ryama
Expert
- Joined
- Mar 3, 2009
- Messages
- 209
- Location
- Kitchener Ontario
- Country
- Canada
- Snowmobile
- Sidewinder R-TX
- LOCATION
- Kitchener
It's funny how sometime you go down a road only to vere off on another path. I know you will figure this out, and I will be buying whatever you come up with. Keep plugging Travis , you have alot of support in your corner .

ROCKERDAN
OCD Sledhead
- Joined
- Oct 8, 2005
- Messages
- 7,496
- Location
- Huntsville Ontario & Niagara NY
- Country
- Other
- Snowmobile
- '18 RTX 50th "Winder"
Very interesting work here. I know when I loctited my bearing down, some extra got around the rotor base and locked it down, and so I had a bad pulsing in brake lever initially. It eventually went away as the rotor loosened up after some miles. Great to see you found this. Definitely need the rotor to be floating, I believe it would be same on a DOO as the tunnel just is not stiff enough, and shafts are not perfectly true ect.Was having a few issues getting the assembly to seat consistently and figured out a simple solution to it. This morning I installed it on a running viper to test it on the stand for pulsations in lever. While I only ran it up to 75-80 mph on the stand I had no pulsations in the lever. Upon this stand test I discovered a more alarming concern. The entire caliper/bearing assembly and tunnel would wiggle back and forth. Locking the rotor down is exposing run out in the drive shaft. As soon as I would unlock the rotor the wiggle went away. Over time I can see this fatiguing the tunnel, so unfortunately locking the rotor down is not something I want to promote.
Don't worry......my quest for a solution is still very much alive. My fit ups and experimenting exposed yet another solution. When I was seating the wedge assembly inside drive shafts on the work bench I discovered that brake rotor wiggle disappeared once the wedge was expanded inside the drove shaft. So I slid the wedge assembly back farther in the shaft where the bearing rides and locked it down. The wedge expands the shaft enough to create an interference fit for the bearing! With wedge loose the bearing just falls off the shaft, but when wedge is tight I have to use some force to pull it off.
My goal is to get wedge to seat tight enough that I can't even pull the bearing off by hand. Right now the class 8 bolts shear off before I can get expand it enough. Tried a higher class bolt and it ripped threads out of wedge. Some new wedge designs are in the works for expansion across the full circumference and a larger bolt. This concept could function as a bolt in solution to preserve a drive shaft or repair worn drive shaft![]()
I'm liking the idea of shaft expanding to get the bearing to tightly fit and not slip. I would not have thought this would work, so im guessing the shaft must be a fairly soft steel?
Keep up the great work brother.
Dan
Fast
TY 4 Stroke Guru
- Joined
- Sep 25, 2018
- Messages
- 995
- Age
- 57
- Location
- Ontario
- Country
- Canada
- Snowmobile
- 2019 srx,2006 apex gt,96 storm hot to go
Have you had a chance to check your drive bearing with the green lock tight? wondering if it's still locked or did it break free when the rotor did?Very interesting work here. I know when I loctited my bearing down, some extra got around the rotor base and locked it down, and so I had a bad pulsing in brake lever initially. It eventually went away as the rotor loosened up after some miles. Great to see you found this. Definitely need the rotor to be floating, I believe it would be same on a DOO as the tunnel just is not stiff enough, and shafts are not perfectly true ect.
I'm liking the idea of shaft expanding to get the bearing to tightly fit and not slip. I would not have thought this would work, so im guessing the shaft must be a fairly soft steel?
Keep up the great work brother.
Dan
Sevey
TY 4 Stroke God
- Joined
- Feb 15, 2011
- Messages
- 1,758
- Location
- Collingwood, ON
- Website
- www.ty4stroke.com
- Country
- Canada
- Snowmobile
- 2018 Sidewinder RTX
Thought I would share this-
I had the caliper/bearing assembly off to repack the bearing and check if it was spinning. All was good so I reinstalled it with bearing mount Loctite. During reassembly I squared the bearing on the shaft and pushed inward until resistance against the inner snap ring. And fastened the three bolts.
Fast forward 1 month when I got around to changing oils and was running the engine. The drive shaft was not running true and cause the tunnel to flex and heave as the track rotated. The rotor was also rotating wonky as well.
Clearly on reassembly something was a miss, now it has to come off. The only thing I can think of; is the shaft may not operate perfectly true in the bearing and by me having locked it in place is causing that issue.
I would recommend anyone doing this, to run the sled after it is put together so the shaft can find where it wants to before the Loctite sets. Any other input would be helpful.
MS
I had the caliper/bearing assembly off to repack the bearing and check if it was spinning. All was good so I reinstalled it with bearing mount Loctite. During reassembly I squared the bearing on the shaft and pushed inward until resistance against the inner snap ring. And fastened the three bolts.
Fast forward 1 month when I got around to changing oils and was running the engine. The drive shaft was not running true and cause the tunnel to flex and heave as the track rotated. The rotor was also rotating wonky as well.
Clearly on reassembly something was a miss, now it has to come off. The only thing I can think of; is the shaft may not operate perfectly true in the bearing and by me having locked it in place is causing that issue.
I would recommend anyone doing this, to run the sled after it is put together so the shaft can find where it wants to before the Loctite sets. Any other input would be helpful.
MS
Fast
TY 4 Stroke Guru
- Joined
- Sep 25, 2018
- Messages
- 995
- Age
- 57
- Location
- Ontario
- Country
- Canada
- Snowmobile
- 2019 srx,2006 apex gt,96 storm hot to go
Maybe Rocker Dan will pipe up,he's done this past winterThought I would share this-
I had the caliper/bearing assembly off to repack the bearing and check if it was spinning. All was good so I reinstalled it with bearing mount Loctite. During reassembly I squared the bearing on the shaft and pushed inward until resistance against the inner snap ring. And fastened the three bolts.
Fast forward 1 month when I got around to changing oils and was running the engine. The drive shaft was not running true and cause the tunnel to flex and heave as the track rotated. The rotor was also rotating wonky as well.
Clearly on reassembly something was a miss, now it has to come off. The only thing I can think of; is the shaft may not operate perfectly true in the bearing and by me having locked it in place is causing that issue.
I would recommend anyone doing this, to run the sled after it is put together so the shaft can find where it wants to before the Loctite sets. Any other input would be helpful.
MS
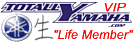

