Blue shadow
TY 4 Stroke Guru
Dont forget before you set the dial indicator to zero the lob has to be away from the valve lifter were the gauge is sitting on top .
rxrider
Jan-Ove Pedersen
- Joined
- Apr 25, 2003
- Messages
- 7,355
- Age
- 60
- Location
- Lakselv - 70N & 25E
- Country
- Norway
- Snowmobile
- 2014 Phazer XTX, 2013 Phazer RTX, 2008 Apex RTX, 2007 Warrior, 2006 Attak
I have the TDC indicator in #4 plughole and the cam timing jig with intake and exhaust dial indicators measuring at #4 cyl as well. When setting the #4 cyl at TDC the lobes are pointing away for the crank and the cam dots and arrows lines up approx, this means that the #4 cyl in at fireing stroke with all valves closed 
Thanks again for verifying that what I do is correct.
It's highly appreciated. I'm at school as said, this is quite a learning curve for a guy that have never done this work before, but I'm learning, and actually I'm getting close. I have the intake cam at 114 degrees and the exhaust at 104.5 so far. I'm happy with 114 degrees for intake as this is where Dave at Powderlites likes to set it.
One last question to you Mike, why did you go with 112 on intake and exhaust?
Jan-Ove
rxrider
Thanks again for verifying that what I do is correct.
It's highly appreciated. I'm at school as said, this is quite a learning curve for a guy that have never done this work before, but I'm learning, and actually I'm getting close. I have the intake cam at 114 degrees and the exhaust at 104.5 so far. I'm happy with 114 degrees for intake as this is where Dave at Powderlites likes to set it.
One last question to you Mike, why did you go with 112 on intake and exhaust?
Jan-Ove
rxrider
Blue shadow
TY 4 Stroke Guru
When I had it all done on 112 degrees I left it that way .It was said that between 112 and 114 degree was fine .
rxrider
Jan-Ove Pedersen
- Joined
- Apr 25, 2003
- Messages
- 7,355
- Age
- 60
- Location
- Lakselv - 70N & 25E
- Country
- Norway
- Snowmobile
- 2014 Phazer XTX, 2013 Phazer RTX, 2008 Apex RTX, 2007 Warrior, 2006 Attak
On the Intake I have managed to get either 113.5 degree by using the grounded stock holes (from MCX setup) or 114 degree by installing the bushings in the first hole to the left on the intake cam. I'll leave it like that.
I don't know how the exhaust cam will turn out yet. That's the next step. Both cams are out of the engine as of now.
rxrider
Jan-Ove Pedersen
- Joined
- Apr 25, 2003
- Messages
- 7,355
- Age
- 60
- Location
- Lakselv - 70N & 25E
- Country
- Norway
- Snowmobile
- 2014 Phazer XTX, 2013 Phazer RTX, 2008 Apex RTX, 2007 Warrior, 2006 Attak
My friends stage 3 IC arrived from Powder Lites together with a set of stage 4 fuel injectors and a BOV. I got a new gasket for the turbo and all the bolts, nuts and Nordlocks needed to tighten down the turbo to the header and downpipe.
PL mean business when wrapping up parts for shipping, the package was so well covered inside that I guess the parts inside would have suvived without a scratch dropping from 4 ft.
The IC
What a piece of art that IC from PL
It's covered by some strange kind of ceramics to improve heat dissipation. Pretty cool color too.
PL mean business when wrapping up parts for shipping, the package was so well covered inside that I guess the parts inside would have suvived without a scratch dropping from 4 ft.
The IC
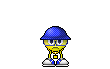



