rxrider
Jan-Ove Pedersen
- Joined
- Apr 25, 2003
- Messages
- 7,355
- Age
- 60
- Location
- Lakselv - 70N & 25E
- Country
- Norway
- Snowmobile
- 2014 Phazer XTX, 2013 Phazer RTX, 2008 Apex RTX, 2007 Warrior, 2006 Attak
No I did not diamond hone the cylinders. I have changed rings on quite a few sled without doing this and never had a problems with ring seal so far.
If your engine uses oil the oil rings and oil division rings are installed incorrectly, that's the major reason for burning oil.
The only problem if the compression rings does not seal to a 100% is that you get more blow by. I have red articles written by engine builders on the topic of blow by. In a racing application you may want less than 5 % leak down, in a everyday street motor or our sleds for that matter he would not care much until blowby reaches 20%. The amount of horsepower lost is not significant enough for him to justify the cost of a total reduild once a year or even more often to keep the leak down below 5%.
In my book, as long as the compression is even across all cylinders I'm happy with it.

rxrider
Jan-O
If your engine uses oil the oil rings and oil division rings are installed incorrectly, that's the major reason for burning oil.
The only problem if the compression rings does not seal to a 100% is that you get more blow by. I have red articles written by engine builders on the topic of blow by. In a racing application you may want less than 5 % leak down, in a everyday street motor or our sleds for that matter he would not care much until blowby reaches 20%. The amount of horsepower lost is not significant enough for him to justify the cost of a total reduild once a year or even more often to keep the leak down below 5%.
In my book, as long as the compression is even across all cylinders I'm happy with it.
rxrider
Jan-O
rxrider
Jan-Ove Pedersen
- Joined
- Apr 25, 2003
- Messages
- 7,355
- Age
- 60
- Location
- Lakselv - 70N & 25E
- Country
- Norway
- Snowmobile
- 2014 Phazer XTX, 2013 Phazer RTX, 2008 Apex RTX, 2007 Warrior, 2006 Attak
SEASON 2013
Update - January 2 - Installing new headgasket and shim. Adjusting valve clearance. Apex MCX260.
This sled was hard to start when warm. And it had oil in the coolat. The owner wanted me to change the headgasket and shim as he suspected the head gasket to be blown out.
Teardown.
When removing the cylinder head I found one of the donuts broken.
I suggested doing a valve clearance check while the engine was apart. As many as 10 out of 20 valves had clearances below specification minimum, one intake valve had 0,079 millimeter clearance. This valve have definitively been leaking, and a lot with a hot engine. I changed out a valve shims and set them close to specification maximum.
The new head gasket/shim came in from MCX-press.
Assembling the sled.
The owner reported back with news that the sled was easy to start when warm and power was way better than ever
Mission completed
Update - January 23 - Installing Apex MCX290 Mid-Mount.
A lot of parts are on order.
Clutch kit -
Boost Meter - arrived.
Turbokit - arrived.
Sled - arrived.
Most of the work is covered in earlier projects an will not be repeated here.
I will focus on the parts of the job that is specific for the MCX290 Mid-Mount turbo kit.
I will also focus on the Gen 5 MCX EFI-Computer.
Later when clutch parts are in I will cover clutch setup.
I have a bit more tear down to do before the install starts, gotta go working.
Teardown continues....
The head is about to be removed. I took the time measuring the valve clearances ahead of removing the cam shafts to save me some work reinstalling the cams when the head is on the workbench.
The cylinder head is going out tonight. I'm adjusting the valve clearances to turbo specification before installing the new headshim
More to come.
Update - January 2 - Installing new headgasket and shim. Adjusting valve clearance. Apex MCX260.
This sled was hard to start when warm. And it had oil in the coolat. The owner wanted me to change the headgasket and shim as he suspected the head gasket to be blown out.
Teardown.

When removing the cylinder head I found one of the donuts broken.


I suggested doing a valve clearance check while the engine was apart. As many as 10 out of 20 valves had clearances below specification minimum, one intake valve had 0,079 millimeter clearance. This valve have definitively been leaking, and a lot with a hot engine. I changed out a valve shims and set them close to specification maximum.

The new head gasket/shim came in from MCX-press.

Assembling the sled.

The owner reported back with news that the sled was easy to start when warm and power was way better than ever
Mission completed
Update - January 23 - Installing Apex MCX290 Mid-Mount.
A lot of parts are on order.
Clutch kit -
Boost Meter - arrived.
Turbokit - arrived.
Sled - arrived.
Most of the work is covered in earlier projects an will not be repeated here.
I will focus on the parts of the job that is specific for the MCX290 Mid-Mount turbo kit.
I will also focus on the Gen 5 MCX EFI-Computer.
Later when clutch parts are in I will cover clutch setup.
I have a bit more tear down to do before the install starts, gotta go working.
Teardown continues....


