yukon yamaha
TY 4 Stroke Master
- Joined
- Jan 30, 2008
- Messages
- 1,092
- Age
- 39
- Location
- WHITEHORSE, YUKON CANADA
- Country
- Canada
- Snowmobile
- 2008 nytro custom! 2014 viper custom
DUDE YOU HAVE TO HAVE THE COOLEST PROJECTS ON THE GO!
I check your page every day to see all the new updates and picts!
thanks for taking the time to do it
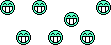
I check your page every day to see all the new updates and picts!
thanks for taking the time to do it

rxrider
Jan-Ove Pedersen
- Joined
- Apr 25, 2003
- Messages
- 7,355
- Age
- 60
- Location
- Lakselv - 70N & 25E
- Country
- Norway
- Snowmobile
- 2014 Phazer XTX, 2013 Phazer RTX, 2008 Apex RTX, 2007 Warrior, 2006 Attak
Thanks yukon yamaha - remarks like that gives me the inspiration to go on documenting my everlasting project. It's nice to know that this thread is helpful and inspireing for other sled heads
More work have been done but not yet posted in here. Will do tonight.
More work have been done but not yet posted in here. Will do tonight.
Need for Speed 2
TY 4 Stroke Junkie
Jan-Ove a tip I use when plumbing my meth. As the line comes out of the pump put a t in that line where it fits best and bring the meth in from both ends of yournozzles . It keeps a better, consistent flow pattern that way, easy to do. Hope this helps
rxrider
Jan-Ove Pedersen
- Joined
- Apr 25, 2003
- Messages
- 7,355
- Age
- 60
- Location
- Lakselv - 70N & 25E
- Country
- Norway
- Snowmobile
- 2014 Phazer XTX, 2013 Phazer RTX, 2008 Apex RTX, 2007 Warrior, 2006 Attak
Thanks Kevin
I'm close to finish the assembly up front in my sled.
We were thinking of placing an auxillary fuel tank up in the nose of the sled to avoid running out of fuel on a long climb up the mountains. We have now ditched that idea and are going for a catch tank inside the fuel tank for the pickup.
My header is now welded up, I've got an hairline crack 1" long. My whole header come loose when 6 bolts unscrewed themselves, also 2 of the bolts holding the turbo to the header came loose. No wonder the header cracked, all my fault for not looking after the header and bolts all season.
I found that the header mounting plate that mounts to the engine is slightly warped, like 1 mm higher in the middle than out on the edges. I decided that haveing it resurfaced on a CNC would be the best solution. Unluckily the machine shop haven't got the time to do the work yet, they got it a month ago..... grrrrr. What can I say I'm falling behind on my schedule.
Time to upload some more pics
I'm close to finish the assembly up front in my sled.
We were thinking of placing an auxillary fuel tank up in the nose of the sled to avoid running out of fuel on a long climb up the mountains. We have now ditched that idea and are going for a catch tank inside the fuel tank for the pickup.
My header is now welded up, I've got an hairline crack 1" long. My whole header come loose when 6 bolts unscrewed themselves, also 2 of the bolts holding the turbo to the header came loose. No wonder the header cracked, all my fault for not looking after the header and bolts all season.
I found that the header mounting plate that mounts to the engine is slightly warped, like 1 mm higher in the middle than out on the edges. I decided that haveing it resurfaced on a CNC would be the best solution. Unluckily the machine shop haven't got the time to do the work yet, they got it a month ago..... grrrrr. What can I say I'm falling behind on my schedule.
Time to upload some more pics
Buy locking fastners from Impulse to secure your header - that should take care of your problem Jan-Ove:
http://impulseturbo.com/accessories.html
http://impulseturbo.com/accessories.html
rxrider
Jan-Ove Pedersen
- Joined
- Apr 25, 2003
- Messages
