Big Pussy
Extreme
- Joined
- Apr 12, 2016
- Messages
- 94
- Age
- 66
- Location
- Woodstock, Ont
- Country
- Canada
- Snowmobile
- 2015 XF7000 LXR
So many things have been done to try to fix the driveshaft/bearing fit. I finally fixed it right. Get your driveshaft turned, spray welded and ground to final size on size fit with new bearings on BOTH ends. The spray weld/machining cost me $275 Canadian plus tax. Cheaper than a new shaft that will still destroy itself. There is no key, no set screws, no welded tab like I tried before. Just a proper interference fit. The bearings will not spin and you don't need a one of a kind special bearing. The challenge is to put it together and take it apart in the future. I have documented the special tools that I had made to do this. Here goes. Assembling the shaft.
First of all, you need to drill out those rivets and remove the lower plastic belly pan pieces. I replaced with M5x0.8 mm aluminum rivnuts and M5 stainless large head screws. The hole at the top by the top shock mount got tapped for an M5x0.8 mm Helicoil insert. Now I can remove the plastic for an easy oil change and chaincase service.
The cup is 45mm ID x 2" long inside. The threaded rod is M10 12.9 grade as are the nuts so they won't easily strip. If you can't get this made, you can cut the outer race off three old bearings and stack them together with a plate with a hole in it. It will be very difficult holding it all in place though.
First, slip the shaft into the tunnel and start it in the chaincase bearing. Slide the threaded rod inside and attach the backup plate to the caliper end. I used a folded rag to center the shaft in the hole so the other end would start straight in the bearing. Coat the bearing and seal surface with molly paste so the surface does not gall during the pressing process.
Put the cup over the end of the shaft and thread on the nut. Crank the nut with a wrench and the shaft will pull into the bearing. You can feel the interference fit when you turn the nut as the shaft goes through the bearing. This will never spin. I had a steel shim laser cut 0.030 thick on the shaft first to space the bearing off the shoulder. This makes the gears and snap ring a very close fit so the shaft does not try to walk in and out of the bearing. When the bearing bottoms on the shoulder and shim, you will feel the nut stop turning. Remove the nut and cup.
Move the backup plate over to the chaincase end. Coat the caliper end of the shaft with molly paste and slip the caliper over the shaft. Install the cup and nut, and start pulling the shaft into the bearing.
As you turn the nut and force the bearing on, look under the tunnel and watch the circlip. Stop turning the nut when the bearing touches the circlip. It is in place.
Remove the nut, cup and threaded rod. You are done with it now. The bearings are installed and cannot spin on the shaft. Continue assembling the seal plate and caliper bolts and torque in place. Spin the shaft and note the nice smooth action and that the caliper DOES NOT wobble.
I designed a nice CNC machined T6061 aluminum seal plate made to stop water from getting to the tunnel side of the bearing. Every year, I found my bearing had the grease washed out and was rusting. This may solve that problem. The OEM plate is junk and you can bend it in your bare hands. It is always bent and has a gap between it and the tunnel allowing water in behind it. This plate is solid and I have a gasket between it and the tunnel along with thick stainless washers and stainless bolts.
The kit looks like this.
Once this is installed, you may wonder how do I get it apart to change a bearing or a track. Well you need to make a special tool to pull the caliper. Here goes.
This part is a machined puller button to place in the ends of the hollow shaft to pull against. The pilot shoulder stops it from slipping down when you install the puller.
The actual puller looks like this.
When installed, it looks like this.
Turn the bolt and the caliper comes right off.
On the chaincase side, remove the spiral lock bearing retainer from the groove. Heat the chaincase around the bearing with a heat gun for a few minutes. Push the shaft and bearing through the case. It will come out VERY easily. Attach a 3 jaw puller to the bearing against the shaft plug, and pull off the bearing. It is now apart.
If you need to change the bearing in the brake caliper, I have a nice tool for that too. This is stack of laser cut disks and a laser cut tube thicker than the width of the bearing. Depending on how it is assembled, it will effortlessly remove or install the bearing. Here goes.
