rxrider
Jan-Ove Pedersen
- Joined
- Apr 25, 2003
- Messages
- 7,355
- Age
- 60
- Location
- Lakselv - 70N & 25E
- Country
- Norway
- Snowmobile
- 2014 Phazer XTX, 2013 Phazer RTX, 2008 Apex RTX, 2007 Warrior, 2006 Attak
The RB3 works great for controlling fuel, ignition referenced to Boost, TP, Rpms. Forget about the launch control or stutter function on the RB3, it's a joke. Go with the MSD 4350 for the Apex if you need a launch control, it works.
rxrider
Jan-Ove Pedersen
- Joined
- Apr 25, 2003
- Messages
- 7,355
- Age
- 60
- Location
- Lakselv - 70N & 25E
- Country
- Norway
- Snowmobile
- 2014 Phazer XTX, 2013 Phazer RTX, 2008 Apex RTX, 2007 Warrior, 2006 Attak
Update October 6. - Adjusting valve clearance. Preparing for cam degreeing. Installing the cylinder head.
Valve clearance adjustment.
I've got the valve shims I ordered. I ordered 4 x 180 shims and 5 x 185 shims.
I have used the Excel spread sheet (downloadable in my last update) to calculate what shims are needed and where.
Part#s for the shims I ordered. Too bad Yamaha only sells the shims in 0.05mm increments, it's a challenge getting all valve clearances within spec.
Here's the shims ready to be installed, the first attempt. To get close on valve spec I had to reposition a lot of shims in addition to the new ones installed.
Here's the left over valve shims.
Second take. Many of the valve shims were still not withing spec and a more thorough repositioning were needed to get more valve clearances withing spec.
It took 5 attempts before all valve clearances was on or below the high end of spec. Here's the left over shims I ended up with when done. It took me a whole evening figuring the shim combination that would get me withing spec on all valves.
Valve clearances set, final measuring done, all clearances are withing spec.
Final measurements.
Cleaned the cylinder top with gasket remover to have a clean surface before installing the head gasket. I've installed a single stock head gasket this time to run 10:1 compression.
Cleaned the head with gasket remover to have a clean surface before installing the head onto the head gasket. Do NOT turn your cylinder head upside down with the cams removed, don't ask how I know LOL. I have to remove all valve buckets and shims to make sure all shims were still in place, I don't wanna find out that a shim or two is out of position when fireing up the sled...
Preparing for cam degreeing.
First thing was taking pics of the current/stock cam sprockets setting.
Next was removing the cam sprocket from the cam shafts. I made marks on the plate not to mix up the parts while make changes to the cam degrees using the sprocket bushings I bought from TWIN TURBO.
Exhaust sprocket.
Intake sprocket.
Installing cylinder head.
When installing the cylinder head to the block make sure not to drop the cam chain down into the motor. It's a pain to get the chain thru the cylinder head when installing it alone but I managed without dropping the cam chain
I secured the cam chain again.
With the cylinder head down on the studs it took some wiggeling of it to make it seat completely. I added molybden grease to the stock nuts, stock washers and ARP washers and installed them onto the studs.
NB! If you have installed ARP head studs make sure you remember to install the ARP thick washers together with the stock washers. If not you are going to destroy the nuts. Because the ARP studs are longer than the stock ones the nuts will bottom on the top of the stud before clamping down the head and threads are ripped out of the nut and stud.
Then it was time to start the torking precedure. I started with torking the nuts to 20Nm (15ft/lb) starting with the two in the center working my way outwards in a star pattern. Then I installed the small bolts on the outside left and torked them to 9Nm (7ft/lb). I went on by torking the 10 nuts to 35Nm (26ft/lb), then I torked the outside bolts to 12Nm (9ft/lb). Next was torking the main nuts to 50Nm (37ft/lb). I let the nuts sit overnight and torked them to 60Nm (44ft/lb) today. I let them sit for a while and retorked them to 60Nm (44ft/lb) once more, just a few of them moved a little bofore clicking out on the tork wrench.
EDIT: After letting the head sit for a few days I backed off the nuts one at the time (in the same sequence that you tork them down) 1/4 turn and retorked them up to 61Nm (45ft/lb) in one movement. After a while I rechecked all nuts to hold 61Nm (45ft/lb) a few still moved before the tork wrench clicked out. I will have a final check before cams go in.
The cylinder head is installed and torked down.
Next will be cam degreeing.
I'm very happy with the engine work so far. I feel that I have learnt a lot by doing everything (measuring valve lash, adjusting valve lash, installing cams) by myself without asking anyone else what to do, only referring to the Service Manual every now and then. I have done many repetitions of every step on the way, cam and head work have become second nature

Valve clearance adjustment.
I've got the valve shims I ordered. I ordered 4 x 180 shims and 5 x 185 shims.