- 7,355
- Age
- 60
- Location
- Lakselv - 70N & 25E
- Country
- Norway
- Snowmobile
- 2014 Phazer XTX, 2013 Phazer RTX, 2008 Apex RTX, 2007 Warrior, 2006 Attak
What is locking fastners? I have Norlocks.
We will most likely modify the bolts and use locking wire to secure the bolts, my friend Odd-Steffen is bringing on aircraft metods to our sleds
Uhhhhh didn't see your link right away duhhhh
Great idea buddy
We will most likely modify the bolts and use locking wire to secure the bolts, my friend Odd-Steffen is bringing on aircraft metods to our sleds
Uhhhhh didn't see your link right away duhhhh
Great idea buddy
rxrider
Jan-Ove Pedersen
- Joined
- Apr 25, 2003
- Messages
- 7,355
- Age
- 60
- Location
- Lakselv - 70N & 25E
- Country
- Norway
- Snowmobile
- 2014 Phazer XTX, 2013 Phazer RTX, 2008 Apex RTX, 2007 Warrior, 2006 Attak
Update November 28. - Installing meth injection Part 2. Preparing for water temp sensor and gauge install. Installing boost controller and meth failsafe bypass solenoid. Preparing for a different install of the meth reservoir.
Saturday afternoon I continued with the meth injection install. I put the IC onto the carbs and started to make new meth line routing. I had the meth injectors underneat the IC last season. This season the injectors are on the top of the IC plenum.
Done with routing of the meth lines
The IC is removed to have room to finish some other work up front.
I have bought a water temp sensor, a tube to install into the coolant hose for the sensor and a gauge to read the water temp. Installing wireing for light, ground, lead, and sensor signal input. I still need a gauge pod to install the water gauge into.
The gauge measures in Centigrades or degrees Celcius.
While I was installing the Hallman Pro RX manual boost controller my friend got nosey and had a real close look at what I were up to. LOL
Here's a pic of the boost controller and the meth injection fail safe controller solenoid installed. I have a fail safe controller that measures flow of meth thru the system, the solenoid will open and bypass the boost controll in case I run out of meth or the nozzles are clogged.
I'm trying to position my meth reservoirs a bit different this time to save some space, I hope
Here's a few pics from my friends project Attak.
He is going to manufacture a exhaust muffler out of his old MCXpress muffler. The muffler is supposed to go in the front of the tunnell. Here's a few pics of him cutting open the MCX muffler, it has to be shortened to fit underneat the tunnel.
Here's a few more tubes and bends that are going into the new muffler arrangement.
We're going to run VES exhaust cutout in combination with the restrictive mufflers to have max power when we need it and run quiet when we need to. It's a great way to get past the noise police. The system in the pic is only for reference, we're not going to run the ATP system in the pic. We're probably going to manufacture our own system based on what you see in this pic. The idea is that we can use a boost controller to control when the exhaust cutout will open. Plan is to make sure the exhaust goes thru the silencer/muffler when cruising down the trail at speed limit and when riding slowly in populated areas. When we reach a set pressure level the valve will start to open and will be completely open way before full boost. We don't want to add any back pressure running at full power thus the straight thru exhaust at any amount of boost.
Ourselves, we're running on junk fuel and beer LOL
Saturday afternoon I continued with the meth injection install. I put the IC onto the carbs and started to make new meth line routing. I had the meth injectors underneat the IC last season. This season the injectors are on the top of the IC plenum.