Assembled like this, the bolt draws the bearing into the tube as the nut is turned. When it is fully removed, the housing falls off the tool. The small disk pulls on the inner race.
The tube pushes on the housing and pulls the bearing into the tube.
To install the bearing the tool is assembled differently to push the bearing in by the outer race.
And this is how I turned this turd of a driveshaft design into something that has the chance to run trouble free using standard bearings available anywhere. I think the seal plate is nice touch. The original is such a piece of junk, that it probably does nothing to protect the bearing from water. I am looking forward to reading your comments. Be kind, it took some time to post this.
BP
First of all, you need to drill out those rivets and remove the lower plastic belly pan pieces. I replaced with M5x0.8 mm aluminum rivnuts and M5 stainless large head screws. The hole at the top by the top shock mount got tapped for an M5x0.8 mm Helicoil insert. Now I can remove the plastic for an easy oil change and chaincase service.
The cup is 45mm ID x 2" long inside. The threaded rod is M10 12.9 grade as are the nuts so they won't easily strip. If you can't get this made, you can cut the outer race off three old bearings and stack them together with a plate with a hole in it. It will be very difficult holding it all in place though.
First, slip the shaft into the tunnel and start it in the chaincase bearing. Slide the threaded rod inside and attach the backup plate to the caliper end. I used a folded rag to center the shaft in the hole so the other end would start straight in the bearing. Coat the bearing and seal surface with molly paste so the surface does not gall during the pressing process.
Put the cup over the end of the shaft and thread on the nut. Crank the nut with a wrench and the shaft will pull into the bearing. You can feel the interference fit when you turn the nut as the shaft goes through the bearing. This will never spin. I had a steel shim laser cut 0.030 thick on the shaft first to space the bearing off the shoulder. This makes the gears and snap ring a very close fit so the shaft does not try to walk in and out of the bearing. When the bearing bottoms on the shoulder and shim, you will feel the nut stop turning. Remove the nut and cup.
Move the backup plate over to the chaincase end. Coat the caliper end of the shaft with molly paste and slip the caliper over the shaft. Install the cup and nut, and start pulling the shaft into the bearing.
As you turn the nut and force the bearing on, look under the tunnel and watch the circlip. Stop turning the nut when the bearing touches the circlip. It is in place.
Remove the nut, cup and threaded rod. You are done with it now. The bearings are installed and cannot spin on the shaft. Continue assembling the seal plate and caliper bolts and torque in place. Spin the shaft and note the nice smooth action and that the caliper DOES NOT wobble.
I designed a nice CNC machined T6061 aluminum seal plate made to stop water from getting to the tunnel side of the bearing. Every year, I found my bearing had the grease washed out and was rusting. This may solve that problem. The OEM plate is junk and you can bend it in your bare hands. It is always bent and has a gap between it and the tunnel allowing water in behind it. This plate is solid and I have a gasket between it and the tunnel along with thick stainless washers and stainless bolts.
The kit looks like this.
Once this is installed, you may wonder how do I get it apart to change a bearing or a track. Well you need to make a special tool to pull the caliper. Here goes.
This part is a machined puller button to place in the ends of the hollow shaft to pull against. The pilot shoulder stops it from slipping down when you install the puller.
The actual puller looks like this.
When installed, it looks like this.
Turn the bolt and the caliper comes right off.
On the chaincase side, remove the spiral lock bearing retainer from the groove. Heat the chaincase around the bearing with a heat gun for a few minutes. Push the shaft and bearing through the case. It will come out VERY easily. Attach a 3 jaw puller to the bearing against the shaft plug, and pull off the bearing. It is now apart.
If you need to change the bearing in the brake caliper, I have a nice tool for that too. This is stack of laser cut disks and a laser cut tube thicker than the width of the bearing. Depending on how it is assembled, it will effortlessly remove or install the bearing. Here goes.
Assembled like this, the bolt draws the bearing into the tube as the nut is turned. When it is fully removed, the housing falls off the tool. The small disk pulls on the inner race.
The tube pushes on the housing and pulls the bearing into the tube.
To install the bearing the tool is assembled differently to push the bearing in by the outer race.