I have used the Excel spread sheet (downloadable in my last update) to calculate what shims are needed and where.


Part#s for the shims I ordered. Too bad Yamaha only sells the shims in 0.05mm increments, it's a challenge getting all valve clearances within spec.

Here's the shims ready to be installed, the first attempt. To get close on valve spec I had to reposition a lot of shims in addition to the new ones installed.

Here's the left over valve shims.

Second take. Many of the valve shims were still not withing spec and a more thorough repositioning were needed to get more valve clearances withing spec.

It took 5 attempts before all valve clearances was on or below the high end of spec. Here's the left over shims I ended up with when done. It took me a whole evening figuring the shim combination that would get me withing spec on all valves.

Valve clearances set, final measuring done, all clearances are withing spec.

Final measurements.

Cleaned the cylinder top with gasket remover to have a clean surface before installing the head gasket. I've installed a single stock head gasket this time to run 10:1 compression.

Cleaned the head with gasket remover to have a clean surface before installing the head onto the head gasket. Do NOT turn your cylinder head upside down with the cams removed, don't ask how I know LOL. I have to remove all valve buckets and shims to make sure all shims were still in place, I don't wanna find out that a shim or two is out of position when fireing up the sled...

Preparing for cam degreeing.
First thing was taking pics of the current/stock cam sprockets setting.

Next was removing the cam sprocket from the cam shafts. I made marks on the plate not to mix up the parts while make changes to the cam degrees using the sprocket bushings I bought from TWIN TURBO.

Exhaust sprocket.

Intake sprocket.

Installing cylinder head.
When installing the cylinder head to the block make sure not to drop the cam chain down into the motor. It's a pain to get the chain thru the cylinder head when installing it alone but I managed without dropping the cam chain
With the cylinder head down on the studs it took some wiggeling of it to make it seat completely. I added molybden grease to the stock nuts, stock washers and ARP washers and installed them onto the studs.
NB! If you have installed ARP head studs make sure you remember to install the ARP thick washers together with the stock washers. If not you are going to destroy the nuts. Because the ARP studs are longer than the stock ones the nuts will bottom on the top of the stud before clamping down the head and threads are ripped out of the nut and stud.
Then it was time to start the torking precedure. I started with torking the nuts to 20Nm (15ft/lb) starting with the two in the center working my way outwards in a star pattern. Then I installed the small bolts on the outside left and torked them to 9Nm (7ft/lb). I went on by torking the 10 nuts to 35Nm (26ft/lb), then I torked the outside bolts to 12Nm (9ft/lb). Next was torking the main nuts to 50Nm (37ft/lb). I let the nuts sit overnight and torked them to 60Nm (44ft/lb) today. I let them sit for a while and retorked them to 60Nm (44ft/lb) once more, just a few of them moved a little bofore clicking out on the tork wrench.

EDIT: After letting the head sit for a few days I backed off the nuts one at the time (in the same sequence that you tork them down) 1/4 turn and retorked them up to 61Nm (45ft/lb) in one movement. After a while I rechecked all nuts to hold 61Nm (45ft/lb) a few still moved before the tork wrench clicked out. I will have a final check before cams go in.
The cylinder head is installed and torked down.
Next will be cam degreeing.
I'm very happy with the engine work so far. I feel that I have learnt a lot by doing everything (measuring valve lash, adjusting valve lash, installing cams) by myself without asking anyone else what to do, only referring to the Service Manual every now and then. I have done many repetitions of every step on the way, cam and head work have become second nature
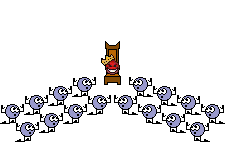