The head is about to be removed. I took the time measuring the valve clearances ahead of removing the cam shafts to save me some work reinstalling the cams when the head is on the workbench.

The cylinder head is going out tonight. I'm adjusting the valve clearances to turbo specification before installing the new headshim
More to come.
judger101
Expert
i love all your pictures and explanations keep it up
rxrider
Jan-Ove Pedersen
- Joined
- Apr 25, 2003
- Messages
- 7,355
- Age
- 60
- Location
- Lakselv - 70N & 25E
- Country
- Norway
- Snowmobile
- 2014 Phazer XTX, 2013 Phazer RTX, 2008 Apex RTX, 2007 Warrior, 2006 Attak
Thanks judger101
It's exactly what this thread is all about.
If I can help a fellow sledder, or at least inspire others to do work on their own sleds I've accomplished something
It's all in the spirit of TY4stroke helping out others.
It's exactly what this thread is all about.
If I can help a fellow sledder, or at least inspire others to do work on their own sleds I've accomplished something
It's all in the spirit of TY4stroke helping out others.

kinger
VIP Member
YES he's back! Welcome back RXRIDER!!
Malibu
Expert
yukon yamaha
TY 4 Stroke Master
- Joined
- Jan 30, 2008
- Messages
- 1,092
- Age
- 39
- Location
- WHITEHORSE, YUKON CANADA
- Country
- Canada
- Snowmobile
- 2008 nytro custom! 2014 viper custom
X3 

rxrider
Jan-Ove Pedersen
- Joined
- Apr 25, 2003
- Messages
- 7,355
- Age
- 60
- Location
- Lakselv - 70N & 25E
- Country
- Norway
- Snowmobile
- 2014 Phazer XTX, 2013 Phazer RTX, 2008 Apex RTX, 2007 Warrior, 2006 Attak
Thank you guys for the warm welcome back.
Yeah it's been a while.
I have a few more projects pending.
I'n a few weeks I'm going to install a Nytro MPI180 SuperCharger kit.
Yeah it's been a while.
I have a few more projects pending.
I'n a few weeks I'm going to install a Nytro MPI180 SuperCharger kit.
rxrider
Jan-Ove Pedersen
- Joined
- Apr 25, 2003
- Messages
- 7,355
- Age
- 60
- Location
- Lakselv - 70N & 25E
- Country
- Norway
- Snowmobile
- 2014 Phazer XTX, 2013 Phazer RTX, 2008 Apex RTX, 2007 Warrior, 2006 Attak
Update - January 28 - Installing Apex MCX290 Mid-Mount - updated.
- Removing the cam caps, shafts, buckets and valve shims
- Cylinder head removal
- Cleaning the cylinder head and cylinders
- Installing head gasket/shim
- Adjusting valve clearances
Prior to removing the cylinder head I measured the valve shim clearances, removed the cam caps, camshafts, valve buckets and valve shims.
The cylinder head has been removed and placed on the workbench.
CAUTION:
If you ever work on the cylinder head with the camshafts off, not removing the buckets and shims, you have to take great care not tilting the cylinderhead too much on its side. The valve shims easily moves out of position may causing the engine to run pourly or in the worst case cause engine damage.
I recommend removing the shims and buckets when working on the cylinder head to avoid any problems with the valve shims. And it's much easier to work with the cylinderhead not having to worry about parts falling out of the cylinder head.
With all cams, buckets and valves off the cylinder head it was time to clean the surfaces.
I use a strong solvent to soften up the silicone residue from the old head gasket from the surfaces of the cylinder head and cylinders. I let the solvent work for a short time, then I wipe it off. The residue still sticking is removed using a Stanley Knife's razor sharp blade. I use the blade to scrape off the residue with the blade at a 90 degree angle to avoid cutting into the aluminum. The surface has been cleaned carefully prior to installing the headgasket/shim.
Luckily this head gasket design has been changed to all steel in the recent years like used in the new head shim that comes with the kit
Compression is lowered from 11.8:1 to around 9.4:1 with the new head gasket/shim
The new headgasket/shim installed to top of the cylinders.
Valve shim clearance adjustment.
I use an Excel Spreadsheet to calculate the valve thickness to install the get the desired valve clearances.
Added the initial measurements I made.
Add the current valve shim thickness.
Read out the suggested valve shim to install.
Intake
Exhaust
Yamaha valve feeler blades. Shows both inces and millimeters. My spreadsheet works with metric measurements.
Measuring the exhaust.... never mind the .002 .... it's there only to show how to measure
I usually have to repeat the measure and valve shim changing 3-4 times before I'm happy with it.
I have a vast number of different shims in stock to suppliment the ones from the engine in work.
Every time new shims are added I have to install the camshafts and caps and tork down the bolts to spec which is 10Nm.
Yamaha specifications are:
Intake: 0.11 - 0.20 millimeter
Exhaust: 0.21 - 0.26 millimeter
In a boosted motor I recommend adjusting valve clearances close to the upper limit of the specification.
Dot not exceed the specifications.
Finally, after a few hours work all final values added and new valve shims installed.
With the valve job done I installed the cylinder head and torked down the nuts to MCX specifications.
Use a tork wrench, tighten the bolts in sequence from the middle and out, starting in the center.
Use the Yamaha Service Manual as your referrence.
Tork down the head in 5 stages.
1. stage, loosely tighten all nuts to seat lightly
2. stage, 20Nm
3. stage, 35Nm
4. stage, 50Nm
5. stage, loosen the nuts one by one in the correct sequence a 1/4 turn and retork to 50Nm.
Next I will continue installing the cams and cylinder head cover.
- Removing the cam caps, shafts, buckets and valve shims
- Cylinder head removal
- Cleaning the cylinder head and cylinders
- Installing head gasket/shim
- Adjusting valve clearances
Prior to removing the cylinder head I measured the valve shim clearances, removed the cam caps, camshafts, valve buckets and valve shims.

