rxrider
Jan-Ove Pedersen
- Joined
- Apr 25, 2003
- Messages
- 7,355
- Age
- 60
- Location
- Lakselv - 70N & 25E
- Country
- Norway
- Snowmobile
- 2014 Phazer XTX, 2013 Phazer RTX, 2008 Apex RTX, 2007 Warrior, 2006 Attak
There are collars with oil rings on the inside, on both the driveshaft and jackshaft. There are also oil seals behind both the upper and lower chaincase bearings. The upper collar and oil ring didn't come off the jackshaft, that's why it was not a part of my install writeup. The lower collar and oil ring was installed as a part of the track and driveshaft install.
Both collars installed on the jackshaft and driveshaft are shown in this pic.
Both collars installed on the jackshaft and driveshaft are shown in this pic.
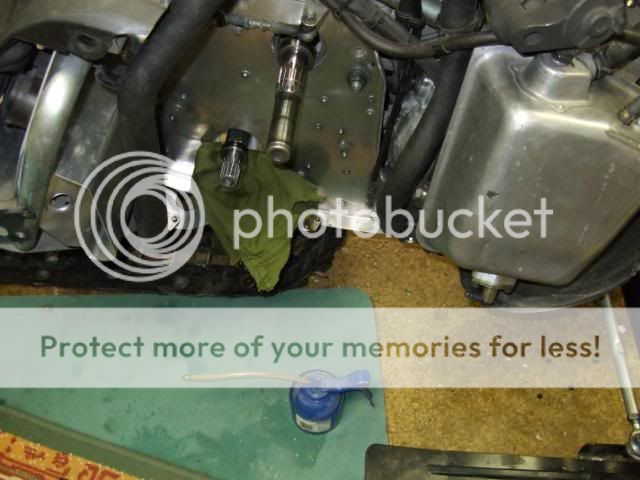
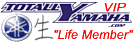

1CrazySledder
Lifetime Member
- Joined
- Aug 11, 2005
- Messages
- 2,006
- Location
- Cartersville, GA.
- Country
- USA
- Snowmobile
- None, looking now!
Ya know. This was the second thing I missed yesterday. Glad I got off line and went to bed. lol
Blind as a bat, I guess. lol Sorry 'bout that.
This is a great job. Much better than the book.
1CS
Blind as a bat, I guess. lol Sorry 'bout that.
This is a great job. Much better than the book.
1CS
After using "ketchup" in your chaincase - atleast your bolts, chain and gears won't rust anymore- LOL
This is my fav. thread at the moment. I can't wait to hear the report on your new skid frame with boost.
I will put my motor together this weekend - my boost project finally back on track. I got the parts I have been waiting for.
Yamaha gave them to me under warrenty after 5 years (2003 rx-1) That is what I call service - and a company that stands behind their product!!!!!!!!!!! Hands down for my local Yamaha dealer!. I would like to see that happend with an other brand.
This is my fav. thread at the moment. I can't wait to hear the report on your new skid frame with boost.
I will put my motor together this weekend - my boost project finally back on track. I got the parts I have been waiting for.
Yamaha gave them to me under warrenty after 5 years (2003 rx-1) That is what I call service - and a company that stands behind their product!!!!!!!!!!! Hands down for my local Yamaha dealer!. I would like to see that happend with an other brand.
rxrider
Jan-Ove Pedersen
- Joined
- Apr 25, 2003
- Messages
- 7,355
- Age
- 60
- Location
- Lakselv - 70N & 25E
- Country
- Norway
- Snowmobile
- 2014 Phazer XTX, 2013 Phazer RTX, 2008 Apex RTX, 2007 Warrior, 2006 Attak
1CrazySledder - Glad to help. Most writeups are done at night after garage time, man I have been tired at times doing the writeups. I had to check up on what you asked for cause I couldn't remember what I'd wrote a few days back. Anyway thanks for asking, I could have forgotten things while writing nearly asleep LOL. Time for the write up, writing ZZZzzzZZZZ uhhhh write some moooorrreeeee zzZZZZzzz ooooopsss 3:00 am - time for bed.
rxrider
Jan-Ove Pedersen
- Joined
- Apr 25, 2003
- Messages
- 7,355
- Age
- 60
- Location
- Lakselv - 70N & 25E
- Country
- Norway
- Snowmobile
- 2014 Phazer XTX, 2013 Phazer RTX, 2008 Apex RTX, 2007 Warrior, 2006 Attak
TT said:After using "ketchup" in your chaincase - atleast your bolts, chain and gears won't rust anymore- LOL
This is my fav. thread at the moment. I can't wait to hear the report on your new skid frame with boost.
I will put my motor together this weekend - my boost project finally back on track. I got the parts I have been waiting for.
Yamaha gave them to me under warrenty after 5 years (2003 rx-1) That is what I call service - and a company that stands behind their product!!!!!!!!!!! Hands down for my local Yamaha dealer!. I would like to see that happend with an other brand.
Ketchup works wonders on them gears LOL