Done with routing of the meth lines

The IC is removed to have room to finish some other work up front.

I have bought a water temp sensor, a tube to install into the coolant hose for the sensor and a gauge to read the water temp. Installing wireing for light, ground, lead, and sensor signal input. I still need a gauge pod to install the water gauge into.


The gauge measures in Centigrades or degrees Celcius.

While I was installing the Hallman Pro RX manual boost controller my friend got nosey and had a real close look at what I were up to. LOL

Here's a pic of the boost controller and the meth injection fail safe controller solenoid installed. I have a fail safe controller that measures flow of meth thru the system, the solenoid will open and bypass the boost controll in case I run out of meth or the nozzles are clogged.

I'm trying to position my meth reservoirs a bit different this time to save some space, I hope


Here's a few pics from my friends project Attak.
He is going to manufacture a exhaust muffler out of his old MCXpress muffler. The muffler is supposed to go in the front of the tunnell. Here's a few pics of him cutting open the MCX muffler, it has to be shortened to fit underneat the tunnel.




Here's a few more tubes and bends that are going into the new muffler arrangement.

We're going to run VES exhaust cutout in combination with the restrictive mufflers to have max power when we need it and run quiet when we need to. It's a great way to get past the noise police. The system in the pic is only for reference, we're not going to run the ATP system in the pic. We're probably going to manufacture our own system based on what you see in this pic. The idea is that we can use a boost controller to control when the exhaust cutout will open. Plan is to make sure the exhaust goes thru the silencer/muffler when cruising down the trail at speed limit and when riding slowly in populated areas. When we reach a set pressure level the valve will start to open and will be completely open way before full boost. We don't want to add any back pressure running at full power thus the straight thru exhaust at any amount of boost.

Ourselves, we're running on junk fuel and beer LOL


rxrider
Jan-Ove Pedersen
- Joined
- Apr 25, 2003
- Messages
- 7,355
- Age
- 60
- Location
- Lakselv - 70N & 25E
- Country
- Norway
- Snowmobile
- 2014 Phazer XTX, 2013 Phazer RTX, 2008 Apex RTX, 2007 Warrior, 2006 Attak
Update December 2-3. - Installing water temp housing and sensor. Installing intercooler. Hooking up meth injection. Rerouting fuel- and fuel return lines. Preparing for new lines for cooling the turbo. Wrapping up the turbo header.
Last night my buddy came over to work on his sled, I joined him and got a few things done on my sled as well.
I started by installing the water temp housing and sensor to the hose coming from the bottom of the motor on the right hand side.
Next was installing the intercooler onto the carbs, tighten down the hose clamps holding it onto the carbs, then strap it down in the front to keep it from blowing off the carbs. I hooked up the meth lines to the feed line coming from the meth injection controllers.
Last season I had the turbo cooling plugged into the carb heating circuitry. I have learnt from Dave at Powder Lites that the flow is insufficient, so I'm going to follow his advice and connect the turbo into the hose coming from the oil cooler and connect the return line back into the thermostat housing. This will provide a much better flow of coolant thru the turbo.
Today I got a call from the machine shop, the header is finally done. I drove and picked it up right away. Great work, the header surface is completely flat. The guy at the machine shop said the header was warped at two axis, it both bent and twisted so they had to machine it from two different directions to make it perfectly flat. They also had to make a special device to hold the header firmly in place on the CNC machine. I'm very happy with the outcome even tho it took a month before I got it back, the wait is all forgotten now.
Here's a few pics of the header.
This time I'm going to wrap up the header with heat insulation to keep as much heat in the turbo as possible and at the same time reducing the underhood heat and rediant heat coming from the header. I used a fiber type insulation wrap with aluminum on the outside of the wrap. It's supposed to keep more heat inside because of the aluminum.
A spent a few hours this evening wrapping the header up. I used a thin stainless steel wire for fastening the wrapping to the header. I have a specially designed plier for twisting the wire until it's firmly tightened, it makes the use of wire darn easy
I started where the pipes are welded to the flange and worked my way up to the turbo flange. I added the wrapping a piece at the time, the pieces had to be fastened both on the end where I started and on the end of every wrap to keep it from unwinding. Lastly I added extra wireing to firmly secure the wrapping to the header.
Here's the end result.
Next work will be installing of the header to the motor

Last night my buddy came over to work on his sled, I joined him and got a few things done on my sled as well.
I started by installing the water temp housing and sensor to the hose coming from the bottom of the motor on the right hand side.

Next was installing the intercooler onto the carbs, tighten down the hose clamps holding it onto the carbs, then strap it down in the front to keep it from blowing off the carbs. I hooked up the meth lines to the feed line coming from the meth injection controllers.


Last season I had the turbo cooling plugged into the carb heating circuitry. I have learnt from Dave at Powder Lites that the flow is insufficient, so I'm going to follow his advice and connect the turbo into the hose coming from the oil cooler and connect the return line back into the thermostat housing. This will provide a much better flow of coolant thru the turbo.

Today I got a call from the machine shop, the header is finally done. I drove and picked it up right away. Great work, the header surface is completely flat. The guy at the machine shop said the header was warped at two axis, it both bent and twisted so they had to machine it from two different directions to make it perfectly flat. They also had to make a special device to hold the header firmly in place on the CNC machine. I'm very happy with the outcome even tho it took a month before I got it back, the wait is all forgotten now.
Here's a few pics of the header.


This time I'm going to wrap up the header with heat insulation to keep as much heat in the turbo as possible and at the same time reducing the underhood heat and rediant heat coming from the header. I used a fiber type insulation wrap with aluminum on the outside of the wrap. It's supposed to keep more heat inside because of the aluminum.