The cylinder head has been removed and placed on the workbench.


CAUTION:
If you ever work on the cylinder head with the camshafts off, not removing the buckets and shims, you have to take great care not tilting the cylinderhead too much on its side. The valve shims easily moves out of position may causing the engine to run pourly or in the worst case cause engine damage.
I recommend removing the shims and buckets when working on the cylinder head to avoid any problems with the valve shims. And it's much easier to work with the cylinderhead not having to worry about parts falling out of the cylinder head.
With all cams, buckets and valves off the cylinder head it was time to clean the surfaces.
I use a strong solvent to soften up the silicone residue from the old head gasket from the surfaces of the cylinder head and cylinders. I let the solvent work for a short time, then I wipe it off. The residue still sticking is removed using a Stanley Knife's razor sharp blade. I use the blade to scrape off the residue with the blade at a 90 degree angle to avoid cutting into the aluminum. The surface has been cleaned carefully prior to installing the headgasket/shim.

Luckily this head gasket design has been changed to all steel in the recent years like used in the new head shim that comes with the kit

The new headgasket/shim installed to top of the cylinders.

Valve shim clearance adjustment.
I use an Excel Spreadsheet to calculate the valve thickness to install the get the desired valve clearances.
Added the initial measurements I made.
Add the current valve shim thickness.
Read out the suggested valve shim to install.
Intake

Exhaust

Yamaha valve feeler blades. Shows both inces and millimeters. My spreadsheet works with metric measurements.

Measuring the exhaust.... never mind the .002 .... it's there only to show how to measure

I usually have to repeat the measure and valve shim changing 3-4 times before I'm happy with it.
I have a vast number of different shims in stock to suppliment the ones from the engine in work.
Every time new shims are added I have to install the camshafts and caps and tork down the bolts to spec which is 10Nm.
Yamaha specifications are:
Intake: 0.11 - 0.20 millimeter
Exhaust: 0.21 - 0.26 millimeter
In a boosted motor I recommend adjusting valve clearances close to the upper limit of the specification.
Dot not exceed the specifications.
Finally, after a few hours work all final values added and new valve shims installed.

With the valve job done I installed the cylinder head and torked down the nuts to MCX specifications.
Use a tork wrench, tighten the bolts in sequence from the middle and out, starting in the center.
Use the Yamaha Service Manual as your referrence.
Tork down the head in 5 stages.
1. stage, loosely tighten all nuts to seat lightly
2. stage, 20Nm
3. stage, 35Nm
4. stage, 50Nm
5. stage, loosen the nuts one by one in the correct sequence a 1/4 turn and retork to 50Nm.