Glad to hear you are getting it together

Yes I know - hands down for my dealer as well, Yamaha really stands behind their products. I got the mountain float bowls and all 4 coils covered under warranty last season, for my '03 RX-1 shorty.
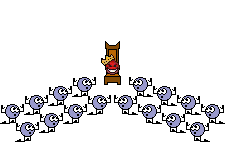
I don't think we will see that kind of support and service from the other makes after the 1 or 2 or whatever their warranty period is. Word most likely would be, to my experience from owning other brands, the problem is fixed on the latest model year sleds, you could buy one at a discount, are you happy now?
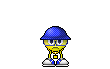
I'll take the quality of build, reliability and milage of a 4stroke Yamaha before anything out there.
rxrider
Jan-Ove Pedersen
- Joined
- Apr 25, 2003
- Messages
- 7,355
- Age
- 60
- Location
- Lakselv - 70N & 25E
- Country
- Norway
- Snowmobile
- 2014 Phazer XTX, 2013 Phazer RTX, 2008 Apex RTX, 2007 Warrior, 2006 Attak
UPDATE - December 7. - Installing the carb rack, intercooler and piping.
Clean the outside of the carbs, the part going into the carb boots. Hook up the carb heater coolant hose on the engine side of the carb rack. Align the carbs onto the carb boots and evenly press the carb rack against the carb boot mouths, it helps rug the carbs up and down while pressing the onto the carb boots. If you cannot push the carbs onto the boots, I recommend lubing the inside of the rubber carb boot mouths by spitting on it and apply it to the inside of the carb boots. It will apply enough lube to ease the install, and when it dries out it will make the carb boots stick to the carbs. Low tech but it works.
When the carbs are installed on the carb boots, tighten down the clamps that holds the carbs onto the carb boots.
Install the electrical carb heating wireing found on the lower left side of the carb rack seen from the front of the sled. Install the TORS (Throttle OverRide System) wireing found on the upper left side of the rack. Install the TPS (Throttle Position Sensor) found just above the carb boots on the engine side of the carb rack.
Install the fuel lines from the carbs to the fuel pumps. In my sled the fuel lines connects to the fuel pressure regulator.
For the MCX-press turbo guys, here's how my crank vent hose is positioned to avoid any oil damp from blowing onto the clutches.
Because of the high pressure fuel delivery on my turbo sled I need hose clamps on all connections. Fuel pressure at full boost is 4-5 lbs over max boost level, running 16 lbs it adds up to a max fuel pressure of 20+ lbs going to the carbs.
Hooking up the pressure signal hose going between the fuel pressure regulator and intercooler.
Now it's time to hook up the throttle cable to the carb throttle lever. To make the install of the throttle wire end to the carb throttle lever, lift the throttle to WOT with a screwdriver and place another large screwdriver underneat the carb throttle lever to keep it at WOT (Wide Open Throttle) or close like shown in this pic.
Hook up the throttle wire end ball to the throttle lever eye, make sure the throttle wire lays inside the groove in the carb throttle lever. Lift the threaded cable end up and tread the wire into the throttle cable adjuster and thread the cable completely down into the adjuster. When done it's time to adjust the throttle cable free play. I run the throttle cable as loose as possible, my TORS has never kicked in ever. I adjust by looking at the gap between the handle bar and throttle lever at WOT. At WOT the throttle lever shall barely touch the handle bar, 1/16" or 1.5 millimeter gap is fine.
Chocke cable install. Install the chocke cable ball end into the carb chocke lever. Loosen the chocke cable holder enough to slid the chocke cable into it. Place the chocke cable into the holder. Tighten down the screw holding the chocke cable in place. Done.
That's all for now, still have some piping to finish up under the hood. Will finish off rest of the carb, IC and piping install writeup when done. I will also do a carb sync any day soon.
Piping and plumbing are done.
Intercooler install. I cleaned the intercooler well. I started the install by inserting the intake air tract into the charge tube rubber hose. Then I aligned the IC to the silicone rubber connections and pressed the IC into place, and finally I tied the IC down in the front.
Next was connecting the pressure signal hose for the carb slides.
Then I hooked up the lines that pressurizes the float bowls.
Connected the pressure signal going to the fuel pressure regulator.
Installed the hose clamps.
Tightened down the IC and float bowl hose clamps.
Tightened down the charge tube hose clamp.
Installed a carb coolant on/off switch to the frame.
Connected a coolant hose from the engine to the on/off switch and from the switch to the carbs. Piping is done.