rxrider
Jan-Ove Pedersen
- Joined
- Apr 25, 2003
- Messages
- 7,355
- Age
- 60
- Location
- Lakselv - 70N & 25E
- Country
- Norway
- Snowmobile
- 2014 Phazer XTX, 2013 Phazer RTX, 2008 Apex RTX, 2007 Warrior, 2006 Attak
Update October 10. - Adjusting cams sprockets. Degreeing cams. Installing cams.
I have got these cam settings from TWIN TURBO aka Greg Santry at http://www.powerbygns.com
Stock specs:
Intake cam lobe center: 103
Exhaust cam lobe center: 102
TWIN TURBO's specs:
Intake: 110 - retareded 7 degrees
Exhaust: 110 - advanced 8 degrees
Preparing intake and exhaust cam sprockets for installation of cam sprockets bushings.
I bought the cam sprocket bushings and all cam degreeing equipment used in this post from TWIN TURBO - http://www.powerbygns.com -
I removed the cam sprockets from the cams to figure out how to set the cam sprocket bushings to change cam lobe centre angles where I want them to be.
The sprockets teeths and the position of the large holes allows me to change the position of the cams by 2.5 degrees approx for every large hole I move the sprocket. On the intake cam I retarded it 7.5 deg by moving to the third hole counterclockwise. On the exhaust cam I advanced it by 7.5 deg by moving to the third hole clockwise.
Cam sprockets are installed to the cams, ready to be installed in the cylinder head.
I installed the True Top Dead Center Dial Indicator to find just that, the true top dead center.
I had to move the crank a little back and forth before I could establish the TDC and set the dial indicator to 0
It looks like if you are really careful aligning the pointer to the single mark on the magneto you will be darn pretty close to true TDC, anyway the dial indicator is accurate to the T and takes out any uncertancy.
I went on by installing the exhaust cam. I had to set the cam sprocket into the chain a few times before the cam dot matched up approx with the arrow on the cam caps. Of course I didn't install the cam caps before the dot were approx in the correct spot.
Next was installing the intake cam, same procedure, a little more difficult to match up the dot to the pointer on the cam caps due to very tight space to move the cam in. It took a few attempts to get it right. With the dot close I installed the cam caps.
NB! When installing cams don't be shy on assembly oil. I use engine oil, same as I'm running in the engine, for assembly oil. Oil every valve bucket, valve lifter, cam caps, journal and bearing surface with plenty of oil before installing the cams. Remember, the cams may not get oil pressure for some time before oil pump are building pressure.
Both cams installed and torked down to spec, 10Nm or 7.4 ft/lb.
Time to release the cam chain tensioner. Remove the bolt covering the cam chain tensioner if not already removed.
Use a small screwdriver and turn the cam chain tensioner mechanism counterclockwise to release the cam tensioner. To activate the cam tensioner you have to rotate the crank a few revolutions.
NB! Rotate the crank very carefully for at least two whole cycles (4 revolutions) to make sure everything moves without binding or without resistance. If you encounter any resistance at all while rotating the crank - STOP IMMEDIATELY. If something is installed the wrong way, valves can hit the piston and in the worst case you may cruch and bend a bunch of valves. NOT GOOD.
Next work will be to set the cam lobe centers (I've already did but don't know what they are yet). I will have to make a conversion as the degree wheel and mounting hardware is based on having the engine on the workbench with the magneto cover off. My engine is in the sled with the magneto cover on. The conversion needs to move the degree wheel away from the crank to make room for it. I will also have to make a new or modify the pointer to reach the degree wheel moving out. Last thing I need is something to clamp the cam timing jig to the head to make sure it doesn't move while rotating the crank and cams.
I really love working on this project and I'm looking forward to start verifying the lobe centers, yet another learning curve to pass
When can I get my Yammi degree LOL

I have got these cam settings from TWIN TURBO aka Greg Santry at http://www.powerbygns.com

Stock specs:
Intake cam lobe center: 103
Exhaust cam lobe center: 102
TWIN TURBO's specs:
Intake: 110 - retareded 7 degrees
Exhaust: 110 - advanced 8 degrees
Preparing intake and exhaust cam sprockets for installation of cam sprockets bushings.
I bought the cam sprocket bushings and all cam degreeing equipment used in this post from TWIN TURBO - http://www.powerbygns.com -
I removed the cam sprockets from the cams to figure out how to set the cam sprocket bushings to change cam lobe centre angles where I want them to be.


The sprockets teeths and the position of the large holes allows me to change the position of the cams by 2.5 degrees approx for every large hole I move the sprocket. On the intake cam I retarded it 7.5 deg by moving to the third hole counterclockwise. On the exhaust cam I advanced it by 7.5 deg by moving to the third hole clockwise.



Cam sprockets are installed to the cams, ready to be installed in the cylinder head.

I installed the True Top Dead Center Dial Indicator to find just that, the true top dead center.

I had to move the crank a little back and forth before I could establish the TDC and set the dial indicator to 0

It looks like if you are really careful aligning the pointer to the single mark on the magneto you will be darn pretty close to true TDC, anyway the dial indicator is accurate to the T and takes out any uncertancy.