Next I will continue installing the cams and cylinder head cover.
rxrider
Jan-Ove Pedersen
- Joined
- Apr 25, 2003
- Messages
- 7,355
- Age
- 60
- Location
- Lakselv - 70N & 25E
- Country
- Norway
- Snowmobile
- 2014 Phazer XTX, 2013 Phazer RTX, 2008 Apex RTX, 2007 Warrior, 2006 Attak
Update - February 1 - Installing Apex MCX290 Mid-Mount - updated.
- Installing cam shafts.
- Adjusting spark plug gap.
- Installing adaptor for oil feed line to turbo.
- Installing cylinder head cover, plugs, coils and coolant pipes.
- Installing exhaust heat shield.
- Installing oil pump.
Before installing the cam shafts make sure to set the crankshaft #1 piston (the one close to the cam chain) at top dead center (TDC). This is done by rotating the crank shaft until the maker on the flywheel aligns with the arrow on the block. Be careful not the loose the cam chain off the sprocket down in the engine, it's a pain to get it back on if you do.
The marker to look for is the single one, not the ones with the arrow in between them.
In this pic it's hard to see the arrow inside the hole, but it's there. The crank is now in the correct position.
With the intake cam gear slotted to MCX specs it was time to install the cam shafts.
Make sure the cam chain tensioner is unhooked. This is done by a screwdriver, turn clockwise until it stops, now the cam chain tensioner is released. Don't be shy on assembly lube, my oil can is full of Yamalube 0-30, the same I use in the motor. Oil all bearing surfaces on the cylinder hear and the cam shafts well before installing the cams.
I always use a lot of oil when assembling an engine, this oil is all what the engine will get until the oil pums starts pumping.
Start by installing the exhaust cam. You have to, no way to get it in there if you install the intake cam first.
The exhaust cam has a dot that is supposed to align with the arrow on the cam cup closest to the cam chain side.
The intake cam has a dot that is supposed to align with the arrow on the cam cup closest to the magneto side.
Set the exhaust cam with the dot pointing straigt up. Rotate the cam carefully counterclockwise until the slack is taken out of the cam chain. If the dot is still pointing straight up, zip-tie the chain to the sprocket on the exhaust cam to prevent it from jumping.
Continue installing the intake cam. Position the cam with the dot pointing straight up, rotate the cam carefully counterclockwise to take up any slack in the cam chain. Make sure that the dot still points straight up. Zip-tie the chain to the intake cam gear to prevent it from jumping.
Add all cam caps. Tighten down the bolts a little of the time until all bolts seats lightly. This way the force added to the camshaft is evenly distributed over the cups preventing damage to the cams and the cups. Tork down the bolts to 10Nm with a tork wrench.
Release the cam chain tensioner.
Remove the zip-ties.
Rotate the engine slowly for a few revolutions to make sure it rotates freely.
If the engine won't turn easily; don't force it or you may destroy internal parts.
What can cause this? A valve shim out of place. The cams installed incorrectly and in the wrong position relative to the crank shaft.
OK with the engine rotates freely. Set the crank back on the ignition marker on the flywheel.
The dots on the cams should be approx. on the markers. On sleds running a head shim or thicker than stock head gasket, the dots will not aligh perfectly.
The dot on the intake cam will be slightly (only a fraction) to the front of the marker.
The dot on the exhaust cam will be slightly to the rear of the marker.
Done deal
the cams are in perfect alignment relative to the crank shaft.
Sorry about the blurry picture.
On a turbo sled I like to reduce spark plug gap down to 0.018 inch or 0.45 millimeter.
When compression pressure increases the spark is actually blowing out.
Decreasing the spark plug gap increases the intensity of the spark keeping the spark from blowing out
I have a nice tool that makes it very easy to adjust spark plug gaps.
I continued installing an adaptor for the oil feed line going to the turbo.
Remove the connector to the oil pressure sensor.
Remove the oil pressure sensor from the engine block.
Install the adaptor contained with the MCX turbo kit, add loctite to the threads before installing it into the block.
Install the oil feed line going to the turbo.
Install the oil pressure sensor.
Install the connector to the oil pressure sensor.
Tighten down the bolt holding everything in place.
Done.
Time to finish the engine job by installing the cylinder head cover.
Clean all surfaces.
Install the cylinder head cover.
Make sure the rubber gasket seals perfectly. If not glue it to the cylinder head cover before installing it. Use a based glue like Yamabond or similar.
OK all is well with the gasket, tighten down the 6 bolts to spec.
Install the spark plugs. Tork to spec, 15Nm, the book says 13Nm but I feel that is way loose.
Install the coils and bolt them tight.
Install the coolant pipes and hoses, make sure the pipe ends and the O-rings are clean, add a few drops of oil to the O-rings, it makes them enter more easily.
Add the two bolts and tighten them to spec.
The charge tube precooler under the left side of the tunnel enters thru a hole drilled in the frame to the left of the exhaust headers. On the teardown I removed the left tunnel protector to make room for the precooler.
The heat shield underneat the headers don't have to be cut, only slightly bent to make room for the precooler. The heat shield above the headers will have to be cut to make room for the precooler.
The heat shields bent, cut and installed.
The deltabox frame and handlebars are back on.
Installing the front rubber mounting points for the MCX Intercooler.
Unscrew the two Philips screws holding the plastic pads in place.
Replace the Philips scews with the MCX rubber mounts, use loctite on the threads to keep them from coming out.
Oil pump install.
Ran into a problem. It seems like the hole in head of the flywheel bolt coming with the kit is slightly off center.
The oil pump shaft is supposed to enter this hole, the pump shaft is driven by the crank shaft thru a cross pin that fits the cross groove in the bolt. Sorry but so, the oil pump shaft binds when installing the pump, the more I tighthen down the pump the worse it gets. I will have to get a new bolt from MCX or have a machine shop fix the off center hole in the bolt head.... I hope, don't wanna wait a week to get stuff shipped all the way from Sweden.
Next time.... fixing the flywheel bolt head, and the oil pump install continues.
- Installing cam shafts.
- Adjusting spark plug gap.
- Installing adaptor for oil feed line to turbo.
- Installing cylinder head cover, plugs, coils and coolant pipes.
- Installing exhaust heat shield.
- Installing oil pump.
Before installing the cam shafts make sure to set the crankshaft #1 piston (the one close to the cam chain) at top dead center (TDC). This is done by rotating the crank shaft until the maker on the flywheel aligns with the arrow on the block. Be careful not the loose the cam chain off the sprocket down in the engine, it's a pain to get it back on if you do.
The marker to look for is the single one, not the ones with the arrow in between them.
In this pic it's hard to see the arrow inside the hole, but it's there. The crank is now in the correct position.