Clean the outside of the carbs, the part going into the carb boots. Hook up the carb heater coolant hose on the engine side of the carb rack. Align the carbs onto the carb boots and evenly press the carb rack against the carb boot mouths, it helps rug the carbs up and down while pressing the onto the carb boots. If you cannot push the carbs onto the boots, I recommend lubing the inside of the rubber carb boot mouths by spitting on it and apply it to the inside of the carb boots. It will apply enough lube to ease the install, and when it dries out it will make the carb boots stick to the carbs. Low tech but it works.
When the carbs are installed on the carb boots, tighten down the clamps that holds the carbs onto the carb boots.
Install the electrical carb heating wireing found on the lower left side of the carb rack seen from the front of the sled. Install the TORS (Throttle OverRide System) wireing found on the upper left side of the rack. Install the TPS (Throttle Position Sensor) found just above the carb boots on the engine side of the carb rack.

Install the fuel lines from the carbs to the fuel pumps. In my sled the fuel lines connects to the fuel pressure regulator.

For the MCX-press turbo guys, here's how my crank vent hose is positioned to avoid any oil damp from blowing onto the clutches.

Because of the high pressure fuel delivery on my turbo sled I need hose clamps on all connections. Fuel pressure at full boost is 4-5 lbs over max boost level, running 16 lbs it adds up to a max fuel pressure of 20+ lbs going to the carbs.

Hooking up the pressure signal hose going between the fuel pressure regulator and intercooler.

Now it's time to hook up the throttle cable to the carb throttle lever. To make the install of the throttle wire end to the carb throttle lever, lift the throttle to WOT with a screwdriver and place another large screwdriver underneat the carb throttle lever to keep it at WOT (Wide Open Throttle) or close like shown in this pic.

Hook up the throttle wire end ball to the throttle lever eye, make sure the throttle wire lays inside the groove in the carb throttle lever. Lift the threaded cable end up and tread the wire into the throttle cable adjuster and thread the cable completely down into the adjuster. When done it's time to adjust the throttle cable free play. I run the throttle cable as loose as possible, my TORS has never kicked in ever. I adjust by looking at the gap between the handle bar and throttle lever at WOT. At WOT the throttle lever shall barely touch the handle bar, 1/16" or 1.5 millimeter gap is fine.

Chocke cable install. Install the chocke cable ball end into the carb chocke lever. Loosen the chocke cable holder enough to slid the chocke cable into it. Place the chocke cable into the holder. Tighten down the screw holding the chocke cable in place. Done.

That's all for now, still have some piping to finish up under the hood. Will finish off rest of the carb, IC and piping install writeup when done. I will also do a carb sync any day soon.
Piping and plumbing are done.
Intercooler install. I cleaned the intercooler well. I started the install by inserting the intake air tract into the charge tube rubber hose. Then I aligned the IC to the silicone rubber connections and pressed the IC into place, and finally I tied the IC down in the front.

