SW Primary bolt Torque:
TD recommendations:
1st 110 ft/lbs
2nd 60 ft/lbs
Yamaha Specs:
1st 108 ft/lbs
2nd 43 ft/lbs
Apex Primary bolt Torque:
Yamaha specs:
1st 85 ft/lbs
2nd 43 ft/lbs
So begs the question...when using an Apex clutch on a SW which torque specs should you use?
I personally stayed with the SW clutch torque specs with Apex clutch on my SW but I had a 300++ hp Apex that I ran Apex clutch torque specs on without any issues.
Torque specs are relative to the bolt, the threads, and the use case. (assuming some kind of realistic design). What matters is the final torque, that first torque spec is just to make sure the clutch is seated properly.

PowderFalcon
Pinnin' it!
I am in the exact same boat! Apex clutch but with sidewinder bolt! hmmmSW Primary bolt Torque:
TD recommendations:
1st 110 ft/lbs
2nd 60 ft/lbs
Yamaha Specs:
1st 108 ft/lbs
2nd 43 ft/lbs
Apex Primary bolt Torque:
Yamaha specs:
1st 85 ft/lbs
2nd 43 ft/lbs
So begs the question...when using an Apex clutch on a SW which torque specs should you use?
I personally stayed with the SW clutch torque specs with Apex clutch on my SW but I had a 300++ hp Apex that I ran Apex clutch torque specs on without any issues.
While their is a science behind torque, I don't know how TD came up with the number they did as 'torque' only equals 'clamping force' in near perfect conditions. IMO the TD recommendation may be from experience where they may have had some problems in testing. As an example, a bolt with imperfect threads or dirty threads will have a different clamping force than one that is both perfect and clean - despite having the same torque applied. Maybe they had one come loose that was not really at the proper clamping force due to dirty threads.. who knows. Also, bolt stretch could come into play as a used bolt that has been torqued many times will experience fatigue. If Yamaha says 43lbs then that is an engineered target for torque/clamping force. In less than great conditions, a bit more equal likely better as you aren't really concerned with breaking something through slightly over torquing (e.g. chain case cover).. Split the difference between Yamaha and TD if you are worried as there is no way to measure actual clamping force, or buy a new bolt, clean the threads well, and torque to Yamahas spec.
JT I have no desire to see anyone stick with anything, you can fill the cavity with vaseline or elmers glue and it makes no difference to me. My point was that it includes grease in the kit that you are paying for when you buy it. Dave tested with that grease and it meets the heat and load requirements. People are going to start using grease they think is better and likely have poor results in long term noise reduction and fault the product. Dave tests alot before releasing and im sure he experimented with different greases too. There isnt really a one size fits all approach with grease IMO, ive spent well over $50,000 on grease over the past decade with my business and ive tried alot and they all have their pros and cons. A tube of grease specifically for this knockout kit would last someone years . Regardless what you pay for it, it will likely need periodic maintenance to keep it doing its job. That being said im sure there may be something better out there than whats included with the kit. I have a feeling theres going to be some posts down the road about how the kit works great for a few hundred miles and gets noisy again and it will likely be related to the grease someone used because they had a tube kicking around.I found the PI sheet for Valvoline Crimson grease. Sadly, Its limited temperature range of effectiveness would not meet the temperature conditions of my intended use. 25° - 250°
So ill have to fall back on Lucas Red & Tacky or like product for general maintenance.
Justin, while I appreciate the desire to stick with what ever Tapp recommends, I like to use what's been working and have the ability to use on other general maintenance. The "one tube works on everything" approach.
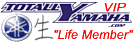

1nc 2000
Lifetime Member Tim
- Joined
- Feb 26, 2010
- Messages
- 3,048
- Location
- Marquette, MI
- Country
- USA
- Snowmobile
- Yamaha FX Nytro RTX SE
While their is a science behind torque, I don't know how TD came up with the number they did as 'torque' only equals 'clamping force' in near perfect conditions. IMO the TD recommendation may be from experience where they may have had some problems in testing. As an example, a bolt with imperfect threads or dirty threads will have a different clamping force than one that is both perfect and clean - despite having the same torque applied. Maybe they had one come loose that was not really at the proper clamping force due to dirty threads.. who knows. Also, bolt stretch could come into play as a used bolt that has been torqued many times will experience fatigue. If Yamaha says 43lbs then that is an engineered target for torque/clamping force. In less than great conditions, a bit more equal likely better as you aren't really concerned with breaking something through slightly over torquing (e.g. chain case cover).. Split the difference between Yamaha and TD if you are worried as there is no way to measure actual clamping force, or buy a new bolt, clean the threads well, and torque to Yamahas spec.
If you can remember back to the fall of 2016 the sidewinders were delivered with the same torque on clutch bolt as what yamaha used on their 4 strokes.
Due to the inferior Chinese metal used in the new sidewinder primary they were spinning on the stub shaft.
Yamaha then released a higher torque to seat the clutch and final torque.
Then we ended up with inconsistencies in clutch operation due to sticking of the primary as it heated up.
Put that primary on the shelf and installed older fx nytro primary and the clutching issues went away.
I torque the fx nytro primary same on sidewinder as I do my japan sleds. No issues.
Carry on...

