
Edited. My ski stance is about 36” so I have the correct lowers. Is it normal on theses sled to have the lower ball joint boot looking like this?
View attachment 167930
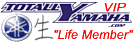

Pic
Similar threads
- Replies
- 4
- Views
- 5K
- Replies
- 32
- Views
- 5K
-
This site uses cookies to help personalise content, tailor your experience and to keep you logged in if you register.
By continuing to use this site, you are consenting to our use of cookies.