Next was connecting the pressure signal hose for the carb slides.

Then I hooked up the lines that pressurizes the float bowls.

Connected the pressure signal going to the fuel pressure regulator.

Installed the hose clamps.

Tightened down the IC and float bowl hose clamps.

Tightened down the charge tube hose clamp.

Installed a carb coolant on/off switch to the frame.

Connected a coolant hose from the engine to the on/off switch and from the switch to the carbs. Piping is done.


rxrider
Jan-Ove Pedersen
- Joined
- Apr 25, 2003
- Messages
- 7,355
- Age
- 60
- Location
- Lakselv - 70N & 25E
- Country
- Norway
- Snowmobile
- 2014 Phazer XTX, 2013 Phazer RTX, 2008 Apex RTX, 2007 Warrior, 2006 Attak
UPDATE - December 7. - Replacing the left hand side jackshaft bearing.
Start removing the secondary clutch and all washers from the jackshaft. With a circlip tool, remove the circlip holding the bearing in place.
It would be nice having the special Yamaha tool for removing and installing the locking collar from the bearing and jackshaft.
I didn't have it when I did the removal, but I managed to remove it anyway, here's how I did it. With a small punch tool and a hammer tap on the inner ring of the bearing, do not use a lot of force or you may damage the frame of your sled. Tap it at one side of the time like shown in the pics. The reaction force of the tapping will eventually make the collar pop out
Enough to get a grip on it and remove it from the jackshaft.
Now it is time to remove the bearing from the frame.
To remove the bearing from the frame you have to partly disassemble the chaincase. This procedure will be covered when it is done.
CORRECTION - you do not have to touch the chaincase at all to remove the left hand side jackshaft bearing. You only need a mechanic friend to invent the tools needed. Thank you Mikkel for fabricating the tools needed and for helping me with the removal and install of that bearing. THANK YOU my friend.
What can I say... it saved me a lot of work and grief. Here are the tools we used to replace the jackshaft bearing.
This funny tool made it possible for us to remove the bearing from the frame. In fact, when we had all the right tools at hand, the procedure of replaceing the bearing took no more than 15 minutes.
With the locking collar and circlip removed we inserted the tool my friend fabricated in between the inner ring of the bearing and the jackshaft.
It's some sort of a hammer, the heavy steel cylinder on the shaft creates the pulling force when slamming it away from the jackshaft. We did not have to add much force to move the bearing when we figured how to apply the tools to the task at hand.
To make it work we had to add a thin steel plate underneat the tool to stop it from slipping the bearing. When we had figured out the procedure I heated the frame with a heat gun. Mikkel applied the tools and the bearing popped out right away.
Prior to the bearing install I had placed the bearing outside in the cold. Reason I did this was to contract the bearing, diameter shrinks when steel is cooled down. While the frame was still hot we installed the freezing cold bearing into the frame, we had to tap it gently around on the outer race to make it seat properly into the frame.
We added the locking collar.
We added the locking collar install tool.
We punched the collar into place by tapping gently on the end of the install tool.
Circlip installed.
Bearing install finished.
Secondary clutch install. Time to install the secondary clutch on the spline. First install the washers.
Place the secondary onto the spline. Add the bolt and washers. Tighten the bolt to spec.
Adjust the offset, insert or subtract washers on the inside and outside as needed. Offset should be 15 millimeter +/- 1.5 millimeter, freeplay about 2-3 millimeter.
Install a good belt and check belt deflection. A good belt should ride flush with or 0.5 millimeter over the top of the sheaves. Adjust by adding/subtracting washers from the 3 adjustment screws behind the secondary. You have to remove the secondary to get to them. Installing thicker washers will make the belt ride higher, subtracting washers will make the belt ride lower in the secondary.
Install the clutch shield, and add good belt as a spare.
Install the side covers.
Done

Start removing the secondary clutch and all washers from the jackshaft. With a circlip tool, remove the circlip holding the bearing in place.