And this is how I turned this turd of a driveshaft design into something that has the chance to run trouble free using standard bearings available anywhere. I think the seal plate is nice touch. The original is such a piece of junk, that it probably does nothing to protect the bearing from water. I am looking forward to reading your comments. Be kind, it took some time to post this.
BP
Fords4life
Expert
- Joined
- Dec 7, 2021
- Messages
- 325
- Age
- 58
- Location
- South Dakota
- Country
- USA
- Snowmobile
- 2021 riot 9000 & 2017 sw rtx
You are 100% correct on a proper fix, well done with your tools you made as well with the seal plate you made, any thoughts of marketing this as a kit for us??? Minus the drive axle.So many things have been done to try to fix the driveshaft/bearing fit. I finally fixed it right. Get your driveshaft turned, spray welded and ground to final size on size fit with new bearings on BOTH ends. The spray weld/machining cost me $275 Canadian plus tax. Cheaper than a new shaft that will still destroy itself. There is no key, no set screws, no welded tab like I tried before. Just a proper interference fit. The bearings will not spin and you don't need a one of a kind special bearing. The challenge is to put it together and take it apart in the future. I have documented the special tools that I had made to do this. Here goes. Assembling the shaft.
First of all, you need to drill out those rivets and remove the lower plastic belly pan pieces. I replaced with M5x0.8 mm aluminum rivnuts and M5 stainless large head screws. The hole at the top by the top shock mount got tapped for an M5x0.8 mm Helicoil insert. Now I can remove the plastic for an easy oil change and chaincase service.
View attachment 176974
View attachment 176975
View attachment 176976
The cup is 45mm ID x 2" long inside. The threaded rod is M10 12.9 grade as are the nuts so they won't easily strip. If you can't get this made, you can cut the outer race off three old bearings and stack them together with a plate with a hole in it. It will be very difficult holding it all in place though.
First, slip the shaft into the tunnel and start it in the chaincase bearing. Slide the threaded rod inside and attach the backup plate to the caliper end. I used a folded rag to center the shaft in the hole so the other end would start straight in the bearing. Coat the bearing and seal surface with molly paste so the surface does not gall during the pressing process.
View attachment 176977
Put the cup over the end of the shaft and thread on the nut. Crank the nut with a wrench and the shaft will pull into the bearing. You can feel the interference fit when you turn the nut as the shaft goes through the bearing. This will never spin. I had a steel shim laser cut 0.030 thick on the shaft first to space the bearing off the shoulder. This makes the gears and snap ring a very close fit so the shaft does not try to walk in and out of the bearing. When the bearing bottoms on the shoulder and shim, you will feel the nut stop turning. Remove the nut and cup.
View attachment 176978
Move the backup plate over to the chaincase end. Coat the caliper end of the shaft with molly paste and slip the caliper over the shaft. Install the cup and nut, and start pulling the shaft into the bearing.
View attachment 176979
As you turn the nut and force the bearing on, look under the tunnel and watch the circlip. Stop turning the nut when the bearing touches the circlip. It is in place.
Remove the nut, cup and threaded rod. You are done with it now. The bearings are installed and cannot spin on the shaft. Continue assembling the seal plate and caliper bolts and torque in place. Spin the shaft and note the nice smooth action and that the caliper DOES NOT wobble.
View attachment 176980
I designed a nice CNC machined T6061 aluminum seal plate made to stop water from getting to the tunnel side of the bearing. Every year, I found my bearing had the grease washed out and was rusting. This may solve that problem. The OEM plate is junk and you can bend it in your bare hands. It is always bent and has a gap between it and the tunnel allowing water in behind it. This plate is solid and I have a gasket between it and the tunnel along with thick stainless washers and stainless bolts.
View attachment 176985
View attachment 176986
View attachment 176987
View attachment 176988
View attachment 176989
The kit looks like this.
View attachment 176990
Once this is installed, you may wonder how do I get it apart to change a bearing or a track. Well you need to make a special tool to pull the caliper. Here goes.
This part is a machined puller button to place in the ends of the hollow shaft to pull against. The pilot shoulder stops it from slipping down when you install the puller.