A spent a few hours this evening wrapping the header up. I used a thin stainless steel wire for fastening the wrapping to the header. I have a specially designed plier for twisting the wire until it's firmly tightened, it makes the use of wire darn easy
Here's the end result.



Next work will be installing of the header to the motor





rxrider
Jan-Ove Pedersen
- Joined
- Apr 25, 2003
- Messages
- 7,355
- Age
- 60
- Location
- Lakselv - 70N & 25E
- Country
- Norway
- Snowmobile
- 2014 Phazer XTX, 2013 Phazer RTX, 2008 Apex RTX, 2007 Warrior, 2006 Attak
Update December 8. - Preparing header bolts. Installing header. Preparing turbo. Installing turbo. Connecting and insulating water lines to turbo. Adding oil to the turbo oil inlet to lube turbine bearings. Installing pressure lines to boost controller and meth injection fail safe solenoid. Installing and insulating oil line. Insulating and installing downpipe. Making a aluminum heat sink for the O2-sensor.
I had a long day of work in the turbo garage tuesday afternoon, evening and night. Got a lot of work done.
Here I am publishing my work on TY, I'm uploading all my pics to www.photobucket.com and link them to my posts on TY. Saves space on the TY servers and helps reducing load on the same servers.
I lost 6 of 8 header bolts last season, I won't have that happen again. My friend Odd-Steffen had another aircraft way of making sure bolt stay put; He adviced me to use locking wire of mild steel to hold the bolt from unscrewing themselves. I had to drill 2mm holes in each bolt before installing the header.
Here's an example. I know it's all wrong, but it's only for reference LOL.
I cleaned up the exhaust outlets on the motor, tried to scrape off most of the carbon, added a solvent and wiped dry. Then I placed a new exhaust gasket in front of the exhaust outlets. It's impossible to get the gasket in place with the header put in place so the gasket had to go in first.
In put the header in place and moveded the gasket in position until I got the first bolt thru the header and gasket and into the threads, only tightened it down a tiny bit. Then I moved on with moving the gasket upwards until I was able to install the next bolt. With two bolt in place the rest of them went on quite easily.
I tightend down the bolts as tight as I could get them or as tight as I dared, whatever came first
Then I started threading the lock wire thru the holes I drilled in them. The wire is to be threaded so it will resist against any movement of the bolts holding them from unthreading.
I moved on to the turbo. I had both the rear bolt come loose last season, I won't have any of that happen again. It's impossible for me to install bolts from underneat as the header is not designed for it. Last year I cut a few 40mm bolt and threaded them in place from the upper side of the header flange, I installed a nut both at the turbo and under neat the header flange, well they unsrewed themselves and disappeared.
To keep this from happen again I decided it was better to use stock bolts threaded from above like the ones at the front of the turbo. On the rear right bolt hole I only had to file off a small amount to get the bolt in place. On the rear left hole there were no room on top to get a bolt thru so I had to cut away metal to the rear to be able to get the bolt in place. The rear left bolt has to be installed together with the 2 Norlocks before the turbo is installed. Here's a pic of the turbo after the preparation.
This is how it looks like with the bolts in place.
I tightened down the turbo and went on installing water lines to the turbo.
Last year I had the coolant line plugged into the carburetor heating circuitry. I have learnt that it's not sufficient flow to cool the turbo effectively. I have now plugged the turbo coolant lines into the oil cooler circuitry. Line goes from the oil cooler to the turbo and returns into the thermostat housing.
Before installing the oil feed line to the turbo I added some oil to the oil inlet at the turbo to make sure the turbine have oil when I start up the engine. Prior to oiling the turbo the turbine hardly spun at all after giving it a spin, it stopped rather quickly. After oiling the turbo the turbine spun for quite a while before it stopped. It does need oil or the bearings will seize on startup, it's important to oil the turbo before every season as it will dry out during summer storage.
Installing pressure lines to boost controller and meth injection fail safe solenoid.
With all water and oil lines connected to the turbo I started to add heat insulation to the lines.
I decided to add heat insulating wrapping to the downpipe as well since I had enough left from insulating the header.
I installed the downpipe and added some more wrapping to the downpipe, turbo and header.
I still have some more insulating to do before It's done, you may recognize the turbo blanket to the right in the pic, it's going to be wrapped around the turbine housing before the heat shields is installed.
Last thing I did was manufacturing a heat sink out of 14gz or 1.5mm aluminum sheet metal. I have a hard time getting hold of copper as the manual calls for so I chose to go with second best as aluminum is a good heat conductor. Now I pray it doesn't melt
My frind Odd-Steffen is modifying some stuff in the tunnel. He's working on the exhaust cutout and muffler that's going to be installed up front in the tunnel.
It's going to be a nice setup, allowing the sled to run in two different modes. When exhaust is routed thru the muffler it's in trail mode and when the it's in race mode all exhaust is dropped directly into the tunnel thru a straight pipe no muffler
We're also working to make this system adjustable be setting up one or more air toggle switches to bleed off air. When bleeding off air the sled will be in trail mode and will pass the noise police. Tipping the first toggle switch will send more air to the actuator controlling the cutout valve, now the sled is in high speed trail mode. Tipping the last toggle switch letting all air to the actuator will make the cutout valve open as soon as there is boost, this is the all out racing mode with no noise dampening going on, all exhaust is dumped straight down into the tunnel.
Pretty cool setup

