Nikolai
TY 4 Stroke God
I’m by no means a turbo expert, I remember a few things from when we originally built the turbo kit this way
1. Log style manifolds are more susceptible to cracking
2. 16” headers make more power (important with low boost kit & no IC)
3. Heat
I’m not changing it for this build, but now that I have a jig and vipers are getting pretty cheap if I buy a viper down the road for a donor and build another I would try a different style turbo setup to compare.
1. Log style manifolds are more susceptible to cracking
2. 16” headers make more power (important with low boost kit & no IC)
3. Heat
I’m not changing it for this build, but now that I have a jig and vipers are getting pretty cheap if I buy a viper down the road for a donor and build another I would try a different style turbo setup to compare.
Last edited:

kinger
VIP Member
The impulse headers on a mid mount kit with a proper turbo support are the most reliable and best for response and power. Those are 321 SS and a work of art. I understand weight balance is a valid thing, turbo weight is not a bad thing back there. I am going to use a meth tank back there to help balance my apex better. That said I agree with @kennyspec you will certainly be changing to a mid mount at some point. add a rad or custom make a longer fuel tank in the back to move weight. Mid mount just do everything better. Get the sled build and put a scale under each ski and under each arm in the rear skid, once you have those measurements I can almost tell you if the sled will feel light and nimble or still to heavy regardless of the physical weight. Aim for 120-130lbs under each ski and most the rear weight on the front arm.
Nikolai
TY 4 Stroke God
Great info Kinger. When I build the fuel tank for this one I’ll see if I can leave enough room in front to give me the option of switching to a mid mount without re-working the tank. I’d like to run it as a rear mount for a season before switching to a mid-mount so I have something to compare to.
If I like the chassis and it handles well I might leave this one alone and look at buying a used turbo apex and build a high HP Apex with a 160sh track.
If I like the chassis and it handles well I might leave this one alone and look at buying a used turbo apex and build a high HP Apex with a 160sh track.
Nikolai
TY 4 Stroke God
Ended up re-doing the front spars a 3rd time. I test fit the throttle bodies with my mocked up intake manifold and it was pretty tight.
Cut the tack welds and removed the spars and then filed them a little to steepen the angle and give me more room. Gained about 3/4” I think.
Mock up of rear tubes. Going to have my wife help me remove the motor tonight to make it sure it clears and then I’ll make the tubes.
Cut the tack welds and removed the spars and then filed them a little to steepen the angle and give me more room. Gained about 3/4” I think.
Mock up of rear tubes. Going to have my wife help me remove the motor tonight to make it sure it clears and then I’ll make the tubes.
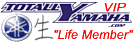

Most all Apex the Turbo is supported by the Manifold. If it wasn't it wouldn't break but if it is it is a major issue. Just have to mount the Turbo to engine=more weight. Could also use a flex in between. Its definitely not as easy as it sounds.How is manifold strength going to be an issue? Even using 16ga stainless i bet it will be a lot tougher than the factory one he is using now.
Nikolai
TY 4 Stroke God
Finished the pyramid tonight. Fused .063 caps over the 3/4 tubes and then welded in some .090 gussets since my 1” tubes would be to large for the 3/4” node.
Old
New
Should be stout. Going to weld what I can in the jig tomorrow and then remove it Friday and finish welding it this weekend.
Old
New
Should be stout. Going to weld what I can in the jig tomorrow and then remove it Friday and finish welding it this weekend.

kinger
VIP Member
What type of welder, process, filler, etc are you using? I am thinking of buying a TIG machine for small projects and learning to TIG. I want to do aluminum and even dabble with Ti
Nikolai
TY 4 Stroke God
I have a Miller Diversion 165. It has been an awesome welder, probably a few hundred hours on it and never an issue.
The Lincoln TIG 200 is a nice welder, only thing I don’t like is the fan runs anytime it’s on whereas my Miller the fan only comes on when needed.
I’m using .045 ER70S2 filler and 1/16 2% Ceriated tungsten. I tried .040 tungsten and didn’t like it, I feel like 1/16 welds better. Gas lens is a must.
The Lincoln TIG 200 is a nice welder, only thing I don’t like is the fan runs anytime it’s on whereas my Miller the fan only comes on when needed.
I’m using .045 ER70S2 filler and 1/16 2% Ceriated tungsten. I tried .040 tungsten and didn’t like it, I feel like 1/16 welds better. Gas lens is a must.
kennyspec
Expert
quarters and dimes make great end caps for tubing.
Quarters and dimes make great caps for welding to tubing.Finished the pyramid tonight. Fused .063 caps over the 3/4 tubes and then welded in some .090 gussets since my 1” tubes would be to large for the 3/4” node.
Nikolai
TY 4 Stroke God
I’m going to weld some coins now just to try it haha.
Tack welded some very crude rear motor mounts just to make 100% sure I could remove the motor with the rear mounts in place. With my wife’s help it’s not too bad to get in and out. Definitely have hours and hours analyzing the tube layout and motor positioning and for the most part I’m happy with how it turned out. I wanted to make the framework compact enough to negate the need for removable frame members and I think I did that. Once I get it welded I’m going to take it over to a buddy who is a structural engineer and get his .02 and see about any needed gusseting.
Got the motor out, turbo out, and shop clean, should have frame welded by the end of the weekend.
Tack welded some very crude rear motor mounts just to make 100% sure I could remove the motor with the rear mounts in place. With my wife’s help it’s not too bad to get in and out. Definitely have hours and hours analyzing the tube layout and motor positioning and for the most part I’m happy with how it turned out. I wanted to make the framework compact enough to negate the need for removable frame members and I think I did that. Once I get it welded I’m going to take it over to a buddy who is a structural engineer and get his .02 and see about any needed gusseting.
Got the motor out, turbo out, and shop clean, should have frame welded by the end of the weekend.
Last edited:

kinger
VIP Member
I weighed my SS housing for you today. 5.4lbs and this is the 1.06 AR. My .82 was probably 1/2 lb lighter. I didn’t weigh that. I will next time I get the sled out. It’s actually still installed. Not sure what your turbine weighs.
Nikolai
TY 4 Stroke God
Thanks! I wrote that down and will weigh mine when I take it apart.
I did a crude flex test on the frame. Unbolted the rear suspension mounts from the frame but the left the front lower a-arm and shock bolts in so just the very front of the frame would be trying to lift both the jig and table (jig is screwed to table). I pushed up on the rear bumper and it was flexing the front spars forward. They weren’t fully welded but still flexed more than I liked. Next time I would design the spars differently but I wasn’t about redo them a 3rd time so I made do with what I had.
Started out adding 3/4 tube gussets behind the valve cover to gusset the rear spars and then added 1” gussets to help strength the front spars. Also added a 3/4 tube below the crank stub. There’s no room to do it on the Mag side.
Then added 2 pieces of 3/4 I had that were just long enough to brace the front spars. That should take all the fore/aft and lateral movement out the pyramid. Spent about 2 days trying to figure out how to strengthen the front spars without it looking stupid. Really wanted to redo it but talked myself out of it.
I think I’m going to add 2 more 3/4 tubes where the blue tape is to eliminate any push/pull from the upper a-arm and then call it good for the frame tubing. I could run them in further to the same node as other 3/4 tubes and still clear my steering post but worried that might look cluttered. Gonna think about it some more tomorrow.
Quite a few things I’d do differently next time but it’s part of the fun.
I did a crude flex test on the frame. Unbolted the rear suspension mounts from the frame but the left the front lower a-arm and shock bolts in so just the very front of the frame would be trying to lift both the jig and table (jig is screwed to table). I pushed up on the rear bumper and it was flexing the front spars forward. They weren’t fully welded but still flexed more than I liked. Next time I would design the spars differently but I wasn’t about redo them a 3rd time so I made do with what I had.
Started out adding 3/4 tube gussets behind the valve cover to gusset the rear spars and then added 1” gussets to help strength the front spars. Also added a 3/4 tube below the crank stub. There’s no room to do it on the Mag side.
Then added 2 pieces of 3/4 I had that were just long enough to brace the front spars. That should take all the fore/aft and lateral movement out the pyramid. Spent about 2 days trying to figure out how to strengthen the front spars without it looking stupid. Really wanted to redo it but talked myself out of it.
I think I’m going to add 2 more 3/4 tubes where the blue tape is to eliminate any push/pull from the upper a-arm and then call it good for the frame tubing. I could run them in further to the same node as other 3/4 tubes and still clear my steering post but worried that might look cluttered. Gonna think about it some more tomorrow.
Quite a few things I’d do differently next time but it’s part of the fun.
Nikolai
TY 4 Stroke God
Need help with the upper a-arm gusset. Can’t decide which way to go.
Option 1. Lightest, directly behind a-arm mount, but doesn’t add any additional strength to overall structure which may not even be needed.
Option 2. Would tie in pyramid and front frame tubes, add strength to entire front frame section but it would not be supporting directly behind the a-arm tab so likely not as effective in reducing twist from a-arm force. Upper a-arms are pretty small so maybe I’m overthinking the amount of force on the frame.
Option 3? Something else?
Option 1. Lightest, directly behind a-arm mount, but doesn’t add any additional strength to overall structure which may not even be needed.
Option 2. Would tie in pyramid and front frame tubes, add strength to entire front frame section but it would not be supporting directly behind the a-arm tab so likely not as effective in reducing twist from a-arm force. Upper a-arms are pretty small so maybe I’m overthinking the amount of force on the frame.
Option 3? Something else?
Nikolai
TY 4 Stroke God
Fit a couple tubes quick to get better idea of option 2.

YamaSpark
VIP Member
- Joined
- Sep 21, 2017
- Messages
- 110
- Location
- Greenfield, Minnesota
- Country
- USA
- Snowmobile
- 2016 SR VIPER S-TX 137 DX
Option 2 gets my vote.Fit a couple tubes quick to get better idea of option 2.
View attachment 167888
View attachment 167889
Similar threads
- Replies
- 4
- Views
- 4K
- Replies
- 32
- Views
- 4K
-
This site uses cookies to help personalise content, tailor your experience and to keep you logged in if you register.
By continuing to use this site, you are consenting to our use of cookies.