View attachment 176991
View attachment 176992
The actual puller looks like this.
View attachment 176993
View attachment 176994
When installed, it looks like this.
View attachment 176995
View attachment 176996
Turn the bolt and the caliper comes right off.
On the chaincase side, remove the spiral lock bearing retainer from the groove. Heat the chaincase around the bearing with a heat gun for a few minutes. Push the shaft and bearing through the case. It will come out VERY easily. Attach a 3 jaw puller to the bearing against the shaft plug, and pull off the bearing. It is now apart.
View attachment 176997
View attachment 176998
If you need to change the bearing in the brake caliper, I have a nice tool for that too. This is stack of laser cut disks and a laser cut tube thicker than the width of the bearing. Depending on how it is assembled, it will effortlessly remove or install the bearing. Here goes.
View attachment 176999
View attachment 177000
Assembled like this, the bolt draws the bearing into the tube as the nut is turned. When it is fully removed, the housing falls off the tool. The small disk pulls on the inner race.
View attachment 177001
The tube pushes on the housing and pulls the bearing into the tube.
View attachment 177002
View attachment 177003
To install the bearing the tool is assembled differently to push the bearing in by the outer race.
View attachment 177004
View attachment 177005
And this is how I turned this turd of a driveshaft design into something that has the chance to run trouble free using standard bearings available anywhere. I think the seal plate is nice touch. The original is such a piece of junk, that it probably does nothing to protect the bearing from water. I am looking forward to reading your comments. Be kind, it took some time to post this.
BP
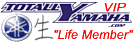

1nc 2000
Lifetime Member Tim
- Joined
- Feb 26, 2010
- Messages
- 3,070
- Location
- Marquette, MI
- Country
- USA
- Snowmobile
- Yamaha FX Nytro RTX SE
Nice work!
Put a grease fitting on the plate you made and remove inner seal off bearing.
Give the bearing some extra life and enjoy less maintenance.
Put a grease fitting on the plate you made and remove inner seal off bearing.
Give the bearing some extra life and enjoy less maintenance.

100MPH
VIP Member
- Joined
- Oct 11, 2024
- Messages
- 8
- Age
- 56
- Location
- Badger State
- Country
- USA
- Snowmobile
- 2020 Yamaha SRX LE
2004 Yamaha RX-1 L
2003 Yamaha 700 SX Viper ER
1997 Yamaha 700 SX
1994 Yamaha V-Max4
1991 Yamaha Exciter2 LE
1983 Yamaha Bravo
Nice post, all of the details covered. Spray weld/machining anyone have a source for this portion of the repair State side? Big Pussy gets these installation kits put together we'll all have forever driveshafts. I do like the grease fitting idea even on the tunnel side only just to keep the water out. Thanks for taking the time to share.
Sevey
TY 4 Stroke God
- Joined
- Feb 15, 2011
- Messages
- 1,756
- Location
- Collingwood, ON
- Website
- www.ty4stroke.com
- Country
- Canada
- Snowmobile
- 2018 Sidewinder RTX
Thats awesome. Great job.
How did you make the machined 'cup' to seat the bearing onto the shaft - pulling on the bearings ID?
Is that pipe you welded a block on the end?
MS
How did you make the machined 'cup' to seat the bearing onto the shaft - pulling on the bearings ID?
Is that pipe you welded a block on the end?
MS
Sevey
TY 4 Stroke God
- Joined
- Feb 15, 2011
- Messages
- 1,756
- Location
- Collingwood, ON
- Website
- www.ty4stroke.com
- Country
- Canada
- Snowmobile
- 2018 Sidewinder RTX
Will you put contemplating making any or all of these for sale?
MS
MS
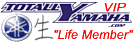

Turboflash
Lifetime Member
- Joined
- Mar 18, 2019
- Messages
- 2,502
- Location
- Southern MN
- Country
- USA
- Snowmobile
- '17 ZR9000 Ltd. 137 - PEFI Stage 4
I did this (interference fit bearings/ie press fit) 5 years ago and happy to report all is well with both tracks shaft bearings. No driveshaft saver necessary, no spinning, no wobbling rotor, no flexing tunnel). Both bearings are happy. I do regrease clutch side bearing. I use puller fabricated using template Travis at BOP supplied to this site about 3-4 years ago. Works perfectly.