Weld and resizing or finding a good shaft that is right size and hardness is best solution in my opinion. Good ones are out there but only real way of knowing is to check after use. Peening still lets it move but has to be redone every season minimum.
yamaha06
TY 4 Stroke Guru
I have removed this bearing every year for re-greasing, peened the shaft before re-installing and have not had any issues with bearing spinning on the shaft so far, knock on wood. Have about 10,000km on the sled now.
NYTurbo
TY 4 Stroke God
Yeah me too, seems to be working.I have removed this bearing every year for re-greasing, peened the shaft before re-installing and have not had any issues with bearing spinning on the shaft so far, knock on wood. Have about 10,000km on the sled now.
YamaSpark
Extreme
- Joined
- Sep 21, 2017
- Messages
- 110
- Location
- Greenfield, Minnesota
- Country
- USA
- Snowmobile
- 2016 SR VIPER S-TX 137 DX
Was having a few issues getting the assembly to seat consistently and figured out a simple solution to it. This morning I installed it on a running viper to test it on the stand for pulsations in lever. While I only ran it up to 75-80 mph on the stand I had no pulsations in the lever. Upon this stand test I discovered a more alarming concern. The entire caliper/bearing assembly and tunnel would wiggle back and forth. Locking the rotor down is exposing run out in the drive shaft. As soon as I would unlock the rotor the wiggle went away. Over time I can see this fatiguing the tunnel, so unfortunately locking the rotor down is not something I want to promote.
Don't worry......my quest for a solution is still very much alive. My fit ups and experimenting exposed yet another solution. When I was seating the wedge assembly inside drive shafts on the work bench I discovered that brake rotor wiggle disappeared once the wedge was expanded inside the drove shaft. So I slid the wedge assembly back farther in the shaft where the bearing rides and locked it down. The wedge expands the shaft enough to create an interference fit for the bearing! With wedge loose the bearing just falls off the shaft, but when wedge is tight I have to use some force to pull it off.
My goal is to get wedge to seat tight enough that I can't even pull the bearing off by hand. Right now the class 8 bolts shear off before I can get expand it enough. Tried a higher class bolt and it ripped threads out of wedge. Some new wedge designs are in the works for expansion across the full circumference and a larger bolt. This concept could function as a bolt in solution to preserve a drive shaft or repair worn drive shaft![]()
Hey Travis, any updates on your new wedge expansion concept?
I was originally thinking about going with the set screw under the bearing, but was never too comfortable with that since it could possibly distort the bearing slightly. I feel that your plan would be ideal.
Fast
TY 4 Stroke Guru
- Joined
- Sep 25, 2018
- Messages
- 995
- Age
- 57
- Location
- Ontario
- Country
- Canada
- Snowmobile
- 2019 srx,2006 apex gt,96 storm hot to go
Travis any word on the oil tank gasket??If you bisect anywhere through the center line of the cross section and weigh both halves they would be the same weight so I'm not sure why it would not be balanced. Also as mentioned the mass is very close to centerline with a radius of .625", so even if I wasn't balanced it wouldn't translate to much.
Are there any big summer drag racers lurking that would be interested in testing the setup for me? By no means are drag runs a durability test, but would at least put some heat cycles to the assembly to see how it holds up. Because it relies on friction to hold one concern is an extreme braking situation causing some expansion of the drive shaft. To be safe maybe I switch to aluminum as it would have a faster expansion rate than the shaft.

