
kinger
VIP Member
- Joined
- Jan 17, 2005
- Messages
- 7,403
- Reaction score
- 1,539
- Points
- 1,963
- Location
- Clear Lake, IA
- Website
- www.piergenius.com
What are you doing for body panels this time? You are right on the skid options. Luckily I bought a spare ZX2 as that is my favorite but will likely mod that with as many light weight parts as I can to try to get to 40 lbs. I have enough parts for that skid to last the life of it now. I am just not interested in a M20 yet. I still like the skid to be performance oriented with skis in the air LOL
Nikolai
TY 4 Stroke God
Body work will either be carbon fiber or kydex. Likely carbon fiber and only 2 halves that overlap in the center. I know the body work on my last sled was weird looking so I will try hard this time to make it look good.

kinger
VIP Member
- Joined
- Jan 17, 2005
- Messages
- 7,403
- Reaction score
- 1,539
- Points
- 1,963
- Location
- Clear Lake, IA
- Website
- www.piergenius.com
I will be following your process. I am trying to stick with factory panels on my twincharged apex but I would love to be able to customize the look of the sled someday. I want 1 of 1 looks.
Nikolai
TY 4 Stroke God
I’ll probably stick with CF due to the strength to weight ratio. When I built my last CF bodywork both panels together were right around 6 lbs iirc, it was light and they were overbuilt. I think I can do all the bodywork for less than 5 lbs. I’ve also thought about the fabric(Mylar I think) that they use on Supercub wings. It’s super light and strong but would need a structure to attach to.
Nikolai
TY 4 Stroke God
I tried to set the 5/16 rivets a few weeks ago by myself and there was no way. I knew they would be difficult but it was clear right away it was going to be a 2 person job. My Dad came over yesterday and gave me a hand.
20 grams for 4 aluminum rivets, way lighter than bolts.
My old Nytro rotor with the cooling fin removed and aluminum rivets.
20 grams for 4 aluminum rivets, way lighter than bolts.
My old Nytro rotor with the cooling fin removed and aluminum rivets.
HighSpeedLowDrag
Pro
Look into a covering called Orotex. It's paintable but doesn't require any coatings. The other type is dacron polyester which is shrunk on with a calibrated iron and needs coatings to protect it from sunlight.I’ll probably stick with CF due to the strength to weight ratio. When I built my last CF bodywork both panels together were right around 6 lbs iirc, it was light and they were overbuilt. I think I can do all the bodywork for less than 5 lbs. I’ve also thought about the fabric(Mylar I think) that they use on Supercub wings. It’s super light and strong but would need a structure to attach to.
Nikolai
TY 4 Stroke God
Thanks, I will look into those!
Edit: Reading the Oratex website it sounds like great stuff. That over an ultra lite aluminum frame might make for lighter body work than CF.
Edit: Reading the Oratex website it sounds like great stuff. That over an ultra lite aluminum frame might make for lighter body work than CF.
Last edited:
Nikolai
TY 4 Stroke God
Here’s what I thought would be a good idea that turned into an epic fail.
I wanted to eliminate the outside bogie wheels up front just because I don’t like the looks and also to save a little weight. The BDX 2-wheel kit uses 2.75” diameter wheels with 6202 bearings which only have a 15mm ID and are tiny. I have had bad luck with BDX products in the past and don’t like the idea of using only a 15mm diameter cross shaft. The Ice Age rails also use a thicker hifax so the wheels really need to be about 2.90” to put a little pressure on the track.
So I thought I would get clever and make my own kit. I purchased 3.25” all plastic wheels from Wahl Brothers racing with 6205 bearings in them. I swapped the 6205 bearings for 6304 bearings which have a 20mm ID. The factory shaft is 22.5mm. So now I would only be turning down the shaft 2.5mm.
Got the shaft turned down on the ends.
Then got the wheels turned down to 2.90”. The problem is the wheel becomes to wide to fit inside the track nubs so I narrowed the wheel until it just got inside the nubs with some play.
Problem is by the time they are turned down there’s not much meat left for the snap ring, I wouldn’t trust it to hold very long.
I don’t know what I’m going to do now. I’ve got a shaft that’s turned down and 1 useless wheel. Probably just order a new cross shaft and run without wheels.
Definitely a couple wasted nights figuring this out the hard way.
I wanted to eliminate the outside bogie wheels up front just because I don’t like the looks and also to save a little weight. The BDX 2-wheel kit uses 2.75” diameter wheels with 6202 bearings which only have a 15mm ID and are tiny. I have had bad luck with BDX products in the past and don’t like the idea of using only a 15mm diameter cross shaft. The Ice Age rails also use a thicker hifax so the wheels really need to be about 2.90” to put a little pressure on the track.
So I thought I would get clever and make my own kit. I purchased 3.25” all plastic wheels from Wahl Brothers racing with 6205 bearings in them. I swapped the 6205 bearings for 6304 bearings which have a 20mm ID. The factory shaft is 22.5mm. So now I would only be turning down the shaft 2.5mm.
Got the shaft turned down on the ends.
Then got the wheels turned down to 2.90”. The problem is the wheel becomes to wide to fit inside the track nubs so I narrowed the wheel until it just got inside the nubs with some play.
Problem is by the time they are turned down there’s not much meat left for the snap ring, I wouldn’t trust it to hold very long.
I don’t know what I’m going to do now. I’ve got a shaft that’s turned down and 1 useless wheel. Probably just order a new cross shaft and run without wheels.
Definitely a couple wasted nights figuring this out the hard way.
Last edited:

kinger
VIP Member
- Joined
- Jan 17, 2005
- Messages
- 7,403
- Reaction score
- 1,539
- Points
- 1,963
- Location
- Clear Lake, IA
- Website
- www.piergenius.com
Ugh I just did something similar, wasted so much time and I hate wasting time. Will you just go back to outside wheels then?
Nikolai
TY 4 Stroke God
I don’t know yet. The ideal bearing for this application would be a 6004 (20x42x12). Lighter and narrower than the 6304 but still significantly larger than the 6202. If I had a larger lathe I would make my own wheels out of 3” UHMW but I don’t. Polaris uses the 6004 but their wheels are 3.25”.
Probably just ignore it for now and work on other stuff. Started working on the jig to build my upper a-arms so I can get them fabricated.
Probably just ignore it for now and work on other stuff. Started working on the jig to build my upper a-arms so I can get them fabricated.
fgauvin7
Newbie
- Joined
- Nov 16, 2016
- Messages
- 4
- Reaction score
- 1
- Points
- 203
- Location
- Québec
- Country
- Canada
- Snowmobile
- Arctic cat M8000 2019
YZ250 Snowbike
Hi, I have been following for a long time but never got to posting...
For the idlers on my snowbike project I used some of the standard (around 5in) boggie wheel with a 6004 inside and cut the excess on the band saw then finished them on the lathe.... I guess this technique could work for your small lathe. Usually I turn an arbor the same size as the OD of the bearing and just press the wheel on the arbor.
On my project I could have built the wheels from scratch (14in lathe) but theses standard boggy wheel cost almost less than the piece of UHMW to make them
Keep on the good work! it is very inspiring
For the idlers on my snowbike project I used some of the standard (around 5in) boggie wheel with a 6004 inside and cut the excess on the band saw then finished them on the lathe.... I guess this technique could work for your small lathe. Usually I turn an arbor the same size as the OD of the bearing and just press the wheel on the arbor.
On my project I could have built the wheels from scratch (14in lathe) but theses standard boggy wheel cost almost less than the piece of UHMW to make them
Keep on the good work! it is very inspiring

74Nitro
VIP Member
- Joined
- Feb 18, 2013
- Messages
- 5,483
- Reaction score
- 4,156
- Points
- 1,853
- Location
- Dublin Ontario
- Country
- Canada
- Snowmobile
- 2019 Sidewinder LTX
Would the Yamaha 3.35 idler with 6004 work?

74Nitro
VIP Member
- Joined
- Feb 18, 2013
- Messages
- 5,483
- Reaction score
- 4,156
- Points
- 1,853
- Location
- Dublin Ontario
- Country
- Canada
- Snowmobile
- 2019 Sidewinder LTX
Would the Yamaha 3.35 idler with 6004 work?

2000 Yamaha SRX700 (SRX700D) Track Suspension 1
Shop online for OEM Track Suspension 1 parts that fit your 2000 Yamaha SRX700 (SRX700D), search all our OEM Parts or call at 269-385-1540
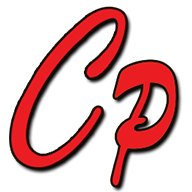

74Nitro
VIP Member
- Joined
- Feb 18, 2013
- Messages
- 5,483
- Reaction score
- 4,156
- Points
- 1,853
- Location
- Dublin Ontario
- Country
- Canada
- Snowmobile
- 2019 Sidewinder LTX
#35![]()
2000 Yamaha SRX700 (SRX700D) Track Suspension 1
Shop online for OEM Track Suspension 1 parts that fit your 2000 Yamaha SRX700 (SRX700D), search all our OEM Parts or call at 269-385-1540www.cyclepartsnation.com
Nikolai
TY 4 Stroke God
Just has to have enough meat on it to be able to turn it down.
Similar threads
- Replies
- 623
- Views
- 203K
- Replies
- 29
- Views
- 6K
- Replies
- 466
- Views
- 114K
-
This site uses cookies to help personalise content, tailor your experience and to keep you logged in if you register.
By continuing to use this site, you are consenting to our use of cookies.