I used a pusher similar to what BP posted that I made.
I think it's the ultimate fix for this issue on Procross chassis.
I used a pusher similar to what BP posted that I made.
I think it's the ultimate fix for this issue on Procross chassis.
Big Pussy
Extreme
- Joined
- Apr 12, 2016
- Messages
- 94
- Age
- 66
- Location
- Woodstock, Ont
- Country
- Canada
- Snowmobile
- 2015 XF7000 LXR
It would be pretty easy to add a high boss on the top rear corner of the seal circle and drill and tap for a zerk, as well as machining a grease channel on the flat side to flow the grease to the caliper side of the seal, I think the grease will just fill the area and then come out the space between the caliper and the tunnel. You can see the shaft looking down the tunnel. The shaft may fling the grease on to the rotor and make a hell of a mess. A seal between the caliper and tunnel would be required to make this work. Maybe some weather strip stuck to the rear of the caliper in a circle crushed against the tunnel would work.Nice work!
Put a grease fitting on the plate you made and remove inner seal off bearing.
Give the bearing some extra life and enjoy less maintenance.
Big Pussy
Extreme
- Joined
- Apr 12, 2016
- Messages
- 94
- Age
- 66
- Location
- Woodstock, Ont
- Country
- Canada
- Snowmobile
- 2015 XF7000 LXR
I wanted to do this a few years ago, but did not know where to get the spray weld/machining done. When I went to 4 days work a week, I had fridays to look around. Turns out, the very first place I went to right here in Woodstock does spray welding and had done two of these shafts already. I have had then do two shafts so far. I mark the bearing surface with a paint stick so they can't get it wrong, and leave them a new bearing to measure. The surface is machined down and then sprayed to build it up while the other surfaces are covered in a brushed on material so the spray won't stick. Then it is rough machined and final ground to size. This is all done in a lathe. The shaft/bearing is pretty much size on size. I measure the shaft at 1.7719 " when they are done.Nice post, all of the details covered. Spray weld/machining anyone have a source for this portion of the repair State side? Big Pussy gets these installation kits put together we'll all have forever driveshafts. I do like the grease fitting idea even on the tunnel side only just to keep the water out. Thanks for taking the time to share.
They are
Whitelaw Machinery
572 Main St, Woodstock, ON N4S 1V6
(519) 539-1287
Ask for Gary.
I think if you phone machine shops in your area and ask, you will find many places that can do this work. It is pretty common today. You don't want to be shipping driveshafts all over the country. I like driving there and talking in person. Whitelaw's specialty is truing up and then corrugating the surface of large milling rolls. The kind used to roll oaks and make Quaker Oats for your breakfast.
Big Pussy
Extreme
- Joined
- Apr 12, 2016
- Messages
- 94
- Age
- 66
- Location
- Woodstock, Ont
- Country
- Canada
- Snowmobile
- 2015 XF7000 LXR
I don't do any of the machining. I have a buddy that I go riding with that has a fab and machining shop. The both of use keep four sleds running and we design the fixes and he makes the parts. The cup is machined out of a solid piece of bar stock in a lathe by drilling the end and then cutting the ID using a boring bar over and over until the ID is to size.. The outside is turned too first. A boring bar is an inside cutter on a bar that goes inside the spinning part.Thats awesome. Great job.
How did you make the machined 'cup' to seat the bearing onto the shaft - pulling on the bearings ID?
Is that pipe you welded a block on the end?
MS
This is sometimes easier than making it out of pipe because the pipe will need boring anyway to get a nice close fit to the shaft.
Big Pussy
Extreme
- Joined
- Apr 12, 2016
- Messages
- 94
- Age
- 66
- Location
- Woodstock, Ont
- Country
- Canada
- Snowmobile
- 2015 XF7000 LXR
We have to talk about it. What parts would you all like to buy ?Will you put contemplating making any or all of these for sale?
MS
Caliper bearing removal/install tool kit. (Made of steel and very heavy for its size with all the disks..)