I went on by installing the exhaust cam. I had to set the cam sprocket into the chain a few times before the cam dot matched up approx with the arrow on the cam caps. Of course I didn't install the cam caps before the dot were approx in the correct spot.
Next was installing the intake cam, same procedure, a little more difficult to match up the dot to the pointer on the cam caps due to very tight space to move the cam in. It took a few attempts to get it right. With the dot close I installed the cam caps.
NB! When installing cams don't be shy on assembly oil. I use engine oil, same as I'm running in the engine, for assembly oil. Oil every valve bucket, valve lifter, cam caps, journal and bearing surface with plenty of oil before installing the cams. Remember, the cams may not get oil pressure for some time before oil pump are building pressure.

Both cams installed and torked down to spec, 10Nm or 7.4 ft/lb.

Time to release the cam chain tensioner. Remove the bolt covering the cam chain tensioner if not already removed.

Use a small screwdriver and turn the cam chain tensioner mechanism counterclockwise to release the cam tensioner. To activate the cam tensioner you have to rotate the crank a few revolutions.

NB! Rotate the crank very carefully for at least two whole cycles (4 revolutions) to make sure everything moves without binding or without resistance. If you encounter any resistance at all while rotating the crank - STOP IMMEDIATELY. If something is installed the wrong way, valves can hit the piston and in the worst case you may cruch and bend a bunch of valves. NOT GOOD.
Next work will be to set the cam lobe centers (I've already did but don't know what they are yet). I will have to make a conversion as the degree wheel and mounting hardware is based on having the engine on the workbench with the magneto cover off. My engine is in the sled with the magneto cover on. The conversion needs to move the degree wheel away from the crank to make room for it. I will also have to make a new or modify the pointer to reach the degree wheel moving out. Last thing I need is something to clamp the cam timing jig to the head to make sure it doesn't move while rotating the crank and cams.
I really love working on this project and I'm looking forward to start verifying the lobe centers, yet another learning curve to pass
When can I get my Yammi degree LOL




NICE!!!!!!!!!!!!!!!!!!!!!!!!!!!! Keep them pics coming buddy!
rxrider
Jan-Ove Pedersen
- Joined
- Apr 25, 2003
- Messages
- 7,355
- Age
- 60
- Location
- Lakselv - 70N & 25E
- Country
- Norway
- Snowmobile
- 2014 Phazer XTX, 2013 Phazer RTX, 2008 Apex RTX, 2007 Warrior, 2006 Attak
Thanks TT - this is really something, I love working on my sled 
Thanks for taking the time to put this together. I love following your projects and seeing the pictures along the way. 

rxrider
Jan-Ove Pedersen
- Joined
- Apr 25, 2003
- Messages
- 7,355
- Age
- 60
- Location
- Lakselv - 70N & 25E
- Country
- Norway
- Snowmobile
- 2014 Phazer XTX, 2013 Phazer RTX, 2008 Apex RTX, 2007 Warrior, 2006 Attak
Thanks RedRocket.
I use this thread as a referrence from time to time when there is something I have forgotten, it happens. Nice if my work can be of any help or inspiration to others working on their sleds. I often have a good time out in the garage working on my sled.
I use this thread as a referrence from time to time when there is something I have forgotten, it happens. Nice if my work can be of any help or inspiration to others working on their sleds. I often have a good time out in the garage working on my sled.
rxrider
Jan-Ove Pedersen
- Joined
- Apr 25, 2003
- Messages
- 7,355
- Age
- 60
- Location
- Lakselv - 70N & 25E
- Country
- Norway
- Snowmobile
- 2014 Phazer XTX, 2013 Phazer RTX, 2008 Apex RTX, 2007 Warrior, 2006 Attak
Update October 11. - Test installing the dial indicator for finding true TDC and the Cam Timing Jig and dial indicators. Making a new degree wheel pointer.
I figured I could spend an hour out in the Turbo garage sunday evening, not much I can do before I have the degree wheel conversion ready.
After cleaning up a bit and pouring used liquids into a 25 liter can I thought it was a good idea to test install all our cam timing equipment just to have a look at it installed. I installed the cam timing jig and the dial indicators first, then I secured the jig to the motor. Next I installed the TDC dial indicator.
Here's the pics.
The two dial indicator on the left and right are the dial that measures the 0.040 lift height and total valve lift height on both cams. The values measured at the degree wheel at this lift height are written down and used in calculating the cam lobe centers.
The centre dial indicator is the True TDC indicator. It will help me find TTDC, fix the pointer at the degree wheel to zero and I have TDC fixed. It's threaded down into the #4 plug hole.
In this pic you can see the bolt attached to the cam cap and piece of metal holding the cam jig in place.
I have to make a conversion that moves the degree wheel away from the engine, the degree wheel is too large to be of any use unless I move it away from the engine. The pointer that came with the set can not be used with the planned conversion so a new pointer has to be made.
I found a 2mm aluminum piece and started to fabricate a new degree wheel pointer. I figured it would work OK to make a pointer that will install on the front oil tank mount. This is how it looks like so far. I will adjust it to fit perfectly when I have the degree wheel conversion ready. No arrow as of yet
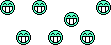
I figured I could spend an hour out in the Turbo garage sunday evening, not much I can do before I have the degree wheel conversion ready.
After cleaning up a bit and pouring used liquids into a 25 liter can I thought it was a good idea to test install all our cam timing equipment just to have a look at it installed. I installed the cam timing jig and the dial indicators first, then I secured the jig to the motor. Next I installed the TDC dial indicator.
Here's the pics.
The two dial indicator on the left and right are the dial that measures the 0.040 lift height and total valve lift height on both cams. The values measured at the degree wheel at this lift height are written down and used in calculating the cam lobe centers.