I had a long day of work in the turbo garage tuesday afternoon, evening and night. Got a lot of work done.

Here I am publishing my work on TY, I'm uploading all my pics to www.photobucket.com and link them to my posts on TY. Saves space on the TY servers and helps reducing load on the same servers.

I lost 6 of 8 header bolts last season, I won't have that happen again. My friend Odd-Steffen had another aircraft way of making sure bolt stay put; He adviced me to use locking wire of mild steel to hold the bolt from unscrewing themselves. I had to drill 2mm holes in each bolt before installing the header.

Here's an example. I know it's all wrong, but it's only for reference LOL.

I cleaned up the exhaust outlets on the motor, tried to scrape off most of the carbon, added a solvent and wiped dry. Then I placed a new exhaust gasket in front of the exhaust outlets. It's impossible to get the gasket in place with the header put in place so the gasket had to go in first.

In put the header in place and moveded the gasket in position until I got the first bolt thru the header and gasket and into the threads, only tightened it down a tiny bit. Then I moved on with moving the gasket upwards until I was able to install the next bolt. With two bolt in place the rest of them went on quite easily.

I tightend down the bolts as tight as I could get them or as tight as I dared, whatever came first

I moved on to the turbo. I had both the rear bolt come loose last season, I won't have any of that happen again. It's impossible for me to install bolts from underneat as the header is not designed for it. Last year I cut a few 40mm bolt and threaded them in place from the upper side of the header flange, I installed a nut both at the turbo and under neat the header flange, well they unsrewed themselves and disappeared.
To keep this from happen again I decided it was better to use stock bolts threaded from above like the ones at the front of the turbo. On the rear right bolt hole I only had to file off a small amount to get the bolt in place. On the rear left hole there were no room on top to get a bolt thru so I had to cut away metal to the rear to be able to get the bolt in place. The rear left bolt has to be installed together with the 2 Norlocks before the turbo is installed. Here's a pic of the turbo after the preparation.

This is how it looks like with the bolts in place.

I tightened down the turbo and went on installing water lines to the turbo.
Last year I had the coolant line plugged into the carburetor heating circuitry. I have learnt that it's not sufficient flow to cool the turbo effectively. I have now plugged the turbo coolant lines into the oil cooler circuitry. Line goes from the oil cooler to the turbo and returns into the thermostat housing.



Before installing the oil feed line to the turbo I added some oil to the oil inlet at the turbo to make sure the turbine have oil when I start up the engine. Prior to oiling the turbo the turbine hardly spun at all after giving it a spin, it stopped rather quickly. After oiling the turbo the turbine spun for quite a while before it stopped. It does need oil or the bearings will seize on startup, it's important to oil the turbo before every season as it will dry out during summer storage.

Installing pressure lines to boost controller and meth injection fail safe solenoid.

With all water and oil lines connected to the turbo I started to add heat insulation to the lines.


I decided to add heat insulating wrapping to the downpipe as well since I had enough left from insulating the header.

I installed the downpipe and added some more wrapping to the downpipe, turbo and header.