With the intake cam gear slotted to MCX specs it was time to install the cam shafts.
Make sure the cam chain tensioner is unhooked. This is done by a screwdriver, turn clockwise until it stops, now the cam chain tensioner is released. Don't be shy on assembly lube, my oil can is full of Yamalube 0-30, the same I use in the motor. Oil all bearing surfaces on the cylinder hear and the cam shafts well before installing the cams.
I always use a lot of oil when assembling an engine, this oil is all what the engine will get until the oil pums starts pumping.
Start by installing the exhaust cam. You have to, no way to get it in there if you install the intake cam first.
The exhaust cam has a dot that is supposed to align with the arrow on the cam cup closest to the cam chain side.
The intake cam has a dot that is supposed to align with the arrow on the cam cup closest to the magneto side.
Set the exhaust cam with the dot pointing straigt up. Rotate the cam carefully counterclockwise until the slack is taken out of the cam chain. If the dot is still pointing straight up, zip-tie the chain to the sprocket on the exhaust cam to prevent it from jumping.
Continue installing the intake cam. Position the cam with the dot pointing straight up, rotate the cam carefully counterclockwise to take up any slack in the cam chain. Make sure that the dot still points straight up. Zip-tie the chain to the intake cam gear to prevent it from jumping.
Add all cam caps. Tighten down the bolts a little of the time until all bolts seats lightly. This way the force added to the camshaft is evenly distributed over the cups preventing damage to the cams and the cups. Tork down the bolts to 10Nm with a tork wrench.
Release the cam chain tensioner.
Remove the zip-ties.
Rotate the engine slowly for a few revolutions to make sure it rotates freely.
If the engine won't turn easily; don't force it or you may destroy internal parts.
What can cause this? A valve shim out of place. The cams installed incorrectly and in the wrong position relative to the crank shaft.
OK with the engine rotates freely. Set the crank back on the ignition marker on the flywheel.
The dots on the cams should be approx. on the markers. On sleds running a head shim or thicker than stock head gasket, the dots will not aligh perfectly.
The dot on the intake cam will be slightly (only a fraction) to the front of the marker.
The dot on the exhaust cam will be slightly to the rear of the marker.
Done deal

Sorry about the blurry picture.
On a turbo sled I like to reduce spark plug gap down to 0.018 inch or 0.45 millimeter.
When compression pressure increases the spark is actually blowing out.
Decreasing the spark plug gap increases the intensity of the spark keeping the spark from blowing out
I have a nice tool that makes it very easy to adjust spark plug gaps.

I continued installing an adaptor for the oil feed line going to the turbo.
Remove the connector to the oil pressure sensor.
Remove the oil pressure sensor from the engine block.
Install the adaptor contained with the MCX turbo kit, add loctite to the threads before installing it into the block.
Install the oil feed line going to the turbo.
Install the oil pressure sensor.
Install the connector to the oil pressure sensor.
Tighten down the bolt holding everything in place.
Done.

Time to finish the engine job by installing the cylinder head cover.
Clean all surfaces.
Install the cylinder head cover.
Make sure the rubber gasket seals perfectly. If not glue it to the cylinder head cover before installing it. Use a based glue like Yamabond or similar.
OK all is well with the gasket, tighten down the 6 bolts to spec.
Install the spark plugs. Tork to spec, 15Nm, the book says 13Nm but I feel that is way loose.
Install the coils and bolt them tight.
Install the coolant pipes and hoses, make sure the pipe ends and the O-rings are clean, add a few drops of oil to the O-rings, it makes them enter more easily.
Add the two bolts and tighten them to spec.