The centre dial indicator is the True TDC indicator. It will help me find TTDC, fix the pointer at the degree wheel to zero and I have TDC fixed. It's threaded down into the #4 plug hole.

In this pic you can see the bolt attached to the cam cap and piece of metal holding the cam jig in place.

I have to make a conversion that moves the degree wheel away from the engine, the degree wheel is too large to be of any use unless I move it away from the engine. The pointer that came with the set can not be used with the planned conversion so a new pointer has to be made.
I found a 2mm aluminum piece and started to fabricate a new degree wheel pointer. I figured it would work OK to make a pointer that will install on the front oil tank mount. This is how it looks like so far. I will adjust it to fit perfectly when I have the degree wheel conversion ready. No arrow as of yet

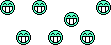
rxrider
Jan-Ove Pedersen
- Joined
- Apr 25, 2003
- Messages
- 7,355
- Age
- 60
- Location
- Lakselv - 70N & 25E
- Country
- Norway
- Snowmobile
- 2014 Phazer XTX, 2013 Phazer RTX, 2008 Apex RTX, 2007 Warrior, 2006 Attak
Update October 12. - Fabricating a degree wheel conversion. Making a new degree wheel pointer. Installing cam degreeing equipment. Initial measuring.... let's go to school 
With the help of my friend Odd Steffen I finally got the degree wheel conversion made. Odd Steffen is helping me out big time with his fabricating skills. We made a hollow bar with threads to fit the crank on one end and threads to install the degree wheel on the other hand.
Here's a pic of what it looks like, conversion and degree wheel mounted to the engine.
With the degree wheel installed to the crank i finished the pointer.
I have installed the degree wheel and indicators the wrong way on purpose. I would like to make cam degreeing an easy one man task. Just a thought I figured I would like to try out. If it doesn't turn out good I will go back to do it the way it's supposed to
I know ...... what some of you might already have figured, reading the degree wheel is misleading. I actually have to read the degree wheel mirrored.... if that is a word.
Ready to start degreeing in the cams. I had already made adjustments to the cam sprockets. The dials are firmly mounted to the engine, time to start rotating the crank in the forward rotation. We figured it would be just as easy to rotate the crank by turning the primary clutch with a socket wrench and a extensioner to make it easy to rotate in baby steps.
First task was to find TDC, next was setting the degree wheel to zero putting the pointer on the TDC marker. When TDC was found we carefully rotated the degree wheel to zero making sure we did not move the cranks and finally we secured the degree wheel to the conversion bolt. All was done while carefully watching the TDC dial indicator, it did not move at all. We were good to go.
TDC found.
Degree wheel set to zero.
With the degree wheel adjusted and TDC dial indicator set to zero. We rotated the crank several rotations and rechecked the TDC dial indicato and degree wheel, both check out correctly as set. We went on by setting the intake and exhaust dial indicators to zero.
Later on we rotated the crank to find maximum valve lift, and to find 0.040" valve lift on the opening side of the cam of the intake cam, # from the degree wheel were recorded.
We also rotated the crank to find 0.040" valve lift on the closing side of the intake cam, # from the degree wheel were recorded.
We also degreed the exhaust cam, but that's another story.
The details will be covered in a later cam degreeing post.

With the help of my friend Odd Steffen I finally got the degree wheel conversion made. Odd Steffen is helping me out big time with his fabricating skills. We made a hollow bar with threads to fit the crank on one end and threads to install the degree wheel on the other hand.
Here's a pic of what it looks like, conversion and degree wheel mounted to the engine.

With the degree wheel installed to the crank i finished the pointer.

I have installed the degree wheel and indicators the wrong way on purpose. I would like to make cam degreeing an easy one man task. Just a thought I figured I would like to try out. If it doesn't turn out good I will go back to do it the way it's supposed to
Ready to start degreeing in the cams. I had already made adjustments to the cam sprockets. The dials are firmly mounted to the engine, time to start rotating the crank in the forward rotation. We figured it would be just as easy to rotate the crank by turning the primary clutch with a socket wrench and a extensioner to make it easy to rotate in baby steps.