It would be nice having the special Yamaha tool for removing and installing the locking collar from the bearing and jackshaft.
I didn't have it when I did the removal, but I managed to remove it anyway, here's how I did it. With a small punch tool and a hammer tap on the inner ring of the bearing, do not use a lot of force or you may damage the frame of your sled. Tap it at one side of the time like shown in the pics. The reaction force of the tapping will eventually make the collar pop out


Enough to get a grip on it and remove it from the jackshaft.


Now it is time to remove the bearing from the frame.

To remove the bearing from the frame you have to partly disassemble the chaincase. This procedure will be covered when it is done.
CORRECTION - you do not have to touch the chaincase at all to remove the left hand side jackshaft bearing. You only need a mechanic friend to invent the tools needed. Thank you Mikkel for fabricating the tools needed and for helping me with the removal and install of that bearing. THANK YOU my friend.


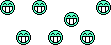




What can I say... it saved me a lot of work and grief. Here are the tools we used to replace the jackshaft bearing.

This funny tool made it possible for us to remove the bearing from the frame. In fact, when we had all the right tools at hand, the procedure of replaceing the bearing took no more than 15 minutes.

With the locking collar and circlip removed we inserted the tool my friend fabricated in between the inner ring of the bearing and the jackshaft.

It's some sort of a hammer, the heavy steel cylinder on the shaft creates the pulling force when slamming it away from the jackshaft. We did not have to add much force to move the bearing when we figured how to apply the tools to the task at hand.

To make it work we had to add a thin steel plate underneat the tool to stop it from slipping the bearing. When we had figured out the procedure I heated the frame with a heat gun. Mikkel applied the tools and the bearing popped out right away.


Prior to the bearing install I had placed the bearing outside in the cold. Reason I did this was to contract the bearing, diameter shrinks when steel is cooled down. While the frame was still hot we installed the freezing cold bearing into the frame, we had to tap it gently around on the outer race to make it seat properly into the frame.

We added the locking collar.

We added the locking collar install tool.


We punched the collar into place by tapping gently on the end of the install tool.

Circlip installed.

Bearing install finished.

Secondary clutch install. Time to install the secondary clutch on the spline. First install the washers.

Place the secondary onto the spline. Add the bolt and washers. Tighten the bolt to spec.

Adjust the offset, insert or subtract washers on the inside and outside as needed. Offset should be 15 millimeter +/- 1.5 millimeter, freeplay about 2-3 millimeter.

Install a good belt and check belt deflection. A good belt should ride flush with or 0.5 millimeter over the top of the sheaves. Adjust by adding/subtracting washers from the 3 adjustment screws behind the secondary. You have to remove the secondary to get to them. Installing thicker washers will make the belt ride higher, subtracting washers will make the belt ride lower in the secondary.

Install the clutch shield, and add good belt as a spare.

Install the side covers.


Done


rxrider
Jan-Ove Pedersen
- Joined
- Apr 25, 2003
- Messages
- 7,355
- Age
- 60
- Location
- Lakselv - 70N & 25E
- Country
- Norway
- Snowmobile
- 2014 Phazer XTX, 2013 Phazer RTX, 2008 Apex RTX, 2007 Warrior, 2006 Attak
UPDATE - December 8. - Installling the plastic covers.
Finished off the exterior of the sled, the side panels and installed the front cone cover.
She's almost done.
I was not able to finish it off before this weekend, still have some more work left:
- Install snow flap
- Add coolant
- Do a WBO2 sensor free air calibration
- Fill up with fresh gas
- Start the engine
- Check for engine oil circulation
- Add more engine oil, adjust to the F mark on the dipstick.
- Adjust track tension
- Take her out for a TESTRIDE
Finished off the exterior of the sled, the side panels and installed the front cone cover.

She's almost done.