What a piece of art that IC from PL
It's covered by some strange kind of ceramics to improve heat dissipation. Pretty cool color too.
rxrider
Jan-Ove Pedersen
- Joined
- Apr 25, 2003
- Messages
- 7,355
- Age
- 60
- Location
- Lakselv - 70N & 25E
- Country
- Norway
- Snowmobile
- 2014 Phazer XTX, 2013 Phazer RTX, 2008 Apex RTX, 2007 Warrior, 2006 Attak
Update October 17. - Cam degreeing. Part 2.
Today I started out as the day before. Setting everything to zero and checking and rechecking before starting to take measurements.
I've had it haveing the cam chain jumping teeths so I figured it was an idea to fasten the chain to the sprocket to prevent the chain from jumping.
The wire I tried was way too much work to install and remove....
The zip ties I tried both small and larger had an even bigger flaw than the wire. Late at night when I was tired I didn't see the black zip ties and when rotating the crank they snapped and fell into the engine....
These ideas of mine turned out to be yet another big NONO not to do which yet again led to disaster...sort of. Luckily I have learnt the way of the angler and I managed to fish up both zip- ties from the engine
With all this crap happening I called it the night as I was starting to get too tired to keep my consentration.
Last thing I did was to make a few small changes to the cam jig and dial indicators to make the intake indicator fit better and hit the valve bucket a little further in from the edge. I moved the point of enty about 0.040" or 1mm further away from the edge of the valve bucket as the pointer hit on the very edge of the valve bucket.
Exhaust dial indicator on the bucket.
Intake dial indicator on the bucket.

Today I started out as the day before. Setting everything to zero and checking and rechecking before starting to take measurements.
I've had it haveing the cam chain jumping teeths so I figured it was an idea to fasten the chain to the sprocket to prevent the chain from jumping.
The wire I tried was way too much work to install and remove....


The zip ties I tried both small and larger had an even bigger flaw than the wire. Late at night when I was tired I didn't see the black zip ties and when rotating the crank they snapped and fell into the engine....

These ideas of mine turned out to be yet another big NONO not to do which yet again led to disaster...sort of. Luckily I have learnt the way of the angler and I managed to fish up both zip- ties from the engine
With all this crap happening I called it the night as I was starting to get too tired to keep my consentration.
Last thing I did was to make a few small changes to the cam jig and dial indicators to make the intake indicator fit better and hit the valve bucket a little further in from the edge. I moved the point of enty about 0.040" or 1mm further away from the edge of the valve bucket as the pointer hit on the very edge of the valve bucket.
Exhaust dial indicator on the bucket.

Intake dial indicator on the bucket.




rxrider
Jan-Ove Pedersen
- Joined
- Apr 25, 2003
- Messages
- 7,355
- Age
- 60
- Location
- Lakselv - 70N & 25E
- Country
- Norway
- Snowmobile
- 2014 Phazer XTX, 2013 Phazer RTX, 2008 Apex RTX, 2007 Warrior, 2006 Attak
Update October 18. - Cam degreeing - Part 3.
I set TDC and checked degree wheel at 0 deg, also set cam jig dial indicators to 0. When the cam was at 120 deg I made set marks on cam cap and cam shaft.
I had the intake cam set the last time out. Now I was ready to make the final adjustments to the exhaust cam sprocket. I had to retard the exhaust cam from where it was on the last adjustment, 117.5 degrees. I removed the bolts from the exhaust cam sprocket and carefully removed the bushings from the sprocket. I moved the bushings to holes counterclockwise and rotated the engine from TDC until the exhaust sprocket bolt holes aligned up with the threads in the cam. Installed bolts and measured the cams once more.
Here's the procedure with pics.
- Set TDC, set the TDC indicator to 0
- Set degree wheel to 0
- Set the exhaust and intake dial indicators to 0
- Rotate crank in the running direction until the intake cam dial indicator is at 0.040" or 1mm on opening.
- Take a reading off the degree wheel, # should be BTDC, in my case it was 2 deg BTDC
- Continue rotating the crank in the running direction until the intake dial indicator shows 0.040" or 1mm on closing.
- Take a reading off the degree wheel, # should be ABDC, in my case it was 50 deg ABDC
Readings taken on the intake cam.
- Rotate to TDC and continue with the exhaust cam.
- Rotate crank in the running direction until the exhaust cam dial indicator is at 0.040" or 1mm on opening.
- Take a reading off the degree wheel, # should be BBDC, in my case it was 50 deg BBDC. (Sorry no pic taken)
- Continue rotating the crank in the running direction until the exhaust dial indicator shows 0.040" or 1mm on closing. (Sorry no pic)
- Take a reading off the degree wheel, # should be ATDC, in my case it was 5 deg ATDC.
- Calculate the numbers.
- Do the procedure over again a few more times to make absolutely sure you have it all done correctly. If you can replicate the #s time and time again you have most likely done it right
This is what the intake cam looks like retarded to 114 degrees.
This is what the exhaust cam looks like advanced to 112.5 degrees.
Finally done with cam degreeing. It was some work to learn it but I feel much better beeing able to do cam degreeing all by myself.
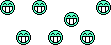
I set TDC and checked degree wheel at 0 deg, also set cam jig dial indicators to 0. When the cam was at 120 deg I made set marks on cam cap and cam shaft.
I had the intake cam set the last time out. Now I was ready to make the final adjustments to the exhaust cam sprocket. I had to retard the exhaust cam from where it was on the last adjustment, 117.5 degrees. I removed the bolts from the exhaust cam sprocket and carefully removed the bushings from the sprocket. I moved the bushings to holes counterclockwise and rotated the engine from TDC until the exhaust sprocket bolt holes aligned up with the threads in the cam. Installed bolts and measured the cams once more.
Here's the procedure with pics.
- Set TDC, set the TDC indicator to 0
- Set degree wheel to 0
- Set the exhaust and intake dial indicators to 0
- Rotate crank in the running direction until the intake cam dial indicator is at 0.040" or 1mm on opening.