First task was to find TDC, next was setting the degree wheel to zero putting the pointer on the TDC marker. When TDC was found we carefully rotated the degree wheel to zero making sure we did not move the cranks and finally we secured the degree wheel to the conversion bolt. All was done while carefully watching the TDC dial indicator, it did not move at all. We were good to go.
TDC found.


Degree wheel set to zero.

With the degree wheel adjusted and TDC dial indicator set to zero. We rotated the crank several rotations and rechecked the TDC dial indicato and degree wheel, both check out correctly as set. We went on by setting the intake and exhaust dial indicators to zero.

Later on we rotated the crank to find maximum valve lift, and to find 0.040" valve lift on the opening side of the cam of the intake cam, # from the degree wheel were recorded.
We also rotated the crank to find 0.040" valve lift on the closing side of the intake cam, # from the degree wheel were recorded.
We also degreed the exhaust cam, but that's another story.
The details will be covered in a later cam degreeing post.

Blue shadow
TY 4 Stroke Guru
Your doing a good job ,I did this last year with Daves hurricane help.I had a bit of trouble at first but it came out ok .
rxrider
Jan-Ove Pedersen
- Joined
- Apr 25, 2003
- Messages
- 7,355
- Age
- 60
- Location
- Lakselv - 70N & 25E
- Country
- Norway
- Snowmobile
- 2014 Phazer XTX, 2013 Phazer RTX, 2008 Apex RTX, 2007 Warrior, 2006 Attak
Blue shadow - Is there any particular problem I should look out for while degreeing the cams? Any help from you are highly appreciated.
At the first attempt I found #s for the lobe centers to be odd at least... don't dare to tell.... hahahaha
I may have got the measurement right but have the calculations screwed up, who knows.
I just had my very first class in cam degreeing last night as none of us have done this before.
Web cams says to remove all valve lash, what do you make out of this?
At the first attempt I found #s for the lobe centers to be odd at least... don't dare to tell.... hahahaha
I just had my very first class in cam degreeing last night as none of us have done this before.
Web cams says to remove all valve lash, what do you make out of this?
Blue shadow
TY 4 Stroke Guru
Yes remove all valve lash on # 4 CLY on the cam lob between the bucket and the lob .Set your pointer at o when the lob is away from the bucket.Turn the crank until you find tdc on # 4 cly and set the pointer on 0 tdc on the degree wheel.I had to used 10 tho before the valve started to open and 10 tho before the valve is fully close on the dial gauge when I took take a reading .
rxrider
Jan-Ove Pedersen
- Joined
- Apr 25, 2003
- Messages
- 7,355
- Age
- 60
- Location
- Lakselv - 70N & 25E
- Country
- Norway
- Snowmobile
- 2014 Phazer XTX, 2013 Phazer RTX, 2008 Apex RTX, 2007 Warrior, 2006 Attak
Thank you Blue shadow, your input is highly appreciated 
How did you remove all valve lash?
By installing thicker valve shims?
Please correct me if I'm wrong, or is there another way of removing valve lash without having to remove the cams.
How did you remove all valve lash?
By installing thicker valve shims?
Please correct me if I'm wrong, or is there another way of removing valve lash without having to remove the cams.
rxrider
Jan-Ove Pedersen
- Joined
- Apr 25, 2003
- Messages
- 7,355
- Age
- 60
- Location
- Lakselv - 70N & 25E
- Country
- Norway
- Snowmobile
- 2014 Phazer XTX, 2013 Phazer RTX, 2008 Apex RTX, 2007 Warrior, 2006 Attak
I have been reading for a few hours at different car sites around the net and what do I find.... hahahahaha I had it all wrong, the paper I had downloaded from webcams was easy to misunderstand, and guess what? I misunderstood most of it, didn't understand a tiny litte bit of what they ment in their writeup, but now I do.
Blue shadow - What did you do to remove valve lash?
Anyone else who knows, please chime in.
Blue shadow - What did you do to remove valve lash?
Anyone else who knows, please chime in.
rxrider
Jan-Ove Pedersen
- Joined
- Apr 25, 2003
- Messages
- 7,355
- Age
- 60
- Location
- Lakselv - 70N & 25E
- Country
- Norway
- Snowmobile
- 2014 Phazer XTX, 2013 Phazer RTX, 2008 Apex RTX, 2007 Warrior, 2006 Attak
Update October 16. - Cam degreeing part 1.
Last time out I installed the degree wheel, TDC dial indicator and the cam timing jig with dial indicator for intake and exhaust cams.
I have been reading a lot of material by supertuner, webcams, twin turbo and others and I think I have the procedure set. If I'm doing something wrong or if I have left out anything I would like your comment.
This is how I do it. Here we go.
- Find TDC on the dial indicator. Zero it.