The charge tube precooler under the left side of the tunnel enters thru a hole drilled in the frame to the left of the exhaust headers. On the teardown I removed the left tunnel protector to make room for the precooler.
The heat shield underneat the headers don't have to be cut, only slightly bent to make room for the precooler. The heat shield above the headers will have to be cut to make room for the precooler.

The heat shields bent, cut and installed.

The deltabox frame and handlebars are back on.

Installing the front rubber mounting points for the MCX Intercooler.
Unscrew the two Philips screws holding the plastic pads in place.
Replace the Philips scews with the MCX rubber mounts, use loctite on the threads to keep them from coming out.

Oil pump install.
Ran into a problem. It seems like the hole in head of the flywheel bolt coming with the kit is slightly off center.
The oil pump shaft is supposed to enter this hole, the pump shaft is driven by the crank shaft thru a cross pin that fits the cross groove in the bolt. Sorry but so, the oil pump shaft binds when installing the pump, the more I tighthen down the pump the worse it gets. I will have to get a new bolt from MCX or have a machine shop fix the off center hole in the bolt head.... I hope, don't wanna wait a week to get stuff shipped all the way from Sweden.

Next time.... fixing the flywheel bolt head, and the oil pump install continues.
rxrider
Jan-Ove Pedersen
- Joined
- Apr 25, 2003
- Messages
- 7,355
- Age
- 60
- Location
- Lakselv - 70N & 25E
- Country
- Norway
- Snowmobile
- 2014 Phazer XTX, 2013 Phazer RTX, 2008 Apex RTX, 2007 Warrior, 2006 Attak
Update - February 1 - Installing Apex MCX290 Mid-Mount - updated.
- Cutting the frame to make room for the mid-mount turbo.
- Installing the precooler charge tube.
- Installing aluminum plate to cover up the hole where the stock exhaust muffler use to be.
Flywheel bolt is at the machine shop.... waiting for it to arrive.
The frame has to be cut open rear of the fuel tank to make room for the mid-mount turbo.
The kit comes with two templates that mounts on the fuel tank rear bolts and the exhaust from bolt holes.
The templates makes it very easy to mark up where to make the cut.
The right hand side template.
The left hand side template.
I've modified the templates slightly to make the marking job a bit easier.
The cut has been done.
Went on installing the precooler charge tube. I've already drilled a 60 millimeter hole to left of the exhaust inside the tunnel. Before installing the Precooler you have to remove a few rives an replace then with flat head bolts.
Two holes were drilled on top of the tunnel for the bolts that mounts the precooler to the frame.
With the precooler in place I've torked down the two bolts. The charge tube fits nicely
With the charge tube in place I installed the plate covering up the hole where the stock exhaust muffler used to sit.
I removed the two rear rivets from the exhaust cover mount, marked up the 6 holes to be drilled.
The plate is riveted to the frame, use four M8 bolts and washers and tighten down the plate.
I also installed the hose between the precooler charge tube and IC to the precooler.
- Cutting the frame to make room for the mid-mount turbo.
- Installing the precooler charge tube.
- Installing aluminum plate to cover up the hole where the stock exhaust muffler use to be.
Flywheel bolt is at the machine shop.... waiting for it to arrive.
The frame has to be cut open rear of the fuel tank to make room for the mid-mount turbo.
The kit comes with two templates that mounts on the fuel tank rear bolts and the exhaust from bolt holes.
The templates makes it very easy to mark up where to make the cut.
The right hand side template.

The left hand side template.

I've modified the templates slightly to make the marking job a bit easier.
The cut has been done.

Went on installing the precooler charge tube. I've already drilled a 60 millimeter hole to left of the exhaust inside the tunnel. Before installing the Precooler you have to remove a few rives an replace then with flat head bolts.
Two holes were drilled on top of the tunnel for the bolts that mounts the precooler to the frame.

With the precooler in place I've torked down the two bolts. The charge tube fits nicely

With the charge tube in place I installed the plate covering up the hole where the stock exhaust muffler used to sit.

I removed the two rear rivets from the exhaust cover mount, marked up the 6 holes to be drilled.
The plate is riveted to the frame, use four M8 bolts and washers and tighten down the plate.