hibshman25
Vendor
- Joined
- Sep 25, 2005
- Messages
- 2,868
- Age
- 41
- Location
- Lebanon, PA 17042
- Country
- USA
- Snowmobile
- 2017 sidewinder ltx dx
2018 snoscoot
Still working on this. Tried a design easier to machine, but it didn't work. Here's a little demonstration video with the most successful version to date. Going to try one more design and hope to get sample made up end of week.
Fast
TY 4 Stroke Guru
- Joined
- Sep 25, 2018
- Messages
- 995
- Age
- 57
- Location
- Ontario
- Country
- Canada
- Snowmobile
- 2019 srx,2006 apex gt,96 storm hot to go
What about the simple oil cover gasket you said you were working on????Still working on this. Tried a design easier to machine, but it didn't work. Here's a little demonstration video with the most successful version to date. Going to try one more design and hope to get sample made up end of week.
snoprof6
Expert
- Joined
- Mar 26, 2007
- Messages
- 264
- Age
- 34
- Location
- Upstate NY
- Country
- USA
- Snowmobile
- 20 Indy XCR
16 Zr 6000 LTD
02 Sx Viper
02 Sx Viper
I like this wedge much better
IH8CROWS
Expert
If it was simple me or you would of come up with something. LOLWhat about the simple oil cover gasket you said you were working on????
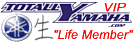

jonlafon1
Lifetime Member
- Joined
- Aug 18, 2014
- Messages
- 4,282
- Age
- 50
- Country
- USA
- Snowmobile
- 2022 Sidewinder LTX_SE
2024 Catalyst RXC
2017 Sidewinder LTX-SE. 11750 miles (SOLD)
Still subscribed to this one!


Similar threads
- Replies
- 6
- Views
- 3K
- Replies
- 5
- Views
- 687
- Replies
- 36
- Views
- 6K
- Replies
- 1
- Views
- 640
- Replies
- 327
- Views
- 58K
-
This site uses cookies to help personalise content, tailor your experience and to keep you logged in if you register.
By continuing to use this site, you are consenting to our use of cookies.