- Zero both intake and exhaust dial indicators.
- Set degree wheel to zero.
- Rotate the engine two revolutions and recheck TDC and degree wheel, if not reset to zero and check again. When both checks out...continue.
- Before takeing measurements, document the position of the cams. I took a few pics of how the cam dots lined up with the arrows on the cam caps.
- Start with intake cam.
- Rotate the crank in the running order until Intake valve dial indicator is at 0.040", take a reading off the degree wheel.
- Rotate the crank in the running order until Intake valve dial indicator returns to 0.040" on the closing side of the lobe, take a reading off the degree wheel.
- Rotate the crank back to TDC on the dial indicator and degree wheel.
- Continue with the exhaust cam.
- Rotate crank in the running order until the exhaust dial indicator shows 0.040" valve lift, take a reading off the degree wheel.
- Rotate the crank in the running order until exhaust valve dial indicator returns to 0.040" on the closing side of the lobe, take a reading off the degree wheel.
- Calculate the #s
Now you will have the current intake and exhaust cam positions.
Stock positions on the RX-1 is:
Intake: 103
Exhaust: 102
Mine were 108 intake and 98 exhaust, but my engine have been touched before when running the MXC turbo kit, the intake cam sprocket were slotted to get the intake cam back to the stock setting when running 3 stacked head gaskets.
With these numbers recorded I started to make assumptions on how to make changes to the cam sprockets to get closer to target degrees of 114 intake and 114 exhaust.
I set the cam sprocket bushings in #3 to the left on the intake came and in hole #3 to the right on the exhaust cam. With these settings I got:
Intake lobe center = 120
Exhaust lobe center = 104.5
Here's a pic of how 120 deg intake looks like.
Here's the exhaust on 104.5 deg.
It looks like I have set the chain one tooth too far counterclockwise. One thooth wrong equals 9 degrees approx. By jumping the sprockets on tooth clockwise I should be set about right at 111 intake and 113.5 exhaust. But man was I wrong on the 9 degree assumption.... the cam makes 2 revolutions for every revolution of the crank, my 9 degrees turn out to be 18 degree movement in cam lobe centerline when the chain is jumping 1 tooth on the cam sprocket.
I was in trouble big time, what is going on. I throw out a question for help and Mike immediately came to my resque. Discussing the problem with him and doing some additional reading got me in the right direction. Like I said I'm at school on this one and the learning curve is pretty steep, but I think I've got it about right - at least in theory
I would like to say a big thank you to Mike aka Blue shadow for helping me out .
OK - time to change the bolt position in the cam sprocket once more. On the first change of bolt positions I had the cams out of the motor. I figured it was way too much work to remove the cams for every adjustment so I tried to do the hole change with the cams in place in the cylinder head.
First I loosened the bolts, rotated the crank and loosened. I removed on bolt on each sprocket then I turned the cams until the dots lined up with the arrows and removed the second bolt.
Next was unhooking the cam chain tensioner. Remove the 10mm bolt and turn the cam tensioner screw clockwise until it stops, this releases the pressure off the chain.
I removed the intake cam sprocket and was removing the exhaust cam sprocket when I lost a cam sprocket bushing into the engine GGRRRRR
Luckily I have good friends who are auto- and aircraft mechanics.
My friend Mikkel (Auto mechanic) came over to help me out. We could see the bushing so he figured he could get to it with a grabber tool, not so too little space down there. He asked me if I had any thin mild steel single wire, which I had. He made a 1.5 ft straight wire and bent it to make a small fishing hook at the end of the wire. With this wire he was able to get it out of the narrow space and out in the open down in the bottom of the motor. He started to get shaky from consentrating so he asked me to give it a try. After three attempts I got it hooked, then turned around 90 deg to get it past obstacles on the way. I slowly and carefully started to hoist it upwards, my frinds said "hold your breath or else you will start to shake before you reach the top" so I did. When it was above the top of the engine I moved it backwards out of harms way quickly,.....
Puuuhhhhh my friend saved my day and the whole week I guess.
I would hate to pull the motor.

I would like to say a big thank you to Mikkel for coming over the same evening to help me out. It's great to have good friends here at home and at TY when in dire need.