I was not able to finish it off before this weekend, still have some more work left:
- Install snow flap
- Add coolant
- Do a WBO2 sensor free air calibration
- Fill up with fresh gas
- Start the engine
- Check for engine oil circulation
- Add more engine oil, adjust to the F mark on the dipstick.
- Adjust track tension
- Take her out for a TESTRIDE
sleddheadd
TY 4 Stroke God
doing a great job here rxrider!!!!! this is an awesome post!!!
rxrider
Jan-Ove Pedersen
- Joined
- Apr 25, 2003
- Messages
- 7,355
- Age
- 60
- Location
- Lakselv - 70N & 25E
- Country
- Norway
- Snowmobile
- 2014 Phazer XTX, 2013 Phazer RTX, 2008 Apex RTX, 2007 Warrior, 2006 Attak
Thank you sleddheadd, yes I'm putting some effort into it. I have to say I got inspired by lakercr's engine build post.

kinger
VIP Member
Looks great, I am putting the similar effort into mine right now, I should be riding in about a week. Thanks again for the pictures, the Chain case and ZX2 went right in for me!
rxrider
Jan-Ove Pedersen
- Joined
- Apr 25, 2003
- Messages
- 7,355
- Age
- 60
- Location
- Lakselv - 70N & 25E
- Country
- Norway
- Snowmobile
- 2014 Phazer XTX, 2013 Phazer RTX, 2008 Apex RTX, 2007 Warrior, 2006 Attak
UPDATE - December 9. - WBO2 free air calibration.
Today I did the free air calibration of the AFR-sensor on my Innovate LC-1 WBO2 system.
Turn on the ignition. When the XD-16 gauge light up press the command button 3 times rapidly, then press the button once more right away to enter the free air calibration mode. After pressing the command button 3 times rapidly the XD-16 gauge flashes CAL for 5 seconds and then return to normal operation if command button is not pressed once more within the 5 seconds.
When calibration is done the gauge will return to normal operation. Since there is no exhaust gas present the gauge will display: o2 and 20.9 - in a flashing pattern shifting between o2 and 20.9, this indicates that the sensor reads free air only. My gauge was showing 20.8 at times with the sensor still inside the exhaust. I figured since I haven't run my engine since May there would not be any exhaust left to screw up the calibration.
Done
Installed the snowflap, riveted into place.
Today I did the free air calibration of the AFR-sensor on my Innovate LC-1 WBO2 system.

Turn on the ignition. When the XD-16 gauge light up press the command button 3 times rapidly, then press the button once more right away to enter the free air calibration mode. After pressing the command button 3 times rapidly the XD-16 gauge flashes CAL for 5 seconds and then return to normal operation if command button is not pressed once more within the 5 seconds.

When calibration is done the gauge will return to normal operation. Since there is no exhaust gas present the gauge will display: o2 and 20.9 - in a flashing pattern shifting between o2 and 20.9, this indicates that the sensor reads free air only. My gauge was showing 20.8 at times with the sensor still inside the exhaust. I figured since I haven't run my engine since May there would not be any exhaust left to screw up the calibration.


Done

Installed the snowflap, riveted into place.