- Take a reading off the degree wheel, # should be BTDC, in my case it was 2 deg BTDC

- Continue rotating the crank in the running direction until the intake dial indicator shows 0.040" or 1mm on closing.

- Take a reading off the degree wheel, # should be ABDC, in my case it was 50 deg ABDC

Readings taken on the intake cam.

- Rotate to TDC and continue with the exhaust cam.
- Rotate crank in the running direction until the exhaust cam dial indicator is at 0.040" or 1mm on opening.

- Take a reading off the degree wheel, # should be BBDC, in my case it was 50 deg BBDC. (Sorry no pic taken)
- Continue rotating the crank in the running direction until the exhaust dial indicator shows 0.040" or 1mm on closing. (Sorry no pic)
- Take a reading off the degree wheel, # should be ATDC, in my case it was 5 deg ATDC.

- Calculate the numbers.

- Do the procedure over again a few more times to make absolutely sure you have it all done correctly. If you can replicate the #s time and time again you have most likely done it right
This is what the intake cam looks like retarded to 114 degrees.

This is what the exhaust cam looks like advanced to 112.5 degrees.

Finally done with cam degreeing. It was some work to learn it but I feel much better beeing able to do cam degreeing all by myself.

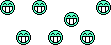
Good work buddy!!!!!!!!!!!!!
rxrider
Jan-Ove Pedersen
- Joined
- Apr 25, 2003
- Messages
- 7,355
- Age
- 60
- Location
- Lakselv - 70N & 25E
- Country
- Norway
- Snowmobile
- 2014 Phazer XTX, 2013 Phazer RTX, 2008 Apex RTX, 2007 Warrior, 2006 Attak
Update October 19. - Installing cylinder head cover, plugs, coils and piping.
After making a final tork check on the cam caps bolts (10Nm) and cam sprocket bolts (24Nm) I installed the cylinder head cover. Make sure the gasket sits prefectly in the groove in the cover before installing. Check again when the cover is on before installing the bolts. With the gasket in place install the 6 Allen bolts, tork them to 12Nm.
I figured it would be way easier to install spark plugs and coils right away when access was easy. Before installing the spark plugs I set the plug gap to 0.020" or 0.5mm. To help me set the plug gap I have this plug gap tool to help me, it's a great tool that makes plug gap adjustments a breeze
I installed the plugs and torked them to 13Nm. Then I installed the coils. Last I installed the piping for the coolant.
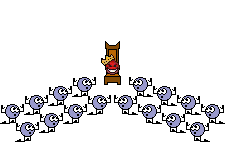
After making a final tork check on the cam caps bolts (10Nm) and cam sprocket bolts (24Nm) I installed the cylinder head cover. Make sure the gasket sits prefectly in the groove in the cover before installing. Check again when the cover is on before installing the bolts. With the gasket in place install the 6 Allen bolts, tork them to 12Nm.