Last time out I installed the degree wheel, TDC dial indicator and the cam timing jig with dial indicator for intake and exhaust cams.
I have been reading a lot of material by supertuner, webcams, twin turbo and others and I think I have the procedure set. If I'm doing something wrong or if I have left out anything I would like your comment.
This is how I do it. Here we go.
- Find TDC on the dial indicator. Zero it.
- Zero both intake and exhaust dial indicators.

- Set degree wheel to zero.

- Rotate the engine two revolutions and recheck TDC and degree wheel, if not reset to zero and check again. When both checks out...continue.
- Before takeing measurements, document the position of the cams. I took a few pics of how the cam dots lined up with the arrows on the cam caps.



- Start with intake cam.
- Rotate the crank in the running order until Intake valve dial indicator is at 0.040", take a reading off the degree wheel.
- Rotate the crank in the running order until Intake valve dial indicator returns to 0.040" on the closing side of the lobe, take a reading off the degree wheel.
- Rotate the crank back to TDC on the dial indicator and degree wheel.
- Continue with the exhaust cam.
- Rotate crank in the running order until the exhaust dial indicator shows 0.040" valve lift, take a reading off the degree wheel.
- Rotate the crank in the running order until exhaust valve dial indicator returns to 0.040" on the closing side of the lobe, take a reading off the degree wheel.
- Calculate the #s
Now you will have the current intake and exhaust cam positions.
Stock positions on the RX-1 is:
Intake: 103
Exhaust: 102
Mine were 108 intake and 98 exhaust, but my engine have been touched before when running the MXC turbo kit, the intake cam sprocket were slotted to get the intake cam back to the stock setting when running 3 stacked head gaskets.
With these numbers recorded I started to make assumptions on how to make changes to the cam sprockets to get closer to target degrees of 114 intake and 114 exhaust.
I set the cam sprocket bushings in #3 to the left on the intake came and in hole #3 to the right on the exhaust cam. With these settings I got:
Intake lobe center = 120
Exhaust lobe center = 104.5
Here's a pic of how 120 deg intake looks like.

Here's the exhaust on 104.5 deg.

It looks like I have set the chain one tooth too far counterclockwise. One thooth wrong equals 9 degrees approx. By jumping the sprockets on tooth clockwise I should be set about right at 111 intake and 113.5 exhaust. But man was I wrong on the 9 degree assumption.... the cam makes 2 revolutions for every revolution of the crank, my 9 degrees turn out to be 18 degree movement in cam lobe centerline when the chain is jumping 1 tooth on the cam sprocket.




I was in trouble big time, what is going on. I throw out a question for help and Mike immediately came to my resque. Discussing the problem with him and doing some additional reading got me in the right direction. Like I said I'm at school on this one and the learning curve is pretty steep, but I think I've got it about right - at least in theory
I would like to say a big thank you to Mike aka Blue shadow for helping me out .

OK - time to change the bolt position in the cam sprocket once more. On the first change of bolt positions I had the cams out of the motor. I figured it was way too much work to remove the cams for every adjustment so I tried to do the hole change with the cams in place in the cylinder head.
First I loosened the bolts, rotated the crank and loosened. I removed on bolt on each sprocket then I turned the cams until the dots lined up with the arrows and removed the second bolt.

Next was unhooking the cam chain tensioner. Remove the 10mm bolt and turn the cam tensioner screw clockwise until it stops, this releases the pressure off the chain.

I removed the intake cam sprocket and was removing the exhaust cam sprocket when I lost a cam sprocket bushing into the engine GGRRRRR








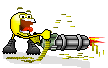
Luckily I have good friends who are auto- and aircraft mechanics.
My friend Mikkel (Auto mechanic) came over to help me out. We could see the bushing so he figured he could get to it with a grabber tool, not so too little space down there. He asked me if I had any thin mild steel single wire, which I had. He made a 1.5 ft straight wire and bent it to make a small fishing hook at the end of the wire. With this wire he was able to get it out of the narrow space and out in the open down in the bottom of the motor. He started to get shaky from consentrating so he asked me to give it a try. After three attempts I got it hooked, then turned around 90 deg to get it past obstacles on the way. I slowly and carefully started to hoist it upwards, my frinds said "hold your breath or else you will start to shake before you reach the top" so I did. When it was above the top of the engine I moved it backwards out of harms way quickly,.....
Puuuhhhhh my friend saved my day and the whole week I guess.
I would hate to pull the motor.


I would like to say a big thank you to Mikkel for coming over the same evening to help me out. It's great to have good friends here at home and at TY when in dire need.





Similar threads
- Replies
- 46
- Views
- 149K
-
This site uses cookies to help personalise content, tailor your experience and to keep you logged in if you register.
By continuing to use this site, you are consenting to our use of cookies.