I also installed the hose between the precooler charge tube and IC to the precooler.
rxrider
Jan-Ove Pedersen
- Joined
- Apr 25, 2003
- Messages
- 7,355
- Age
- 60
- Location
- Lakselv - 70N & 25E
- Country
- Norway
- Snowmobile
- 2014 Phazer XTX, 2013 Phazer RTX, 2008 Apex RTX, 2007 Warrior, 2006 Attak
Update - February 4 - Installing Apex MCX290 Mid-Mount - updated.
- Installing silicone hose from Precooler to Intercooler.
- Installing MCX oil return pump.
- Installing Battery bracket, battery and the stock ECU.
- Installing crank vent hose.
- Modifying throttle spring tension.
- Installing throttle bodies.
- Installing oil tank.
- Strapping up air intake temp sensor.
With the precooler in place I installed the silicone charge tube to the precooler.
The fly wheel bolt came in from the machine shop
They put the bolt in a lathe and enlarged the centre hole slightly to make it perfectly round.
Installed the bolt and tightened it to 120Nm.
The pump shaft and cross pin installed with ease.
I added engine oil to the O-rings prior to the install.
I installed the battery bracket, the stock ECU, the battery.
Next I connected all the electrical connectors, relays and fuses.
I installed a bracket to clamp down the IC. Installed it on the upper bolt on the starter motor.
Removed this hose from inside the stock air box, installed it to the crank breather vent, hooked the other end with the two small holes up front to the rubber band that used to hold down the stock air box.
To prevent the throttles to blow open when you let off throttle modify one of the two springs on the throttle shaft.
This is typical for the MCX turbo kits and the higher the boost level the worse it gets. The feel you get when letting off throttle is like you have not fully let off.... scary when going into a tight turn.
To remedy this situation I wind up the right hand spring a half turn.
First you have to bend the hook at the end of the spring 90 degrees to the right, then use a steel wire to pull the spring a half turn and hook it on the bracket where the philips screw sits.
Installed the throttle bodies, tightened down the clamps, hooked up coolant lines, hooked up all electrical connectors. Installed throttle wire. Make sure you have the trottlebodies pressed fully on, use your body weight and lean forward when pushing to make sure the throttlebodies will seat fully.
Add spacers to move the oil tank away from the MCX oil return pump.
Installed the oil tank, hooked up the oil hoses, and installed the oil drain plug.
Installed the coolant hose down in front of the oil tank.
Next I strapped down the air intake temp sensor, that used to sit inside the stock air box, to the harness.
Next is installing the MCX EFI computer and wireing.
- Installing silicone hose from Precooler to Intercooler.
- Installing MCX oil return pump.
- Installing Battery bracket, battery and the stock ECU.
- Installing crank vent hose.
- Modifying throttle spring tension.
- Installing throttle bodies.
- Installing oil tank.
- Strapping up air intake temp sensor.
With the precooler in place I installed the silicone charge tube to the precooler.

The fly wheel bolt came in from the machine shop
They put the bolt in a lathe and enlarged the centre hole slightly to make it perfectly round.
Installed the bolt and tightened it to 120Nm.
The pump shaft and cross pin installed with ease.
I added engine oil to the O-rings prior to the install.

I installed the battery bracket, the stock ECU, the battery.
Next I connected all the electrical connectors, relays and fuses.
I installed a bracket to clamp down the IC. Installed it on the upper bolt on the starter motor.


Removed this hose from inside the stock air box, installed it to the crank breather vent, hooked the other end with the two small holes up front to the rubber band that used to hold down the stock air box.

To prevent the throttles to blow open when you let off throttle modify one of the two springs on the throttle shaft.
This is typical for the MCX turbo kits and the higher the boost level the worse it gets. The feel you get when letting off throttle is like you have not fully let off.... scary when going into a tight turn.
To remedy this situation I wind up the right hand spring a half turn.
First you have to bend the hook at the end of the spring 90 degrees to the right, then use a steel wire to pull the spring a half turn and hook it on the bracket where the philips screw sits.

Installed the throttle bodies, tightened down the clamps, hooked up coolant lines, hooked up all electrical connectors. Installed throttle wire. Make sure you have the trottlebodies pressed fully on, use your body weight and lean forward when pushing to make sure the throttlebodies will seat fully.

Add spacers to move the oil tank away from the MCX oil return pump.
Installed the oil tank, hooked up the oil hoses, and installed the oil drain plug.
Installed the coolant hose down in front of the oil tank.


Next I strapped down the air intake temp sensor, that used to sit inside the stock air box, to the harness.