rxrider
Jan-Ove Pedersen
- Joined
- Apr 25, 2003
- Messages
- 7,355
- Age
- 60
- Location
- Lakselv - 70N & 25E
- Country
- Norway
- Snowmobile
- 2014 Phazer XTX, 2013 Phazer RTX, 2008 Apex RTX, 2007 Warrior, 2006 Attak
UPDATE - December 10. - Adjusting oil and coolant level.
Time to fill up the coolant into the system and pray that my left cooler is not leaking too bad. If it does I would put in some coolant leak stopper stuff in, like radiator repair or similar product.
WARNING - do not pour a large amount of cold coolant into a hot engine.
Prior to adding coolant I opened the rear exchanger bleeding bolt. With a cold engine, I opened the filler cap and poured coolant until it came out the bleeder hole in the rear. I installed the bleeder bolt and continued the refill. I poured 2.5 litres or 2/3 gallon of coolant into the system, that was all she took before the can was full.
I use Esso/Exxon premixed coolant good down to -36 C or -33 F.
I already had 2.5 litres or 2/3 gallons of oil in the engine. Next was fireing up the machine to circulate the oil. I let it idle for about 15-20 seconds and shut it off. Filled up another litre or quarter of oil into the oil tank and fired the engine again to check for circulation by looking into the oil tank with the engine running.
Oil was circulating.
I inserted the dipstick and filled it up with more oil. Then I ran the engine for a minute, shut it down and checked the oil once more. I topped it up to the F mark and ran the engine for 15-20 seconds. Then I checked for oil leaks, no leaks were spotted. I checked the oil level once more, it was still at the F mark. I ddded the dipstick and oil sensor connector to the dipstick, done with it.
Now it was time to re-check the coolant level, and as I assumed the coolant level had dropped out of the can. I filled up with more coolant until the can was completely full.
Then I opened the bleeder bolt in the rear cooler and looked for air bubbles, none where spotted. I shut it off after a few seconds and checked the can, the level had sunk so I refilled the can.
Ran the engine a few more minutes and refilled every time the coolant level sank in the can. Then I topped off the can, installed the coolant cap and hoisted the sleds rear end up 3-4 ft and opened the rear heat exchanger bleeder screw to check for air, no air bubbles spotted. With the sled on the floor I once more filled up the can to the cold level mark and ran the machine with the cap open. Finally I shut it down and installed the cap again, then I checked the rear cooler one more time for air bubbles, none spotted. Finally I checked for coolant leaks, a small leak spotted where the welder predicted it would leak. No big leak, easy to fix with radiator repair or similar product. Remember to re-check the coolant level when engine is cold, coolant level will drop as the engine cools down. I did re-check the coolant the day after, it had dropped a few inches so I refilled it to the cold level line. Done.
Last thing to look after was the hot engine idle AFR reading.
Idle speed: 1500 rpms
HPG vacuum: 5
AFR Idle, warm engine: 12.4 - IS THIS TOO LOW? Any comments are appreciated.
Inside temp in garage: +12 C or 53 F
I found the 1500 rpms idle speed a little high so I adjusted the idle down some.
Idle speed: 1350 rpms
HPG vacuum: 5-6
AFR idle, warm engine: 12.3 - IS THIS TOO LOW? Any comments are appreciated.
Inside temp in garage: +12 C or 53 F
Throttle response is way better than last season, when I ran 17.5 pilots (22.5 now). Back then my hot engine idle AFR showed 14.7-16.2 with idle speed at 1500 rpms, I had to blip the throttle a few times to wake up the low end response. Now throttle response feels very crisp even inside my garage.
My dashboard.
I support TY.
Yes I got a turbo
She's finally ready for a test ride.
I still have to sync my carbs. Will do after my first short testride, I'll wait until I know that all is well before syncronizing the carbs. If I have to tear apart the carbs and piping the sync work have been a waste of time, cause you have to sync them again if the carb rack have been off. If you're looking for perfection that is.
Update: My welder was right on his assumption that it would still leak. The left cooler did barely leak, I have to add some stuff into the coolant to seal off the small leak.
And of course I need new fresh premium gas, thanks yamaslob for the reminder
I have to add fresh premium gasoline (93 Octane - US / 98 Octane - Europe) before running it on boost.
She's almost done and READY TO TESTRIDE - yeeeeehaaaaaa
Time to fill up the coolant into the system and pray that my left cooler is not leaking too bad. If it does I would put in some coolant leak stopper stuff in, like radiator repair or similar product.
WARNING - do not pour a large amount of cold coolant into a hot engine.
Prior to adding coolant I opened the rear exchanger bleeding bolt. With a cold engine, I opened the filler cap and poured coolant until it came out the bleeder hole in the rear. I installed the bleeder bolt and continued the refill. I poured 2.5 litres or 2/3 gallon of coolant into the system, that was all she took before the can was full.


I use Esso/Exxon premixed coolant good down to -36 C or -33 F.

I already had 2.5 litres or 2/3 gallons of oil in the engine. Next was fireing up the machine to circulate the oil. I let it idle for about 15-20 seconds and shut it off. Filled up another litre or quarter of oil into the oil tank and fired the engine again to check for circulation by looking into the oil tank with the engine running.


Oil was circulating.