I still have some more insulating to do before It's done, you may recognize the turbo blanket to the right in the pic, it's going to be wrapped around the turbine housing before the heat shields is installed.
Last thing I did was manufacturing a heat sink out of 14gz or 1.5mm aluminum sheet metal. I have a hard time getting hold of copper as the manual calls for so I chose to go with second best as aluminum is a good heat conductor. Now I pray it doesn't melt

My frind Odd-Steffen is modifying some stuff in the tunnel. He's working on the exhaust cutout and muffler that's going to be installed up front in the tunnel.

It's going to be a nice setup, allowing the sled to run in two different modes. When exhaust is routed thru the muffler it's in trail mode and when the it's in race mode all exhaust is dropped directly into the tunnel thru a straight pipe no muffler
Pretty cool setup


kinger
VIP Member
Looks good Jan-Ove! If the wire still fails, these are stage 8 locking fasterner, you coudl make them yourself, check out the web site on how they work.
http://www.stage8.com/
http://www.stage8.com/
Attachments
rxrider
Jan-Ove Pedersen
- Joined
- Apr 25, 2003
- Messages
- 7,355
- Age
- 60
- Location
- Lakselv - 70N & 25E
- Country
- Norway
- Snowmobile
- 2014 Phazer XTX, 2013 Phazer RTX, 2008 Apex RTX, 2007 Warrior, 2006 Attak
Thanks a lot buddy for the link, I'll save the link if I ever need those fasteners. Looks like a great product... I'll keep them in mind.
EDIT - Just finished reading the whole Stage8 web site, wow, they sure know how to lock thing down, especially I liked their Bizarre page... who would have tought of that... the LIAR was and eyeopener, not that I didn't know but tho
Thanks kinger for sharing the insight on locking fasternes with me.
EDIT - Just finished reading the whole Stage8 web site, wow, they sure know how to lock thing down, especially I liked their Bizarre page... who would have tought of that... the LIAR was and eyeopener, not that I didn't know but tho
Thanks kinger for sharing the insight on locking fasternes with me.

kinger
VIP Member
No problem my friend! If I had a turbo I would be using these, looks like it would save a ton of aggrevation!
rxrider
Jan-Ove Pedersen
- Joined
- Apr 25, 2003
- Messages
- 7,355
- Age
- 60
- Location
- Lakselv - 70N & 25E
- Country
- Norway
- Snowmobile
- 2014 Phazer XTX, 2013 Phazer RTX, 2008 Apex RTX, 2007 Warrior, 2006 Attak
Update December 10. - Connecting coolant hose from the turbo to the thermostat housing. Adding heat shilding material to lines, hoses and turbo. Installing O2 sensor. Installing turbo blanket.
This evening I started by installing the coolant hose coming from the turbo to the thermostat housing.
Next was shielding up all lines and hoses with heat shielding material to protect them against the heat produced by the engine.
Next I installed the O2 sensor to the downpipe. It's hidden and out of sight. I also used the last of the wrapping on the turbo to shield it completely before installing the turbo blanket.
The last thing I did was installing a turbo blanket, I wrapped it around the exhaust turbine housing. With all the wrapping and insulation I have added this time I will be very suprised if I have anything plastic melting this season. One can only hope
I'm done with heat shielding. Next work will be adding the aluminum heat shields and start installing charge tube and steering column, throttle cable and chocke cable. Connecting the electric is also close... So far so good.

This evening I started by installing the coolant hose coming from the turbo to the thermostat housing.

Next was shielding up all lines and hoses with heat shielding material to protect them against the heat produced by the engine.


Next I installed the O2 sensor to the downpipe. It's hidden and out of sight. I also used the last of the wrapping on the turbo to shield it completely before installing the turbo blanket.

The last thing I did was installing a turbo blanket, I wrapped it around the exhaust turbine housing. With all the wrapping and insulation I have added this time I will be very suprised if I have anything plastic melting this season. One can only hope



I'm done with heat shielding. Next work will be adding the aluminum heat shields and start installing charge tube and steering column, throttle cable and chocke cable. Connecting the electric is also close... So far so good.



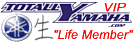

Dam Jan...Your project may Never End, sure a lot of work there plus taking the time to show the steps with pic's....GREAT JOB.
To bad I can't see the pic's from work.

To bad I can't see the pic's from work.
Similar threads
- Replies
- 46
- Views
- 150K
-
This site uses cookies to help personalise content, tailor your experience and to keep you logged in if you register.
By continuing to use this site, you are consenting to our use of cookies.