Next is installing the MCX EFI computer and wireing.
rxrider
Jan-Ove Pedersen
- Joined
- Apr 25, 2003
- Messages
- 7,355
- Age
- 60
- Location
- Lakselv - 70N & 25E
- Country
- Norway
- Snowmobile
- 2014 Phazer XTX, 2013 Phazer RTX, 2008 Apex RTX, 2007 Warrior, 2006 Attak
Update - February 5 - Installing Apex MCX290 Mid-Mount - updated.
- Installing MCX EFI Computer.
- Connecting the EFI wireing to the stock harness.
- Connecting pressure/vacuum lines.
- Installing silicone boots and hose clamps.
- Installing IC.
- Connecting EFI signal wire to injectors on the IC.
- Installing BOV and vacuum line.
This evening I started installing the MCX EFI computer and wireing.
The EFI computer is installed on the Deltabox frame just in front of the steering column.
I drilled out two holes in the deltabox frame and installed M6 thread inserts.
I found some spacers to keep the EFI box off the steering post. Sadly the spacers did not come with the kit, and the install manual did not contain any information on how to install the EFI box. Not that I care, but it would be nice for a guy doing his first install.
There are two wires from the EFI box that has to be soldered to the stock wire harness.
The wire are soldered to the stock wireing.
The Orange wire goes to the Orange-Black wire in the stock harness at this connector to the left of the throttlebodies close to the primary clutch.
The Red wire (power supply) goes to the Red-White wire down at the starter relay.
A few pressure vacuum lines comes with the kit.
One is connected to the sensor on the throttlebodies, remove the stock line from the throttlebodies and add the MCX line. The other end goes to the MCX EFI box's internal MAP sensor. I always Zip-Tie all lines ends to keep them from blowing off.
The second line connects to the outer front nipples on both sides fo the throttlebodies, the line connects to the Blow-off-valve BOV on the IC.
Installed the silicone boots for the IC.
Connected and installed the wire harness at the left hand side.
Two of the three connectors coming from the MCX EFI box.
The black connector is for the optional MCX Display Unit.
The grey connector goes back to the Electronic Boost Controller close to the turbo.
The IC is installed, the last connector from the MCX EFI box are hooked up with the injectors inside the IC.
Fuel line to the IC injectors are routed and ready to connect to the external inline fuel pumpl.
The silicone boots have been tightened down with hose clamps. The two hoses in the rear left of the IC have been connected the throttlebodies idle air controller IAC. The two rubber mounts and the bracket installed earlier have been connected to the IC.
Installed BOV to the IC and hooked up the vacuum line.
The work done so far.
Next work will be installling exhaust and turbo.

- Installing MCX EFI Computer.
- Connecting the EFI wireing to the stock harness.
- Connecting pressure/vacuum lines.
- Installing silicone boots and hose clamps.
- Installing IC.
- Connecting EFI signal wire to injectors on the IC.
- Installing BOV and vacuum line.
This evening I started installing the MCX EFI computer and wireing.
The EFI computer is installed on the Deltabox frame just in front of the steering column.
I drilled out two holes in the deltabox frame and installed M6 thread inserts.
I found some spacers to keep the EFI box off the steering post. Sadly the spacers did not come with the kit, and the install manual did not contain any information on how to install the EFI box. Not that I care, but it would be nice for a guy doing his first install.


There are two wires from the EFI box that has to be soldered to the stock wire harness.
The wire are soldered to the stock wireing.
The Orange wire goes to the Orange-Black wire in the stock harness at this connector to the left of the throttlebodies close to the primary clutch.

The Red wire (power supply) goes to the Red-White wire down at the starter relay.

A few pressure vacuum lines comes with the kit.
One is connected to the sensor on the throttlebodies, remove the stock line from the throttlebodies and add the MCX line. The other end goes to the MCX EFI box's internal MAP sensor. I always Zip-Tie all lines ends to keep them from blowing off.

The second line connects to the outer front nipples on both sides fo the throttlebodies, the line connects to the Blow-off-valve BOV on the IC.

Installed the silicone boots for the IC.

Connected and installed the wire harness at the left hand side.

Two of the three connectors coming from the MCX EFI box.
The black connector is for the optional MCX Display Unit.
The grey connector goes back to the Electronic Boost Controller close to the turbo.

The IC is installed, the last connector from the MCX EFI box are hooked up with the injectors inside the IC.

Fuel line to the IC injectors are routed and ready to connect to the external inline fuel pumpl.
The silicone boots have been tightened down with hose clamps. The two hoses in the rear left of the IC have been connected the throttlebodies idle air controller IAC. The two rubber mounts and the bracket installed earlier have been connected to the IC.

Installed BOV to the IC and hooked up the vacuum line.

The work done so far.

Next work will be installling exhaust and turbo.

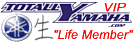

Welcome Back Homes..
...GEEEEEZ Almost 300,000 Views on your ride.....Good thing your back buddy those number will climb now
...GEEEEEZ Almost 300,000 Views on your ride.....Good thing your back buddy those number will climb now

Similar threads
- Replies
- 46
- Views
- 149K
-
This site uses cookies to help personalise content, tailor your experience and to keep you logged in if you register.
By continuing to use this site, you are consenting to our use of cookies.