Cailper puller plate with pull bolt
Puller shaft plug to pull against for both ends of the shaft.
Bearing pusher cup for the threaded rod.
Puller backup plate for the threaded rod.
Threaded rod with nuts. M10 or 3/8" threaded rod will work.
CNC seal plate with gasket and stainless bolts and thick washers.
All this could be heavy to ship. I don't think shipping in Canada is a problem. Shipping to the US needs to be looked into.
That is a great fix for sure and many of had sucess with all the others too but as much as people will disagree with me I run absolutely nothing at all on 2023 and newer shafts. Does it slip? Im sure it does because fit isnt any better but having equal hardness as the bearing it doesnt wear anything. 4400 miles on my riot Turbo and did run shaft saver for a few miles at first but ended up tossing it. Wifes riot has nearly 3000 miles with nothing at all and all is good. I believe stone88 had posted he had over 2500 miles on a 23 shaft with nothing and it measured identical to new. Talked to many others who have used nothing on the updated shafts with no issues. Local dealer hasnt replaced any on the sleds sold in since the driveshaft was updated. Their fix wasnt what everyone wanted but for me the driveshaft is an afterthought now so thats an improvement
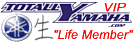

STAIN
Lifetime Member
- Joined
- Feb 29, 2004
- Messages
- 4,195
- Location
- Vermont
- Country
- USA
- Snowmobile
- 2022 SIDEWINDER LTX GT
- LOCATION
- Vermont
I saw a T-Cat with 5k on the shaft and it looked new. At 7500 it was trash. you never know.That is a great fix for sure and many of had sucess with all the others too but as much as people will disagree with me I run absolutely nothing at all on 2023 and newer shafts. Does it slip? Im sure it does because fit isnt any better but having equal hardness as the bearing it doesnt wear anything. 4400 miles on my riot Turbo and did run shaft saver for a few miles at first but ended up tossing it. Wifes riot has nearly 3000 miles with nothing at all and all is good. I believe stone88 had posted he had over 2500 miles on a 23 shaft with nothing and it measured identical to new. Talked to many others who have used nothing on the updated shafts with no issues. Local dealer hasnt replaced any on the sleds sold in since the driveshaft was updated. Their fix wasnt what everyone wanted but for me the driveshaft is an afterthought now so thats an improvement
A complete shaft with drivers was around $300 The last time I checked on Paritzilla. If I get two seasons out of it, I will buy a new one and put it on if my driveshaft decides to wear out. That is a lot better than the 1200 miles I had on my 2020 with excessive wear.Half the gadgets they sell are nearly 1/2 the price of a new shaft and can introduce vibrations and a bunch of other issues when not installed properly and sometimes don’t work properly because they weren’t installed right in the first place. I have yet to see any issues with the latest updated shaft but maybe they just take longer to appear. Who knows? Moral of the story is to not worry about it too much if you’re on a newer sled or have an updated shaft.
Sevey
TY 4 Stroke God
- Joined
- Feb 15, 2011
- Messages
- 1,756
- Location
- Collingwood, ON
- Website
- www.ty4stroke.com
- Country
- Canada
- Snowmobile
- 2018 Sidewinder RTX
The cup to press the bearing on in the caliper assembly and the new fancy machined plate on the inside of the tunnel.We have to talk about it. What parts would you all like to buy ?
Caliper bearing removal/install tool kit. (Made of steel and very heavy for its size with all the disks..)
Cailper puller plate with pull bolt
Puller shaft plug to pull against for both ends of the shaft.
Bearing pusher cup for the threaded rod.
Puller backup plate for the threaded rod.
Threaded rod with nuts. M10 or 3/8" threaded rod will work.
CNC seal plate with gasket and stainless bolts and thick washers.
All this could be heavy to ship. I don't think shipping in Canada is a problem. Shipping to the US needs to be looked into.
MS
Similar threads
- Replies
- 327
- Views
- 54K
- Replies
- 6
- Views
- 3K
-
This site uses cookies to help personalise content, tailor your experience and to keep you logged in if you register.
By continuing to use this site, you are consenting to our use of cookies.