max rolph
Expert
- Joined
- Feb 10, 2021
- Messages
- 447
- Age
- 60
- Location
- horse shoe valley
- Country
- Canada
- Snowmobile
- 998 turbo
i BELIEVE dave would have done his due diligents to get the best grease for temp and pressure available, but whos to say something better doesnt come along.... i my self have kit coming and will use the supplied substance, but after will prob research the tackiest,, highest temp lithium synthetic available.... prob amsoil race
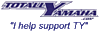
Doc Harley
TY 4 Stroke God
- Joined
- Oct 17, 2016
- Messages
- 3,406
- Age
- 55
- Location
- Here & there
- Country
- USA
- Snowmobile
- '17 Sidewinder LTX SE
Until you mentioned it, I didn't realize grease was included. It will be considered. I was completely unaware of you're Intricate background with lubrication products. That also will be noted, and appreciated during future conversations.
Last edited:
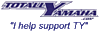
Doc Harley
TY 4 Stroke God
- Joined
- Oct 17, 2016
- Messages
- 3,406
- Age
- 55
- Location
- Here & there
- Country
- USA
- Snowmobile
- '17 Sidewinder LTX SE
Amsoil is looking promising. They're load rating is a bit higher then both Lucus and Mobil 1. just need to keep digging.i BELIEVE dave would have done his due diligents to get the best grease for temp and pressure available, but whos to say something better doesnt come along.... i my self have kit coming and will use the supplied substance, but after will prob research the tackiest,, highest temp lithium synthetic available.... prob amsoil race
Turboflash
TY 4 Stroke God
- Joined
- Mar 18, 2019
- Messages
- 2,443
- Location
- Southern MN
- Country
- USA
- Snowmobile
- '17 ZR9000 Ltd. 137 - PEFI Stage 4
IMO, whatever torque one decides on, the goal is to get clutch securely seated on stub and make sure it never slips or spins on stub. That gets ugly fast. The number 1 thing to do to virtually guarantee the clutch won't slip on stub is always lap the clutch to the stub prior to install. This gets the two tapers to match better for sure and get maximum contact between the two. Once you do that, you can tell right away because even with just hand tightening the bolt with your fingers, or even just banging to clutch onto stub with your hand, you will need a puller to get it back off.While their is a science behind torque, I don't know how TD came up with the number they did as 'torque' only equals 'clamping force' in near perfect conditions. IMO the TD recommendation may be from experience where they may have had some problems in testing. As an example, a bolt with imperfect threads or dirty threads will have a different clamping force than one that is both perfect and clean - despite having the same torque applied. Maybe they had one come loose that was not really at the proper clamping force due to dirty threads.. who knows. Also, bolt stretch could come into play as a used bolt that has been torqued many times will experience fatigue. If Yamaha says 43lbs then that is an engineered target for torque/clamping force. In less than great conditions, a bit more equal likely better as you aren't really concerned with breaking something through slightly over torquing (e.g. chain case cover).. Split the difference between Yamaha and TD if you are worried as there is no way to measure actual clamping force, or buy a new bolt, clean the threads well, and torque to Yamahas spec.
Fast
TY 4 Stroke Guru
- Joined
- Sep 25, 2018
- Messages
- 967
- Age
- 56
- Location
- Ontario
- Country
- Canada
- Snowmobile
- 2019 srx,2006 apex gt,96 storm hot to go
Where are you getting this kit from, is there a part number?It seems to me that items that have to get shipped across the border have been taking a bit more time lately.
I ordered a part from a shop in Canada that is only 2 hours away and it took a week to get here.
ryama
Expert
- Joined
- Mar 3, 2009
- Messages
- 209
- Location
- Kitchener Ontario
- Country
- Canada
- Snowmobile
- Sidewinder R-TX
- LOCATION
- Kitchener
Well installed the Knockout kit and started my sled up today. All I can say, if it last. This is the best money I have spend on my sled ever!
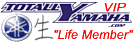

1nc 2000
Lifetime Member Tim
- Joined
- Feb 26, 2010
- Messages
- 3,048
- Location
- Marquette, MI
- Country
- USA
- Snowmobile
- Yamaha FX Nytro RTX SE
max rolph
Expert
- Joined
- Feb 10, 2021
- Messages
- 447
- Age
- 60
- Location
- horse shoe valley
- Country
- Canada
- Snowmobile
- 998 turbo
just a question, when pulling snub out, the factory crank seal comes out with it, is there any specific process when putting snub back in ... that makes sure the seal goes squarely in and should you put loc tite around it or silicone to be sure its in tight. n sealed
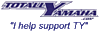
Doc Harley
TY 4 Stroke God
- Joined
- Oct 17, 2016
- Messages
- 3,406
- Age
- 55
- Location
- Here & there
- Country
- USA
- Snowmobile
- '17 Sidewinder LTX SE
Is it like getting a new sled? Lol. I bet it is....Well installed the Knockout kit and started my sled up today. All I can say, if it last. This is the best money I have spend on my sled ever!

Clintww
VIP Member
- Joined
- Mar 6, 2022
- Messages
- 108
- Age
- 53
- Location
- Central MN
- Country
- USA
- Snowmobile
- 2001 SXR. 2005 RX1. 2017 Sidewinder
- LOCATION
- MN
I was wondering this too. I think I used a light coating of grease since it was in so hard I ruined it getting it off.just a question, when pulling snub out, the factory crank seal comes out with it, is there any specific process when putting snub back in ... that makes sure the seal goes squarely in and should you put loc tite around it or silicone to be sure its in tight. n sealed
Similar threads
- Replies
- 21
- Views
- 33K
- Replies
- 25
- Views
- 46K
-
This site uses cookies to help personalise content, tailor your experience and to keep you logged in if you register.
By continuing to use this site, you are consenting to our use of cookies.