I figured it would be way easier to install spark plugs and coils right away when access was easy. Before installing the spark plugs I set the plug gap to 0.020" or 0.5mm. To help me set the plug gap I have this plug gap tool to help me, it's a great tool that makes plug gap adjustments a breeze

I installed the plugs and torked them to 13Nm. Then I installed the coils. Last I installed the piping for the coolant.

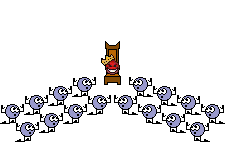
Blue shadow
TY 4 Stroke Guru
looks good ,rxrider
rxrider
Jan-Ove Pedersen
- Joined
- Apr 25, 2003
- Messages
- 7,355
- Age
- 60
- Location
- Lakselv - 70N & 25E
- Country
- Norway
- Snowmobile
- 2014 Phazer XTX, 2013 Phazer RTX, 2008 Apex RTX, 2007 Warrior, 2006 Attak
Thanks guys
rxrider
Jan-Ove Pedersen
- Joined
- Apr 25, 2003
- Messages
- 7,355
- Age
- 60
- Location
- Lakselv - 70N & 25E
- Country
- Norway
- Snowmobile
- 2014 Phazer XTX, 2013 Phazer RTX, 2008 Apex RTX, 2007 Warrior, 2006 Attak
Update October 20. - Installing delta box frame.
Installed the delta box frame and bolted it to the sled.
Next will be installing the steering new aluminum steering mounting blocks with oillite bushings, 2 for the steering column and 1 for the transfer rod going in behind the oil tank.
Installed the delta box frame and bolted it to the sled.



Next will be installing the steering new aluminum steering mounting blocks with oillite bushings, 2 for the steering column and 1 for the transfer rod going in behind the oil tank.
I still say I should send my sled over and ave you work on it for free.
Looking good and I cant wait to meet you on the maine TY ride and have a couple
.
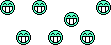
Looking good and I cant wait to meet you on the maine TY ride and have a couple

Jan-Ove, sorry if I missed anything in this thread, but that Apex in the background, does it have the new 'mid' mounted Apex kit?
rxrider
Jan-Ove Pedersen
- Joined
- Apr 25, 2003
- Messages
- 7,355
- Age
- 60
- Location
- Lakselv - 70N & 25E
- Country
- Norway
- Snowmobile
- 2014 Phazer XTX, 2013 Phazer RTX, 2008 Apex RTX, 2007 Warrior, 2006 Attak
Hahahahaha buddy.... curious now LOL
No it's not. This is a special trail version of the full race turbo system, my buddy's sled makes 440 HP.
It has stock tank, the turbo is placed just rear of the tank, it has a huge tial external wastegate. And works on pump fuel up to 380 HP. It has new exhaust piping running 4 into 1 pipes all the way from the engine to the collector at the turbo.
Throttle response are not the best but when the turbo spools it's crazy fast, but he have to play catch up with the rest of us turbo guys around here.
No it's not. This is a special trail version of the full race turbo system, my buddy's sled makes 440 HP.
It has stock tank, the turbo is placed just rear of the tank, it has a huge tial external wastegate. And works on pump fuel up to 380 HP. It has new exhaust piping running 4 into 1 pipes all the way from the engine to the collector at the turbo.
Throttle response are not the best but when the turbo spools it's crazy fast, but he have to play catch up with the rest of us turbo guys around here.
Similar threads
- Replies
- 46
- Views
- 149K
-
This site uses cookies to help personalise content, tailor your experience and to keep you logged in if you register.
By continuing to use this site, you are consenting to our use of cookies.