I inserted the dipstick and filled it up with more oil. Then I ran the engine for a minute, shut it down and checked the oil once more. I topped it up to the F mark and ran the engine for 15-20 seconds. Then I checked for oil leaks, no leaks were spotted. I checked the oil level once more, it was still at the F mark. I ddded the dipstick and oil sensor connector to the dipstick, done with it.




Now it was time to re-check the coolant level, and as I assumed the coolant level had dropped out of the can. I filled up with more coolant until the can was completely full.

Then I opened the bleeder bolt in the rear cooler and looked for air bubbles, none where spotted. I shut it off after a few seconds and checked the can, the level had sunk so I refilled the can.


Ran the engine a few more minutes and refilled every time the coolant level sank in the can. Then I topped off the can, installed the coolant cap and hoisted the sleds rear end up 3-4 ft and opened the rear heat exchanger bleeder screw to check for air, no air bubbles spotted. With the sled on the floor I once more filled up the can to the cold level mark and ran the machine with the cap open. Finally I shut it down and installed the cap again, then I checked the rear cooler one more time for air bubbles, none spotted. Finally I checked for coolant leaks, a small leak spotted where the welder predicted it would leak. No big leak, easy to fix with radiator repair or similar product. Remember to re-check the coolant level when engine is cold, coolant level will drop as the engine cools down. I did re-check the coolant the day after, it had dropped a few inches so I refilled it to the cold level line. Done.



Last thing to look after was the hot engine idle AFR reading.
Idle speed: 1500 rpms
HPG vacuum: 5
AFR Idle, warm engine: 12.4 - IS THIS TOO LOW? Any comments are appreciated.
Inside temp in garage: +12 C or 53 F

I found the 1500 rpms idle speed a little high so I adjusted the idle down some.
Idle speed: 1350 rpms
HPG vacuum: 5-6
AFR idle, warm engine: 12.3 - IS THIS TOO LOW? Any comments are appreciated.
Inside temp in garage: +12 C or 53 F

Throttle response is way better than last season, when I ran 17.5 pilots (22.5 now). Back then my hot engine idle AFR showed 14.7-16.2 with idle speed at 1500 rpms, I had to blip the throttle a few times to wake up the low end response. Now throttle response feels very crisp even inside my garage.
My dashboard.

I support TY.

Yes I got a turbo

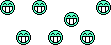

She's finally ready for a test ride.

I still have to sync my carbs. Will do after my first short testride, I'll wait until I know that all is well before syncronizing the carbs. If I have to tear apart the carbs and piping the sync work have been a waste of time, cause you have to sync them again if the carb rack have been off. If you're looking for perfection that is.
Update: My welder was right on his assumption that it would still leak. The left cooler did barely leak, I have to add some stuff into the coolant to seal off the small leak.
And of course I need new fresh premium gas, thanks yamaslob for the reminder

She's almost done and READY TO TESTRIDE - yeeeeehaaaaaa
yamaslob
TY 4 Stroke Guru
One thing I noticed and you should take into consideration is
you need gas
nice ride enjoy!
you need gas
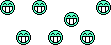
rxrider
Jan-Ove Pedersen
- Joined
- Apr 25, 2003
- Messages
- 7,355
- Age
- 60
- Location
- Lakselv - 70N & 25E
- Country
- Norway
- Snowmobile
- 2014 Phazer XTX, 2013 Phazer RTX, 2008 Apex RTX, 2007 Warrior, 2006 Attak
yamaslob said:One thing I noticed and you should take into consideration is
you need gasnice ride enjoy!
WOW - I completely forgot about that. In fact I did empty it as much as I could sunday morning with a siphoon and poured the old gas into the '05 RX-1 ER.
I'll update my last post, I have to add fresh premium gasoline (93 Octane - US / 98 Octane - Europe) before running it on boost.
yamaslob - Thanks for the reminder LOL
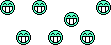


Similar threads
- Replies
- 46
- Views
- 149K
-
This site uses cookies to help personalise content, tailor your experience and to keep you logged in if you register.
By continuing to use this site, you are consenting to our use of cookies.